14644 Cleanroom Blog
Here you find my blog with Cleanroom-articles and news
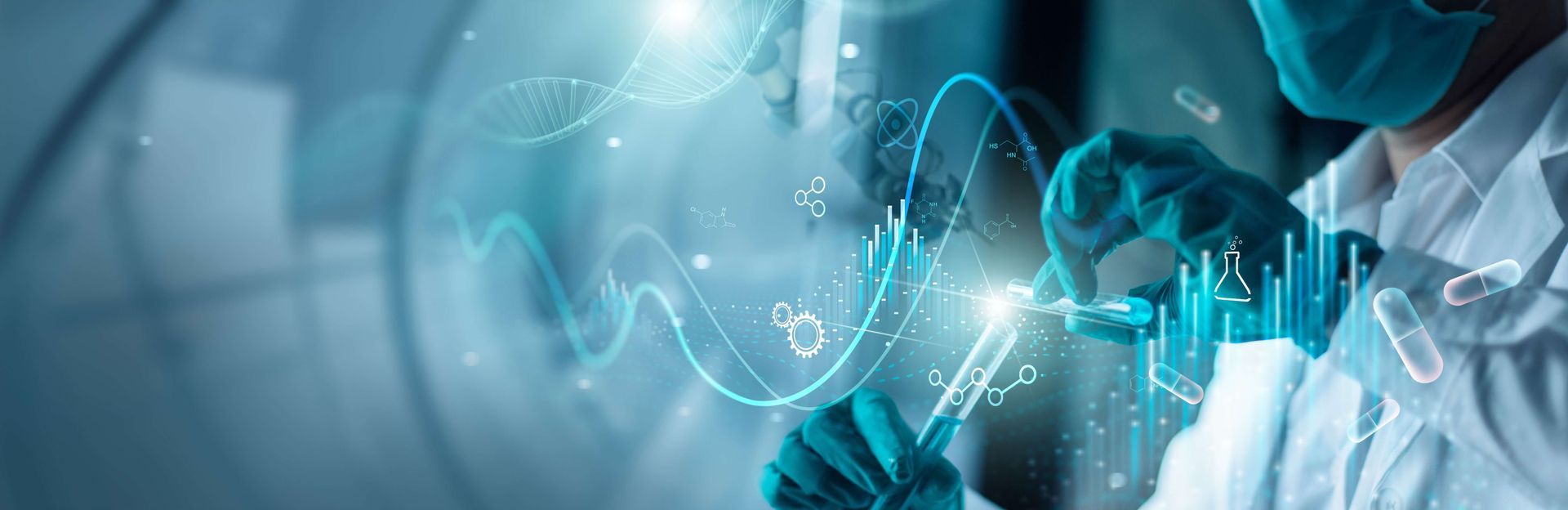
Introduction Cleanrooms, crucial environments in industries like pharmaceuticals, biotechnology, semiconductor manufacturing, aerospace, and healthcare, are designed to minimize contamination and maintain stringent environmental controls. These spaces require high levels of energy input to maintain optimal conditions, such as precise temperature, humidity, air filtration, and pressure regulation. Cleanroom systems typically operate continuously, making them some of the most energy-intensive spaces within manufacturing and research facilities. While cleanrooms are designed with safety, product integrity, and contamination control in mind, it is equally important for businesses to consider energy efficiency. With rising energy costs, growing environmental concerns, and increasing regulatory pressure, cleanroom operators must find ways to minimize energy consumption without compromising performance, cleanliness, or safety. This article explores key strategies and technologies for improving energy efficiency in cleanroom operations, focusing on sustainable approaches that can reduce operating costs, enhance environmental impact, and improve overall system performance. The Energy Demands of Cleanrooms Before diving into strategies for energy efficiency, it's important to understand why cleanrooms are so energy-demanding. Cleanrooms typically require: HVAC Systems : Cleanrooms rely on high-efficiency heating, ventilation, and air conditioning (HVAC) systems to maintain precise temperature, humidity, and air quality standards. HVAC systems must continuously filter and circulate large volumes of air, ensuring that the air is free from particles, microorganisms, and chemical contaminants. This high airflow and filtration requirement consumes a significant amount of energy. Air Filtration : Cleanrooms use specialized filtration systems, such as HEPA (High-Efficiency Particulate Air) or ULPA (Ultra-Low Penetration Air) filters, to remove airborne particles. These filters need to be replaced or cleaned regularly, and the ventilation systems must work harder as filters become clogged, leading to higher energy usage. Pressure Control : Cleanrooms must maintain precise pressure differentials to prevent contaminants from entering the space from adjacent areas. This requires continuous control and monitoring of airflow, which is energy-intensive. Lighting and Equipment : Cleanrooms also use specialized lighting and equipment that are designed for cleanroom environments. These may include bright, flicker-free LED lights, which are energy-efficient but still add to the overall energy load, especially when the cleanroom is operational 24/7. Why Energy Efficiency Matters in Cleanrooms Energy efficiency in cleanrooms is vital for several reasons: Cost Savings : Given the constant energy demand for HVAC systems, filtration, lighting, and equipment, energy consumption in cleanrooms can account for a significant portion of a facility's total energy costs. Implementing energy-saving strategies can reduce electricity and heating/cooling expenses over time, helping businesses control costs. Environmental Responsibility : As businesses become more aware of their environmental impact, reducing energy consumption helps minimize carbon footprints. Many industries, particularly those in high-regulation sectors, are facing increasing pressure to demonstrate environmental stewardship and sustainability. Compliance with Regulations : Government regulations and industry standards for energy use are tightening. Cleanroom operators need to comply with these standards to avoid penalties or fines. Additionally, energy-efficient practices may also be mandated in certain sectors to align with sustainability goals and reduce overall environmental impact. Operational Performance : Inefficient energy systems can lead to unnecessary wear and tear on equipment, increased maintenance costs, and, in some cases, disruptions in cleanroom operations. Efficient systems are often more reliable and cost-effective to maintain. Strategies for Improving Energy Efficiency in Cleanrooms There are several strategies that cleanroom operators can implement to improve energy efficiency without compromising the integrity of the cleanroom environment. These strategies can be broadly categorized into operational, technological, and design-based approaches. 1. Optimizing HVAC Systems Given that HVAC systems are the most energy-intensive component of a cleanroom, improving the efficiency of these systems should be a primary focus. Several techniques can enhance HVAC energy efficiency: Variable Air Volume (VAV) Systems : A variable air volume system adjusts the amount of airflow depending on the cleanroom's needs. By reducing airflow when less filtration is required (e.g., during periods of low activity), VAV systems help lower energy consumption. The system only increases airflow when high air exchange rates are necessary, such as during production or cleaning cycles. Demand-Controlled Ventilation (DCV) : DCV adjusts ventilation rates based on real-time occupancy or contaminant levels. For instance, during periods when fewer people are in the cleanroom, or when the contaminants are minimal, the system can reduce airflow, saving energy. Sensors can be used to monitor CO2 levels, air quality, and particle counts to control the ventilation rates dynamically. Heat Recovery Ventilation (HRV) : Heat recovery ventilation systems capture energy from the exhaust air and use it to precondition incoming air. This can significantly reduce the need for heating and cooling energy, as the HRV system recycles energy that would otherwise be wasted. In cold climates, this can reduce heating costs, while in warm climates, it reduces the cooling load. Airflow Optimization : Optimizing airflow through careful layout and design of air distribution systems can improve HVAC efficiency. Strategies include eliminating unnecessary ducts, reducing air leakage, and placing air inlets and outlets in optimal locations for effective air distribution. Proper sealing and insulation also ensure that air does not escape through cracks or gaps in the cleanroom envelope. 2. Energy-Efficient Filtration Systems The filtration system is another significant energy consumer in cleanrooms. To improve energy efficiency, consider the following options: Filter Efficiency and Maintenance : The efficiency of filters plays a major role in how hard HVAC systems have to work. Choosing the right filter for the cleanroom’s needs—whether HEPA or ULPA—ensures optimal performance. Furthermore, regular maintenance, such as cleaning or replacing filters, reduces strain on HVAC systems and ensures that air filtration is both effective and energy-efficient. Low-Resistance Filters : Newer technologies have introduced low-resistance filters that require less power to move air through them. These filters maintain the high filtration standards necessary for cleanrooms but reduce the pressure drop across the filter, thereby reducing energy use. Modular Filter Banks : Modular filter banks allow for the addition or removal of filters as needed. This helps maintain airflow without overburdening the system. If the cleanroom’s requirements change (e.g., higher particle filtration or changing regulatory standards), the system can be adjusted without significantly impacting energy use. 3. Energy-Efficient Lighting Lighting is an important component of cleanroom energy use. Cleanrooms often require bright, uniform lighting to ensure optimal working conditions. However, this can result in high energy consumption. To optimize lighting: LED Lighting : LED lighting is much more energy-efficient than traditional fluorescent lighting. LED bulbs consume less energy, last longer, and generate less heat. Additionally, LEDs can be integrated with smart lighting systems that adjust based on the time of day or occupancy, further reducing energy consumption. Motion Sensors and Timers : Installing motion sensors and timers can ensure that lights are only on when needed. For example, lights can automatically dim or turn off when no personnel are present in the cleanroom, which significantly reduces energy consumption without affecting operations. Daylight Harvesting : If the cleanroom has access to natural light, consider using daylight harvesting systems that adjust artificial lighting levels based on available natural light. This can reduce the amount of electricity needed to illuminate the space during daylight hours. 4. Energy-Efficient Equipment Other energy-consuming equipment, such as sterilizers, autoclaves, and other machinery, also contributes to the overall energy usage of a cleanroom. To improve energy efficiency in equipment: Upgrading Equipment : Older equipment may not be optimized for energy use. Upgrading to newer, energy-efficient models can result in significant energy savings. For instance, modern sterilizers are designed to use less water, energy, and time compared to older models. Scheduling Equipment Use : In some cases, the timing of equipment use can affect energy consumption. For example, scheduling equipment like autoclaves to run during off-peak hours or during low-energy-demand periods helps reduce the overall energy load on the system. 5. Design Considerations for Cleanroom Energy Efficiency The design phase offers many opportunities to incorporate energy efficiency into cleanroom operations. These strategies include: Room Layout : Properly designing the cleanroom layout can optimize airflow and minimize the need for excessive HVAC energy. The placement of equipment, personnel areas, and materials should be considered to ensure efficient air distribution, minimize contamination, and reduce energy use. Building Envelope : The cleanroom's exterior walls, windows, and roof should be well insulated to prevent heat loss in cold climates and heat gain in hot climates. Proper insulation reduces the heating and cooling demands of the HVAC system. Energy-Efficient Materials : The use of energy-efficient materials in the construction and design of cleanrooms, such as energy-efficient doors, windows, and walls, can help optimize energy use and prevent unnecessary energy loss. Conclusion Energy efficiency in cleanrooms is critical for reducing operational costs, improving environmental sustainability, and ensuring long-term operational performance. By implementing strategies such as optimizing HVAC systems, improving filtration efficiency, utilizing energy-efficient lighting, and upgrading equipment, cleanroom operators can significantly reduce their energy consumption while maintaining the cleanliness and functionality required for sensitive manufacturing processes. Cleanroom design, including room layout and material selection, also plays an important role in achieving energy efficiency. Ultimately, by adopting these energy-efficient strategies, cleanroom operators can not only lower costs but also contribute to broader sustainability goals and comply with increasingly stringent regulatory requirements. Read more: All About Cleanrooms - The ultimate Guide
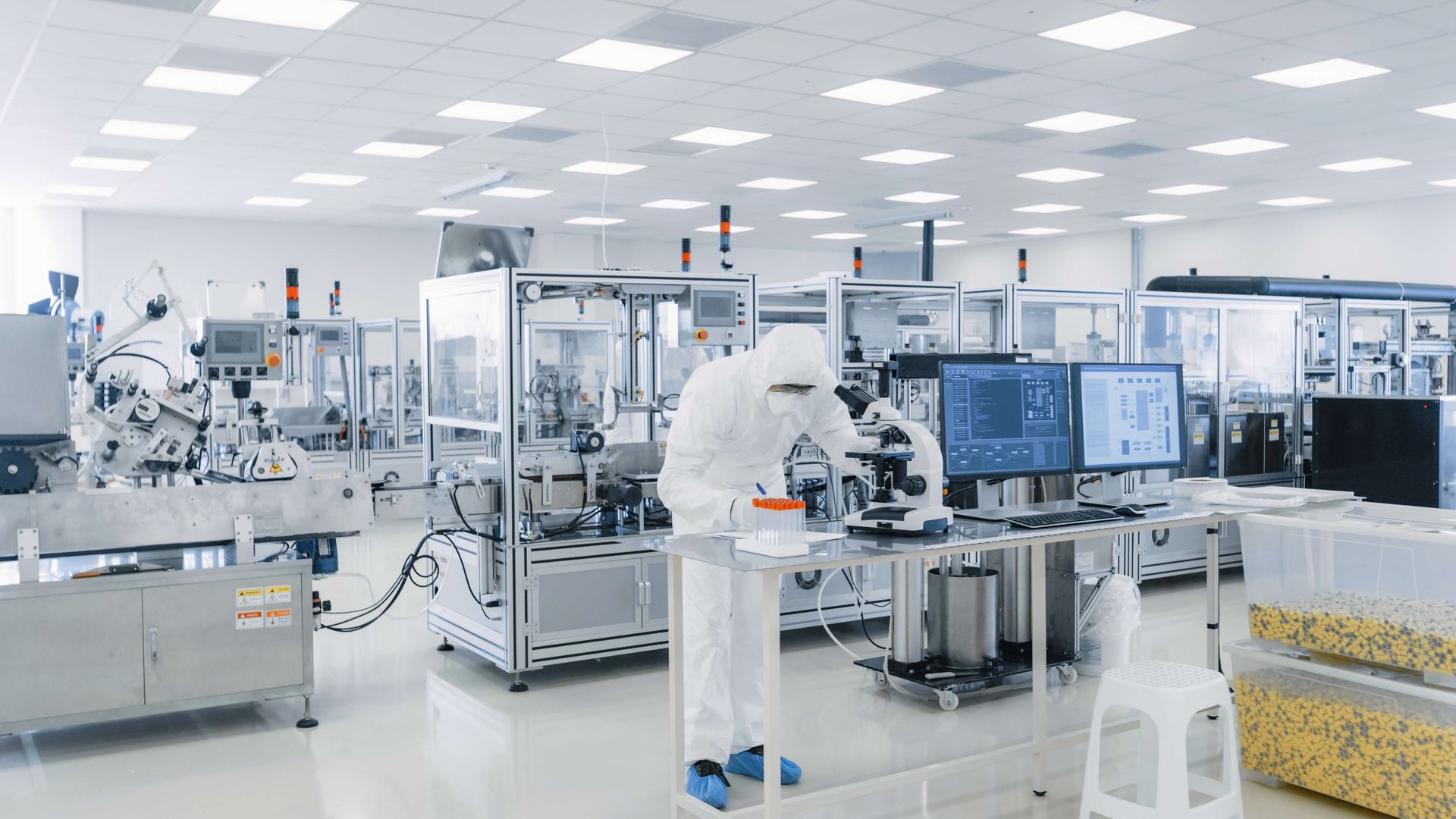
Introduction Cleanrooms are essential for industries where contamination control is critical to ensuring product quality, safety, and regulatory compliance. Whether in pharmaceuticals, biotechnology, aerospace, semiconductor manufacturing, or medical device production, cleanrooms are designed to maintain controlled environments to minimize particulate contamination. These controlled environments must adhere to strict guidelines, standards, and regulations to ensure they meet safety, health, and environmental requirements. In this article, we will explore the legal and regulatory aspects of cleanroom compliance. We will focus on the standards that govern cleanroom operations, the legal implications of non-compliance, and the various frameworks that help businesses operate within the parameters of health, safety, and environmental regulations. We will also look at the importance of certification and the role of audits and inspections in maintaining cleanroom standards. Legal and Regulatory Standards for Cleanrooms There are various regulatory bodies and standards that govern cleanroom design, operations, and performance. These standards ensure that cleanrooms operate within safe and controlled environments, particularly in industries where contamination could have serious consequences. 1. ISO 14644: The Global Standard for Cleanroom Classifications ISO 14644, developed by the International Organization for Standardization (ISO), is the most widely recognized global standard for cleanroom operations. It is essential for establishing cleanroom classifications based on the level of particulate contamination in the air. The standard defines air cleanliness by the number of airborne particles per volume of air, typically measured in particles per cubic meter, for different particle sizes. ISO 14644 is divided into several parts: ISO 14644-1 : Defines cleanroom classification based on particulate cleanliness. ISO 14644-2 : Provides guidelines on the monitoring of cleanrooms and controlled environments. ISO 14644-3 : Specifies testing methods for air cleanliness. ISO 14644-4 : Provides guidelines for design, construction, and operation of cleanrooms. The classification is defined by ISO 14644-1, which assigns a class number to cleanrooms, such as ISO Class 1 to ISO Class 9. Each class has different limits for the maximum allowable particulate count, with ISO Class 1 being the cleanest and most stringent. These classifications are critical for industries like pharmaceuticals and semiconductor manufacturing, where the cleanliness of the air directly impacts the quality of products and processes. 2. Good Manufacturing Practices (GMP) Good Manufacturing Practices (GMP) are a set of regulations set forth by authorities like the U.S. Food and Drug Administration (FDA), the European Medicines Agency (EMA), and other national regulatory bodies. These practices ensure that products are consistently produced and controlled according to quality standards. For cleanrooms, GMP guidelines include provisions for environmental control, including temperature, humidity, and particulate contamination. GMP also addresses cleanroom maintenance, personnel hygiene, gowning procedures, cleaning schedules, and equipment handling—all of which must be followed to minimize the risk of contamination in environments where drugs, medical devices, and other sensitive products are manufactured. Non-compliance with GMP regulations can lead to severe consequences, such as product recalls, fines, or even shutdowns of manufacturing operations. Compliance is, therefore, essential not just for maintaining product quality but also for protecting public health and safety. 3. The Food and Drug Administration (FDA) The FDA is responsible for ensuring the safety and effectiveness of drugs, medical devices, and other healthcare products in the United States. The FDA's guidelines for cleanroom operations, particularly in the pharmaceutical and medical device sectors, align with GMP requirements. Specific provisions from the FDA, such as 21 CFR Part 210 and Part 211, address cleanroom conditions, which include air quality, temperature and humidity control, and sterilization procedures. The FDA requires that companies adhere to these regulations to ensure that their cleanrooms provide a controlled environment for drug and device manufacturing. Any deviation from FDA guidelines can lead to warnings, citations, and regulatory action. 4. European Union (EU) Regulations The European Medicines Agency (EMA) oversees the regulation of pharmaceuticals and medical devices within the European Union. The EMA follows the EU’s GMP guidelines and has specific requirements for cleanroom standards, which are similar to those established by the FDA. In addition to GMP, the EU also follows other regulations like the European Union Medical Device Regulation (MDR) and In Vitro Diagnostic Regulation (IVDR) , which address the manufacturing of medical devices and in-vitro diagnostic products. These regulations also include provisions for cleanroom environments, where the risk of contamination must be strictly controlled. The EU guidelines are enforceable by law and carry serious consequences for non-compliance, including the withdrawal of products from the market and possible criminal charges. Key Legal Implications of Cleanroom Non-Compliance Non-compliance with cleanroom regulations can have significant legal implications for businesses, especially in highly regulated industries like pharmaceuticals, biotechnology, and medical devices. The legal risks include: 1. Product Recalls and Penalties Non-compliance with cleanroom regulations, such as failing to meet ISO cleanliness standards or GMP guidelines, can lead to product recalls. If contaminated products make it to the market—such as pharmaceutical drugs or medical devices—they can pose a serious threat to public health. This can lead to a company being held liable for damages, loss of reputation, and substantial financial penalties. In addition to product recalls, regulatory bodies like the FDA or EMA may issue warnings, fines, or suspend manufacturing licenses, depending on the severity of the violation. For example, a manufacturer found to have violated GMP regulations may face a warning letter from the FDA, a costly product recall, or even a suspension of operations. 2. Litigation and Liability In industries like pharmaceuticals, biotechnology, and medical devices, cleanroom non-compliance can lead to litigation if contaminated products cause harm. Patients or users of medical devices can file lawsuits, and the company could be held liable for damages. This can be financially disastrous and damage the company’s reputation in the industry. 3. Loss of Certification or Accreditation Cleanrooms often require certification from regulatory agencies, particularly in highly regulated industries. Failure to maintain compliance with relevant standards can lead to the loss of certifications or accreditations, such as ISO 14644, GMP certifications, or other industry-specific certifications. Losing certification means the company cannot legally manufacture or distribute its products in certain markets. 4. Regulatory Inspections and Audits Regulatory bodies frequently conduct audits and inspections of cleanroom facilities. The FDA, EMA, and other organizations perform inspections to ensure compliance with regulatory guidelines and standards. An inspection that reveals non-compliance with cleanroom requirements could result in costly penalties, production stoppages, or long-term damage to the company’s ability to operate. Ensuring Compliance: Cleanroom Certification and Audits 1. Cleanroom Certification Certification is a critical aspect of ensuring that cleanrooms meet legal and regulatory requirements. Cleanroom certification is an ongoing process that involves regular testing, documentation, and verification of air cleanliness, temperature, humidity, and pressure. Cleanroom operators must use certified equipment and personnel trained in proper cleanroom procedures. The most common cleanroom certification standard is ISO 14644, but other certifications may be required depending on industry-specific regulations. For example, pharmaceutical companies must adhere to GMP standards for cleanrooms, which may also require certification from regulatory bodies like the FDA or EMA. 2. Regulatory Audits and Inspections Regular audits and inspections are necessary for cleanroom operators to demonstrate compliance. These audits typically evaluate: The condition of the cleanroom environment (air quality, temperature, humidity). Equipment maintenance and calibration records. Compliance with GMP and other industry-specific regulations. Personnel training and gowning procedures. Cleaning protocols and disinfecting practices. Auditors assess the overall compliance of the facility and the implementation of best practices to ensure ongoing adherence to regulations. Conclusion Cleanroom compliance is crucial for industries where contamination control is essential to product safety, quality, and efficacy. Legal and regulatory frameworks, such as ISO 14644, GMP, and FDA guidelines, provide essential guidelines for maintaining a cleanroom environment that meets the strictest cleanliness standards. Non-compliance can have serious legal and financial consequences, including product recalls, lawsuits, and loss of accreditation. By adhering to these legal and regulatory requirements, businesses can minimize contamination risks, protect public health, and ensure the integrity of their products. Certification, regular audits, and continuous compliance with standards are necessary to maintain cleanroom standards and safeguard the reputation and operational success of companies within highly regulated industries. Read more: All About Cleanrooms - The ultimate Guide
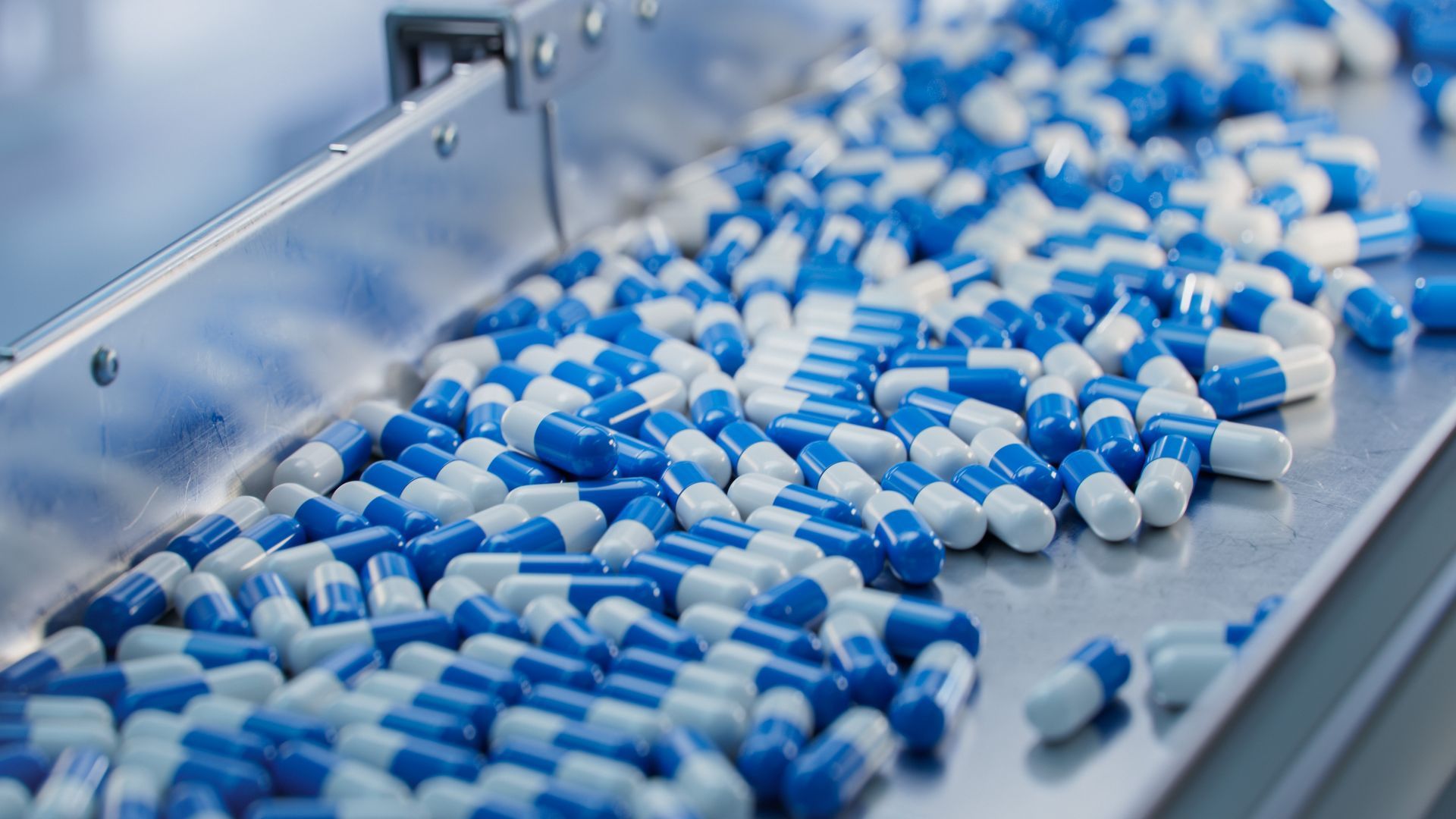
Introduction Cleanrooms are environments that require stringent control over airborne particles, temperature, humidity, and other factors to ensure product quality, safety, and operational effectiveness. The materials used for cleanroom walls and ceilings are vital in maintaining cleanliness, structural integrity, and performance in highly regulated environments such as pharmaceuticals, biotechnology, electronics manufacturing, and aerospace. Over time, innovations in cleanroom wall and ceiling materials have significantly advanced in response to evolving regulatory demands, sustainability needs, and operational efficiency. This article delves into the most impactful innovations in cleanroom wall and ceiling materials, highlighting new technologies, materials, and design concepts. 1. Introduction to Cleanroom Requirements Cleanrooms are classified based on the level of particulate contamination they can tolerate. The materials used for the walls and ceilings in these rooms are expected to meet specific criteria that ensure optimal cleanliness and safety. These criteria include: Non-porosity : Walls and ceilings should be smooth and resistant to particle accumulation. Cleanability : Materials must be easy to clean, durable, and resistant to wear. Durability : Resistance to physical damage, chemicals, and thermal stress is critical. Fire resistance : Fire safety is crucial in highly regulated environments. Energy efficiency : Cleanroom materials must contribute to energy-saving solutions, especially with high operational costs. 2. Key Innovations in Cleanroom Wall Materials Innovations in wall materials primarily focus on improving functionality, sustainability, and ease of installation. Below are some of the key innovations: a. Modular Cleanroom Wall Systems Design Flexibility : Modular systems consist of pre-fabricated panels made from various materials, including metals, composites, and plastics. This modular approach allows for fast and easy construction, customization, and upgrades. Easy Maintenance : The modularity of the panels makes it easier to replace or adjust sections of the walls without disrupting the entire cleanroom operation. Integrated Features : Some modular systems feature integrated components like lights or airflow management systems. b. High-Performance Coatings Anti-Microbial Coatings : These coatings help prevent the growth of harmful microorganisms on the surface, a critical feature in environments such as pharmaceuticals and food processing. Low-VOC Paints : Low volatile organic compound (VOC) paints improve air quality by releasing fewer harmful chemicals into the environment, contributing to cleaner air in the controlled environment. Enhanced Durability : These coatings improve the resistance of cleanroom surfaces to chemicals, moisture, and physical impact. c. Composites and Hybrid Materials Fiberglass Reinforced Panels (FRP) : FRP provides a smooth, durable, and resistant surface that is easy to clean, making it ideal for cleanroom environments. Hybrid Materials : Combining multiple materials (e.g., metals and plastics) allows for greater flexibility in achieving the desired balance of strength, durability, and ease of maintenance. 3. Innovations in Cleanroom Ceiling Materials Ceilings in cleanrooms serve multiple functions, from supporting air filtration systems to ensuring uniform air circulation. Some innovations in ceiling materials include: a. Suspended Ceiling Systems Improved Grid Systems : Modern suspended ceiling grids are designed with tight seals to reduce the accumulation of dust and particulate matter. Lightweight and Fire-Resistant Materials : Ceiling panels made from metals or composites offer better fire resistance and longer-lasting performance while maintaining ease of maintenance. Flexibility in Installation : Suspended ceilings offer flexibility in concealing electrical wiring, ducts, and other essential systems without compromising the cleanroom’s functionality. b. Integrated Lighting and Air Filtration Systems Airflow Optimization : Integrated ceiling designs allow for the seamless incorporation of high-efficiency particulate air (HEPA) filters, ensuring that clean air is continually supplied to the room. Streamlined Maintenance : The integration of lighting and filtration systems into the ceiling minimizes the need for separate installations, reducing the risk of contamination and simplifying maintenance. c. Thermal Insulation Materials Aerogels and Composites : Advanced thermal insulation materials such as aerogels help maintain consistent temperatures and reduce energy consumption. These materials are highly efficient at preventing heat transfer, contributing to better temperature control and reduced energy costs. Condensation Control : Proper insulation materials help prevent condensation on ceiling surfaces, which could lead to contamination in sensitive cleanroom environments. 4. Sustainability and Energy Efficiency As sustainability becomes a primary focus, cleanroom designs are evolving to incorporate energy-efficient materials and environmentally friendly practices. a. Energy-Efficient Materials Reflective Foils and Aerogels : These materials provide superior insulation, reducing the need for heating and cooling systems while maintaining temperature stability. Smart Materials : Thermochromic or photochromic materials that respond to temperature or light conditions can further optimize energy consumption and reduce operational costs. b. Recyclable Materials Eco-Friendly Composites : Many new cleanroom materials are designed to be recyclable, reducing waste generated during construction and operation. Green Certifications : Manufacturers are developing materials that meet sustainability certifications, contributing to cleaner construction practices and helping companies achieve their green building goals. 5. Future Trends and Research Directions Ongoing research in material science and cleanroom design is focused on enhancing the performance, sustainability, and cost-efficiency of cleanroom environments. a. Smart Cleanroom Technologies Sensors and Monitoring : The integration of smart sensors into walls and ceilings will allow for real-time monitoring of temperature, humidity, and particle counts. This technology will enable automated adjustments, improving the efficiency of cleanroom operations. Predictive Maintenance : With the help of machine learning and data analytics, cleanroom wall and ceiling systems will be able to predict wear and tear, enabling more efficient maintenance schedules. b. Advanced Airflow Systems Dynamic Airflow Control : Research into dynamic airflow systems aims to enhance air circulation and particle removal based on real-time conditions, reducing energy consumption and improving the overall cleanliness of the room. Modular Airflow Management : New innovations in modular air filtration and ventilation systems are designed to be integrated into both walls and ceilings, offering better control over airflow distribution. Conclusion Innovations in cleanroom wall and ceiling materials have significantly advanced over the years, driven by the need for higher performance, greater sustainability, and operational efficiency. From modular cleanroom wall systems to advanced ceiling panels with integrated air filtration and lighting, these innovations contribute to better control over the cleanroom environment and ensure compliance with stringent regulations. As the demand for cleaner, more sustainable, and more efficient cleanrooms grows, it is likely that further advancements will continue to reshape the way cleanroom walls and ceilings are designed and constructed, making these environments even more adaptable and effective in meeting the needs of various industries. The growing focus on energy efficiency, smart technologies, and recyclable materials indicates that the future of cleanroom construction will prioritize sustainability without compromising on performance, safety, or cleanliness. Read more: All about Cleanrooms : The Ultimate Guide
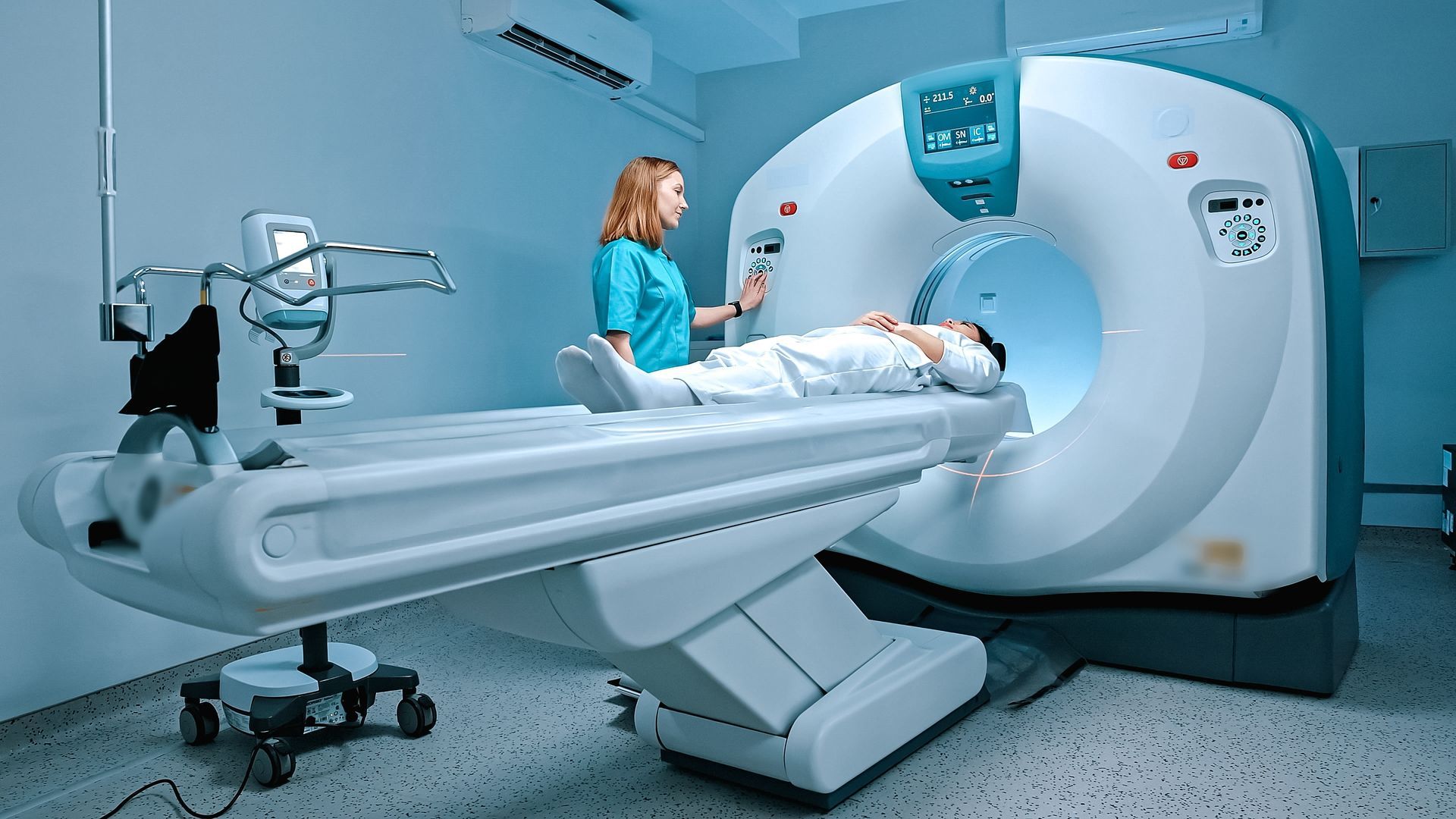
Introduction Cleanrooms are essential in industries where maintaining a contamination-free environment is critical to the quality, safety, and efficacy of the products being produced. These specialized environments are designed to minimize airborne particles, dust, microbes, and other potential contaminants, ensuring that sensitive processes and materials remain uncontaminated throughout their lifecycle. Cleanrooms are widely used across various sectors, including pharmaceuticals, biotechnology, aerospace, semiconductor manufacturing, and medical device production, where even the slightest deviation in environmental conditions can have significant consequences. In this article, we will explore the crucial role cleanrooms play in enhancing product quality, how they impact manufacturing processes, and the various factors that contribute to maintaining the highest standards of cleanliness. We will also delve into the operational and regulatory implications of cleanroom environments and how they help businesses maintain product integrity, meet compliance standards, and ultimately drive customer satisfaction. Cleanrooms and Their Role in Product Quality The primary goal of a cleanroom is to provide a controlled environment where contamination risks are minimized, and product integrity is safeguarded. These environments are equipped with specialized air filtration systems, humidity and temperature controls, pressure differentials, and meticulous protocols for cleaning, gowning, and material handling. By maintaining strict control over these factors, cleanrooms ensure that products and processes meet the highest quality standards and regulatory requirements. The impact of cleanrooms on product quality is evident across various stages of the product lifecycle, from design and development to manufacturing and packaging. Below are several key ways in which cleanrooms positively influence product quality: 1. Contamination Control One of the most significant ways in which cleanrooms impact product quality is through contamination control. In industries like pharmaceuticals, biotechnology, and semiconductor manufacturing, even the smallest particle or microorganism can cause defects, contamination, or failure of products. For example, in the production of injectable drugs, the presence of airborne bacteria or particles can compromise the sterility of the product, making it unsafe for human use. Cleanrooms are designed to minimize the introduction of contaminants from various sources, including personnel, equipment, materials, and the external environment. Air filtration systems, such as High-Efficiency Particulate Air (HEPA) or Ultra-Low Penetration Air (ULPA) filters, are used to trap airborne particles, while positive pressure ventilation systems help ensure that cleanroom air flows outward, preventing the ingress of contaminants from surrounding areas. By maintaining strict cleanliness standards, cleanrooms reduce the likelihood of defects or contamination, ultimately ensuring that the product remains safe, effective, and of the highest quality. 2. Consistency in Manufacturing In cleanrooms, process control is critical, and a stable, controlled environment is crucial to ensure consistent results. Variations in environmental factors such as temperature, humidity, and particle levels can cause discrepancies in the manufacturing process, which can lead to inconsistencies in product quality. Cleanrooms help eliminate these variables by regulating and maintaining precise environmental conditions that are required for specific processes. For example, in the semiconductor manufacturing industry, where microchips are produced, even the smallest temperature fluctuation or particle in the environment can result in defective chips. Cleanrooms allow manufacturers to maintain consistent conditions during critical processes like photolithography, chemical vapor deposition (CVD), and etching, ensuring that the end product consistently meets the desired specifications. 3. Enhanced Precision and Accuracy Certain industries, such as aerospace, medical device manufacturing, and biotechnology, require a high level of precision in their products. Cleanrooms provide the optimal environment for ensuring that these precision-engineering processes are conducted without interference from environmental factors. In the medical device industry, for instance, cleanrooms are used to manufacture components that must meet strict dimensional and functional tolerances. A small variation caused by external contamination or environmental fluctuations could render a product ineffective or unsafe for use. Cleanrooms help minimize these risks by providing a controlled space in which the product can be created with the utmost precision. In biotechnology research, cleanrooms also play a critical role in ensuring that experimental results are accurate and reproducible. By maintaining a contamination-free environment, researchers can work with sensitive biological materials without the risk of interference from airborne particles or microorganisms, ensuring the accuracy of their findings and the quality of any products derived from their research. 4. Regulatory Compliance and Product Safety Cleanrooms are essential for meeting the rigorous regulatory standards set forth by organizations such as the U.S. Food and Drug Administration (FDA), the European Medicines Agency (EMA), and the International Organization for Standardization (ISO). These regulatory bodies require that products—particularly in industries like pharmaceuticals, biotechnology, and medical devices—be manufactured under strict conditions to ensure their safety, efficacy, and quality. For example, the pharmaceutical industry adheres to Good Manufacturing Practices (GMP), which dictate that cleanrooms must meet specific cleanliness classifications based on the number of allowable particles per cubic meter. These regulations ensure that products such as sterile drugs, biologics, or vaccines are not contaminated during production, testing, or packaging. Failure to comply with these standards can result in product recalls, penalties, and damage to a company's reputation. By ensuring compliance with regulatory standards, cleanrooms help manufacturers produce high-quality products that meet the safety requirements set forth by health authorities, ultimately benefiting both businesses and consumers. 5. Improved Product Longevity and Stability In industries such as pharmaceuticals and biotechnology, the shelf life and stability of a product are critical to its success in the market. Cleanrooms help extend the longevity of products by ensuring that they are produced and stored in optimal conditions, free from contaminants that could compromise their stability. For example, in the production of biologic drugs or vaccines, environmental factors like temperature and humidity can significantly impact the efficacy of the final product. Cleanrooms with precise control over these factors help maintain the stability of these sensitive products, ensuring that they remain effective for the duration of their shelf life. 6. Protection of Sensitive Products and Materials Many products in industries such as electronics, aerospace, and pharmaceuticals contain highly sensitive materials that can be damaged by environmental factors like dust, moisture, or temperature fluctuations. Cleanrooms provide a controlled environment to protect these materials during manufacturing and assembly. In the semiconductor industry, for example, the production of microchips involves delicate processes that require extreme precision. Even a tiny speck of dust can interfere with the production of a microchip, causing defects that can affect the chip’s performance or lead to product failure. Cleanrooms offer a safe, controlled space to manufacture these components, ensuring that they meet the rigorous quality standards required for use in sensitive devices like smartphones, computers, and medical equipment. Factors Contributing to Cleanroom Impact on Product Quality Several factors contribute to how cleanrooms affect product quality. These factors can vary depending on the type of cleanroom, the industry, and the specific processes involved, but the following are some of the most critical: 1. Air Quality and Filtration Systems Air filtration is one of the most critical components of cleanroom design. HEPA or ULPA filters are used to capture particulate matter from the air, ensuring that the cleanroom remains free from contaminants. The efficiency of the filtration system directly affects the cleanliness of the environment and, by extension, the quality of the products being manufactured or processed. 2. Temperature and Humidity Control Temperature and humidity control are vital for maintaining the stability and integrity of certain products. Cleanrooms are equipped with HVAC systems that regulate these factors, ensuring that they remain within optimal ranges for the specific product or process being performed. For example, temperature fluctuations can affect the viscosity of materials in pharmaceutical production or interfere with the curing process of coatings in semiconductor fabrication. 3. Personnel and Gowning Protocols Personnel play a crucial role in maintaining cleanroom standards. The introduction of contaminants from clothing, skin cells, or hair can lead to contamination. Cleanrooms implement strict gowning protocols, requiring workers to wear specialized clothing, including gowns, gloves, masks, and hairnets, to prevent the introduction of particles or microorganisms. 4. Equipment Calibration and Maintenance In cleanroom environments, equipment must be regularly calibrated and maintained to ensure that it operates within the required tolerances. Malfunctioning equipment can introduce defects or contamination into the product, leading to variations in quality. Routine checks and maintenance schedules ensure that the equipment is operating optimally, contributing to consistent product quality. 5. Training and Protocol Adherence Proper training for personnel is essential to ensure that cleanroom protocols are followed consistently. Workers must be aware of the importance of cleanliness, how to handle materials safely, and the correct procedures for gowning and decontaminating surfaces. Strict adherence to protocols ensures that the cleanroom environment remains sterile and that product quality is not compromised. Conclusion Cleanrooms play a fundamental role in ensuring product quality across various industries, from pharmaceuticals to semiconductor manufacturing. By controlling contamination, maintaining consistency, optimizing precision, and ensuring regulatory compliance, cleanrooms help businesses produce high-quality products that meet the stringent standards required for safety and efficacy. Whether producing drugs, medical devices, or microchips, the impact of cleanrooms on product quality cannot be overstated. They are an essential tool in ensuring that products are safe, reliable, and effective, and that the processes used to create them are efficient and compliant with industry regulations. By maintaining strict control over environmental factors, cleanrooms provide the foundation for high-quality products that meet the needs and expectations of consumers worldwide. Read more: All About Cleanrooms - The ultimate Guide
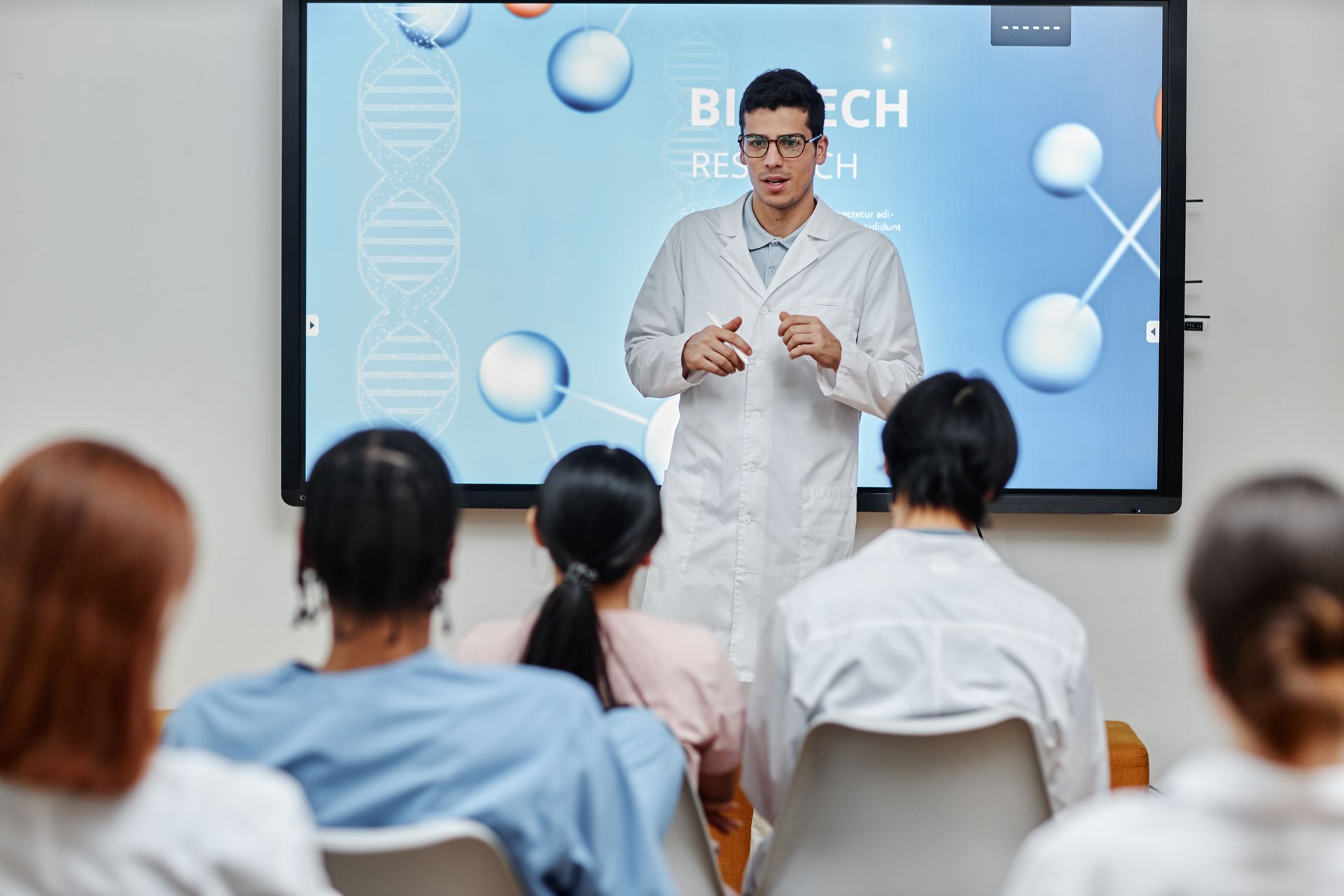
Introduction In the highly regulated world of cleanroom operations, every detail is essential. Whether you’re producing life-saving pharmaceuticals, manufacturing microelectronics with extreme precision, or assembling aerospace components, maintaining the highest standards is non-negotiable. For decades, cleanroom standards have been critical in ensuring the quality and safety of these operations, but after more than 20 years, one of the most important standards is undergoing its first major revision. ISO 14644-5, titled Cleanrooms and Associated Controlled Environments – Part 5: Operations, has served as the global guideline for cleanroom operations since its publication in 2004. Over the years, the industry has evolved, yet the standard has remained largely unchanged. That is, until the upcoming update in May 2025, which promises to modernize and streamline cleanroom practices to align with today's technological and regulatory advancements. The Long-Awaited Update to Cleanroom Operations ISO 14644-5 has long been a cornerstone of cleanroom management, covering everything from gowning and cleaning protocols to materials handling and personnel practices. However, with the advancements in controlled environments and stricter regulations, the original document was no longer enough to provide comprehensive guidance. In response, various organizations, including IEST, ANSI, ASTM, ESD, USP, PDA, and ISPE, have issued their own sets of recommended practices to address gaps in the existing ISO framework. While useful, this fragmented approach has meant that cleanroom professionals needed to consult multiple sources for best practices, often leading to confusion and inefficiency. Now, the new ISO 14644-5 revision consolidates these fragmented practices into a cohesive, updated framework, providing cleanroom operators with one unified set of standards that reflect current industry practices, risks, and regulatory expectations. Key Changes in the 2025 Revision One of the most notable updates in the 2025 revision is the integration of ISO 14644-18 , titled Cleanrooms and Associated Controlled Environments – Part 18: Assessment of Suitability of Consumables, which was published in 2023. ISO 14644-18 focuses on the selection and qualification of consumables such as gloves, wipers, garments, and other materials commonly used in cleanrooms. Historically, these consumables have been viewed as secondary materials. However, the 2025 update acknowledges that consumables are a critical component in maintaining contamination control. The updated standard now includes comprehensive criteria for evaluating consumables, such as particle counts, chemical contaminants, biocontamination risks, and functional performance. This helps ensure that materials do not become a source of contamination, which could compromise product integrity and compliance. IEST Recommended Practices (RPs) Now Part of ISO 14644-5 A significant development in the 2025 revision is the formal inclusion of IEST Recommended Practices (RPs) in the ISO framework. For the first time, these test-based, procedural guides are referenced in ISO standards to support cleanroom operations. Some key IEST RPs integrated into the updated standard include: IEST-RP-CC003 – Cleanroom Garments: This RP covers the selection, material types, and proper usage of cleanroom garments. It also provides guidelines for lifecycle management through modern tracking tools like barcoding and RFID. IEST-RP-CC004 – Wipers: This guide details the testing methods for wipers, including absorbency, particle release, and chemical compatibility, offering a more precise selection for specific applications. IEST-RP-CC005 – Gloves and Finger Cots: This RP covers the testing of barrier performance, microbial risks, and static dissipation, ensuring that gloves and other materials meet the strict requirements of cleanroom environments. By incorporating these IEST RPs, the 2025 revision enhances the technical direction available to cleanroom managers, allowing for better-informed decision-making when selecting consumables and managing cleanroom operations. What Does This Mean for Cleanroom Operators? The 2025 revision of ISO 14644-5 offers cleanroom professionals an opportunity to update their practices to better align with current standards and best practices. To fully take advantage of this updated framework, cleanroom managers should: Reevaluate Consumables: Reassess the selection, testing, and qualification of consumables to ensure they meet the new ISO and IEST criteria. This will help minimize contamination risks and improve overall compliance. Update SOPs and Procurement Standards: Review and revise Standard Operating Procedures (SOPs) and procurement standards to ensure they align with the new guidelines outlined in the revised ISO 14644-5. Utilize IEST RPs for Detailed Guidance: Leverage the IEST Recommended Practices to implement specific, test-based procedures in cleanroom operations, enhancing the quality and consistency of decisions made on a daily basis. Revise Training Programs: Update training programs to reflect the new operational requirements and best practices introduced by the 2025 revision. Ensure all staff are aware of the changes and trained to meet the updated standards. The Path Forward The 2025 update to ISO 14644-5 represents a critical milestone in the evolution of cleanroom standards. By consolidating fragmented practices into one unified standard and incorporating modern approaches to consumables and operational management, the new revision ensures that cleanroom operations remain effective and compliant in an increasingly complex environment. For organizations operating in cleanroom environments, adopting these changes early is essential to stay ahead of regulatory expectations, minimize contamination risks, and maintain the integrity of products. The 2025 ISO 14644-5 revision provides the opportunity to optimize processes, improve efficiency, and ultimately safeguard the quality of products that can have life-or-death consequences. Read more: All About Cleanrooms - The ultimate Guide
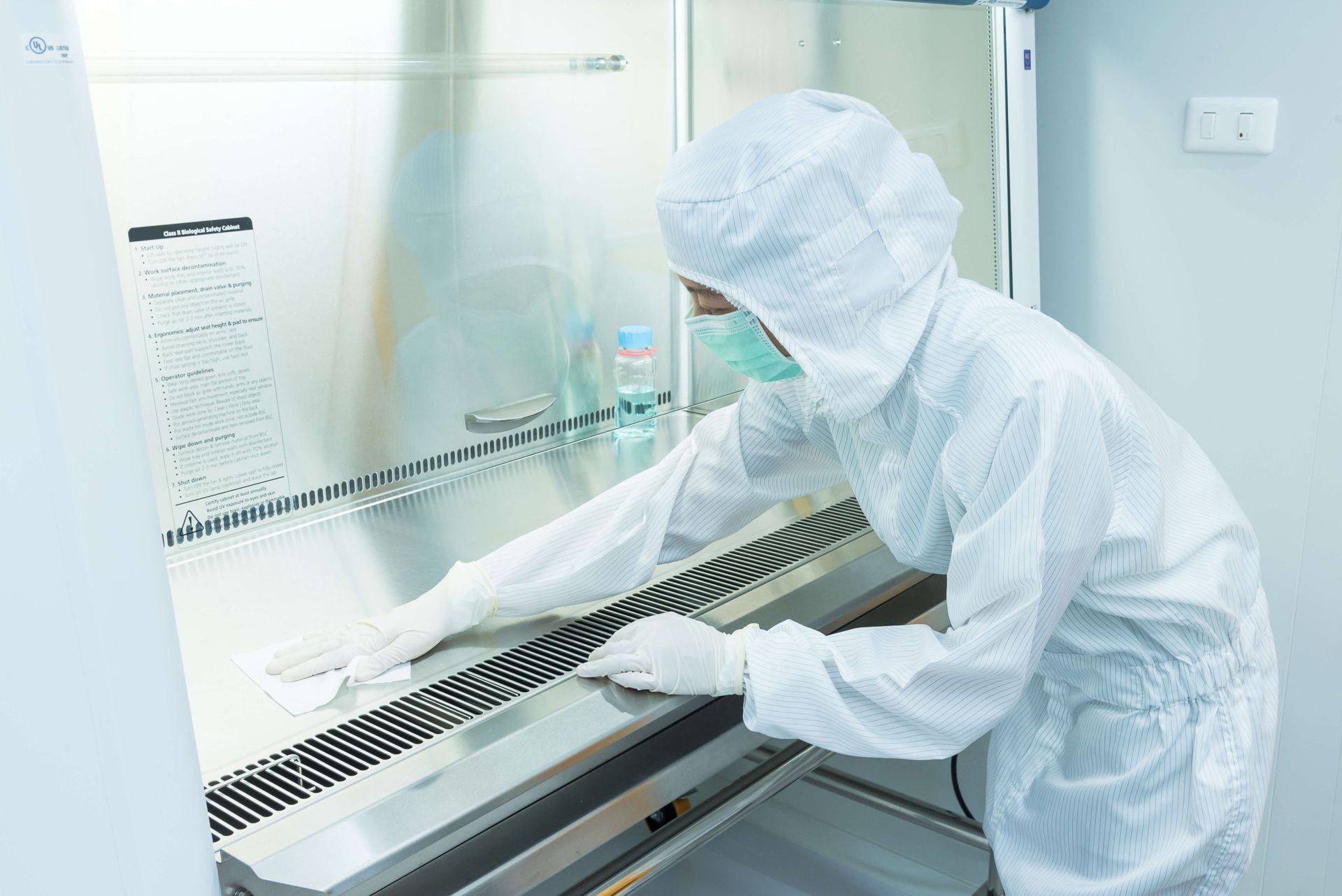
Introduction Cleanrooms are specialized environments designed to minimize contamination, ensuring the safety, quality, and precision of processes in industries such as pharmaceuticals, biotechnology, semiconductor manufacturing, aerospace, and medical devices. However, despite the rigorous design, maintenance, and operational protocols in place, cleanrooms are not immune to violations or contamination events. Even a small failure in maintaining cleanliness standards can have significant consequences for product quality, research accuracy, and, in some cases, the safety of consumers or patients. When a cleanroom violation or contamination event occurs, it is crucial to handle the situation swiftly and efficiently to minimize potential damage. This article will provide a comprehensive guide on how to handle cleanroom violations and contamination events, detailing key strategies, responses, and protocols that should be followed to mitigate risks and restore cleanroom conditions. Understanding Cleanroom Violations and Contamination Events Before diving into how to handle violations or contamination events, it’s important to understand what constitutes a cleanroom violation or contamination event. Cleanroom Violation : This refers to any situation in which cleanroom protocols are not followed or maintained. These violations could be related to improper gowning, non-compliance with cleanliness standards, equipment malfunction, failure to adhere to operational procedures, or human error. Violations can lead to contamination, compromised product quality, or regulatory non-compliance. Contamination Event : A contamination event occurs when an external or internal factor introduces undesirable particles, microorganisms, or chemical agents into the cleanroom environment. This could include the introduction of particles from the air, uncontrolled personnel movement, equipment malfunctions, or accidental breaches of sterile areas. A contamination event could be severe enough to compromise the entire cleanroom’s functionality, requiring immediate remediation. Both cleanroom violations and contamination events are critical occurrences that need to be addressed promptly and appropriately. The handling of these events can prevent severe consequences such as compromised product integrity, regulatory fines, or damage to the brand’s reputation. Immediate Response to Cleanroom Violations and Contamination Events When a cleanroom violation or contamination event occurs, immediate action must be taken to address the issue and prevent further contamination. The first response must be systematic, controlled, and well-documented to ensure that the violation or event is effectively managed. 1. Identify the Source of the Violation or Contamination Event The first step in managing a cleanroom violation or contamination event is to identify the source of the issue. Immediate steps should be taken to contain the contamination and isolate the affected area, if necessary. The following steps can help in identifying the source: Visual Inspection : Conduct a visual inspection of the area to assess whether the contamination is caused by human error (e.g., improper gowning, failure to follow protocols) or equipment malfunction. Monitor Airflow and Filtration Systems : Check the cleanroom’s HVAC system, air filtration systems, and particle counters to ensure they are operating correctly. A malfunction in these systems can lead to contamination. Evaluate Personnel : Ensure that all personnel are wearing the proper personal protective equipment (PPE) and are adhering to gowning protocols. Personnel should be re-trained or temporarily removed from the cleanroom if violations are found. Equipment Check : Inspect equipment and machinery for potential sources of contamination, such as leaks, spillage, or malfunctioning filters that could have caused a contamination event. 2. Contain the Contamination or Violation Once the source of contamination or the violation is identified, the next step is to immediately contain the issue to prevent further contamination. This is done by isolating the affected area and restricting access to the cleanroom until it is determined to be safe. Lockdown the Area : Implement immediate lockdown procedures. Restrict access to the cleanroom by personnel and visitors until the issue is identified and addressed. Quarantine Affected Products or Materials : If contamination has occurred in specific products, batches, or materials, quarantine these items immediately to prevent them from being used or distributed. Products that may have been contaminated should not be released into the production chain until they have been thoroughly checked and cleared. Ventilation Control : Ensure that the cleanroom’s ventilation system is functioning properly. If the contamination event originated from air handling systems, ventilation should be reconfigured to isolate the affected area and limit the spread of contaminants. 3. Follow Established Contamination Control Procedures Handling contamination events in a cleanroom requires adherence to established protocols that aim to reduce contamination and prevent future occurrences. These steps include: Stop Work Protocols : When contamination occurs, stop work immediately to prevent the spread of contaminants. This may involve halting production, research, or packaging processes. Decontamination Protocols : Once the source of contamination is isolated, begin decontaminating the area. This includes cleaning and disinfecting surfaces, equipment, and materials. Follow the proper decontamination procedures for the specific type of contamination (e.g., particulate, microbial, chemical). Air Quality Assessment : Utilize air monitoring systems to assess the level of contamination and determine whether additional filtration or cleaning systems are required to restore air quality to acceptable levels. These procedures must be documented in accordance with cleanroom operational protocols and regulatory requirements, ensuring transparency and accountability in the event of a contamination incident. Post-Incident Actions and Corrective Measures Once a contamination event or violation has been contained and cleaned, the next step is to investigate the cause, implement corrective actions, and restore cleanroom conditions. It is essential to focus on both short-term recovery and long-term improvements. 1. Conduct Root Cause Analysis A thorough investigation into the root cause of the contamination event or violation is essential to prevent recurrence. Root cause analysis (RCA) helps to identify the underlying factors that contributed to the incident. The investigation process should involve: Reviewing Cleanroom Logs and Procedures : Check the cleanroom’s operational logs and review the procedures followed leading up to the event. This will help identify whether there were lapses in protocol or operational failures. Personnel Interviews : Speak with cleanroom staff to gather insights into their actions, mistakes, or deviations from protocol that may have led to the violation or contamination. Equipment and System Checks : Ensure that equipment such as HVAC systems, particle counters, and sterilization equipment was functioning properly before and after the event. Once the root cause is identified, corrective actions can be implemented. 2. Implement Corrective and Preventive Actions (CAPA) Corrective and preventive actions (CAPA) are critical to addressing the underlying issues and ensuring that contamination events do not happen again. After identifying the root cause, take the following actions: Corrective Actions : These are immediate actions taken to address the specific incident. For example, if contamination was caused by improper gowning practices, corrective actions might involve re-training personnel on proper gowning protocols and reinforcing adherence to cleanroom protocols. Preventive Actions : These are measures designed to prevent future occurrences. For example, if contamination was caused by equipment malfunction, preventive actions might involve regular calibration and maintenance schedules for the affected equipment. Implementing CAPA is critical not only to address the immediate issue but also to prevent similar incidents in the future. These actions should be documented thoroughly and followed up with regular audits and reviews. 3. Communicate with Regulatory Bodies and Stakeholders Depending on the severity of the contamination event or cleanroom violation, it may be necessary to inform regulatory bodies such as the Food and Drug Administration (FDA), European Medicines Agency (EMA), or local health authorities. This is especially true in regulated industries like pharmaceuticals, biotechnology, or medical device manufacturing, where non-compliance could affect product safety or public health. Ensure transparent communication with stakeholders, including management, customers, and supply chain partners. This is crucial for maintaining trust and ensuring that all affected parties are informed of the incident, the investigation, and the corrective measures taken. 4. Review and Update Cleanroom Protocols Following a contamination event, it is essential to review and update cleanroom protocols and procedures. This ensures that any weaknesses or gaps identified during the investigation are addressed. This may include: Revising standard operating procedures (SOPs) for cleanroom operations, gowning, equipment handling, and cleaning. Updating training materials and conducting refresher training for all cleanroom personnel. Implementing new technologies, such as more advanced air filtration systems or enhanced contamination monitoring systems, to prevent future violations. Continuous improvement is key to ensuring that the cleanroom environment meets stringent standards and operates efficiently. Conclusion Cleanroom violations and contamination events, though rare, present serious risks to the integrity of the cleanroom environment and the quality of the products or research being conducted. Handling these events swiftly, thoroughly, and systematically is essential for maintaining a high level of contamination control and ensuring continued compliance with industry standards. By following a structured approach to containment, root cause analysis, corrective and preventive actions, and post-incident communication, organizations can mitigate the risks associated with contamination events and improve their overall cleanroom protocols. Through vigilance, training, and continuous improvement, cleanrooms can remain effective in maintaining the sterility and precision needed for industries that depend on these controlled environments.
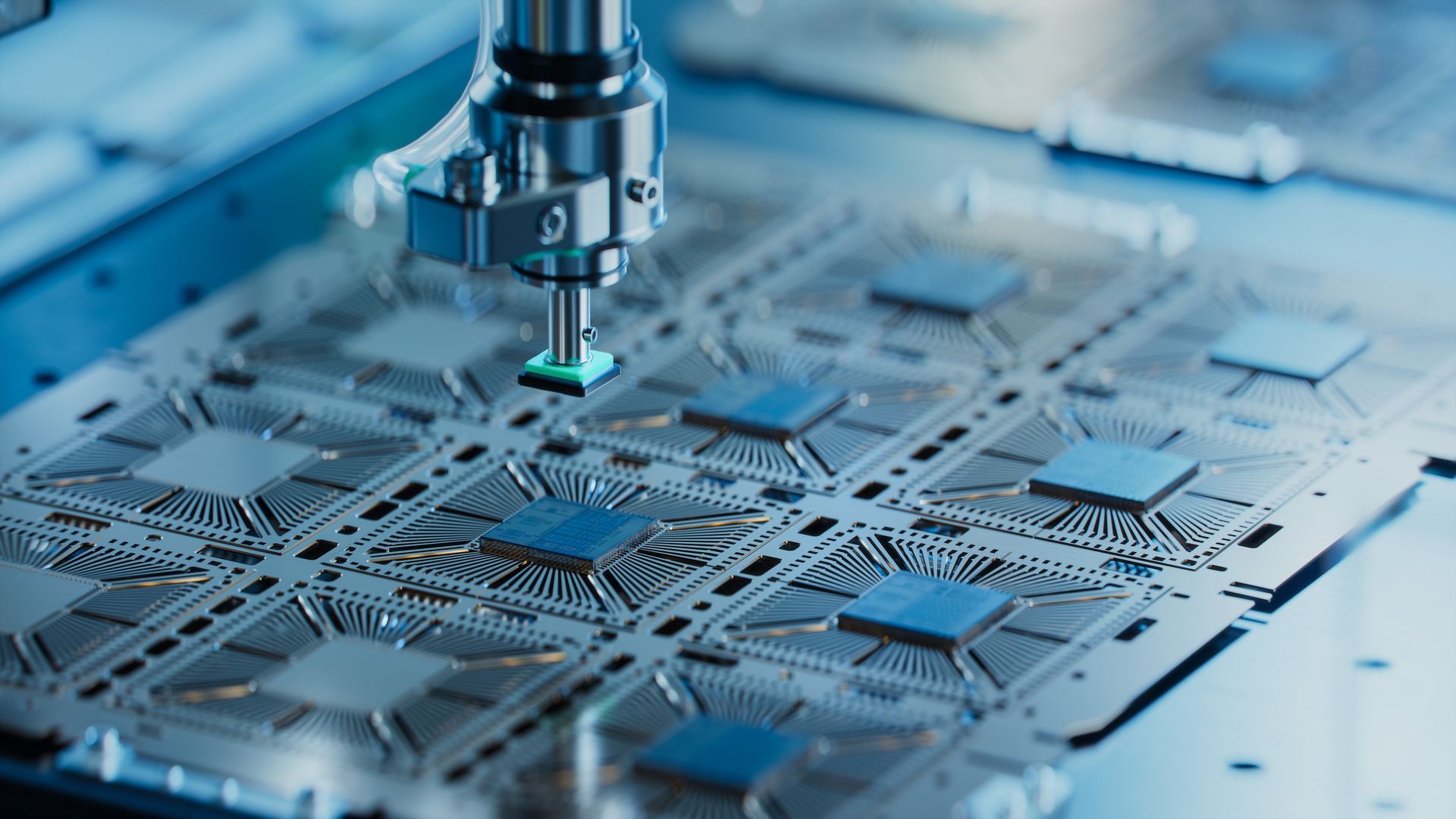
Introduction Electrostatic discharge (ESD) is a phenomenon that occurs when there is a sudden flow of electricity between two electrically charged objects. This discharge can be incredibly damaging, especially in environments that handle sensitive electronic components or biological materials. Cleanrooms, which are meticulously controlled environments used for various applications like semiconductor manufacturing, pharmaceuticals, biotechnology, and medical device production, must be designed to control all potential sources of contamination. ESD is one of the most critical factors in maintaining the integrity of cleanroom processes and the safety of the equipment and materials being handled. In this article, we will delve into the concept of electrostatic discharge, its impact on cleanroom environments, the best practices for controlling ESD, and the technologies used to prevent its occurrence in sensitive areas. Understanding the complexities of ESD and its control is essential for ensuring the quality, safety, and efficiency of cleanroom operations, particularly in industries dealing with advanced electronics, sensitive biological research, or high-precision manufacturing. What is Electrostatic Discharge (ESD)? Electrostatic discharge refers to the sudden transfer of electrostatic charge between two objects of different electrical potentials. This can happen when one object, often a human body, carries an electrostatic charge and comes into contact with another object, like a piece of sensitive electronic equipment or a semiconductor wafer. The charge transfer that occurs during ESD can result in short circuits, malfunctioning devices, or permanent damage to components that cannot be repaired. In cleanrooms, where precision is critical, and equipment must perform at optimal levels, even the smallest ESD event can have disastrous consequences. For example, in semiconductor manufacturing, a single static discharge could render an entire wafer batch unusable, leading to financial losses and delays in production schedules. In the pharmaceutical or medical device industry, the presence of static electricity could cause contamination or negatively affect the quality of drugs, devices, or biological samples. The Impact of ESD on Cleanrooms The impact of ESD in cleanrooms can be far-reaching, affecting both the safety of workers and the quality of the products or research being conducted. Some of the main risks of ESD in cleanroom environments include: Damage to Electronic Components : In cleanrooms, especially in industries like semiconductor manufacturing, electronics, and aerospace, ESD is one of the leading causes of damage to sensitive components. Modern electronic devices are increasingly smaller and more complex, with increasingly delicate circuits. Static electricity can destroy or degrade the functionality of integrated circuits, transistors, microchips, and other critical components, leading to failed products and costly losses. Contamination Risk : In certain cleanroom environments, such as those used in the pharmaceutical or biotechnology sectors, ESD can create sparks that ignite combustible or flammable substances. This poses a serious safety risk, especially in areas where hazardous chemicals or volatile compounds are used or stored. Additionally, uncontrolled ESD can lead to the movement of particles, which can interfere with sterile processes or experiments, further compromising the cleanliness of the environment. Loss of Product Yield : In semiconductor manufacturing, even a single ESD event can result in the loss of entire product batches. Given the high value of materials and components, the financial implications of an ESD-induced failure can be significant. For example, a microchip that is subjected to an ESD event might be rendered useless, forcing manufacturers to discard it and start the production process over. Inconsistent Test Results : In laboratories that rely on controlled environments, such as research labs in biotechnology or pharmaceuticals, ESD can introduce unpredictable variables into experiments. For example, in cell culture research, sensitive biological samples can be affected by minor static charges that disrupt the growth of cells or alter experimental results. This can lead to unreliable data, delays in research, and, in some cases, the need to repeat entire experimental procedures. Best Practices for Controlling ESD in Cleanrooms Controlling electrostatic discharge in cleanrooms is a comprehensive effort that requires the integration of various technologies, design elements, and operational practices. Cleanroom environments should be designed to minimize the accumulation and discharge of static electricity, and personnel should be trained to follow proper procedures to prevent static buildup. Here are several best practices to control ESD effectively: 1. Control of Ambient Humidity One of the most effective ways to reduce the buildup of static electricity in cleanrooms is through the careful management of humidity levels. Electrostatic charges are more likely to accumulate in environments with low humidity, as the lack of moisture in the air allows the static charge to build up and discharge more readily. By increasing humidity levels to a range of 40-60%, static buildup can be minimized. Many cleanrooms, particularly in industries like electronics and pharmaceuticals, use humidifiers as part of their HVAC systems to maintain the desired humidity levels. Proper control of temperature and humidity not only reduces static electricity but also improves overall air quality, which is important for maintaining a clean environment. 2. Anti-Static Flooring Flooring is a critical element in controlling ESD in cleanrooms. The materials used in cleanroom floors must be selected based on their ability to dissipate static charges and prevent static buildup. Anti-static and conductive flooring options, such as vinyl and rubber with conductive additives, are commonly used to control ESD in cleanrooms. Conductive Floors : Conductive flooring allows static electricity to travel safely to the ground, preventing static charges from accumulating on surfaces or equipment. Static-Dissipative Floors : These floors offer a slightly slower dissipation of charge, providing a safe environment for sensitive electronic components while minimizing the risk of electrical discharge. It is essential to ground the flooring system correctly to ensure that any accumulated static charges are safely directed away from critical equipment and personnel. 3. ESD-Safe Workstations and Furniture Workstations and furniture in cleanrooms must also be designed to minimize static buildup. Anti-static or ESD-safe work surfaces and chairs are commonly used to prevent electrostatic charge accumulation during work. These workstations are often equipped with grounding straps, which provide a pathway for any built-up static electricity to be safely discharged to the ground. Other ESD-safe equipment, such as ionizers, are also used to neutralize static charges in the work area. Ionizers generate ions that balance out the charge differential between objects, ensuring that static buildup does not reach dangerous levels. 4. Personal Protective Equipment (PPE) Personnel working in cleanrooms must wear appropriate personal protective equipment to prevent the introduction of static charges into the environment. This includes: ESD Wrist Straps : These wrist straps are designed to discharge any static electricity that may accumulate on a person’s body. They should be worn at all times when working with sensitive electronic components or equipment. ESD Gloves : Non-static generating gloves are essential to prevent the transfer of static electricity from human hands to products or work surfaces. Conductive Footwear : Anti-static or conductive footwear is crucial in maintaining a constant grounding path for personnel, preventing the buildup of static charges as they move around the cleanroom. Proper training and awareness of static control practices are critical for personnel to minimize the risks associated with ESD. Workers should be educated on the importance of ESD control, how to handle sensitive equipment, and how to use anti-static clothing and accessories effectively. 5. Ionization Systems Ionization systems are often installed in cleanrooms to neutralize static charges in the air. These systems generate ions, which help neutralize charged surfaces by balancing the electrical charge, thereby preventing static buildup. Ionizers are particularly useful in areas where humidity levels cannot be easily controlled or in processes that require extremely low levels of contamination. Ionization is especially critical in environments where sensitive electronic components are handled, such as semiconductor fabrication or assembly lines for consumer electronics. In these environments, the presence of any static charge can lead to costly damage to microchips, circuit boards, or other components. 6. ESD-Safe Packaging For cleanrooms involved in electronics assembly or semiconductor manufacturing, packaging materials must also be ESD-safe to protect sensitive components during transport and storage. Conductive or static-dissipative materials, such as antistatic bags, trays, and boxes, are used to ensure that components are not exposed to static charges. Monitoring and Maintenance To ensure that ESD control measures remain effective, cleanroom environments must be regularly monitored and maintained. This includes: Routine Grounding Inspections : Periodic checks of the grounding system (including floors, workstations, and personnel equipment) are essential to ensure that all components are properly grounded. Air Quality and Humidity Monitoring : Environmental monitoring systems should be installed to track humidity levels, temperature, and static charge buildup in real-time. This ensures that conditions remain optimal for controlling ESD and minimizing risks to sensitive equipment. Training and Protocols : Cleanroom personnel should undergo regular training on ESD control protocols, including handling ESD-sensitive equipment, using proper PPE, and understanding the risks associated with electrostatic discharge. Conclusion Controlling electrostatic discharge in cleanrooms is a critical component of maintaining the integrity of sensitive materials, equipment, and processes. ESD can cause irreparable damage to electronic components, lead to contamination in sterile environments, and even cause safety hazards. Through proper design, careful material selection, and the implementation of best practices, cleanrooms can effectively control ESD and minimize its impact on operations. By controlling ambient humidity, installing anti-static flooring, utilizing ESD-safe workstations, equipping personnel with proper protective gear, and using ionization systems, cleanroom operators can create an environment that minimizes the risks associated with electrostatic discharge. With continued monitoring and maintenance, cleanrooms can ensure that the integrity of research, manufacturing, and production processes remains intact, supporting industries where precision and safety are paramount. Read more: All About Cleanrooms - The ultimate Guide
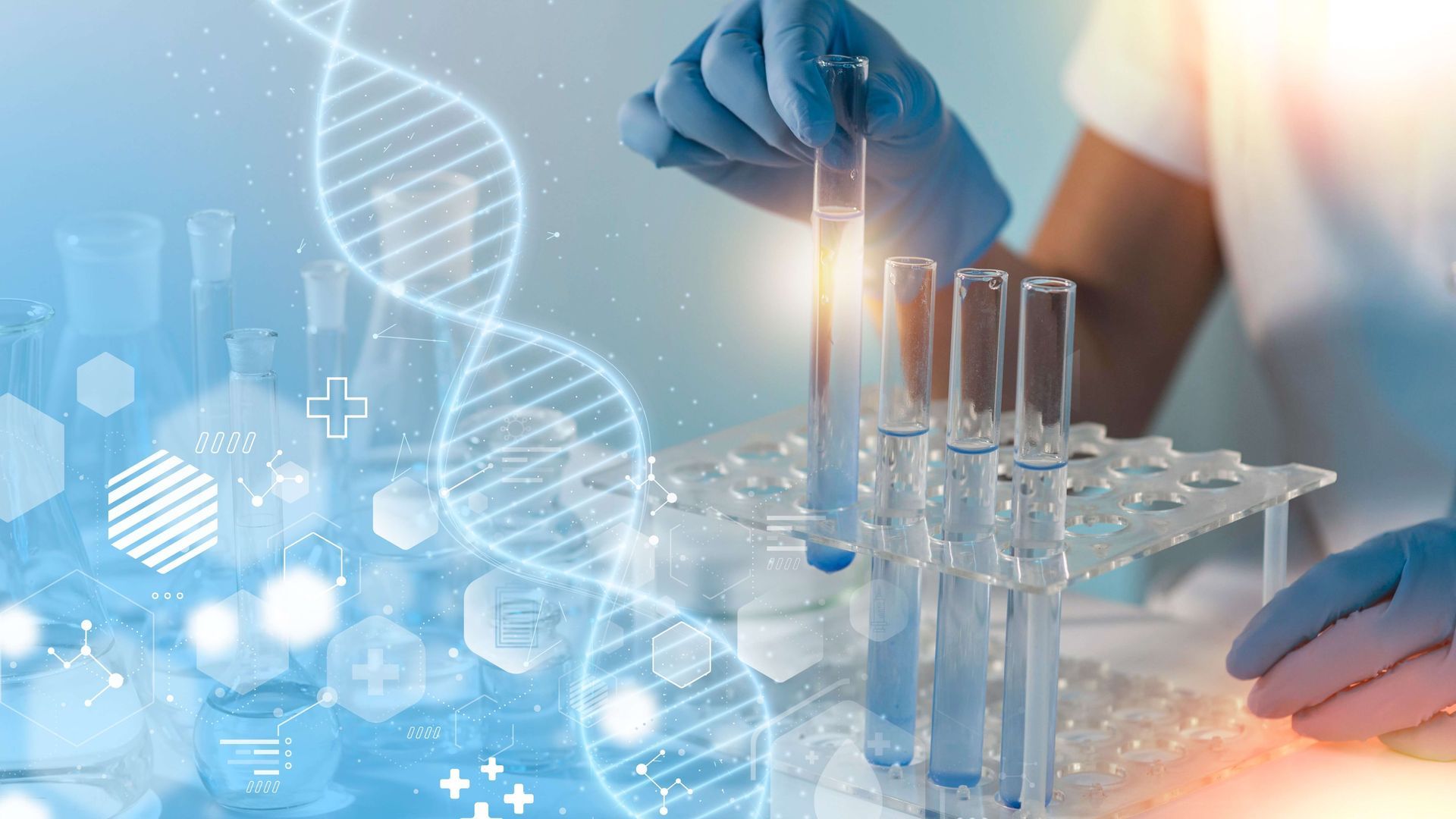
Introduction Biotechnology is one of the most innovative and rapidly advancing fields, spanning diverse areas including pharmaceuticals, genetic research, agricultural development, and environmental biotechnology. As the field pushes the boundaries of scientific discovery, the need for specialized environments that can maintain the highest levels of sterility and precision becomes even more critical. This is where cleanrooms come into play. In biotechnology research, cleanrooms provide a controlled environment that ensures the integrity of experiments, the safety of research subjects, and the consistency of results. These environments are specifically designed to minimize contamination from airborne particles, microorganisms, and other potential pollutants, which is essential for ensuring the validity and success of biotechnology research. In this article, we will explore the role of cleanrooms in biotechnology research, the specific functions they serve, the types of research that benefit from cleanroom environments, and the various standards and technologies used to maintain the necessary conditions for cutting-edge biotechnological advancements. What is a Cleanroom? A cleanroom is a controlled environment where the level of contamination by particles, chemicals, and microorganisms is minimized to the greatest extent possible. Cleanrooms use specialized ventilation systems, air filtration methods, and carefully designed structures to maintain these sterile conditions. The goal of a cleanroom is to provide an environment that supports the integrity and safety of sensitive processes and materials, whether in a laboratory, manufacturing facility, or research space. Cleanrooms are classified based on the concentration of airborne particles, with standards such as ISO 14644-1 categorizing them into different classes. The lower the class number, the cleaner the room. For example, ISO Class 5 is a very clean environment, suitable for delicate and high-precision work, while ISO Class 7 or 8 may suffice for less critical tasks. In biotechnology research, the need for cleanrooms is particularly vital because biological materials, experiments, and equipment are highly susceptible to contamination, which could lead to inaccurate results or failed experiments. The Importance of Cleanrooms in Biotechnology Research Biotechnology research often deals with sensitive materials such as cell cultures, viruses, DNA, proteins, and other biological substances that require highly controlled conditions to thrive. Even the smallest contaminant can disrupt biological processes, compromise results, or introduce harmful pathogens that could skew data. This is why the role of cleanrooms in biotechnology research cannot be overstated. 1. Minimizing Contamination Risks Biotechnological experiments, especially those involving genetic engineering or tissue culture, are highly sensitive to contamination. A single particle of dust, a microorganism, or an uncontrolled variable could lead to faulty results, affecting not only the quality of the research but also the safety of products derived from this research. Cleanrooms mitigate these risks by offering a controlled environment where contaminants from air, surfaces, or personnel are minimized. Contaminants can come from many sources: human skin cells, hair, clothing, the materials being used in research, and even airborne bacteria or mold. Cleanrooms maintain air quality by using HEPA (High-Efficiency Particulate Air) or ULPA (Ultra-Low Penetration Air) filters, which can trap particles as small as 0.3 microns. This ensures that the research environment remains free of contaminants that could compromise the biological materials under study. 2. Ensuring Safe Handling of Biological Materials In biotechnology research, it is not only the environment that must be clean, but also the handling and manipulation of biological materials. Cleanrooms provide the safety needed to manage potentially dangerous substances, such as genetically modified organisms (GMOs), pathogens, or toxic chemicals, without risking contamination. The strict sterilization processes and air filtration systems help reduce the risks associated with handling hazardous materials. For instance, in gene editing research, such as CRISPR, or in the production of genetically modified crops, cleanrooms ensure that laboratory personnel and the research itself are not exposed to harmful agents. Cleanrooms also provide containment measures to ensure that any harmful biological agents or GMOs do not accidentally contaminate the surrounding environment. 3. Optimizing Experimental Conditions Many biotechnological processes require strict environmental conditions for success. Temperature, humidity, and airflow all need to be controlled to ensure the proper growth and behavior of biological materials. For instance, cell cultures often need a very specific temperature and humidity to grow effectively, and even small changes in these factors can drastically affect the results of an experiment. Cleanrooms in biotechnology research are equipped with state-of-the-art HVAC systems that allow researchers to control the temperature, humidity, and airflow with extreme precision. These systems ensure that conditions inside the cleanroom remain within optimal ranges for biological growth or chemical reactions. This is particularly important for work involving pharmaceuticals or biopharmaceutical production, where even minor deviations can lead to the failure of experiments or loss of product batches. 4. Preventing Cross-Contamination Between Experiments Cross-contamination is a significant risk in any research environment, and cleanrooms are designed to prevent this by implementing specific airflow patterns and pressure differentials. In biotechnology research, experiments often involve the manipulation of various biological materials, each with its own unique properties and susceptibility to contamination. By utilizing specialized air filtration systems and laminar airflow designs, cleanrooms can maintain a clean environment around specific experiments and prevent cross-contamination between research materials. Cleanrooms often feature zones with different cleanliness levels, ensuring that less critical research areas do not compromise the more sterile zones. Types of Biotechnology Research That Benefit from Cleanroom Environments Biotechnology research encompasses a wide range of disciplines, many of which require cleanroom environments for their success. Some of the most notable areas of biotechnology research that benefit from cleanroom environments include: 1. Pharmaceutical and Biopharmaceutical Research Cleanrooms play an indispensable role in pharmaceutical and biopharmaceutical research, particularly in the development and production of vaccines, biologics, and gene therapies. These types of research require stringent sterility to ensure that the final product is safe for human use. Cleanrooms provide an environment where researchers can perform tasks such as cell culture, protein purification, or drug formulation without worrying about contamination from airborne particles or pathogens. Additionally, the production of sterile injectable drugs, medical devices, and diagnostic tools also requires cleanroom environments to prevent contamination during manufacturing. Cleanrooms ensure that all surfaces, air, and personnel are properly sanitized, minimizing the risk of product contamination that could lead to health hazards. 2. Genetic Engineering and CRISPR Research Research involving genetic modification, particularly using tools like CRISPR (Clustered Regularly Interspaced Short Palindromic Repeats), is highly sensitive and must be conducted in highly controlled environments. Cleanrooms provide the controlled conditions necessary to maintain the integrity of genetic material and the accuracy of gene-editing techniques. Any contamination during genetic modification could lead to inaccurate results, poor experimental outcomes, or the accidental introduction of unintended genetic material. Cleanrooms in genetic engineering research also help protect researchers from exposure to potentially hazardous materials such as viruses or genetically altered microorganisms, providing a safer working environment. 3. Cell and Tissue Culture Research In biotechnology, cell and tissue culture are foundational techniques used in areas such as drug discovery, regenerative medicine, and cancer research. These delicate biological systems require strict environmental control, including optimal temperatures, humidity, and sterile conditions. Cleanrooms help provide the perfect environment for these cultures to thrive and ensure that they remain free from contaminants that could affect their growth or lead to false results. 4. Microbial Research and Fermentation Microbial biotechnology, which includes areas like fermentation and the study of microorganisms for the production of biofuels, enzymes, and antibiotics, benefits greatly from cleanroom conditions. Microbial cultures and fermentation processes are highly sensitive to contamination, and cleanrooms provide the necessary environment to ensure that experiments proceed without interference from outside sources. In these environments, cleanrooms ensure that unwanted microorganisms do not contaminate the research cultures, leading to invalid results or unintentional bacterial growth that could damage experiments or contaminate the final products. Maintaining Cleanroom Standards in Biotechnology Research In biotechnology research, cleanrooms are maintained according to strict standards to ensure they are effective in reducing contamination risks. These standards typically involve: ISO Classification : Cleanrooms are classified based on the number of particles allowed per cubic meter of air. For high-precision biotechnology work, rooms must meet stringent ISO 5 or ISO 6 standards, with very low levels of particulate contamination. Environmental Monitoring : Regular monitoring of temperature, humidity, pressure, airflow, and particle levels is critical to ensure the cleanroom remains within required specifications. Sterilization Protocols : Frequent cleaning and sterilization of surfaces, equipment, and air filtration systems are necessary to ensure that no biological contaminants remain in the environment. Personal Protective Equipment (PPE) : Personnel working in cleanrooms must wear specialized protective gear, including gowns, gloves, face masks, and hair coverings, to prevent contamination from human sources. Conclusion Cleanrooms play a vital role in biotechnology research by providing the sterile and controlled environments necessary to ensure the integrity of experiments, the safety of biological materials, and the quality of final products. With applications ranging from pharmaceutical production to genetic engineering and microbial research, cleanrooms support critical biotechnology advancements by minimizing contamination risks, optimizing experimental conditions, and maintaining the safety of researchers. As the field of biotechnology continues to evolve and expand, cleanrooms will remain integral to the success of research efforts, ensuring that the groundbreaking discoveries made in these environments are safe, effective, and reproducible. With the continuing emphasis on precision and safety, cleanroom technology and design will likely evolve further to meet the challenges of tomorrow’s biotechnology innovations. Read more: All About Cleanrooms - The ultimate Guide

Introduction In industries such as pharmaceuticals, biotechnology, semiconductor manufacturing, aerospace, and medical devices, maintaining a contamination-free environment is essential. Cleanrooms are critical spaces where environmental conditions must be meticulously controlled to prevent contamination from airborne particles, microorganisms, and other potential pollutants. The cleanliness of a cleanroom is often the determining factor in ensuring the quality and safety of sensitive products, research, or manufacturing processes. While many cleanroom designs focus on elements like air filtration, temperature and humidity control, and gowning procedures, cleanroom furniture also plays a vital role in maintaining the integrity of the controlled environment. The design and material selection for cleanroom furniture are crucial considerations because they can influence how easily the room can be cleaned, the level of particle generation, and the overall functionality of the space. In this article, we will dive into the importance of cleanroom furniture, factors influencing its design, and the best materials to use in cleanroom environments. We will explore how furniture design and material selection contribute to maintaining cleanliness, safety, and operational efficiency in cleanrooms. The Role of Furniture in Cleanroom Environments Cleanroom furniture includes a variety of items, such as workbenches, chairs, shelves, storage cabinets, carts, and other pieces used by personnel to support tasks in the controlled space. Furniture in cleanrooms is different from typical office or industrial furniture due to its unique demands. In cleanrooms, all furniture needs to be: Easily Cleanable : Furniture should not trap dust, particles, or microorganisms that could contaminate the cleanroom environment. Smooth, non-porous surfaces that are easy to clean and disinfect are essential. Particle-Free : Furniture in cleanrooms should generate as few particles as possible. Materials with low particle shedding are preferred to prevent the introduction of contaminants. Durable : Cleanroom furniture must withstand frequent cleaning, chemicals, temperature variations, and heavy usage while maintaining its functionality and structural integrity. Non-Reactive : Furniture materials should be non-reactive to chemicals and other substances used in cleanrooms. Some materials may react with cleaning agents or chemicals in ways that could lead to contamination or degradation. Safe and Ergonomic : The furniture design should support safe, comfortable working conditions for personnel. Ergonomic considerations are especially important for workers who may spend long hours in the cleanroom. Key Considerations in Cleanroom Furniture Design When designing cleanroom furniture, several factors need to be taken into account to ensure that the furniture supports the cleanroom’s primary functions while minimizing the potential for contamination: 1. Functionality and Layout The design of the furniture should align with the specific processes carried out in the cleanroom. For example, in semiconductor fabrication, workbenches must be designed to support the delicate assembly and testing of microelectronic components, while in pharmaceutical cleanrooms, furniture must facilitate the handling and preparation of sterile drug formulations. Workbenches and Tables : The size, shape, and height of workbenches must be optimized for the tasks being performed. Work surfaces must be spacious enough to accommodate equipment and materials while allowing for easy access and movement. Shelving and Storage : Shelving and storage units should be designed to hold materials and equipment in an organized, easily accessible manner. Shelves and cabinets should have smooth, sealed surfaces to prevent dust and particle accumulation. Additionally, storage units may need to be specially designed to handle chemicals or hazardous materials in specific industries, like pharmaceuticals or biotechnology. Carts and Mobile Furniture : For flexibility and ease of movement, cleanroom carts and other mobile furniture are often used. These pieces must be easy to maneuver and clean and should be designed to reduce the potential for cross-contamination. 2. Material Selection The choice of materials for cleanroom furniture is one of the most important factors in the design process. The materials must meet several stringent requirements, including being durable, easy to clean, non-reactive, and resistant to the harsh cleaning agents commonly used in cleanroom environments. Some of the most common materials used in cleanroom furniture include: 1. Stainless Steel Stainless steel is one of the most widely used materials for cleanroom furniture, particularly in workbenches, storage units, and equipment racks. It is valued for its durability, resistance to corrosion, and ease of cleaning. Stainless steel does not absorb contaminants, making it an ideal material for environments where cleanliness is paramount. Advantages of Stainless Steel : Highly resistant to chemicals and corrosion Easy to clean and maintain Non-porous, preventing the absorption of contaminants Considerations : Can be prone to scratching, which may allow particles to accumulate in the scratches Cold to the touch, which may be uncomfortable in some cleanroom settings 2. Aluminum Aluminum is another popular material for cleanroom furniture. It is lighter than stainless steel but still offers many of the same benefits, such as durability, resistance to corrosion, and ease of cleaning. Advantages of Aluminum : Lightweight and easy to handle Resistant to corrosion and rust Cost-effective compared to stainless steel Considerations : Not as durable as stainless steel and may not withstand harsh chemicals as well Can be more prone to denting or bending under heavy use 3. Plastic and Polymer Materials Plastic and polymer materials, such as polypropylene, polycarbonate, and high-density polyethylene (HDPE), are commonly used in cleanroom furniture, especially for shelves, drawers, and smaller storage units. These materials are lightweight, non-porous, and resistant to chemical corrosion. Advantages of Plastic/Polymer Materials : Lightweight and cost-effective Resistant to chemicals and moisture Easy to clean and maintain Considerations : May not offer the same level of durability and strength as metals like stainless steel May not provide adequate static protection for sensitive electronic work 4. Laminate Surfaces Laminate surfaces are often used for work surfaces and countertops in cleanrooms. These surfaces can be made from materials such as phenolic resin or melamine, which provide a durable, non-porous, and easy-to-clean surface. Advantages of Laminate Surfaces : Essential for electronics, semiconductor, and other ESD-sensitive environments Prevents the buildup of harmful static charges Considerations : The effectiveness of antistatic coatings may degrade over time and with wear Can add to the overall cost of the furniture 5. ESD-Safe Materials I n cleanrooms where electrostatic discharge (ESD) could damage sensitive equipment, furniture must be designed to minimize static buildup. Furniture made from materials with antistatic or conductive properties, such as ESD-safe mats, chairs, and workstations, is critical in environments like semiconductor manufacturing. Advantages of ESD-Safe Materials : Aesthetic appeal in non-critical areas Easy to work with and can be shaped into custom designs Considerations : Porous and difficult to clean thoroughly in high-contamination risk areas Susceptible to warping or damage when exposed to moisture or chemicals Specialized Cleanroom Furniture Designs In addition to general furniture items like tables, chairs, and shelving, cleanroom environments may require specialized furniture for unique tasks or environments. Some of these include: ESD-Safe Workbenches : These workstations are equipped with special materials or coatings that prevent electrostatic charge buildup, which is vital for electronics and semiconductor manufacturing. Ergonomic Seating : Cleanroom chairs are designed for comfort and safety, particularly in settings where workers spend long hours. They often feature adjustable components and materials that minimize particle release while providing maximum support. Customizable Storage Units : Cleanroom storage units often feature specialized shelving, drawers, and compartments designed for easy cleaning, particle control, and optimal organization. Conclusion The design and material selection of cleanroom furniture are integral to the success of a cleanroom's operation. Choosing the right materials and ensuring furniture is functional, durable, and easy to clean are key factors that contribute to the overall cleanliness, safety, and efficiency of the environment. Whether opting for stainless steel for its durability, plastic for its versatility, or specialized materials for static control, the proper selection of materials can help mitigate contamination risks and improve worker comfort. By considering factors such as particle generation, chemical resistance, and ergonomic needs, businesses can ensure their cleanroom furniture meets the highest standards and plays a critical role in maintaining a controlled, sterile environment conducive to the specific needs of their industry. Read more: All About Cleanrooms - The ultimate Guide
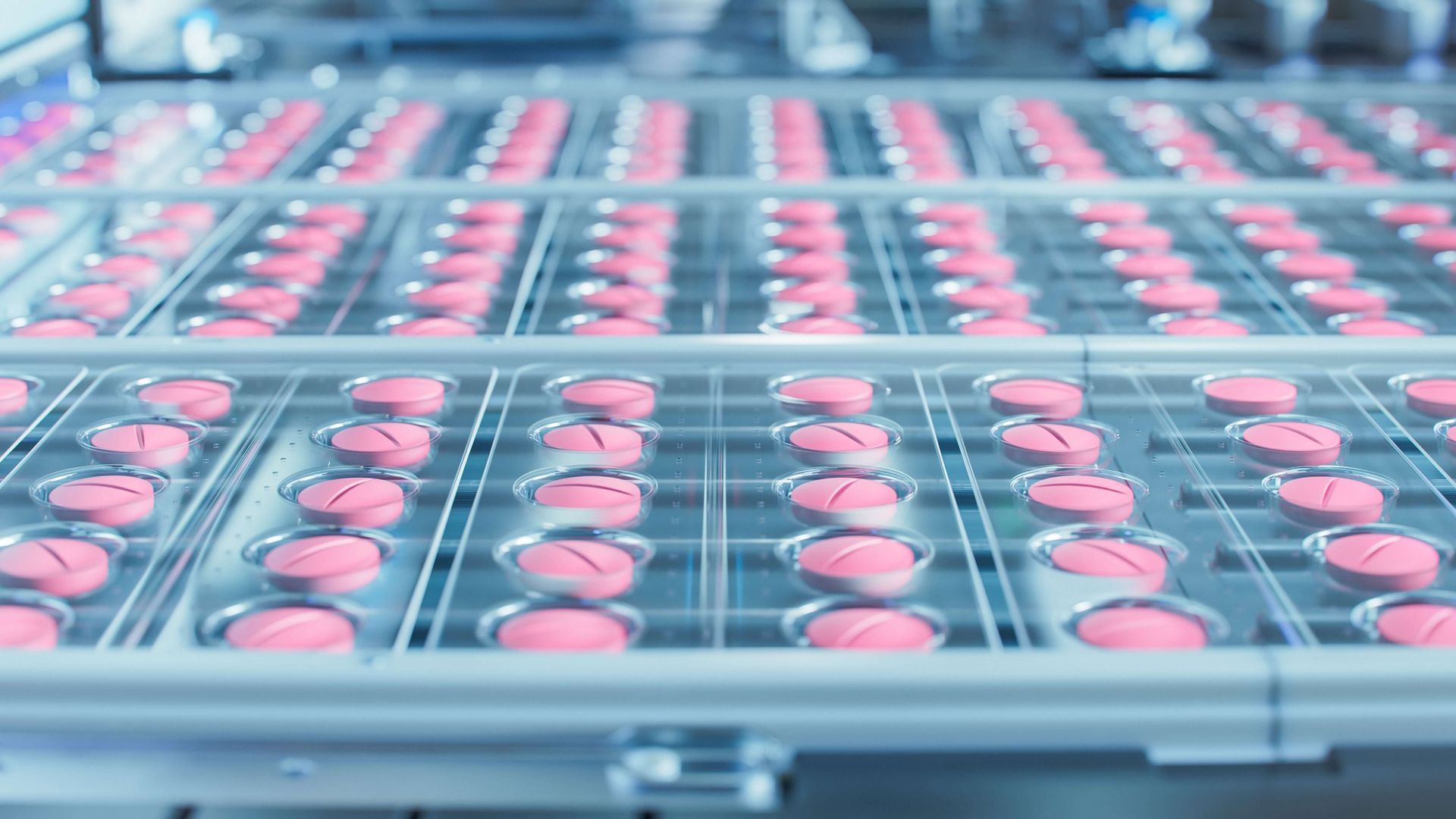
Introduction Cleanrooms are controlled environments designed to minimize contamination risks and maintain the highest standards of cleanliness. Industries such as pharmaceuticals, biotechnology, aerospace, semiconductor manufacturing, and medical devices rely on these spaces to ensure the safety, efficiency, and quality of their processes and products. One of the most critical aspects of cleanroom design is the management of airflow patterns. Proper airflow patterns ensure that particulate contamination is minimized, clean air is evenly distributed, and the cleanroom environment remains effective in preventing contamination. In this article, we will explore why air flow patterns are so important in cleanroom design, how they influence contamination control, and the strategies used to optimize air flow in cleanrooms to meet stringent industry standards. Understanding Cleanroom Air Flow Air flow patterns in a cleanroom refer to how air circulates throughout the space, from its entry into the room to its exit. The flow of air directly impacts how contaminants—such as particles, dust, or microorganisms—are carried and removed from the environment. Airflow also affects the room's pressure, temperature, humidity, and, ultimately, its classification according to standards like ISO 14644-1. The main goal of airflow design in a cleanroom is to ensure that particles generated within the cleanroom, whether from equipment, materials, or personnel, are swiftly removed without contaminating the workspace or settling onto sensitive products. Proper air flow patterns achieve this by directing contaminated air out of the cleanroom, replacing it with clean, filtered air. The Role of Airflow in Cleanroom Contamination Control Contamination control is one of the core functions of cleanroom airflow design. In cleanrooms, contamination can originate from several sources: Personnel : Workers in cleanrooms, even with protective gowns and gear, can shed skin cells, hair, and particles. Proper airflow ensures that these particles are removed from the workspace before they have a chance to settle on surfaces or products. Equipment and Materials : Cleanroom equipment, machinery, and materials may also generate particulate contamination. Efficient airflow ensures that particles generated by these sources are quickly carried away from sensitive areas. External Contamination : Airflow patterns can also help control the ingress of contaminants from external sources, such as ventilation systems or the air outside the cleanroom. Ensuring a proper differential pressure between the cleanroom and adjacent areas reduces the risk of contaminants entering the cleanroom from uncontrolled spaces. By designing air flow to remove particles from critical areas efficiently, cleanroom designers help ensure the integrity and sterility of the products being manufactured or processed. Types of Airflow Patterns in Cleanroom Design There are several types of airflow patterns commonly used in cleanroom design, each of which plays a different role in particle control and cleanroom performance: 1. Laminar Flow Laminar flow is one of the most commonly used airflow patterns in cleanrooms, particularly in environments where the risk of contamination is high, such as pharmaceutical manufacturing or semiconductor fabrication. In laminar flow, air moves in parallel layers with minimal disruption between them. This flow pattern is characterized by smooth, unidirectional movement, which helps sweep contaminants away from sensitive areas. Laminar flow can be horizontal or vertical, depending on the cleanroom's design. Vertical Laminar Flow : In vertical laminar flow, air is drawn from the ceiling and moves downward toward the floor. This type of flow is most common in cleanrooms where sensitive products or processes are located near the floor, such as in assembly areas or packaging areas. The air is typically filtered through HEPA (High-Efficiency Particulate Air) or ULPA (Ultra-Low Penetration Air) filters before being introduced into the cleanroom to ensure the highest possible level of air purity. Horizontal Laminar Flow : In horizontal laminar flow, air is drawn into the cleanroom from one side and moves horizontally across the room, typically towards an exhaust vent or filtration system. This design is often used in areas where large equipment or workbenches are placed along one side of the room. Advantages of Laminar Flow: Effective in sweeping airborne particles away from critical areas. Minimizes turbulence that could disturb the particulate settling in sensitive areas. Provides consistent air distribution across the cleanroom, ensuring all areas receive a uniform level of air cleanliness. Considerations: It requires precise control over airflow to ensure that particles are continually removed. Potential inefficiency in rooms with a large number of obstructions or complex layouts, as airflow might not reach all areas efficiently. 2. Turbulent Flow Turbulent flow, on the other hand, is less controlled than laminar flow and results in chaotic air movement. This flow pattern is typically found in environments where contamination is less critical, such as in low-ISO cleanrooms (ISO 7 and 8), or in support areas like storage rooms. While turbulent flow is less efficient at removing particles from critical areas, it can still play an important role in larger, more open spaces or less-sensitive parts of the cleanroom. The air will still eventually be filtered, but the air moves more erratically compared to laminar flow. Advantages of Turbulent Flow: Easier to implement in larger or less critical areas of a cleanroom. Can be used in non-production areas where contamination control requirements are less stringent. Considerations: Less effective at maintaining uniform cleanliness in areas where contamination is critical. Can lead to stagnant air pockets, where particles can accumulate. 3. Unidirectional Flow Unidirectional flow, often used in combination with laminar flow, refers to a specific type of air circulation where the airflow is directed in one consistent direction. Unidirectional airflow is designed to ensure that contaminants are constantly being directed out of the cleanroom, and it is typically used in spaces like clean benches, isolators, or controlled workstations. This airflow system combines laminar flow principles with the continuous movement of air to create a highly controlled, sterile environment in areas where very high standards are required. Advantages of Unidirectional Flow: Perfect for maintaining a highly sterile environment for critical processes such as drug compounding or electronics manufacturing. Reduces the potential for cross-contamination between workers or workstations. Considerations: Requires careful design and placement of air supply and exhaust systems. Generally not suitable for large-scale production areas due to its focused nature. The Importance of Airflow Patterns for ISO Cleanroom Classes Cleanroom standards, such as those set by the International Organization for Standardization (ISO 14644-1), define the cleanliness of a room based on the number of particles per cubic meter at specific sizes. As the cleanroom class decreases (i.e., from ISO 5 to ISO 8), the acceptable particle count increases, which directly impacts airflow requirements. ISO Class 1 to Class 5 : These classes require highly efficient airflow systems, including laminar flow and unidirectional airflow. The air must be filtered multiple times (often through HEPA or ULPA filters) to remove particles, and the air must be delivered in a controlled, uniform manner to avoid turbulence and particle deposition. Cleanrooms of these classes are typically used for highly sensitive processes like semiconductor manufacturing, pharmaceuticals, and biotechnology. ISO Class 6 to Class 8 : As the cleanliness standards become less strict, airflow systems can become less stringent, but they still need to ensure that contaminants are removed from critical areas. These classes are often found in industries like food packaging or less-sensitive assembly lines, where a less precise level of airflow is acceptable. Key Considerations for Designing Airflow Patterns When designing airflow patterns in a cleanroom, several factors need to be taken into account: Cleanroom Size and Layout : The size and layout of the cleanroom will influence how air flows through the space. For large rooms, multiple air handling units may be needed, and careful planning is required to ensure that airflow is evenly distributed across all critical areas. Personnel and Equipment Placement : The location of personnel and equipment will also influence air flow patterns. Workstations, machinery, and equipment should be positioned in such a way that they do not disrupt airflow or create turbulence that could lead to contamination. Airflow Velocity : The velocity of the airflow must be carefully regulated to avoid disturbing settled particles or causing turbulence that could affect contamination control. Too high a velocity can cause particulate movement, while too low a velocity may allow particles to settle back onto surfaces. Pressure Differentials : To ensure that contaminants do not enter the cleanroom, pressure differentials between the cleanroom and surrounding areas must be maintained. Positive pressure is typically used in cleanrooms to prevent the ingress of contaminated air from adjacent spaces. Filtration Systems : Filtration is a critical component of cleanroom airflow. Air entering and exiting the cleanroom must pass through high-efficiency filters, such as HEPA or ULPA, to ensure that airborne particles are removed before the air enters the cleanroom or exits to the environment. Conclusion Airflow patterns are a fundamental aspect of cleanroom design and performance. By ensuring that air circulates effectively, cleanrooms can maintain their cleanliness standards, protect product integrity, and prevent contamination from personnel, equipment, and external sources. Whether utilizing laminar flow, turbulent flow, or unidirectional flow, the proper design of airflow systems is essential for meeting ISO classification requirements and creating a safe, sterile environment for sensitive processes and products. Cleanroom designers must carefully consider factors such as room layout, airflow velocity, personnel positioning, and filtration systems to achieve the best possible airflow design for their specific application. Read more: All About Cleanrooms - The ultimate Guide
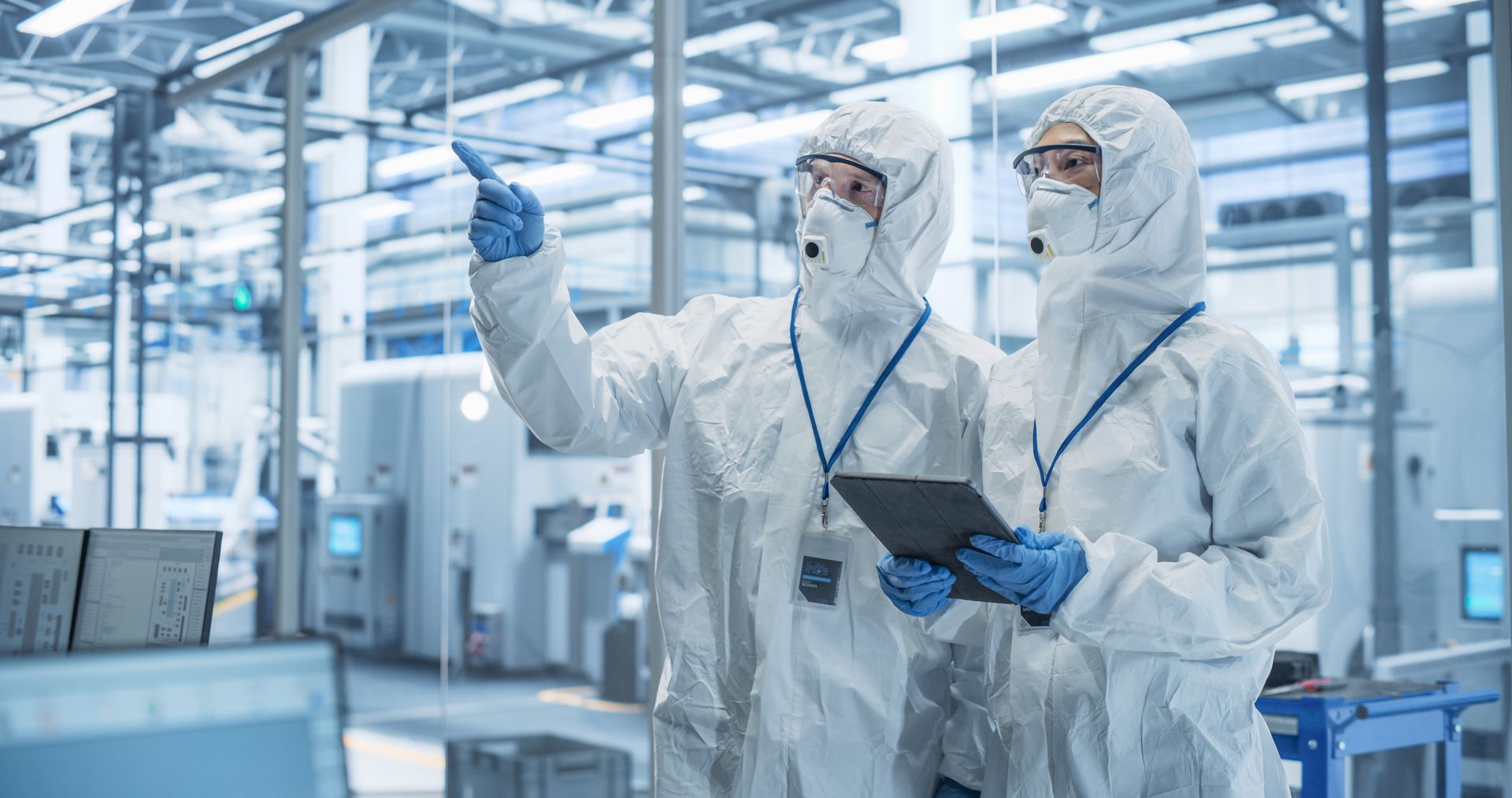
Introduction Cleanrooms are critical environments that must adhere to stringent contamination control standards, primarily to protect the integrity of sensitive processes and products. In industries like pharmaceuticals, biotechnology, aerospace, semiconductor manufacturing, and healthcare, even the smallest contaminant can have a devastating effect on product quality, safety, and regulatory compliance. While particle contamination is the most commonly discussed issue in cleanroom design, managing environmental factors such as humidity and temperature is equally essential for maintaining the desired cleanroom performance. Humidity and temperature directly impact both the cleanliness and the performance of processes within the cleanroom, influencing not only the integrity of products but also the comfort and safety of the personnel working in these controlled environments. Maintaining precise control over these factors is therefore crucial to achieving optimal cleanroom conditions. This article will explore the role of humidity and temperature in cleanroom management, the risks associated with improper control of these factors, and the strategies and technologies used to regulate temperature and humidity within cleanrooms. The Role of Humidity and Temperature in Cleanroom Performance In cleanrooms, temperature and humidity affect both the physical properties of materials and the behavior of airborne particles. Each of these factors is tightly regulated to ensure that the cleanroom maintains its classification and that processes are completed without interruption or contamination. Temperature Control Temperature control in cleanrooms is typically dictated by the processes that occur within the environment. For instance, the temperature may need to be precisely regulated in areas such as pharmaceutical compounding, semiconductor fabrication, or aerospace testing, where even slight fluctuations can lead to undesirable outcomes. Impact on Chemical Reactions : In cleanrooms where chemicals are used in manufacturing processes or research, temperature plays a critical role in the efficiency and consistency of chemical reactions. In pharmaceutical production, for example, the temperature must be controlled to ensure that drug compounds are mixed, stored, and processed at optimal temperatures, avoiding any degradation or loss of potency. Impact on Equipment : Many cleanrooms, particularly those used in semiconductor fabrication and electronics manufacturing, contain sensitive equipment that operates under strict temperature conditions. Equipment can fail or perform poorly if subjected to temperatures that are too high or too low, leading to potential damage to the machinery and compromising product quality. Thermal Expansion : In environments that deal with sensitive instruments, such as aerospace testing cleanrooms, precise temperature control is necessary to prevent thermal expansion or contraction of materials that could affect measurement accuracy, structural integrity, or functionality. Human Comfort : The temperature in cleanrooms also affects the comfort and productivity of the personnel. If the temperature is too high, workers may experience fatigue, while temperatures that are too low can lead to discomfort or even impair cognitive performance. Striking a balance between process requirements and worker comfort is essential. Humidity Control Humidity management is equally critical in maintaining the quality of processes and products in a cleanroom. Humidity levels—defined by the amount of water vapor present in the air—are crucial for several reasons: Impact on Electrostatic Discharge (ESD) : In cleanrooms dedicated to semiconductor manufacturing or electronics assembly, static electricity can wreak havoc on sensitive components. High humidity levels can help dissipate electrostatic charges by increasing the conductive properties of the air, thus reducing the risk of ESD damage. Microbial Growth and Contamination : In pharmaceutical or healthcare cleanrooms, where sterile conditions are required, humidity must be tightly controlled to prevent the growth of mold, bacteria, or other microorganisms. High humidity levels can create favorable conditions for microbial growth, while very low humidity can cause dry air that leads to particles and contaminants being more easily carried through the air. Material Properties : In industries such as aerospace or biotechnology, humidity can impact the physical properties of materials, such as polymers, adhesives, or coatings. Excessive humidity can affect the curing process of certain materials, while too little humidity can cause brittleness or cracking. Worker Comfort and Health : Similar to temperature, improper humidity levels can affect the comfort and health of personnel. High humidity can cause discomfort, fatigue, and dehydration, while low humidity can lead to dry skin, respiratory problems, and increased susceptibility to colds and other illnesses. The Risks of Improper Temperature and Humidity Control Improper regulation of temperature and humidity in cleanrooms can lead to several problems: Product Contamination : High humidity can cause condensation, which can lead to contamination on surfaces, equipment, or products. This is particularly problematic in environments such as pharmaceutical manufacturing, where sterility is paramount. Excess moisture can also cause corrosion, potentially damaging sensitive instruments. Degradation of Product Quality : In some industries, temperature and humidity must be maintained within very tight tolerances. For example, in semiconductor manufacturing, even small temperature fluctuations can affect the performance of microchips, leading to failures in product yields. Similarly, in the pharmaceutical industry, improper storage conditions can cause chemical degradation of drugs, reducing their efficacy. Compromised Process Integrity : Certain cleanroom processes, such as drug compounding, semiconductor fabrication, or coating applications, rely on very specific temperature and humidity conditions. Deviations from these conditions can lead to defects or suboptimal results, thus undermining the integrity of the manufacturing process. Health and Safety Issues : For personnel working in cleanrooms, poorly managed temperature and humidity can create an unsafe environment. Low humidity can cause discomfort and dry out respiratory passages, increasing the risk of infections. High humidity, on the other hand, can increase the likelihood of mold growth, leading to health risks for cleanroom operators. Managing Temperature and Humidity in Cleanrooms Managing temperature and humidity in cleanrooms involves several key strategies, from selecting the appropriate HVAC (Heating, Ventilation, and Air Conditioning) systems to continuous monitoring and adjustment of conditions. Below are the best practices for controlling these variables: 1. HVAC Systems for Temperature and Humidity Control Cleanrooms are typically equipped with specialized HVAC systems designed to maintain precise control over temperature and humidity levels. These systems can include: Air Handling Units (AHUs) : These units are responsible for regulating the temperature and humidity of the incoming air. They use advanced filtration and dehumidification processes to ensure that the air entering the cleanroom is free of contaminants and at the desired conditions. Humidity Control Units : In addition to standard HVAC units, many cleanrooms are equipped with dehumidifiers or humidifiers that can adjust the moisture levels in the air. These systems often use advanced sensors to measure humidity and make automatic adjustments to keep it within acceptable ranges. Temperature Control Units : Depending on the cleanroom’s requirements, temperature control units such as chillers, heating coils, and thermal storage systems can be used to regulate the temperature. These systems can be integrated with the cleanroom’s air handling system for precise temperature management. 2. Continuous Monitoring To ensure that temperature and humidity remain within the acceptable range, continuous monitoring is crucial. Cleanroom environments are typically equipped with temperature and humidity sensors that constantly track these variables. Data from these sensors is sent to a central control system, where it is analyzed and used to make real-time adjustments to the HVAC system. Many modern systems allow for automated adjustments based on preset parameters. Sensors and monitoring systems must be regularly calibrated to ensure their accuracy. These monitoring systems also help in maintaining compliance with regulatory standards by providing reliable data for audits and inspections. 3. Environmental Control Standards The specific temperature and humidity levels that must be maintained in a cleanroom depend on the cleanroom's classification, the type of work being performed, and the standards set by regulatory agencies. For instance: ISO Class 1 to Class 5 Cleanrooms : These cleanrooms require extremely tight control over both temperature and humidity, often in the range of 18°C to 22°C (64°F to 72°F) for temperature, and 30-60% relative humidity for humidity. These standards ensure that the cleanroom environment remains stable for sensitive production processes, such as semiconductor fabrication or high-grade pharmaceutical manufacturing. Pharmaceutical Cleanrooms : The temperature and humidity levels in pharmaceutical cleanrooms are often defined by GMP (Good Manufacturing Practices) standards. These facilities may need to maintain a temperature range of 18°C to 25°C (64°F to 77°F) and a relative humidity range of 30% to 65%. 4. Redundancy and Backup Systems Given the critical nature of temperature and humidity control, cleanrooms often incorporate redundant systems to ensure that any failure in the primary system does not compromise cleanroom conditions. These can include backup power supplies, redundant air handling units, and fail-safe systems that alert operators to any deviations from acceptable conditions. 5. Routine Maintenance To ensure the ongoing performance of HVAC systems and to avoid costly breakdowns, routine maintenance is essential. This includes regular checks of air filters, humidity control systems, and temperature control units, as well as cleaning and servicing of sensors and other monitoring equipment. Conclusion Managing temperature and humidity in cleanrooms is essential for maintaining product quality, process integrity, and personnel safety. These factors affect not only the physical environment but also the behavior of particles, chemicals, and materials, all of which are vital to cleanroom operations. The use of advanced HVAC systems, continuous monitoring, and adherence to industry-specific environmental standards ensures that cleanrooms maintain the desired conditions at all times. By implementing proper temperature and humidity control measures, cleanroom operators can safeguard the success of their processes, enhance operational efficiency, and meet regulatory compliance standards. Read more: All About Cleanrooms - The ultimate Guide
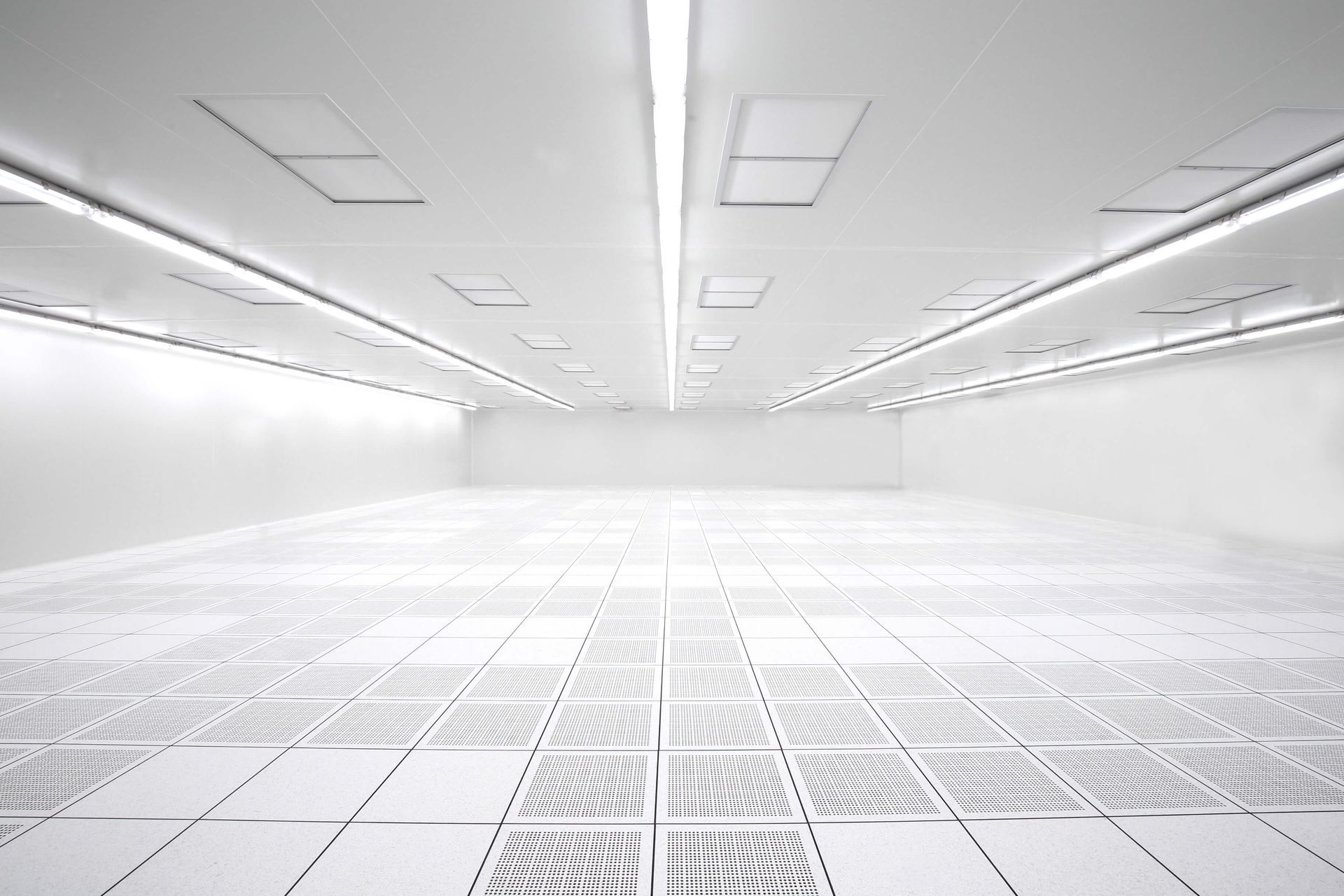
Introduction Cleanrooms are environments meticulously controlled to maintain a specific level of cleanliness and to minimize contamination, such as dust, airborne particles, microbes, and chemical vapors. These environments are critical in industries such as pharmaceuticals, biotechnology, semiconductor manufacturing, aerospace, and medical device production, where the slightest contamination can have severe consequences for product quality, safety, and regulatory compliance. While most discussions about cleanrooms focus on air filtration, gowning procedures, and other aspects of contamination control, one area that deserves careful attention is the floor. Cleanroom flooring plays a crucial role in maintaining the integrity of the controlled environment. It must support the high standards of cleanliness required in such spaces while also providing durability, ease of maintenance, and safety. Flooring in a cleanroom is subjected to foot traffic, machinery, spills, and harsh cleaning protocols, which all require careful consideration in selecting the appropriate material and system. This article delves into the various options for cleanroom flooring, the factors that influence the choice of flooring, and the key considerations to ensure that the flooring helps to maintain the cleanroom's stringent cleanliness and safety standards. Importance of Cleanroom Flooring Cleanroom flooring is not just about aesthetic appeal; it plays a vital role in several important aspects of cleanroom functionality. Cleanroom floors help in the following areas: Contamination Control : Flooring is a primary surface in cleanrooms that must not contribute to contamination. It needs to be resistant to particulate buildup and easy to clean to ensure the elimination of potential contaminants. Safety : In some industries, such as pharmaceuticals or food production, safety is paramount. Cleanroom flooring needs to offer slip resistance, especially in areas where fluids or chemicals may be present. Durability : Given the heavy equipment, foot traffic, and cleaning routines in cleanrooms, the flooring must be robust enough to withstand wear and tear without compromising its ability to maintain cleanliness standards. Maintenance : Flooring should be easy to maintain, as cleanroom environments require constant cleaning. The material chosen should be resistant to staining, chemical damage, and abrasion, allowing for quick and effective cleaning routines. Cleanroom Flooring Options The type of flooring selected for a cleanroom will depend on factors such as the cleanroom’s ISO classification, the nature of the industry, and the anticipated traffic levels. Below are some of the most common cleanroom flooring options: 1. Epoxy Resin Flooring Epoxy resin flooring is one of the most popular choices for cleanroom environments due to its excellent durability, seamless surface, and resistance to chemicals, wear, and abrasion. Epoxy floors consist of a two-part system: a hardener and a resin that, when mixed, form a chemical bond, creating a strong and long-lasting floor. Advantages of Epoxy Flooring : Seamless Surface : Epoxy floors are seamless, meaning there are no joints or seams where dust and debris can accumulate, which helps in maintaining a high level of cleanliness. Chemical Resistance : Epoxy flooring is resistant to many industrial chemicals, making it an excellent choice for cleanrooms in industries like pharmaceuticals, biotechnology, and food production. Durability : Epoxy floors are highly resistant to wear, abrasion, and impact, ensuring that they can withstand heavy foot traffic and equipment movement. Considerations : Surface Hardness : While epoxy flooring is durable, it can be prone to cracking under extreme impacts, and its hardness may cause damage to equipment if something is dropped. Initial Setup Costs : Epoxy floors can be costly to install, and the process may involve preparation of the substrate before application to ensure proper adhesion. 2. Vinyl Flooring Vinyl flooring, specifically static-dissipative and conductive vinyl, is another common cleanroom flooring option. It is available in rolls or tiles and is highly valued for its cost-effectiveness and ease of installation. Advantages of Vinyl Flooring : Ease of Installation : Vinyl flooring is easy to install and can be laid down quickly, making it ideal for projects where speed is of the essence. Antistatic Properties : Certain types of vinyl flooring are designed with antistatic properties, which is especially important in environments like semiconductor manufacturing, where static electricity could damage sensitive components. Comfort : Vinyl flooring is more forgiving underfoot than epoxy or tile, offering a degree of comfort for workers who spend long hours on their feet. Considerations : Durability : While vinyl is durable, it is generally less robust than epoxy flooring and can be more susceptible to damage from sharp objects or heavy equipment. Cleaning Requirements : Vinyl floors can show signs of wear over time, especially in high-traffic areas, and may require periodic polishing or refinishing to maintain their appearance and effectiveness. 3. Rubber Flooring Rubber flooring is another option that is particularly beneficial in cleanrooms where durability and safety are essential. Rubber floors are available in various thicknesses and are often used in cleanrooms where noise reduction and slip resistance are priorities. Advantages of Rubber Flooring : Slip Resistance : Rubber provides excellent slip resistance, which is crucial in environments where wet conditions or spills are likely. Noise Reduction : Rubber flooring can help to absorb sound, making it ideal for cleanrooms in laboratories or production areas where noise can be an issue. Flexibility : Rubber flooring is highly flexible and can be cut to fit any shape or layout, providing versatility in design. Considerations : Chemical Resistance : While rubber is resistant to many chemicals, it may not be as effective as vinyl or epoxy in environments with highly corrosive substances. Surface Maintenance : Rubber floors require more frequent cleaning and may show signs of wear or staining over time. 4. Antistatic and Conductive Flooring In industries like semiconductor manufacturing and electronics assembly, the risk of static discharge is a significant concern. Antistatic and conductive flooring options are designed to dissipate electrostatic charges, preventing damage to sensitive equipment or components. Advantages of Antistatic Flooring : Electrostatic Discharge (ESD) Protection : These floors prevent the buildup of static electricity, which could otherwise damage sensitive electronic components. Seamless and Durable : Similar to epoxy floors, antistatic flooring options are often seamless and durable, providing a clean and safe environment for critical production activities. Considerations : Cost : Antistatic and conductive flooring solutions tend to be more expensive than standard flooring options. Maintenance : These floors require regular maintenance to ensure that their conductive properties are preserved over time. 5. Ceramic or Porcelain Tile Flooring Ceramic or porcelain tile flooring is a traditional option that is sometimes used in cleanrooms, particularly in environments where temperature fluctuations, chemical resistance, and easy cleaning are priorities. Advantages of Ceramic/Porcelain Flooring : Chemical Resistance : Tiles are resistant to most chemicals, making them suitable for cleanrooms in industries like pharmaceuticals and food production. Durability : Tiles are highly durable and resistant to scratching and impact, making them ideal for areas with heavy foot traffic. Considerations : Seams : The grout between tiles can collect dust and debris, making cleaning more difficult than with seamless options like epoxy or vinyl. Installation Complexity : Installing tile flooring can be more complex and time-consuming than other options, particularly in cleanrooms where a high level of precision is required. Raised Flooring in Cleanrooms: A Key Consideration In many high-class cleanrooms, such as those classified under ISO 5, 4, 3, 2, and 1, a raised floor system is essential to meet the specific needs of cleanliness, safety, and airflow. A raised floor system creates an elevated platform above the subfloor, allowing for the placement of air filtration systems, wiring, cables, and utilities beneath the floor. This system is particularly important in cleanrooms where strict environmental control is required. Advantages of Raised Flooring : Airflow and Ventilation : Raised floors allow for optimal airflow management, essential for maintaining the required cleanliness levels. With a raised floor, the air distribution system (typically underfloor ventilation) can maintain laminar airflow, which is crucial in controlling particulate contamination. Utility Management : In cleanrooms, there is a need to hide utilities, cables, and other equipment that should not be exposed to the cleanroom environment. Raised floors provide an efficient way to route all these utilities under the floor, ensuring they do not interfere with the cleanliness or the room’s functionality. Flexibility : Raised flooring systems provide flexibility in terms of layout and redesign. As cleanroom requirements change over time, the layout can be easily adjusted without the need for major renovations. Easy Maintenance : With a raised floor, cleaning and maintenance become easier as utilities and air systems are accessible without disturbing the cleanroom environment itself. Considerations : Initial Installation Costs : Raised flooring systems can increase the initial cost of setting up a cleanroom, especially in high-class environments where precision is paramount. Potential Contamination Sources : If the raised floor is not maintained properly, it can become a source of contamination. The space between the raised floor and the subfloor must be regularly cleaned to prevent the accumulation of dust or particles that could compromise the cleanroom environment. Conclusion Cleanroom flooring is an essential component of any controlled environment, and the right choice of flooring can help maintain cleanliness, enhance safety, and ensure compliance with industry regulations. Each flooring option—be it epoxy, vinyl, rubber, ceramic, or antistatic—has its own set of advantages and considerations. When choosing the appropriate flooring for a cleanroom, it is critical to consider factors such as the cleanroom’s classification, the level of foot traffic, the potential for chemical exposure, and the ease of maintenance. Additionally, for high-class cleanrooms (ISO 5, 4, 3, 2, 1), raised floor systems provide significant advantages in maintaining airflow, managing utilities, and ensuring flexibility, making them a vital part of the cleanroom design. By selecting the right flooring material and system for the specific needs of the cleanroom, businesses can ensure that their cleanroom remains a safe, functional, and contamination-free environment. Whether the focus is on durability, chemical resistance, or static control, the right cleanroom flooring choice is key to maintaining the overall effectiveness of the cleanroom and supporting the industries that rely on them. Read more: All About Cleanrooms - The ultimate Guide
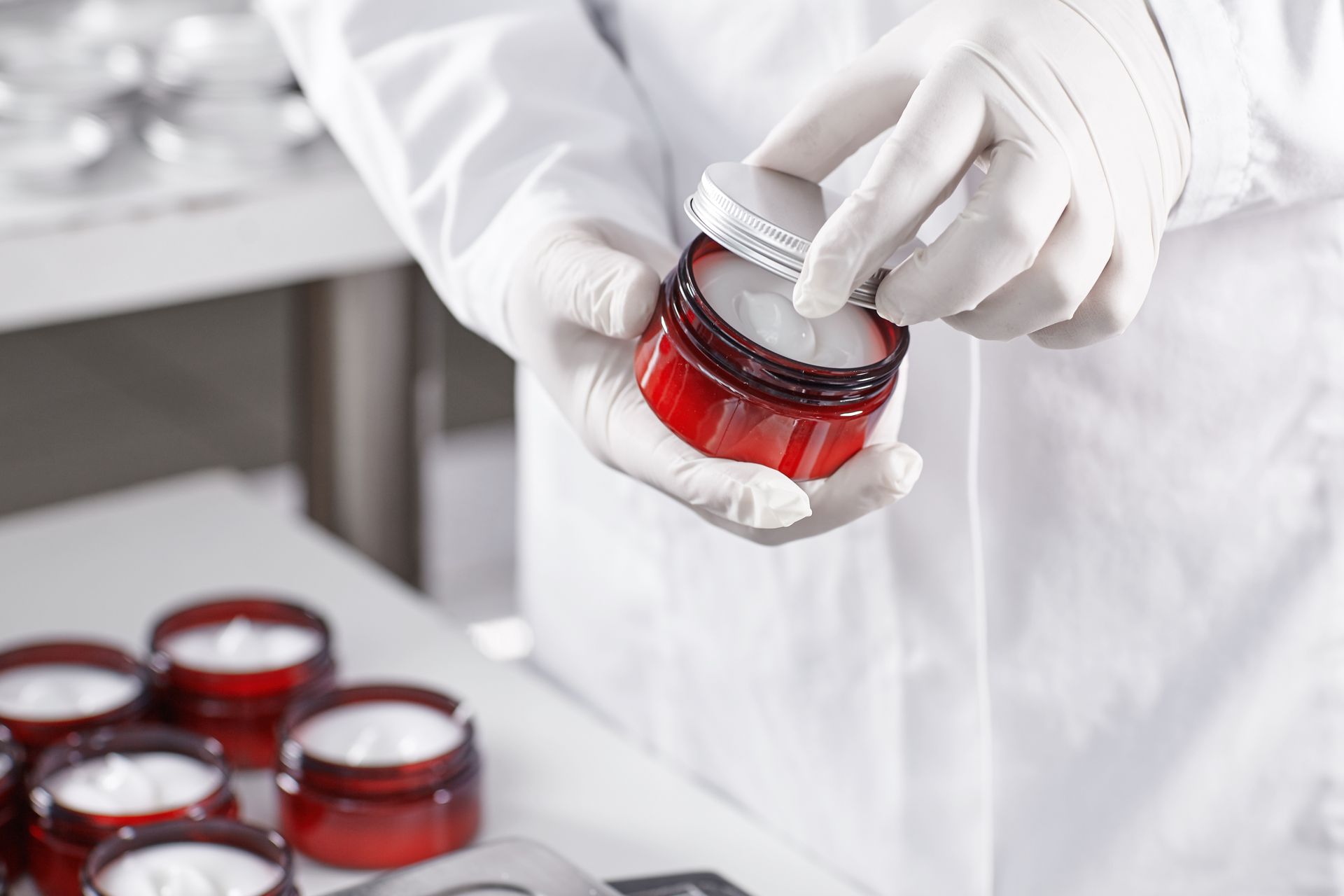
Introduction Cleanrooms are critical in industries where the production or processing of materials requires a highly controlled environment, free of contamination from airborne particles, microbes, or other impurities. These controlled spaces are commonly used in fields like semiconductor manufacturing, pharmaceuticals, biotechnology, aerospace, and healthcare. In some scenarios, however, a permanent, traditional cleanroom may not be practical or necessary. This is where modular cleanrooms—temporary, flexible, and easily customizable cleanroom solutions—come into play. Modular cleanrooms are becoming increasingly popular as they offer significant advantages over conventional, permanent cleanroom structures, especially when temporary cleanroom facilities are required. These modular units can be quickly assembled and dismantled, providing a cost-effective and scalable solution for industries that need cleanroom environments for short-term projects or fluctuating production needs. This article will explore the use of modular cleanrooms in temporary situations, their benefits, and the industries that can benefit from their use. What are Modular Cleanrooms? Modular cleanrooms are pre-fabricated, portable, and adaptable cleanroom systems designed to meet the specific contamination control requirements of a facility. These cleanrooms are made up of modular panels that can be easily assembled and disassembled without the need for permanent construction. They are typically equipped with essential cleanroom components such as high-efficiency particulate air (HEPA) or ultra-low penetration air (ULPA) filters, laminar airflow systems, and controlled ventilation. The modular nature of these cleanrooms means that they can be customized to the size, shape, and level of cleanliness required for a specific application. Whether it is a small unit for a lab setup or a large facility for manufacturing, modular cleanrooms can be configured according to the industry’s needs. Additionally, they are designed to be flexible in terms of portability, allowing them to be relocated or expanded as necessary. Why Choose Modular Cleanrooms for Temporary Situations? Flexibility and Scalability : One of the most significant advantages of modular cleanrooms is their flexibility and scalability. Temporary cleanroom needs often arise in industries with fluctuating production schedules or project-based work, such as research and development (R&D) labs, pharmaceutical clinical trials, or medical device manufacturing. Modular cleanrooms can be tailored to meet specific, temporary needs, whether it is for short-term projects or seasonal production. Cost-Effectiveness : Permanent cleanroom construction is a costly and time-consuming endeavor. Not only does it require significant capital investment, but it also involves regulatory approvals, construction delays, and ongoing maintenance. Modular cleanrooms, on the other hand, are much more affordable and can be deployed quickly without the need for extensive construction work. Speed of Installation and Relocation : Modular cleanrooms are designed for rapid assembly and disassembly. In situations where time is of the essence, such as when urgent production needs arise, the ability to set up a cleanroom in a matter of weeks, or even days, can be a game-changer. This speed of deployment allows businesses to quickly scale their operations or expand their production capacity without the long wait associated with traditional cleanroom construction. Compliance with Industry Standards : Despite being temporary, modular cleanrooms are built to comply with stringent industry standards, such as ISO 14644 for cleanliness classification and Good Manufacturing Practices (GMP) for pharmaceuticals. Modular cleanrooms are equipped with the same high-quality filtration systems, controlled airflow, and air handling systems as permanent cleanroom facilities. As a result, they can provide the same level of contamination control and meet regulatory requirements for specific industries. Reduced Downtime and Increased Productivity : Temporary cleanroom setups are ideal for industries that need to maintain operational efficiency but experience short-term fluctuations in production. By using modular cleanrooms, companies can ensure minimal downtime during periods of expansion or transition. For instance, a manufacturer may need to temporarily increase capacity due to a sudden spike in demand, such as during a product launch or seasonal production increase. The availability of a modular cleanroom enables the business to continue production without halting operations to build or refurbish a permanent cleanroom. Customizable Design : Modular cleanrooms can be customized to suit specific operational needs. This includes the ability to modify the layout, air filtration systems, size, and cleanliness levels. Whether the requirement is for a highly sterile environment for pharmaceuticals or a less stringent environment for electronics assembly, modular cleanrooms can be designed and configured to meet these diverse needs. Industries That Benefit from Modular Cleanrooms Pharmaceuticals and Biotechnology : The pharmaceutical and biotechnology industries are among the primary users of modular cleanrooms, particularly for clinical trials, research, and small-scale production. Modular cleanrooms allow companies to set up sterile environments for drug formulation, testing, or production, all while ensuring regulatory compliance. Semiconductor Manufacturing : The semiconductor industry is one of the most stringent sectors when it comes to cleanroom standards. The production of microchips and other semiconductor components requires extremely low levels of particulate contamination, making cleanroom environments an absolute necessity. Modular cleanrooms can be used in semiconductor fabs (fabrication facilities) when additional space or specialized environments are required for temporary projects or test runs. Aerospace and Defense : Aerospace manufacturing often involves the need for cleanroom environments to assemble sensitive components such as avionics, sensors, or precision equipment. Modular cleanrooms offer aerospace companies the flexibility to set up temporary cleanroom spaces when new components are being tested or during production surges related to new missions or aircraft models. Medical Devices : The production of medical devices, particularly sterile devices such as surgical instruments, implants, or diagnostic equipment, requires strict contamination control. Modular cleanrooms provide a practical solution for medical device manufacturers when short-term, high-quality production is needed. Food and Beverage Industry : While cleanrooms are often associated with high-tech industries, food and beverage manufacturers are also embracing modular cleanrooms for specific production needs. For example, high-precision packaging of pharmaceutical-grade supplements, specialty food products, or handling of sensitive ingredients might require cleanroom environments. Modular cleanrooms can be used to ensure that contamination risks are minimized during production. Conclusion Modular cleanrooms offer a versatile, cost-effective solution for industries that require temporary, flexible, and scalable cleanroom environments. Whether for clinical trials, small-scale production, R&D, or seasonal increases in demand, these temporary cleanrooms meet the stringent requirements of contamination control without the financial and logistical challenges of permanent cleanroom installations. The ability to quickly deploy, relocate, and customize modular cleanrooms to suit specific needs makes them an invaluable tool for a wide range of industries, including pharmaceuticals, biotechnology, semiconductor manufacturing, aerospace, medical devices, and even food production. As the demand for temporary cleanroom solutions grows, modular cleanrooms will continue to play an essential role in providing efficient and adaptable solutions to contamination control challenges in industries worldwide. Read more: All About Cleanrooms - The ultimate Guide
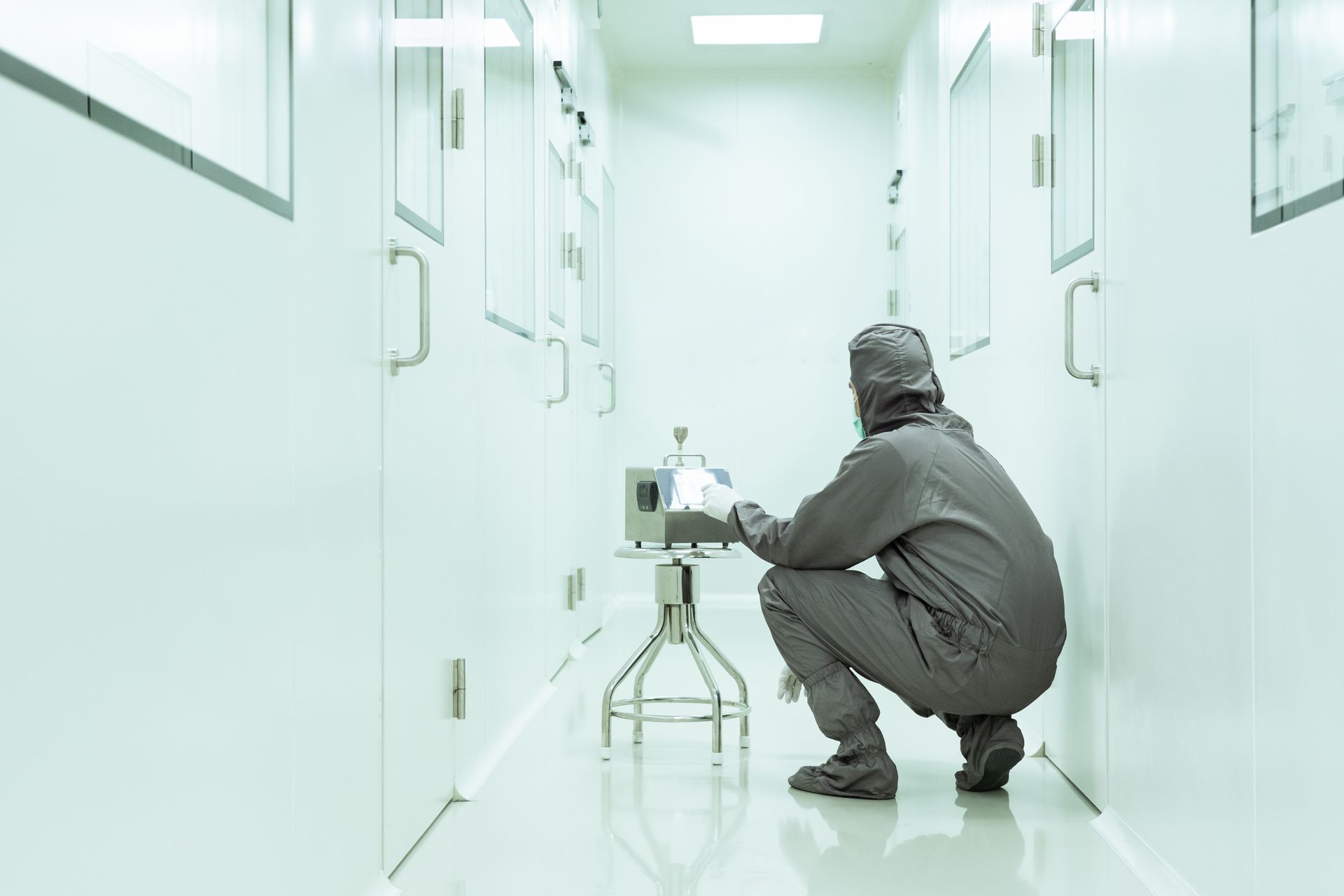
Introduction Cleanrooms are highly controlled environments designed to minimize the presence of contaminants such as dust, airborne microbes, and chemical vapors, among others. These controlled environments are essential in various industries, including semiconductor manufacturing, pharmaceuticals, biotechnology, aerospace, and healthcare. One of the most critical aspects of cleanroom performance is the monitoring and control of particle count, as it directly influences the quality of products and processes within the cleanroom. Particle count refers to the measurement of airborne particles within a given volume of air, typically expressed as the number of particles per cubic foot or cubic meter. These particles vary in size, ranging from nanometers to micrometers, and their presence can significantly impact the cleanroom environment, the products being manufactured, and the health and safety of individuals working within the facility. In this article, we will explore the relationship between particle count and cleanroom performance, examining how particle contamination affects cleanroom operations and the steps taken to mitigate this issue. Understanding Particle Count and Its Measurement In a cleanroom, air quality is meticulously regulated to meet industry standards, which are often based on the number and size of particles per unit of air. These standards are defined by organizations like the International Organization for Standardization (ISO) through the ISO 14644 series of standards, which classify cleanrooms into different cleanliness classes based on particle counts. Particle counters, which measure the number of particles present in the air, are the primary tools used to monitor particle count. These devices are capable of detecting particles at various sizes, such as 0.5 microns, 1 micron, or even smaller. The particle count data obtained from these counters allow cleanroom operators to assess the cleanliness of the environment and determine whether corrective actions are necessary. The particle count is typically expressed in terms of particles per cubic foot or cubic meter, with different classes specifying the acceptable limits for different particle sizes. For instance, an ISO Class 5 cleanroom has stricter particle count limits than an ISO Class 7 room. These classifications are critical in industries where even a single particle can have severe consequences on the final product or process. How Particle Count Affects Cleanroom Performance Product Quality and Reliability : Particle contamination can directly impact product quality in industries such as semiconductor manufacturing and pharmaceuticals. In semiconductor fabrication, for example, even the smallest particle can cause defects in microchips, leading to reduced performance or failure of electronic devices. Similarly, in the pharmaceutical industry, contamination by airborne particles can compromise the sterility of drug products, potentially resulting in product recalls, safety risks, or non-compliance with regulatory standards. Equipment and Process Integrity : Cleanroom performance is also tied to the operational efficiency of equipment. Particle contamination can cause wear and tear on sensitive machinery, leading to reduced equipment lifespan and frequent maintenance. This is particularly important in industries such as aerospace, where even tiny particles can cause significant damage to precision instruments or spacecraft components. Health and Safety Risks : Beyond product and process concerns, particle count can also influence the health and safety of workers within the cleanroom. In environments such as healthcare and biotechnology, where cleanrooms are used for sterile medical device production or cell culture work, particles can carry harmful microorganisms. The presence of these contaminants can increase the risk of infection or cross-contamination, particularly in sensitive environments like operating rooms, research labs, or drug manufacturing facilities. Compliance with Regulatory Standards : Cleanrooms in regulated industries must meet specific cleanliness criteria set by regulatory bodies such as the Food and Drug Administration (FDA), European Medicines Agency (EMA), and ISO. The particle count is a key factor in ensuring compliance with these standards. Non-compliance can result in product recalls, fines, and reputational damage. For example, pharmaceutical manufacturers are required to ensure that their cleanrooms meet specific ISO class standards for particle count, particularly for aseptic processes, where contamination could directly affect patient health. The Role of Cleanroom Design and Maintenance To maintain an optimal cleanroom environment, particle count must be continuously monitored and controlled. The design of the cleanroom plays a crucial role in this process. Cleanrooms are equipped with high-efficiency particulate air (HEPA) or ultra-low penetration air (ULPA) filters to capture airborne particles. These filters are strategically placed in the ventilation system to ensure a continuous flow of clean air while trapping contaminants. The cleanroom design must also take into account factors such as airflow patterns, temperature, humidity, and personnel movement. For instance, laminar airflow, where the air flows in a uniform direction, is crucial in minimizing particle contamination in critical areas. Inadequate airflow can result in the accumulation of particles in certain zones, compromising the cleanliness of the entire room. Regular maintenance and calibration of particle counters, filters, and other cleanroom equipment are also essential for keeping particle counts within acceptable limits. Filters must be replaced on a scheduled basis, and particle counters should be calibrated regularly to ensure their accuracy. Strategies to Control Particle Count Implementing Stringent Protocols : Establishing strict protocols for cleanroom entry and exit is a fundamental strategy for minimizing particle count. Personnel working in cleanrooms must wear protective clothing, including gowns, gloves, face masks, and hair covers, to prevent shedding particles from clothing and skin. Additionally, the use of air showers and gowning areas at entry points helps to reduce the introduction of contaminants into the cleanroom environment. Proper Maintenance of HVAC Systems : The HVAC (heating, ventilation, and air conditioning) systems within cleanrooms must be regularly serviced to maintain the proper air exchange rate and pressure differential. Filters must be changed periodically, and the system should be designed to meet specific air cleanliness standards for the size and type of cleanroom. Monitoring and Real-Time Data Collection : Continuous monitoring of particle counts is crucial to maintaining cleanroom performance. Advanced particle counters provide real-time data, allowing cleanroom operators to make immediate adjustments if particle levels exceed acceptable thresholds. Automated alarm systems can alert operators to issues like filter failures or excessive airborne particles, enabling them to take corrective action swiftly. Routine Cleaning and Housekeeping : Regular cleaning and decontamination procedures help minimize the accumulation of particles. Special cleaning agents and techniques must be used to clean surfaces without generating additional airborne particles. Vacuuming systems equipped with HEPA filters and cleaning methods that minimize disruption to airflow are essential in keeping particle counts low. Conclusion The effect of particle count on cleanroom performance cannot be overstated. High particle levels can compromise product quality, process efficiency, and worker safety, while also hindering compliance with regulatory standards. To maintain a high-performing cleanroom, it is crucial to monitor particle counts closely, design the room with adequate air handling and filtration systems, and implement stringent protocols for cleanliness and maintenance. Ultimately, controlling particle count in cleanrooms is a complex but necessary task that requires ongoing vigilance and attention to detail. The impact of a single particle on the integrity of a product or process highlights the importance of maintaining an environment with a low particle count to ensure safety, quality, and regulatory compliance.
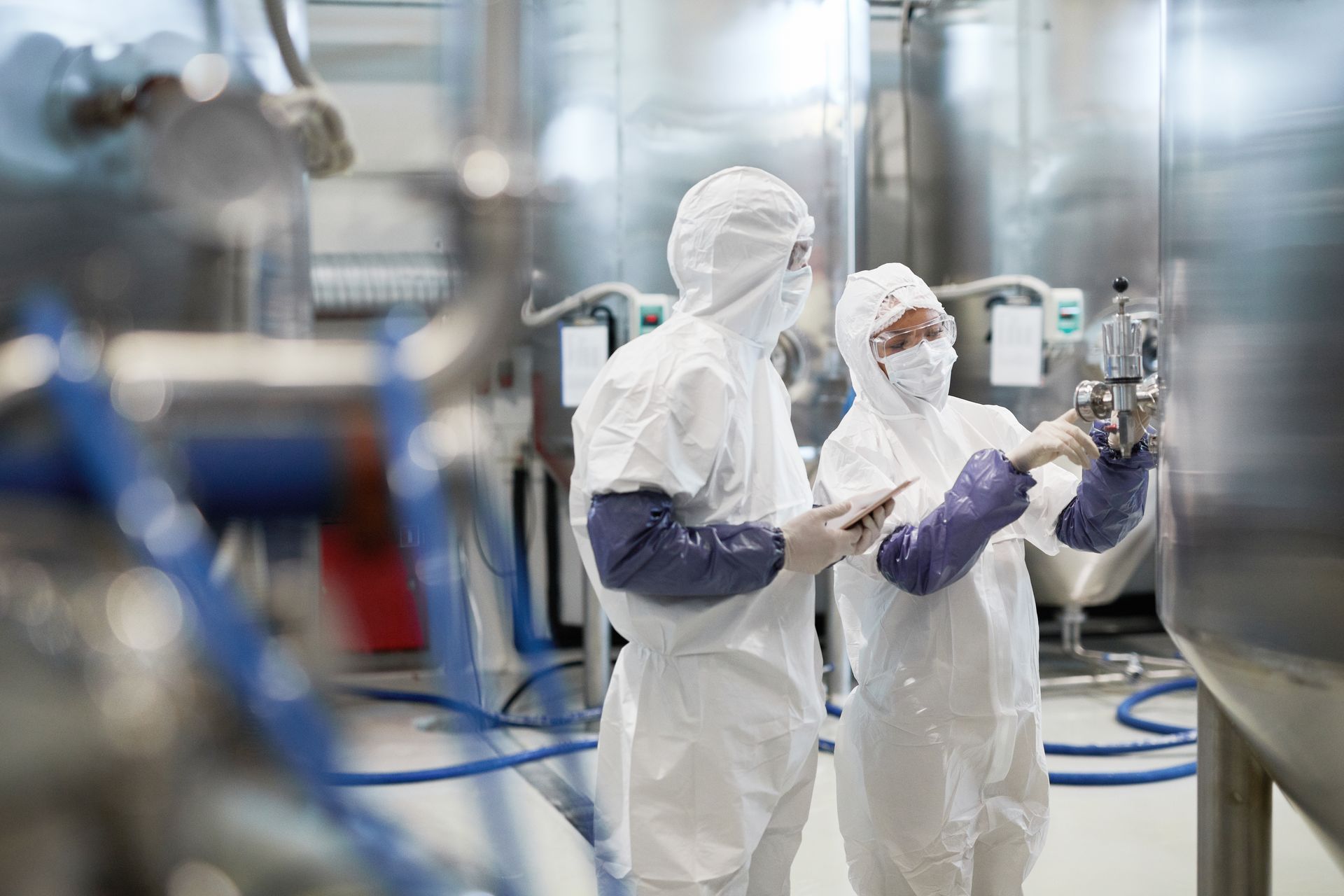
Introduction In the precise world of cleanrooms, every element, including lighting, plays a critical role in maintaining an environment conducive to high-quality production and research. Cleanroom lighting solutions are designed to meet stringent standards that prevent contamination while providing adequate illumination for complex tasks. This article explores the unique challenges of cleanroom lighting, the types of lighting solutions used, and their impact on both the environment and the operations conducted within cleanrooms. Understanding the Challenges of Cleanroom Lighting Cleanrooms require a controlled environment where pollutants, such as dust, airborne microbes, and chemical vapors, are kept at minimal levels. Lighting in such environments must not only prevent contamination but also ensure that it does not interfere with the delicate processes carried out in these spaces. Here are some of the specific challenges faced when implementing lighting solutions in cleanrooms: Contamination Control: Traditional lighting fixtures can be a source of contamination. They must be designed to prevent the accumulation of dust and to facilitate easy cleaning. This involves using sealed fixtures and smooth surfaces that minimize particle retention. Heat Emission: Lighting can significantly affect the temperature and humidity levels within a cleanroom. Excessive heat from lighting fixtures can disrupt the delicate balance required to maintain specific environmental conditions. Energy Efficiency: Cleanrooms operate continuously, requiring lighting solutions that are energy efficient to minimize operational costs and environmental impact. Brightness and Uniformity: Adequate illumination is critical for ensuring that cleanroom staff can perform precise tasks effectively. The lighting must provide uniform coverage and sufficient brightness without creating glare or shadows that could impede visibility. Types of Cleanroom Lighting Solutions To address these challenges, several types of lighting fixtures are commonly used in cleanrooms, each offering specific benefits: LED Lighting: Light Emitting Diode (LED) technology is favored in cleanroom settings due to its energy efficiency, long lifespan, and minimal heat output. LED fixtures can be easily sealed to prevent contamination. Additionally, they provide excellent color rendering and uniform light distribution, which are crucial for detailed tasks in cleanrooms. Sealed Fluorescent Lighting: Although being gradually replaced by LEDs, sealed fluorescent lighting has been a staple in cleanrooms due to its efficiency and good color rendering. These fixtures are designed with seals that prevent the ingress of particles and vapors. Indirect Lighting: To reduce glare and improve visual comfort, some cleanrooms employ indirect lighting solutions where light is bounced off the ceiling or walls. This technique provides a softer, diffused light that is evenly spread across the room. Task Lighting: In areas where precise or intricate work is performed, task lighting is used to provide additional illumination. These solutions must also be designed to be cleanroom compliant, with easy-to-clean surfaces and minimal particle generation. Impact of Lighting Solutions on Cleanroom Operations The right lighting solutions can significantly impact the efficiency and effectiveness of cleanroom operations: Enhanced Visibility for Precision Work: Proper lighting is essential for tasks that require high levels of accuracy, such as assembling microelectronics or preparing pharmaceutical products. Poor lighting can lead to errors and increased waste. Improved Worker Comfort and Productivity: Adequate and comfortable lighting reduces eye strain and fatigue, thereby enhancing worker productivity and reducing the likelihood of mistakes. Energy Consumption and Cost: By adopting energy-efficient lighting solutions, such as LEDs, cleanrooms can significantly reduce their energy usage and operational costs. Given the continuous operation of these facilities, even small savings per unit of light can add up to substantial amounts. Compliance with Safety Standards: Appropriate lighting is critical for maintaining a safe work environment. It helps ensure that all areas are properly illuminated to prevent accidents and allows for safe evacuation in case of emergencies. Conclusion Lighting in cleanrooms is a critical component that affects not only the operational integrity of the environment but also the well-being of the staff and the financial efficiency of the operations. As technology advances, lighting solutions continue to evolve, offering greater efficiency, better contamination control, and improved working conditions. The choice of the right lighting system in a cleanroom is a key factor that contributes to the overall success and sustainability of operations in critical environments like pharmaceuticals, biotechnology, and semiconductor manufacturing. Read more: All About Cleanrooms - The ultimate Guide
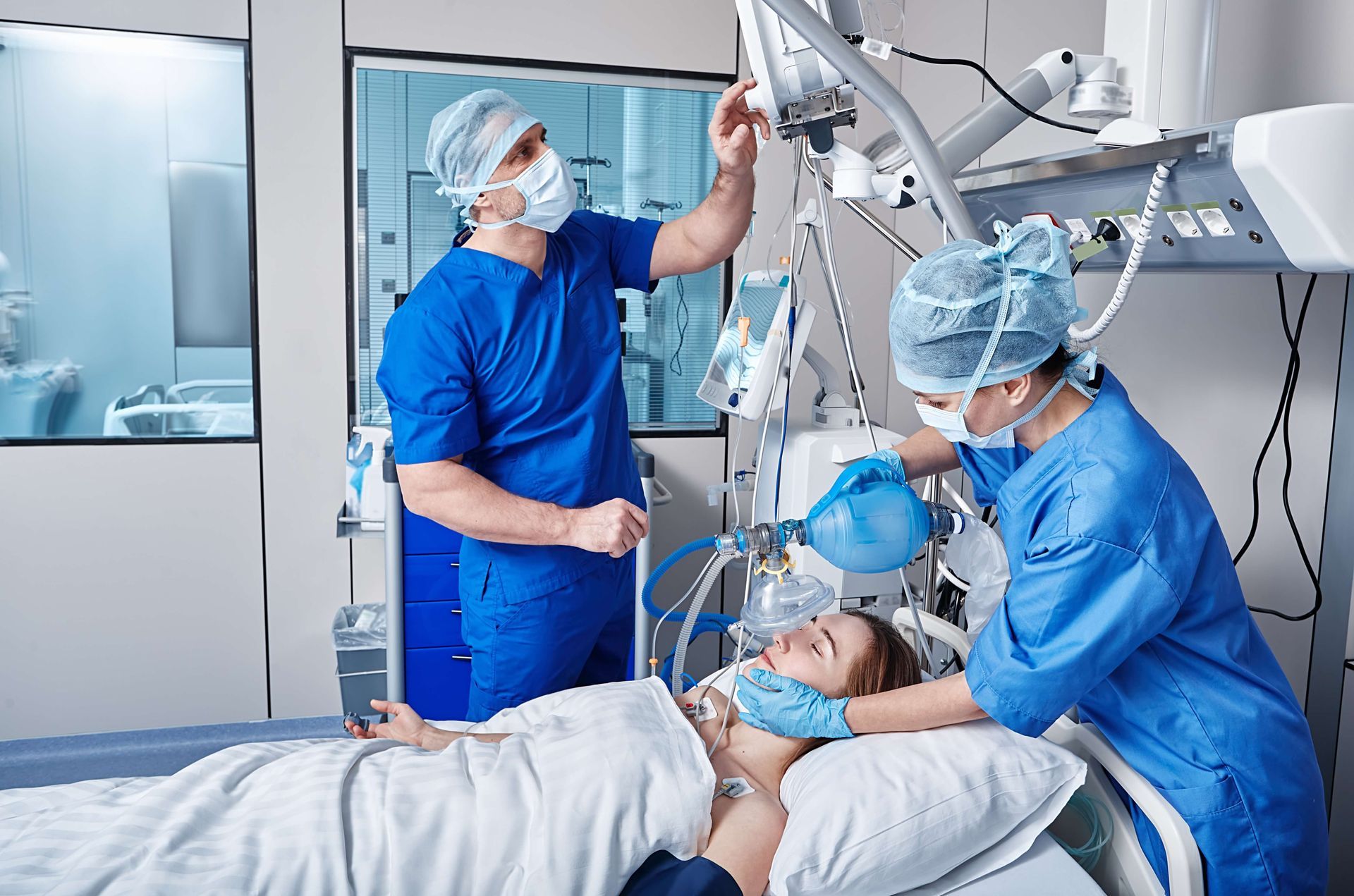
Introduction In the complex ecosystem of healthcare, the implementation of cleanrooms plays a crucial role in ensuring patient safety, enhancing the quality of care, and facilitating the advancement of medical research. Traditionally associated with semiconductor manufacturing and biotechnology, cleanrooms are now a vital component in hospitals and healthcare settings. This article explores the importance of cleanrooms in these environments, focusing on their design, function, and the critical standards they must meet. Introduction to Cleanrooms in Healthcare Cleanrooms in healthcare settings are designed to control the environmental parameters such as airborne particles, temperature, humidity, and pressure. These controlled environments are essential for activities where the presence of microbes and other contaminants can adversely affect health outcomes, such as in compounding pharmacies, operating rooms, and laboratories involved in tissue culture and in vitro fertilization. Key Functions of Cleanrooms in Healthcare: Compounding Pharmacies: Cleanrooms in compounding pharmacies are critical for the preparation of sterile medications. They prevent contamination during the compounding process, ensuring that medications are safe for patient use. This is particularly crucial for injectable medications, eye drops, and other formulations that require sterility to prevent infections. Operating Rooms: Modern operating rooms often incorporate cleanroom technology to maintain ultra-clean environments, reducing the risk of surgical site infections (SSIs). These infections are a significant concern in surgeries involving implants and highly invasive procedures where the infection risk is high. Medical Device Manufacturing: The production of medical devices, particularly implants and surgical instruments, requires cleanroom facilities to prevent contamination that could lead to infections or device failures. These environments ensure that products meet regulatory standards for sterility and safety. Research and Development: Cleanrooms are indispensable in biotechnological research and the development of pharmaceutical products. They provide the controlled environments necessary for conducting experiments that require manipulation of organisms and materials sensitive to environmental contaminants. Design and Standards The design of cleanrooms in healthcare is governed by stringent standards to ensure they effectively control environmental parameters. Key standards include: ISO 14644 and EU GMP Standards: These standards specify the air cleanliness class required for different types of cleanrooms. Healthcare cleanrooms typically operate at ISO Class 7 or better, depending on the specific activities performed within them. USP Standards: In the United States, USP Chapter <797> provides guidelines for the compounding of sterile preparations, detailing the requirements for cleanroom design, environmental monitoring, and personnel qualifications. HEPA Filtration: High-Efficiency Particulate Air (HEPA) filters are crucial in healthcare cleanrooms, capturing at least 99.97% of particles 0.3 microns in diameter or larger. This level of filtration is essential for removing bacteria and other airborne contaminants. Challenges in Healthcare Cleanrooms Operating a cleanroom in a healthcare setting presents unique challenges: Cost and Complexity: The construction and maintenance of cleanrooms are costly, requiring specialized equipment and materials. Additionally, the operational costs are high due to the need for ongoing environmental monitoring and strict adherence to cleaning protocols. Regulatory Compliance: Healthcare facilities must navigate a complex landscape of regulations that vary by country and region. Keeping up with changes in standards and ensuring compliance require dedicated resources and continual training of personnel. Balancing Accessibility with Containment: In hospital settings, there is often a need to balance the restrictive nature of cleanrooms with the need for patient and staff accessibility. This can complicate the design and operational protocols of cleanrooms in these environments. Conclusion The integration of cleanroom technology in healthcare settings is a testament to the sector's evolution towards higher standards of patient care and product safety. By providing controlled environments, cleanrooms help prevent infections, ensure the safety of medications and medical devices, and support cutting-edge research and development. As medical science advances, the role of cleanrooms in hospitals and healthcare facilities is likely to grow, underscoring their importance in the critical mission of saving lives and improving health outcomes. Read more: All About Cleanrooms - The ultimate Guide
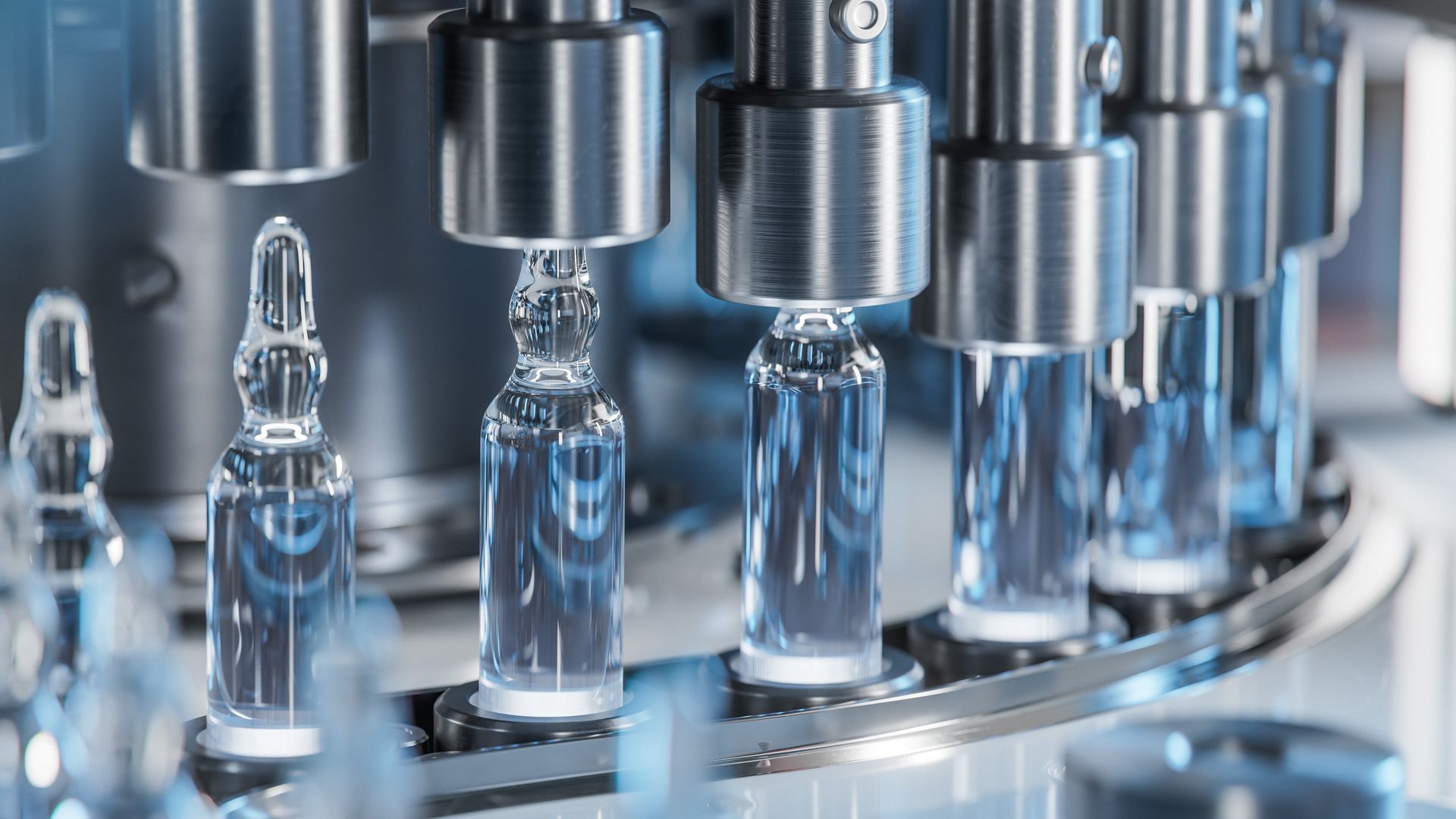
Introduction In the highly controlled environments of cleanrooms, where the smallest particle can cause significant production issues, the compatibility of materials used within these spaces is paramount. Material compatibility in cleanrooms is critical not only for maintaining the integrity and functionality of the products being manufactured but also for ensuring the safety and efficiency of the operations. This article explores the essential considerations of material compatibility in cleanrooms, examining how these factors impact safety and operational success. Understanding Material Compatibility in Cleanrooms Material compatibility in cleanrooms refers to the suitability of construction materials, tools, and equipment to operate under the stringent conditions without degrading or releasing contaminants. Materials must be selected based on their resistance to corrosion, their non-particulate-shedding properties, and their chemical stability when exposed to cleanroom cleaning agents and processes. Non-shedding Materials: Materials that do not release particles or fibers are essential in cleanroom environments. Options often include polymer and stainless steel for surfaces, and specialized non-linting fabrics for cleanroom garments. Chemical Resistance: Cleanroom materials must withstand frequent cleaning and sterilization with various chemicals without degrading. Chemical compatibility charts are often referenced to ensure that materials like seals, gaskets, and surface coatings will not break down over time. Biocompatibility: In pharmaceutical and biotech cleanrooms, materials must not only be chemically inert but also non-toxic and non-reactive with the products being handled. Critical Areas of Material Use in Cleanrooms Materials used in cleanrooms range from construction elements to tools and protective gear. Each category has specific requirements: Construction Materials: Walls, floors, and ceiling panels in cleanrooms are typically made from materials that are easy to clean and resistant to microbial growth. Options include epoxy or polyurethane-coated surfaces, stainless steel, and PVC or vinyl-covered gypsum. Furniture and Storage: All furniture used in cleanrooms, including tables, chairs, and shelving, must be designed to minimize particle retention and withstand regular sanitization. Furnishings are often made of stainless steel or covered with anti-static coatings to reduce particle attraction. T ools and Equipment: All tools, from wrenches to microscopes, must be made from materials that do not generate contaminants. Tools are often made from stainless steel or have special coatings to prevent rust and particle generation. Protective Clothing: Garments such as overalls, hoods, gloves, and booties are made from materials designed to trap contaminants shed by the human body while also preventing the external release of these particles. Advanced fabrics are tested for their particle retention and release properties under movement. Challenges in Material Compatibility Choosing the right materials for cleanrooms presents several challenges: Balancing Cost and Performance: High-quality materials that meet all cleanroom requirements can be expensive. Balancing cost with performance is a crucial consideration for cleanroom design and operation. Longevity and Durability: Materials must be durable enough to withstand the operational lifespan of the cleanroom without degrading. Replacing materials in a cleanroom can be costly and disruptive. Regulatory Compliance: Materials must comply with local and international standards for cleanrooms, which may vary depending on the industry and the specific application of the cleanroom. Safety Considerations with Cleanroom Materials The safety of cleanroom operations heavily relies on the appropriate selection of materials. Inappropriate or incompatible materials can lead to safety hazards, including: Chemical Hazards: Using materials not resistant to cleaning agents can lead to degradation, which not only contaminates the cleanroom but also poses chemical exposure risks to personnel. Fire Safety: Materials must be chosen with regard to their fire-retardant properties to reduce the risk of fire within the cleanroom, which is especially critical in environments with flammable substances. Particulate Contamination: Materials that shed particles can lead to product defects, which in severe cases can cause device failures, particularly in the electronics and pharmaceutical industries. Conclusion Material compatibility is a cornerstone of cleanroom design and operation, impacting everything from safety and efficiency to regulatory compliance and product integrity. Understanding the interactions between various materials and the cleanroom environment is crucial for maintaining a safe and effective workspace. As cleanroom technologies evolve, ongoing research and development into new materials and compatibility assessments remain critical for advancing cleanroom safety and functionality. Read more: All About Cleanrooms - The ultimate Guide
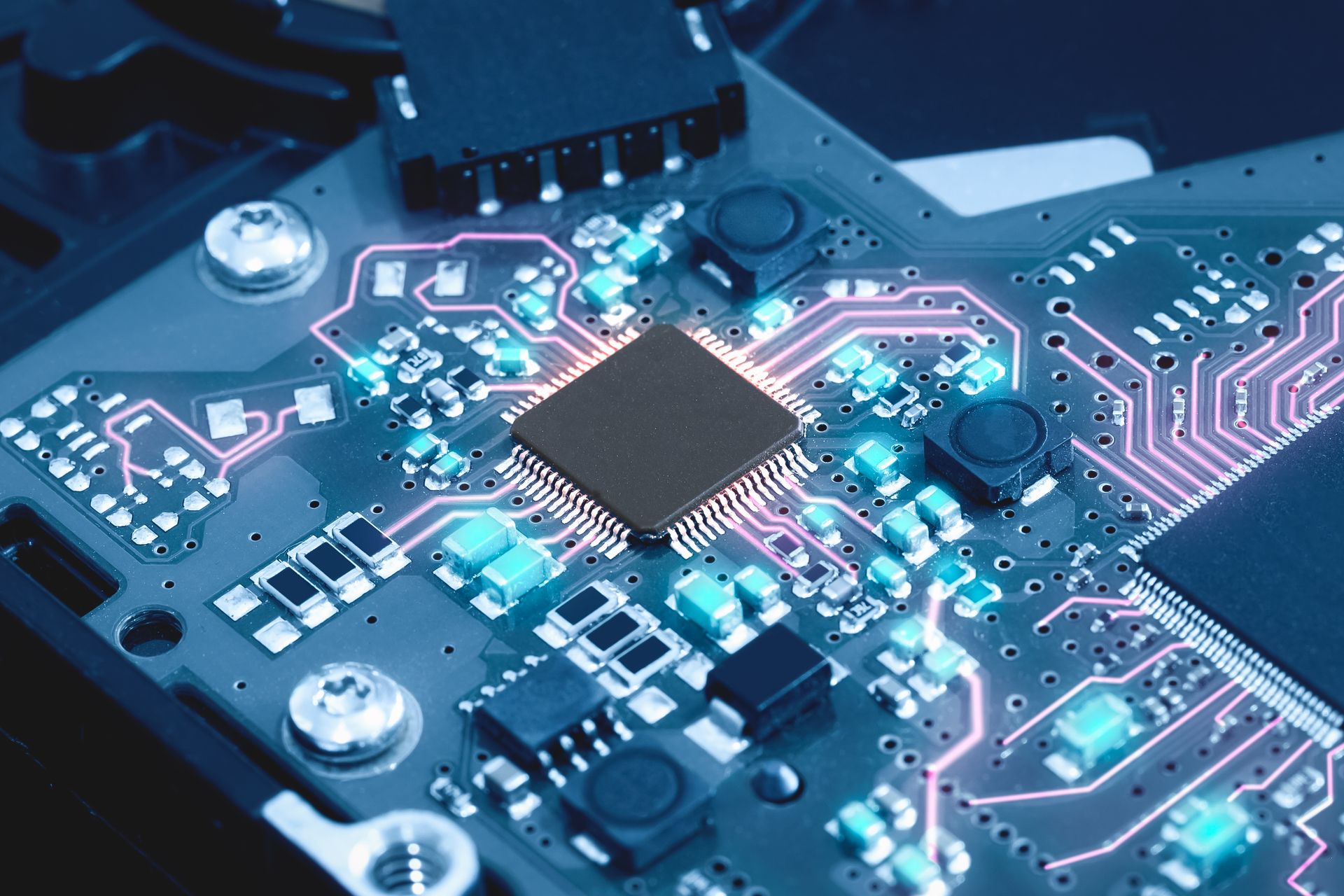
Introduction Cleanrooms are essential in industries where environmental contamination can significantly affect product quality and safety, such as in semiconductor manufacturing, pharmaceutical production, and biotechnological research. Over the years, cleanroom standards have evolved dramatically, shaped by advances in technology, scientific understanding, and the need for international harmonization. This article explores the historical development and evolution of cleanroom standards globally, with a particular focus on the International Organization for Standardization (ISO) standards, U.S. Federal Standards, and European Good Manufacturing Practices (GMP), including Annex 1. Origins and Early Development of Cleanroom Standards The concept of a cleanroom was pioneered in the 1960s by Willis Whitfield of Sandia National Laboratories. His invention marked a revolution by introducing an environment where the air's particle count was controlled through a laminar flow of filtered air. This innovation prompted the initial formulation of standards that would define the cleanliness levels required for various sensitive processes. Standardization Efforts: From Federal to International Standards Initially, cleanroom standards were disparate and varied significantly by industry and region, reflecting localized manufacturing practices and regulatory requirements. As global trade expanded, especially in high-tech sectors, there was a critical need for standardized criteria to ensure quality and compatibility across international borders. U.S. Federal Standard 209E: Introduced in 1963, this was the first significant cleanroom standard in the United States, categorizing cleanrooms based on the number of particles 0.5 micrometers or larger per cubic foot of air. This standard guided cleanroom specifications until it was superseded in the early 2000s. ISO 14644 Standards: In the late 1990s, the ISO developed the ISO 14644 series to harmonize cleanroom standards globally. These standards provided a detailed classification of air cleanliness by particle concentration and included methodologies for testing and monitoring clean environments. ISO 14644 parts 1 and 2 became the global benchmarks, replacing several national standards, including Federal Standard 209E. European GMP and Annex 1 In Europe, the integration of ISO standards was complemented by specific regulatory guidelines for pharmaceutical manufacturing: European GMP Guidelines: The EU's Good Manufacturing Practice (GMP) guidelines are critical for ensuring that products are consistently produced and controlled according to quality standards. These guidelines cover all aspects of production, from raw materials to finished products, ensuring safety and efficacy. Annex 1: Part of the European GMP guidelines, Annex 1 specifically addresses the manufacture of sterile medicinal products. This document provides detailed guidance on the design, operation, and monitoring of cleanrooms and controlled environments, emphasizing the prevention of microbial and particulate contamination. The latest revisions of Annex 1 have significantly influenced global practices by integrating risk-based approaches to aseptic processing, enhanced cleanroom behaviors, and more stringent contamination control measures. Global Harmonization and Its Impact The adoption of ISO 14644 and the alignment with guidelines like EU GMP and Annex 1 have facilitated global harmonization. This uniformity is especially beneficial for multinational corporations operating across different regulatory landscapes. It ensures consistent quality standards and simplifies compliance, which is crucial for international trade and cooperation. Recent Updates and Future Trends Recent updates to cleanroom standards and guidelines reflect technological advancements and a growing emphasis on sustainability. The future likely holds further integration of digital tools like IoT and AI in cleanroom monitoring and management, offering real-time data and predictive analytics. Moreover, as fields like nanotechnology and biotechnology evolve, cleanroom standards will need continuous adaptation to address these industries' unique challenges and risks. Conclusion The evolution of cleanroom standards, including the critical roles of ISO 14644 and EU GMP Annex 1, demonstrates the importance of international cooperation and technological advancement in maintaining high-quality, safe production environments. As technology progresses and global integration deepens, these standards will continue to evolve, ensuring that cleanrooms meet the exacting requirements of modern manufacturing and research activities.
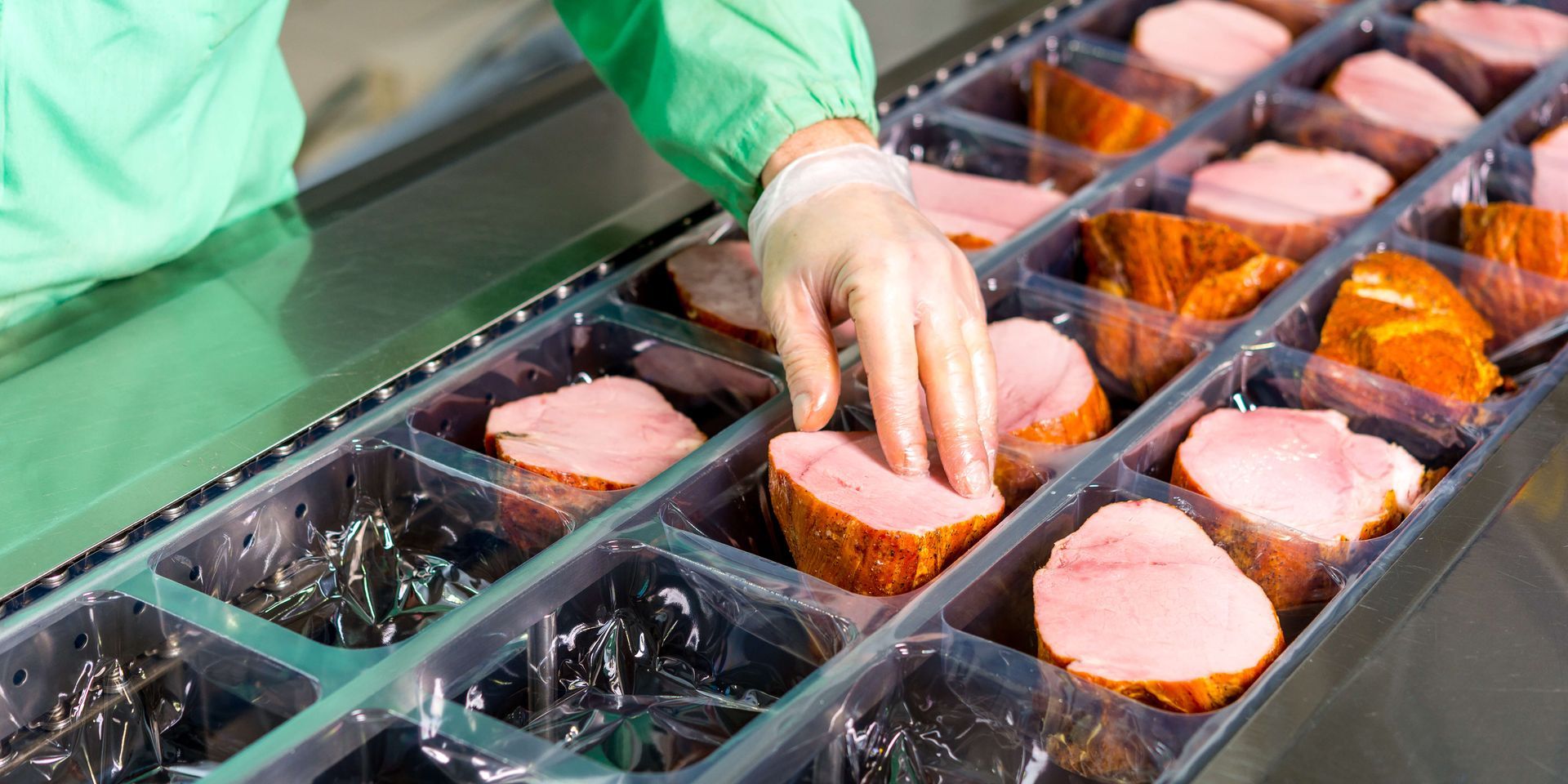
Introduction Microbial environmental monitoring (MEM) is a critical aspect of food safety and quality control within food production environments. It involves the systematic collection, analysis, and evaluation of environmental samples from food processing facilities to detect and control microbial contamination. With foodborne illnesses remaining a significant global health concern, ensuring that microbial safety standards are maintained is essential in any food production setting. This article explores the specifications of microbial environmental monitoring for food industries, highlighting its importance, methodology, key components, and regulatory standards. 1. Understanding Microbial Environmental Monitoring (MEM) Microbial environmental monitoring refers to the process of monitoring microorganisms present in the environment of food processing areas, including air, surfaces, water, equipment, and even personnel. The goal of MEM is to detect potential sources of microbial contamination that could compromise the safety, quality, and shelf-life of food products. It is crucial for identifying risks before they lead to significant problems, such as foodborne outbreaks or recalls. In food manufacturing, contamination often comes from microorganisms like bacteria, yeasts, molds, and viruses. They can contaminate the product directly or indirectly through contact with the surfaces or air within the production environment. By regularly monitoring and analyzing microbial data, food manufacturers can better control and mitigate microbial risks. 2. Key Microorganisms of Concern in Food Environments There are a variety of microorganisms that pose risks in food production environments, which can be categorized into the following: Pathogenic bacteria : These include Salmonella, Listeria monocytogenes, Escherichia coli (E. coli), and Campylobacter. These bacteria are of significant concern because they are associated with serious foodborne illnesses that can cause widespread health issues. Spoilage bacteria : Bacteria such as Pseudomonas, Bacillus, and Clostridium are common spoilage organisms that impact the shelf-life and organoleptic properties of food products. Fungi : Molds and yeasts can grow on food surfaces or in the processing environment, potentially affecting food quality and safety. Molds such as Aspergillus and Penicillium can produce mycotoxins that are harmful to consumers. Viruses : Though rarer, viruses like norovirus and hepatitis A are also a risk in food environments, particularly through contamination via food handlers. 3. Microbial Environmental Monitoring Specifications The specifications for microbial environmental monitoring within the food industry are designed to ensure a robust framework for identifying contamination risks. These specifications generally include: a. Sampling Strategy The sampling strategy is a core component of MEM and must be carefully designed to accurately reflect the microbial load in the environment. The key specifications in sampling include: Frequency of sampling : The frequency of environmental sampling depends on the type of food product, the production process, and regulatory requirements. High-risk environments (e.g., ready-to-eat food processing plants) typically require more frequent sampling, often daily or weekly. Low-risk environments (e.g., dry food processing) may have less frequent sampling. Types of samples : Environmental samples can be collected from various surfaces, air, water, equipment, and even personnel. Surfaces, especially those in direct contact with food, are among the most common sampling sites. Airborne microbial sampling is also critical in environments with high levels of airborne dust and moisture. Sampling methods : There are several methods for microbial sampling, including swabbing, using contact plates, air sampling, and water sampling. Swabbing surfaces with sterile wipes and placing contact plates on surfaces to capture microbial growth are common practices. Air sampling can be done using impaction methods or filtration through specific air monitoring devices. b. Microbial Testing Methods Once samples are collected, the microbial testing phase begins. This involves using specific techniques to culture and identify microorganisms in the samples. Some of the standard methods include: Plate count methods : These involve culturing microbial samples on nutrient agar plates and counting the colonies that grow. It is one of the most widely used methods for detecting and quantifying bacteria in food processing environments. Most probable number (MPN) : This statistical method is used for quantifying microorganisms, especially in liquid samples like water. It helps estimate the concentration of microbes in a sample. PCR (Polymerase Chain Reaction) : Molecular techniques such as PCR are used to identify specific microorganisms' DNA. This is particularly useful in detecting pathogens like Salmonella or E. coli in environmental samples. ATP bioluminescence : This rapid test method measures the presence of adenosine triphosphate (ATP), a molecule present in all living cells, to assess the cleanliness of surfaces and the presence of microbial contamination. c. Risk-Based Monitoring Risk-based environmental monitoring specifies that sampling and testing efforts should be focused on high-risk areas and critical control points within the production facility. Some risk-based strategies involve: Targeted monitoring : Emphasizing areas where microbial contamination is most likely to occur, such as wet zones, food contact surfaces, and high-touch equipment. Microbial hazard analysis : This involves evaluating the entire production process to identify where contamination may occur and focusing monitoring efforts on these points, such as raw material handling, cooking, cooling, and packaging areas. Environmental mapping : Creating detailed maps of the processing environment helps to identify potential hotspots for contamination, allowing for targeted microbial monitoring. d. Action Limits and Corrective Actions For MEM to be effective, established action limits must be in place. These limits dictate the maximum allowable microbial counts in environmental samples. If these limits are exceeded, corrective actions must be implemented immediately. The following components are critical: Action limits : These are thresholds for microbial levels above which corrective actions must be taken. These thresholds vary depending on the type of microorganism and the food product involved. For example, pathogens like Salmonella may require immediate corrective actions at even low levels, while spoilage organisms might allow for more flexibility. Corrective actions : If action limits are exceeded, corrective actions may include increasing the cleaning and sanitation protocols, adjusting the production process, or conducting additional microbiological testing to identify the source of contamination. 4. Regulatory Framework and Guidelines Numerous regulatory bodies establish guidelines and standards for microbial environmental monitoring in food industries. Some of the most important organizations include: The Food and Drug Administration (FDA) : In the United States, the FDA provides guidelines for environmental monitoring in food facilities, particularly through its Food Safety Modernization Act (FSMA), which emphasizes proactive controls, including MEM, to prevent contamination. The European Food Safety Authority (EFSA) : EFSA provides risk assessments and guidelines for food safety, which are integral to MEM practices in Europe. The Codex Alimentarius Commission : This international organization provides food safety standards and guidelines that help establish best practices for MEM in food production environments globally. HACCP (Hazard Analysis and Critical Control Points) : HACCP is a preventive approach to food safety and is widely adopted across the food industry. It incorporates MEM as a critical component of identifying, monitoring, and controlling microbial hazards. 5. Conclusion Microbial environmental monitoring plays a vital role in ensuring the safety and quality of food products. By establishing robust monitoring programs that include frequent sampling, effective testing methods, and a focus on critical risk areas, food manufacturers can significantly reduce the risk of microbial contamination. Coupled with a regulatory framework and corrective action protocols, MEM helps maintain food safety standards, protect consumers, and ensure compliance with food safety regulations. As food industries continue to innovate and adapt to new technologies, the specifications of microbial environmental monitoring will remain integral to safeguarding public health. Read more: All About Cleanrooms - The ultimate Guide
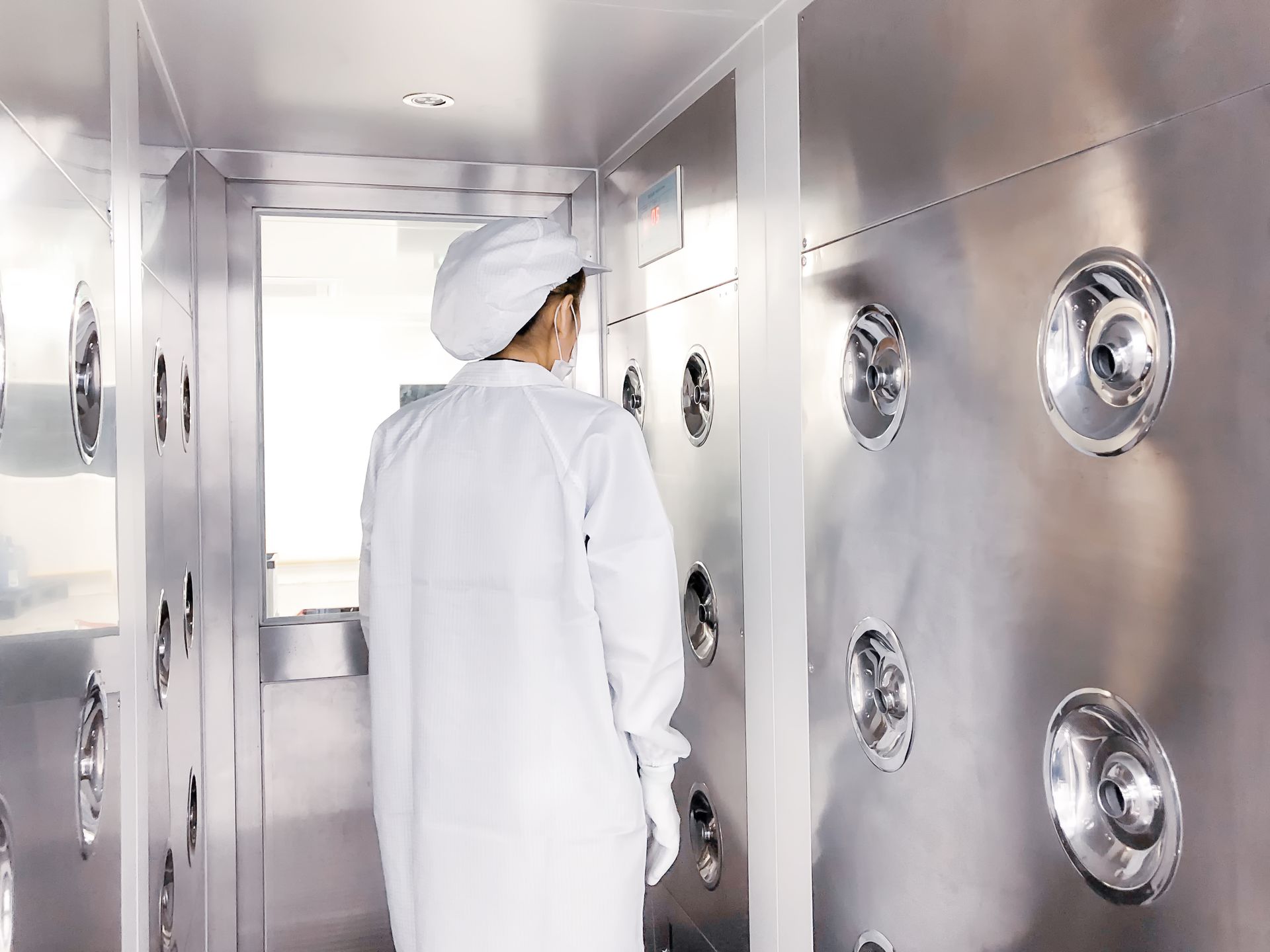
Introduction Setting up a cleanroom from scratch is a complex, high-stakes project crucial in industries such as pharmaceuticals, biotechnology, electronics, and aerospace. Each step, from design and construction to certification and maintenance, must adhere to stringent standards to ensure the space meets the specific cleanliness requirements necessary for production or research. This article presents a detailed case study of setting up a cleanroom, highlighting the challenges faced and solutions implemented during the process. Initial Planning and Design The first step in establishing a cleanroom is comprehensive planning and design tailored to the specific needs of the operations it will support. This phase involves: Requirements Analysis: Understanding the specific ISO class requirements, which define the maximum allowable particle count in the cleanroom. For instance, an ISO Class 5 cleanroom allows fewer airborne particles than an ISO Class 8. Design Considerations: Architectural design that facilitates airflow management, personnel movement, and material flow to minimize contamination. This includes deciding on the layout, the materials for walls and floors (typically non-porous and easy to clean), and the type of HEPA or ULPA filters needed. HVAC System Design: Critical for controlling the cleanroom's environment by managing air supply, temperature, humidity, and pressure differentials. The design must ensure sufficient airflow and correct placement of air returns to avoid turbulence and contamination. Construction Phase Following design, the construction phase begins, which requires strict adherence to cleanliness and contamination control, even before the cleanroom is operational: Material Selection: Use of non-shedding materials that can withstand frequent cleaning and disinfection. Common choices include stainless steel, sealed concrete, and specific plastics. Controlled Construction Environment: Construction itself must occur under controlled conditions, often employing temporary clean tents to prevent contamination during the build. Installation of Systems: This includes the HVAC system, lighting (typically LED for energy efficiency and minimal heat production), and filtration units. All systems must be installed in a manner that maintains the integrity of the cleanroom environment. Testing, Validation, and Certification Before the cleanroom can be operational, it must undergo rigorous testing and validation: Testing Air Filtration and Flows: Ensuring that the installed filters effectively remove particles from the air and that air flows as designed to prevent stagnant areas where contaminants could accumulate. Validating Environmental Controls: Checking temperature, humidity, and pressure differentials to ensure they meet design specifications. These factors are critical for preventing the ingress of contaminants and ensuring comfortable working conditions for staff. Certification: A third-party certifier typically performs final testing to certify the cleanroom’s compliance with the relevant ISO standards. This process includes particle counting and recovery tests to validate the cleanroom's ability to maintain cleanliness standards over time. Challenges Encountered During the setup of a cleanroom, several challenges can arise: Budget Overruns: Due to the high-tech nature of cleanroom setups, costs can escalate quickly. Effective project management and contingency planning are essential to keep the project within budget. Delays in Supply Chain: Specialized equipment and materials such as specific filters and construction materials may have long lead times or limited availability, potentially delaying the project. Compliance Issues: Ensuring that every aspect of the cleanroom meets regulatory requirements is crucial. Any oversight can lead to failing certification, requiring costly modifications and retesting. Ongoing Maintenance and Monitoring Once operational, the cleanroom requires continuous monitoring and maintenance to ensure it continues to meet cleanliness standards: Routine Cleaning and Disinfection: Scheduled cleaning regimens using appropriate disinfectants and methods are essential to maintain the required levels of cleanliness. Regular Testing and Recertification: Ongoing testing of environmental conditions and periodic recertification ensure the cleanroom remains compliant with industry standards. Training Personnel: Continuous training for all personnel on proper cleanroom behavior is critical to prevent human-caused contamination. Conclusion Setting up a cleanroom from scratch is an intensive process that requires meticulous attention to detail at every stage, from design through to ongoing maintenance. This case study demonstrates the level of commitment and resources needed to ensure a cleanroom not only meets industry standards but also supports high-quality production or research activities effectively. The lessons learned here underscore the importance of careful planning, expert execution, and diligent maintenance in achieving and maintaining the optimal cleanroom environment. Read more: All About Cleanrooms - The ultimate Guide
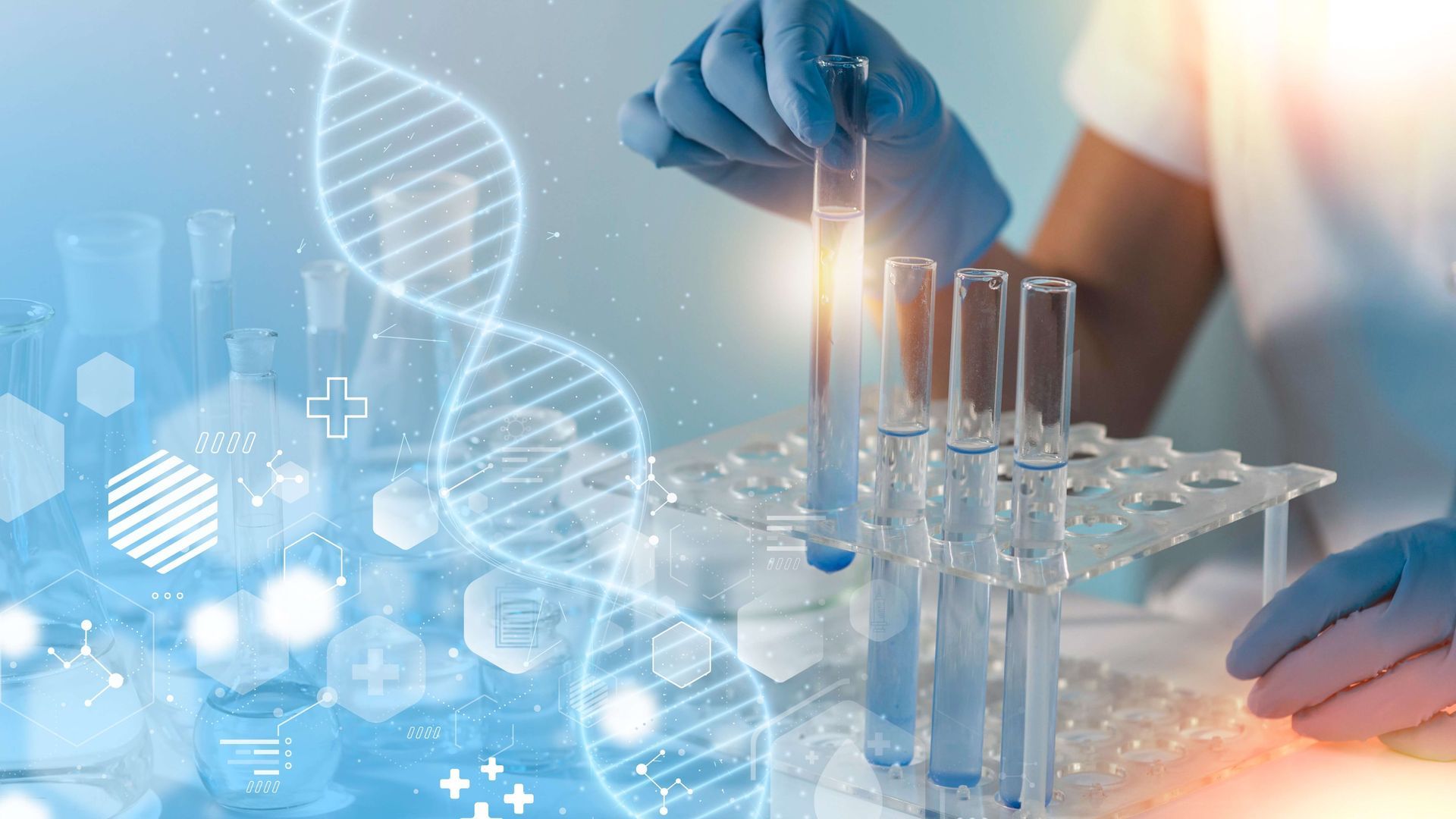
Introduction In the high-stakes environments of cleanrooms, where even minuscule contaminants can lead to costly product failures, robotics and automation play pivotal roles. Industries such as pharmaceuticals, semiconductors, and biotechnology rely on cleanrooms for the manufacturing of products that require environments free from dust, microbes, and other pollutants. This article explores the critical applications of robotics and automation in these settings, detailing how they enhance efficiency, precision, and contamination control. The Role of Robotics and Automation in Cleanrooms Cleanrooms demand stringent control of environmental conditions to prevent contamination. Human activity is one of the largest sources of contamination in these environments, shedding particles through skin flakes, clothing fibers, and cosmetics. Automation and robotics significantly mitigate this risk by minimizing human presence and intervention in critical areas. Reduced Contamination: Robots and automated systems do not produce contaminants that humans do, such as fibers or particles. They can be designed with smooth surfaces that are easy to clean and are made from materials that do not shed particles. Consistency and Precision: Automation provides consistent results in processes that require high precision. For instance, in semiconductor manufacturing, robots handle the intricate assembly of microchips with precision that far exceeds human capabilities, ensuring high yields and product quality. Increased Efficiency: Robots can operate continuously without breaks, fatigue, or the need for shifts, significantly increasing productivity. They can also perform tasks faster than human workers, further enhancing operational efficiency. Key Technologies in Cleanroom Robotics Several technologies have been developed to optimize the use of robotics and automation in cleanrooms: SCARA Robots: Selective Compliance Articulated Robot Arms (SCARA) are commonly used in cleanroom applications for tasks that require high-speed, high-precision handling and assembly. These robots are designed to operate in tight spaces and perform repetitive tasks with high accuracy. Cleanroom Cobots: Collaborative robots, or cobots, are designed to work alongside human operators safely. In cleanroom settings, cobots are equipped with features that minimize particle emission and are often used in delicate processes where gentle handling of sensitive materials is crucial. Mobile Robots: Autonomous Mobile Robots (AMRs) and Automated Guided Vehicles (AGVs) are used for transporting materials within cleanrooms. These robots are equipped with navigation and collision-avoidance systems, allowing them to move materials efficiently without human intervention. Advanced Vision Systems: Integrated vision systems in robots enable precise operations such as inspection, orientation, and placement of parts. These systems are crucial in industries like electronics, where they help identify defects that are imperceptible to the human eye. Implementation Challenges and Solutions Implementing robotics in cleanrooms is not without challenges. The initial investment in robotics technology can be high, and integrating these systems into existing processes may require significant redesigns and downtime. Moreover, maintaining robots in a cleanroom environment necessitates regular cleaning and sterilization to prevent them from becoming sources of contamination themselves. To address these challenges, companies often engage in pilot projects to measure the effectiveness and integration capacity of robotics before full-scale implementation. Regular maintenance and updates of robotic systems also ensure they operate at peak efficiency without compromising the cleanroom's cleanliness standards. Future Trends in Robotics for Cleanrooms The future of cleanroom robotics looks toward greater integration of AI and machine learning, enhancing the ability of robots to make decisions and perform complex tasks autonomously. Advances in materials science are also expected to produce new types of robots that shed even fewer particles, thus further reducing contamination risks. Conclusion Robotics and automation have become indispensable in the operation of cleanrooms across various industries. By enhancing precision, reducing contamination risks, and increasing efficiency, these technologies support the high-quality standards required in sensitive manufacturing processes. As robotic technology continues to evolve, its integration into cleanroom environments promises even greater improvements in product quality and operational efficiency, making it a critical component of modern manufacturing landscapes. Read more: All About Cleanrooms - The ultimate Guide
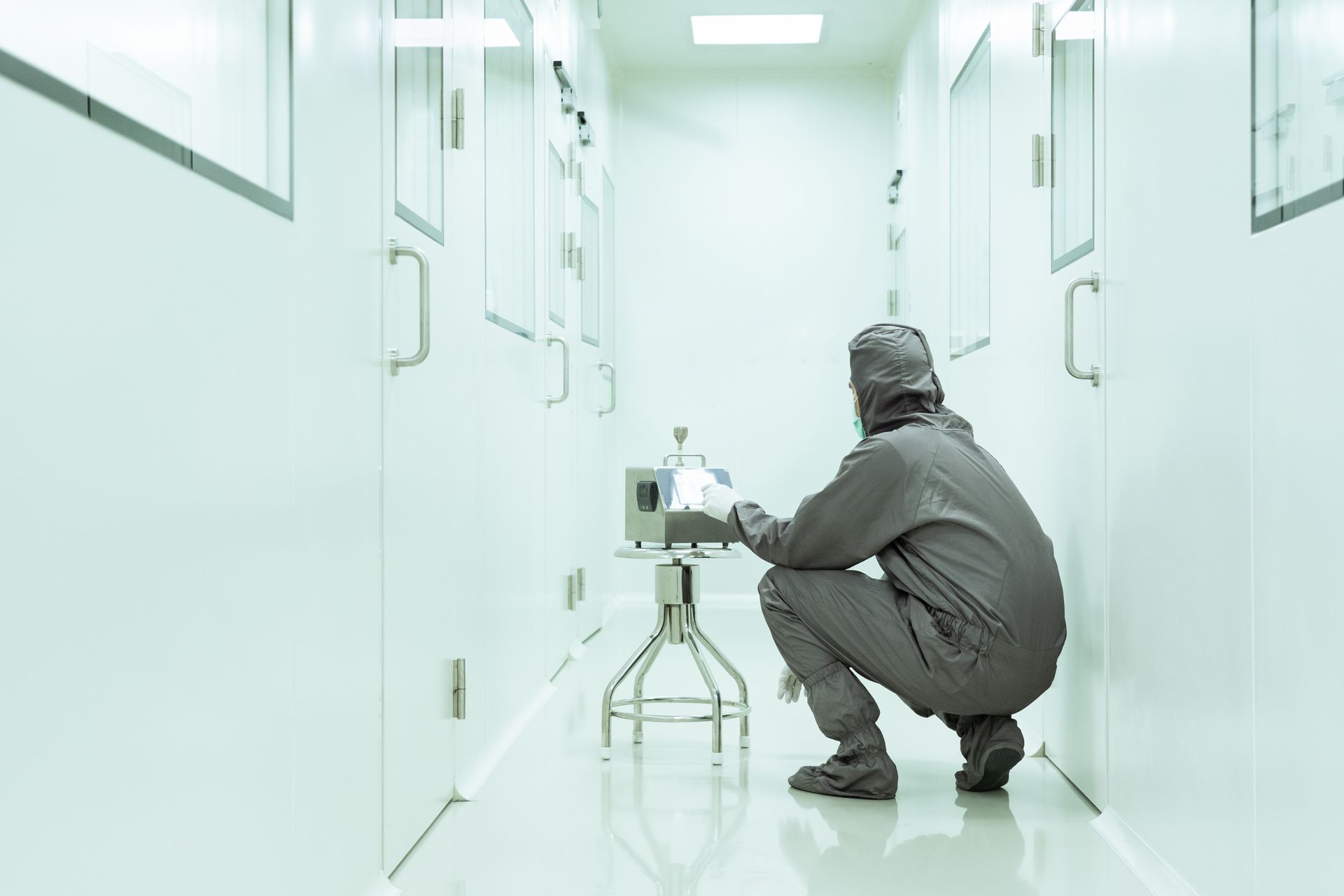
Introduction Environmental monitoring is a critical practice within cleanrooms, crucial for industries such as pharmaceuticals, biotechnology, electronics manufacturing, and many others where high standards of cleanliness and contamination control are essential. This detailed exploration provides insights into the strategies, technologies, and protocols involved in environmental monitoring, ensuring that cleanrooms meet stringent regulatory and quality standards. Importance of Environmental Monitoring in Cleanrooms Environmental monitoring involves the systematic sampling of air, surfaces, and personnel to detect contamination that can adversely affect the manufacturing process or the final product's quality. This process is integral to maintaining the controlled environment necessary for the production of high-quality, contamination-free products. Monitoring helps in identifying trends, pinpointing potential contamination sources, and verifying that cleanroom controls are effective. Key Components of Environmental Monitoring Airborne Particle Monitoring: This measures the concentration of particles in the cleanroom air, which could compromise product purity. Real-time monitoring devices capable of detecting particles as small as 0.1 microns are used to ensure compliance with standards like ISO 14644 or EU GMP Annex 1. Microbial Monitoring: Air, surfaces, and personnel are tested for microbial contamination. Methods include active air sampling, where air is passed over a culture medium to capture and grow microorganisms, and passive methods, such as settle plates, which expose a culture medium to the environment for a specified period. Surface Monitoring: This involves testing surfaces that come into contact with the product or that are in critical areas of the cleanroom. Techniques such as contact plates, swabs, or rinse samples are used to assess the presence of contaminants. Personnel Monitoring: Given that humans are significant sources of contamination, monitoring includes evaluating the microbial flora from the skin and garments of personnel working within the cleanroom. Technologies and Techniques for Environmental Monitoring Particle Counters: These devices are essential tools in cleanrooms. They provide continuous data on particle size and concentration in the air. Portable particle counters can be used for routine monitoring and for checking suspected problem areas. Air Samplers: These are used for microbial monitoring, capturing microorganisms on suitable growth media. The samples are then incubated and analyzed to determine the types and levels of microbial contamination. Rapid Microbial Methods (RMM): New technologies like ATP bioluminescence, PCR (Polymerase Chain Reaction), and flow cytometry offer faster, more sensitive alternatives to traditional culture techniques, providing quicker results and the ability to respond rapidly to contamination events. Environmental Monitoring Software: Advanced software systems are used to track and manage data from environmental monitoring activities. These systems help in trend analysis, data visualization, and compliance with regulatory requirements by providing detailed reports and real-time data access. Best Practices for Effective Environmental Monitoring Establishing a Baseline: It is crucial to establish baseline levels of contamination through initial intensive monitoring to understand the typical contamination profile of the cleanroom. Routine and Risk-Based Monitoring: Environmental monitoring should be a regular activity with additional intensive monitoring during high-risk operations such as product changeovers or after maintenance work. Proper Sampling Techniques: The effectiveness of monitoring programs depends on the correct techniques for sample collection, handling, and analysis. Training for personnel conducting these activities is essential. Response Procedures: Establishing clear procedures for responding to excursions from normal contamination levels is crucial. This includes investigation to identify the source of contamination and measures to prevent recurrence. Conclusion Environmental monitoring in cleanrooms is not just a regulatory requirement; it's a fundamental component of quality control, ensuring that products meet the required standards of purity and safety. By employing advanced technologies, adhering to best practices, and continuously analyzing monitoring data, organizations can maintain control over their cleanroom environments, thereby safeguarding their processes and products from contamination. This proactive approach not only helps in regulatory compliance but also supports the overall goal of excellence in manufacturing. Read more: All About Cleanrooms - The ultimate Guide
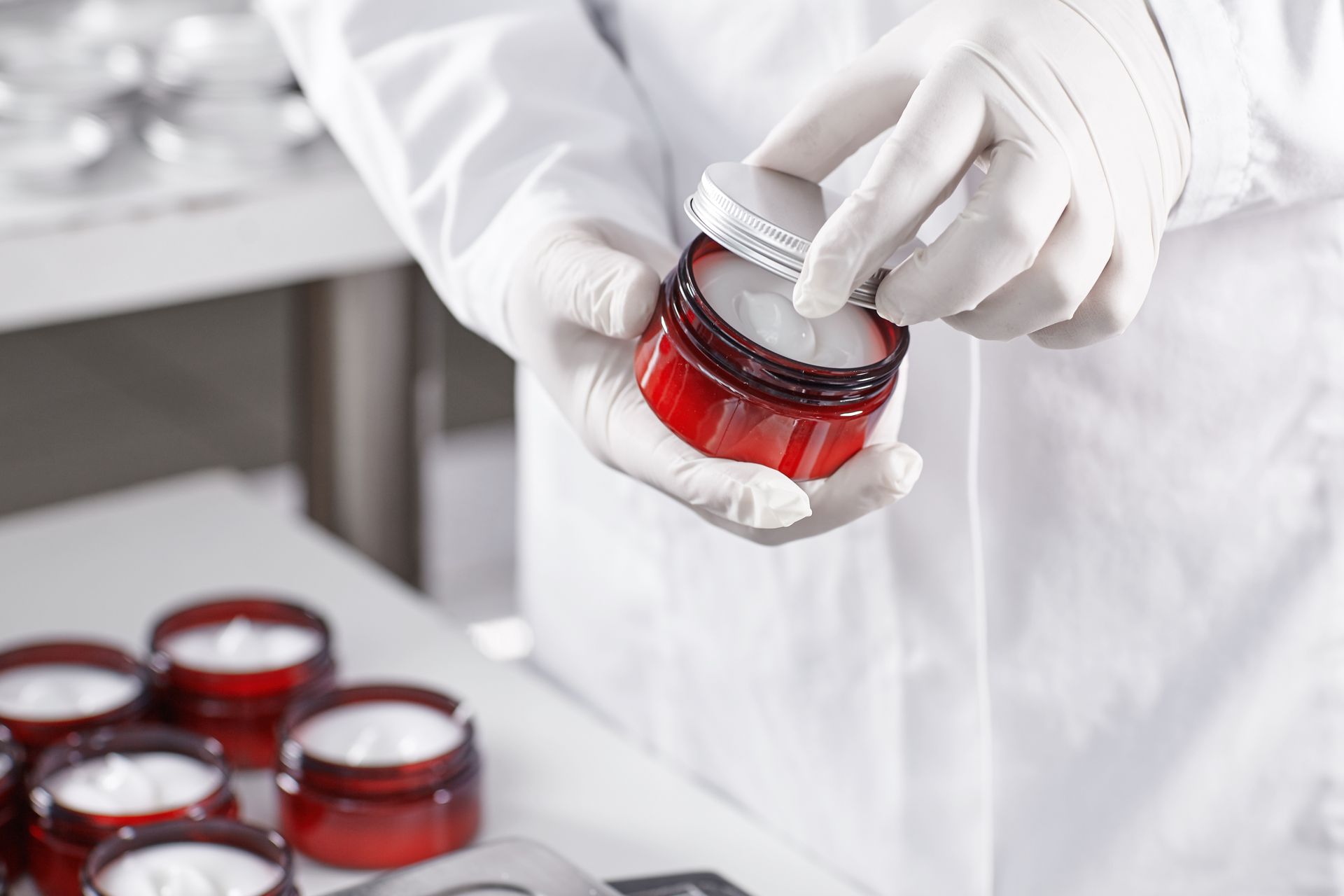
Introduction Cleanrooms are essential environments for industries where small particles can cause significant production issues, such as in semiconductor manufacturing, pharmaceuticals, biotechnology, and aerospace engineering. In these controlled environments, maintaining air quality and minimizing contaminants are critical to product integrity and compliance with regulatory standards. Environmental monitoring plays a pivotal role in this process, ensuring that the cleanroom conditions meet the stringent requirements necessary for high-quality production. This article delves into the sophisticated techniques and technologies used in cleanroom environmental monitoring, highlighting their importance and implementation. Fundamentals of Environmental Monitoring in Cleanrooms Environmental monitoring in cleanrooms is primarily concerned with the measurement and control of particles, but it also involves managing microbial contamination, temperature, humidity, and chemical vapors. The goal is to identify and quantify potential contaminants that could adversely affect the manufacturing process or product quality. Particle Counting: Particles are the primary concern in most cleanrooms. Monitoring their concentration involves using particle counters that can detect and quantify particles of various sizes, often as small as 0.1 microns. These devices operate either continuously or at specified intervals, providing real-time data to help maintain cleanroom standards. Microbial Monitoring: In pharmaceutical and biotechnology cleanrooms, controlling microbial contamination is crucial. Techniques include active air sampling, where air is pulled through a microbiological growth medium to capture and later culture organisms. Surface monitoring using contact plates or swabs that are subsequently cultured to identify and quantify microbial contamination is also common. Environmental Parameters: Besides particles and microbes, other environmental parameters such as temperature, humidity, and pressure are vital. Sensors and gauges are strategically placed throughout the cleanroom to provide continuous data, ensuring that conditions remain within necessary specifications to prevent product spoilage or process interruption. Advanced Techniques in Cleanroom Monitoring To achieve the high standards required in cleanroom environments, several advanced monitoring techniques are employed: Real-Time Continuous Monitoring Systems: These systems use sensors and particle counters integrated into the cleanroom’s HVAC system to provide continuous feedback on the environment. They can detect shifts in particle counts or other conditions immediately, enabling quick corrective actions. Optical Particle Counters (OPCs): OPCs provide high-resolution, real-time analysis of particle sizes and concentrations. These devices are crucial for semiconductor manufacturing where even the smallest particles can cause defects in microchips. Airborne Molecular Contamination (AMC) Monitors: AMC monitors are used to detect and measure levels of chemical vapors and gases that can adversely affect sensitive manufacturing processes, particularly in the electronics industry. Rapid Microbial Monitoring Technologies: New advancements in microbial detection offer faster results than traditional culture-based methods. Techniques such as ATP bioluminescence, PCR (polymerase chain reaction), and impedance microbiology allow for near real-time detection of microbial contamination, significantly reducing response times and improving production safety. Challenges and Solutions in Cleanroom Monitoring While environmental monitoring is critical, it poses several challenges, including the need for high sensitivity and accuracy, as well as ensuring minimal human intervention to avoid contamination. Automation and robotics have become part of the solution, handling routine monitoring tasks and thereby reducing human traffic in the cleanroom. Moreover, data integration systems that compile and analyze data from various sensors can provide a comprehensive view of the cleanroom’s status, facilitating better decision-making and predictive maintenance strategies. Conclusion Effective environmental monitoring in cleanrooms is a sophisticated blend of technology, methodology, and operational protocols. By employing advanced sensors, automated systems, and real-time data analysis, industries relying on cleanrooms can maintain the necessary conditions for producing high-quality, contamination-free products. As technology evolves, so too does the capability for more precise and efficient monitoring, ensuring that cleanrooms meet the exacting standards required both today and in the future. Read more: All About Cleanrooms - The ultimate Guide
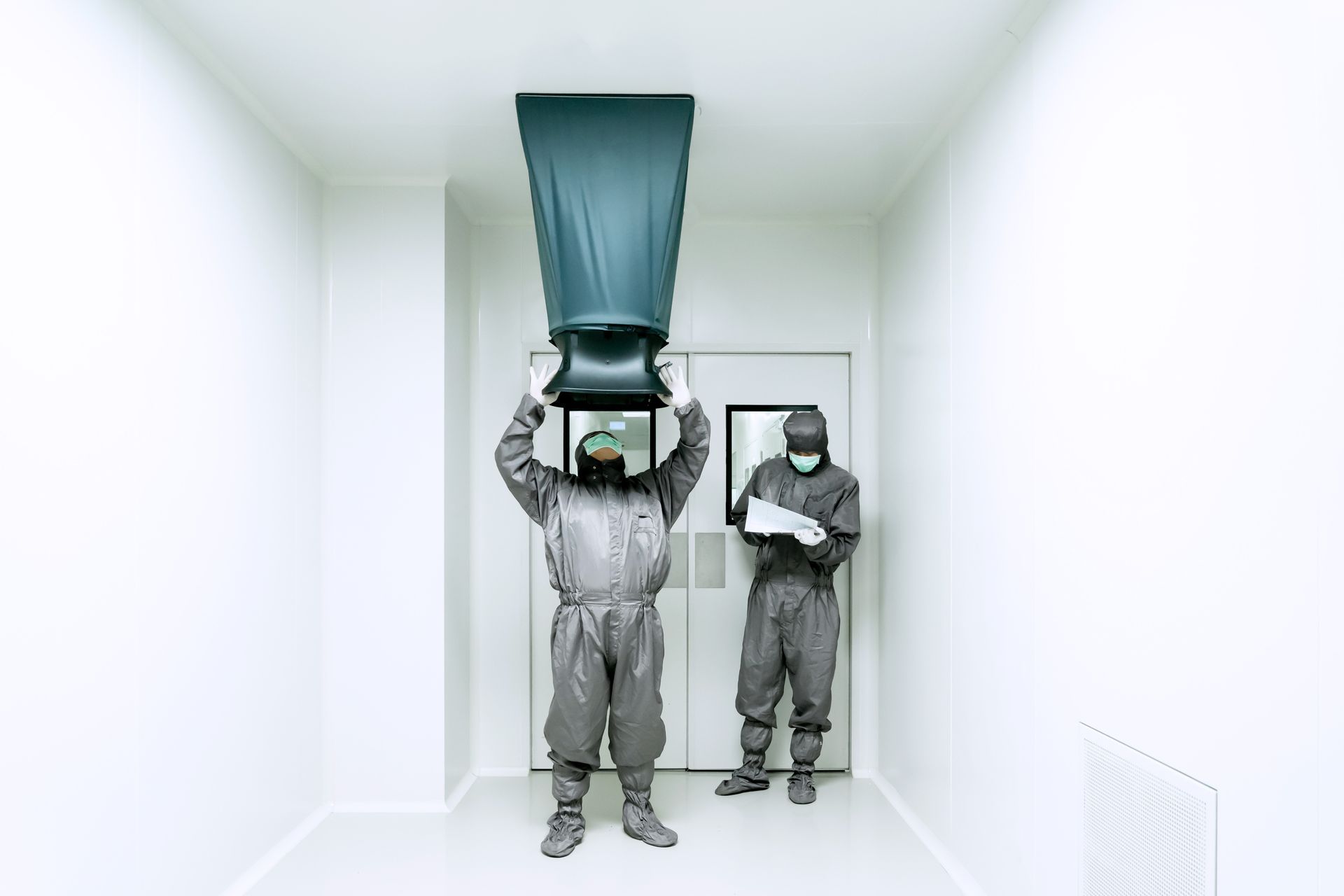
Introduction In the precise world of cleanroom environments, where the smallest particles can lead to the failure of complex manufacturing processes or compromise product sterility, air filtration plays a crucial role. High-Efficiency Particulate Air (HEPA) and Ultra-Low Particulate Air (ULPA) filters are the cornerstones of effective cleanroom contamination control, protecting products and processes from particulate pollutants. This article offers a detailed examination of how these filters work, their applications in various industries, and best practices for their maintenance and testing. Understanding HEPA and ULPA Filters HEPA Filters: Defined by their ability to trap 99.97% of particles that are 0.3 microns in diameter, HEPA filters are made from dense sheets of fiber (usually composed of fiberglass) arranged in a random matrix. The size of 0.3 microns is targeted because it represents the Most Penetrating Particle Size (MPPS), which is the most difficult size to filter out effectively. Particles that are larger or smaller than 0.3 microns are trapped with even higher efficiency due to mechanisms like impaction, interception, and diffusion. ULPA Filters: With an even higher standard, ULPA filters can remove at least 99.999% of dust, pollen, mold, bacteria, and any airborne particles with a size of 120 nanometers (0.12 microns) or larger. The increased density of the fibers in ULPA filters makes them suitable for environments where extremely low levels of particulate contamination are required. Mechanisms of Filtration The filtration mechanisms for HEPA and ULPA filters are a complex interaction of several physical processes: Interception: Particles following a stream of air come within one radius of a fiber and adhere to it. Impaction: Larger particles are unable to avoid fibers because of their inertia and are embedded directly into the fiber. Diffusion: Smaller, ultrafine particles move erratically, which increases the probability of hitting a fiber. Sieving: This happens when particles are larger than the spaces between fibers. These mechanisms ensure that HEPA and ULPA filters provide superior performance in critical environments where air purity is a non-negotiable aspect. Applications in Industries HEPA and ULPA filters find applications in various high-stake environments beyond traditional cleanrooms: Pharmaceuticals: Ensuring the sterility of pharmaceutical products, especially in aseptic processing and filling areas. Electronics and Semiconductors: Preventing particulate contamination in the fabrication of semiconductor chips, where even the smallest particle can cause defects. Biotechnology and Healthcare: Providing sterile environments for the production of biotech products and in hospitals to reduce the spread of airborne diseases. Aerospace and Optical Industries: Utilized in the manufacturing of aerospace components and optical devices which require very low levels of dust and other contaminants. Installation and Operational Considerations When installing HEPA and ULPA filters, several factors must be considered to maintain their efficacy: Airflow and Load Capacity: The filters must be matched with the HVAC system to handle the appropriate volume and speed of airflow without compromising the integrity of the filter media. Sealing and Framing: Proper sealing and secure framing are essential to prevent bypass air, which would allow unfiltered air to enter the cleanroom environment. Maintenance and Testing To ensure ongoing performance, HEPA and ULPA filters require regular maintenance and testing: Integrity Testing: Performed using a photometer or aerosol generator and detector to verify that there are no leaks or integrity issues with the filter installation. Load Testing and Replacement: Filters should be tested for pressure drop and loading to determine when replacement is necessary. This is critical to not exceed the filter's capacity, which can reduce its efficiency and increase operational costs. Regular Inspections: Visual inspections and checking for seal integrity can help catch issues before they lead to contamination problems. Conclusion HEPA and ULPA filters are pivotal in maintaining the critical environments necessary for high-quality production in various sensitive and high-precision industries. Understanding their function, proper installation, and diligent maintenance are key to ensuring these filters perform their role effectively, maintaining the sterile and contaminant-free conditions required in cleanrooms around the globe. As industries continue to advance, the role of these advanced filtration systems remains central to achieving the highest standards of cleanliness and operational excellence. Read more: All About Cleanrooms - The ultimate Guide
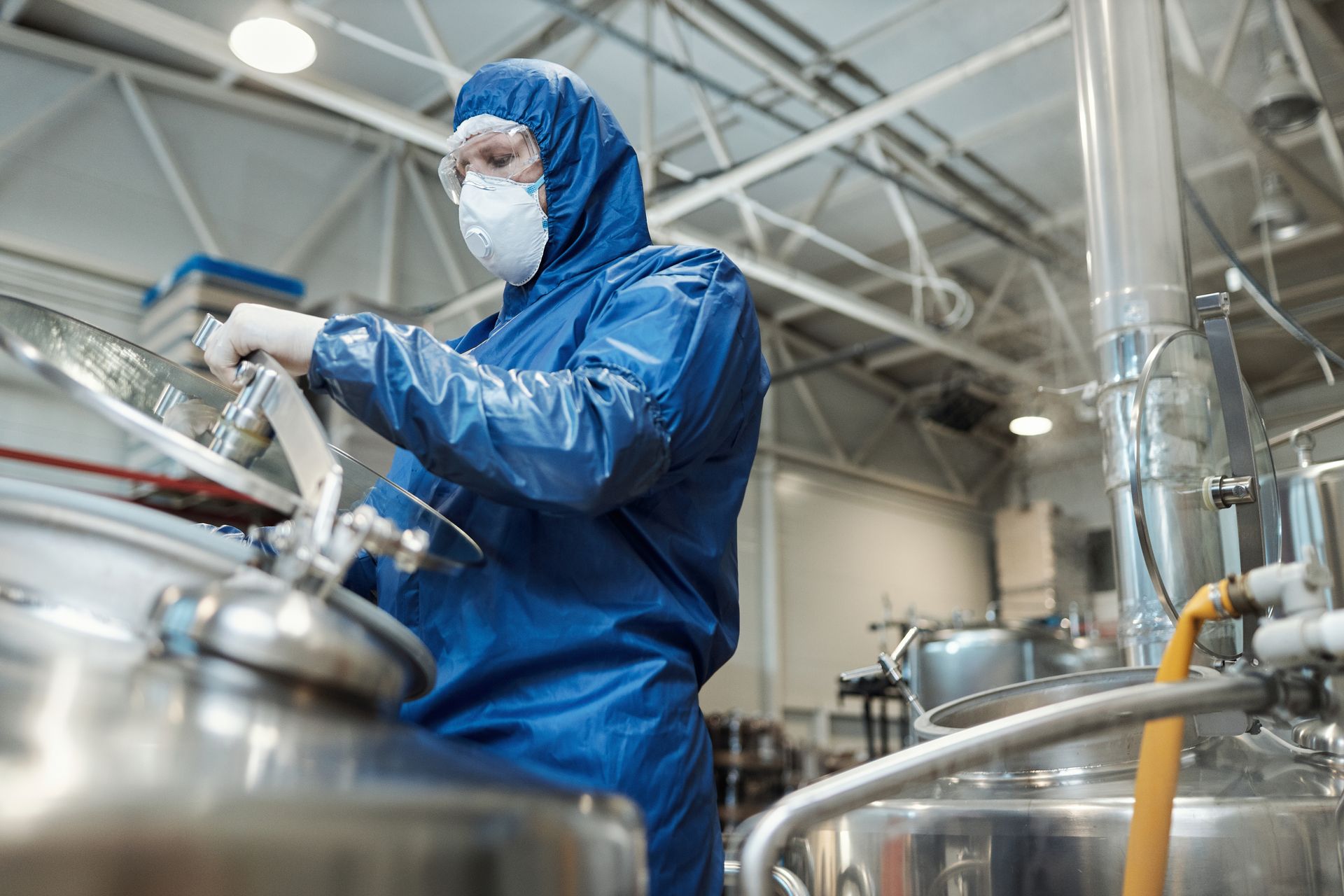
Introduction In the highly specialized world of cleanroom operations, cost management is crucial for maintaining efficiency without compromising the stringent environmental standards required for contamination-sensitive production environments. These controlled spaces, crucial in industries like pharmaceuticals, biotech, semiconductor manufacturing, and aerospace, demand precision not only in process control but also in financial oversight. This article explores the various strategies and considerations involved in optimizing cost management within cleanroom operations. Understanding Cleanroom Costs The operation of a cleanroom involves several key expenses: Construction and Design: The initial setup of a cleanroom is capital-intensive, involving specialized materials and technology to ensure air purity, controlled humidity, and temperature levels. The design must also facilitate easy cleaning and minimal particle generation. Equipment and Supplies: Cleanrooms require high-grade equipment that can operate without contaminating the environment. Regular purchases of consumables like gloves, gowns, and wipes add to the operational costs. Utilities and Maintenance: High-efficiency particulate air (HEPA) and ultra-low particulate air (ULPA) filters, which are essential for maintaining air purity, consume a significant amount of energy. Additionally, the maintenance of these systems, along with regular validation and calibration of equipment, incurs considerable expense. Personnel Training: S taff working in cleanrooms must be trained not only in the specific processes they will carry out but also in practices that prevent contamination. This training needs to be updated regularly to comply with industry standards and technological advancements. Strategies for Cost Optimization Optimizing the costs of cleanroom operations requires a multi-faceted approach: Energy Efficiency: I mplementing energy-efficient practices is crucial. For example, using variable speed drives on air handling units can reduce energy consumption. Additionally, the layout of the cleanroom can be designed to minimize the volume of space that needs to be conditioned, reducing energy costs. Technology Upgrades: I nvesting in automation can lead to significant cost savings in the long run. Automated systems reduce the risk of contamination and decrease the need for human intervention, thereby reducing labor costs and increasing process efficiency. Lean Manufacturing Principles: Applying lean principles can help minimize waste in cleanroom operations. This includes streamlining workflows, reducing redundancies in the movement of materials and personnel, and improving inventory management of consumables to avoid overstocking. Regular Maintenance and Calibration: Proactive maintenance of equipment and regular calibration can prevent costly downtime and repairs. Scheduled maintenance ensures that equipment operates at optimal efficiency, reducing the risk of unexpected breakdowns. Training and Development: Investing in comprehensive training programs for cleanroom staff can reduce contamination risks caused by human error, which are often much costlier to rectify than the training itself. Continuous improvement in operational protocols based on the latest industry standards can also drive efficiency. Real-Time Monitoring and Continuous Improvement Implementing real-time monitoring systems to track environmental parameters such as particle counts, temperature, and humidity levels can provide immediate feedback on cleanroom conditions. This data allows for quick adjustments and helps maintain the required standards consistently, preventing deviations that could lead to product failures and costly rework. Conclusion Cost management in cleanroom operations is a complex but crucial aspect of ensuring economic viability while meeting the rigorous standards required in sensitive production environments. By focusing on energy efficiency, technology upgrades, lean manufacturing, proactive maintenance, and robust training programs, companies can achieve a balance between cost and quality. Continuous improvement and real-time monitoring play pivotal roles in maintaining this balance, enabling organizations to stay competitive in industries where the margin for error is minimal. Read more: All About Cleanrooms - The ultimate Guide
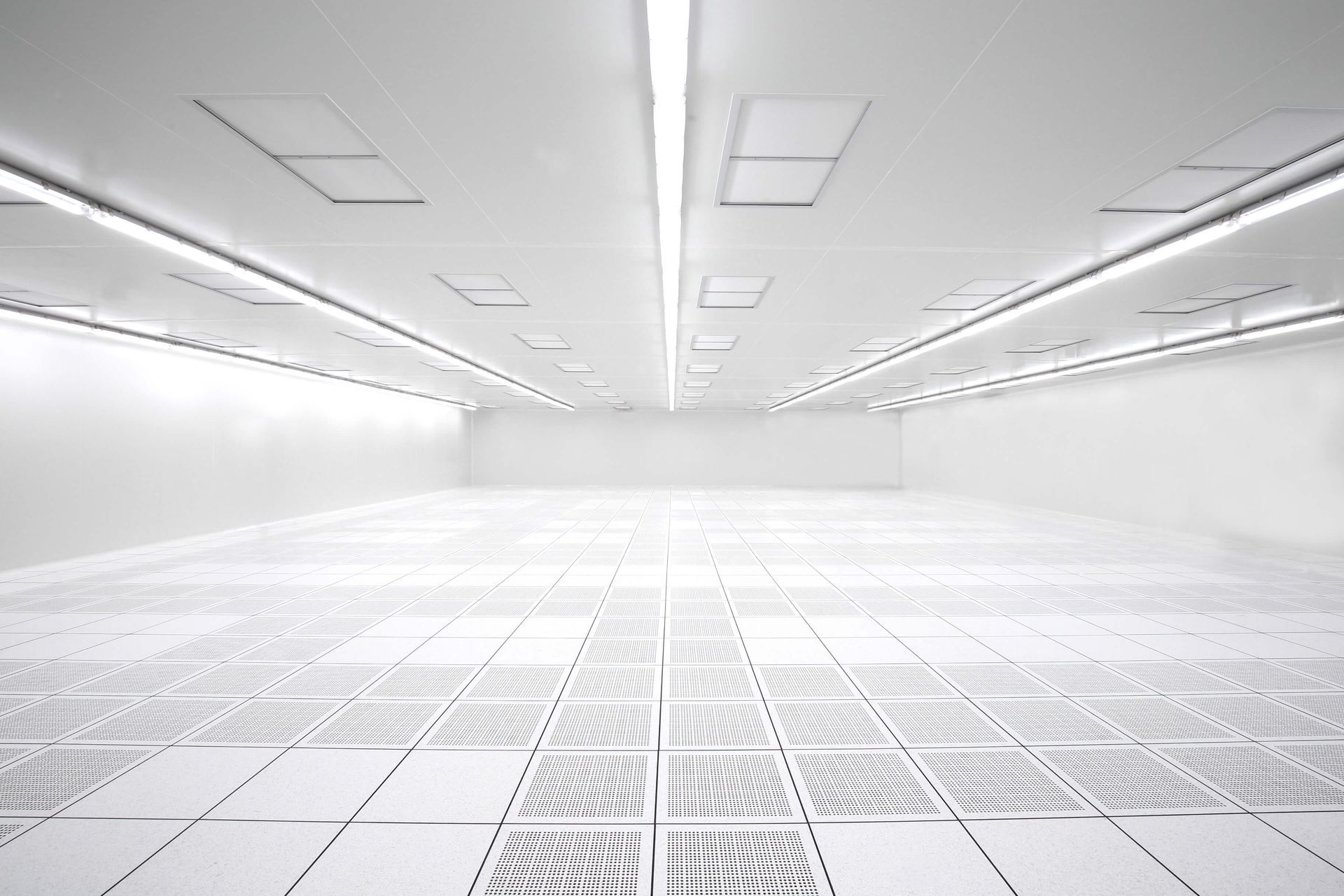
Introduction Cleanrooms are specialized environments with controlled levels of contamination that are used in industries such as pharmaceuticals, biotechnology, electronics, and aerospace manufacturing. The design and construction of cleanrooms are critical components that determine their effectiveness in controlling particulate and microbial contamination. This article delves into the complexities of cleanroom design and construction, offering a detailed overview of the considerations, technologies, and practices that ensure these environments meet stringent industry standards. Key Considerations in Cleanroom Design Designing a cleanroom involves more than just controlling the amount of dust in the air; it requires a holistic approach that addresses several critical factors: Classification and Standards: The first step in cleanroom design is determining the required cleanliness level, often defined by ISO 14644-1 or other relevant standards. This classification will dictate many aspects of the cleanroom's construction and operation, including air filtration needs, airflow patterns, and materials used. Airflow Management: Effective airflow design is crucial for preventing contamination. Cleanrooms typically use laminar or turbulent airflow systems. Laminar, or unidirectional, airflow systems direct filtered air downward in a constant stream. Turbulent, or non-unidirectional, airflow systems use random patterns that can still effectively dilute airborne contaminants. Pressure Differentiation: To prevent ingress of particles, cleanrooms maintain a positive pressure relative to adjacent less-clean areas. This means air flows out of, rather than into, the cleanroom when doors are opened. Material Selection: The materials used in cleanroom construction must be non-particle shedding and resistant to frequent cleaning and sometimes sterilization. Common choices include stainless steel, sealed concrete, and special non-shedding tiles for floors, and coated aluminum or stainless steel for walls and ceilings. Technologies Employed in Cleanroom Construction The integration of advanced technologies is essential for achieving and maintaining the desired cleanliness standards: HEPA and ULPA Filters: High-Efficiency Particulate Air (HEPA) filters and Ultra-Low Particulate Air (ULPA) filters are crucial in removing particles from the air. These filters can trap 99.99% of particles 0.3 microns in diameter or larger (HEPA) and even smaller particles (ULPA). HVAC Systems: Heating, ventilation, and air conditioning (HVAC) systems in cleanrooms are designed to not only control temperature and humidity but also to ensure proper filtration and airflow to avoid contamination. Control Systems: Modern cleanrooms are often equipped with sophisticated control systems that continuously monitor conditions such as temperature, humidity, and particulate levels. These systems can automatically adjust conditions to maintain the specified environment. Construction Practices and Challenges Building a cleanroom is a complex process that involves unique challenges: Modular vs. Traditional Construction: Modular cleanrooms are pre-fabricated and can be quickly assembled, offering flexibility and scalability. Traditional construction, while more time-consuming, is often required for large-scale or highly specialized applications. Sealing and Containment: Ensuring that all joints, fixtures, and fittings are sealed correctly is crucial for maintaining the integrity of the cleanroom. Even minor leaks can compromise the controlled environment. Compliance and Validation: Post-construction, cleanrooms must be validated to ensure they meet the specific standards. This process involves a series of tests for airflow, particle count, and microbial contamination, among others. Maintenance and Upkeep Post-construction, the challenge shifts to maintaining the cleanroom's performance: Regular Cleaning and Maintenance: Scheduled cleaning using appropriate materials and methods is vital. Additionally, regular maintenance checks on the HVAC systems and recalibration of sensors and filters are necessary to sustain performance. Staff Training and Protocols: Personnel working in cleanrooms must undergo rigorous training in contamination control practices, including proper gowning and behavior to minimize contamination. Conclusion The design and construction of cleanrooms are multifaceted processes that require detailed planning and expert execution. By understanding and implementing the various considerations and technologies outlined in this article, industries can effectively manage contamination risks and ensure that their cleanrooms operate at the peak of their potential. This not only enhances product quality but also complies with international regulatory standards, safeguarding the health and safety of consumers and the integrity of sensitive products.
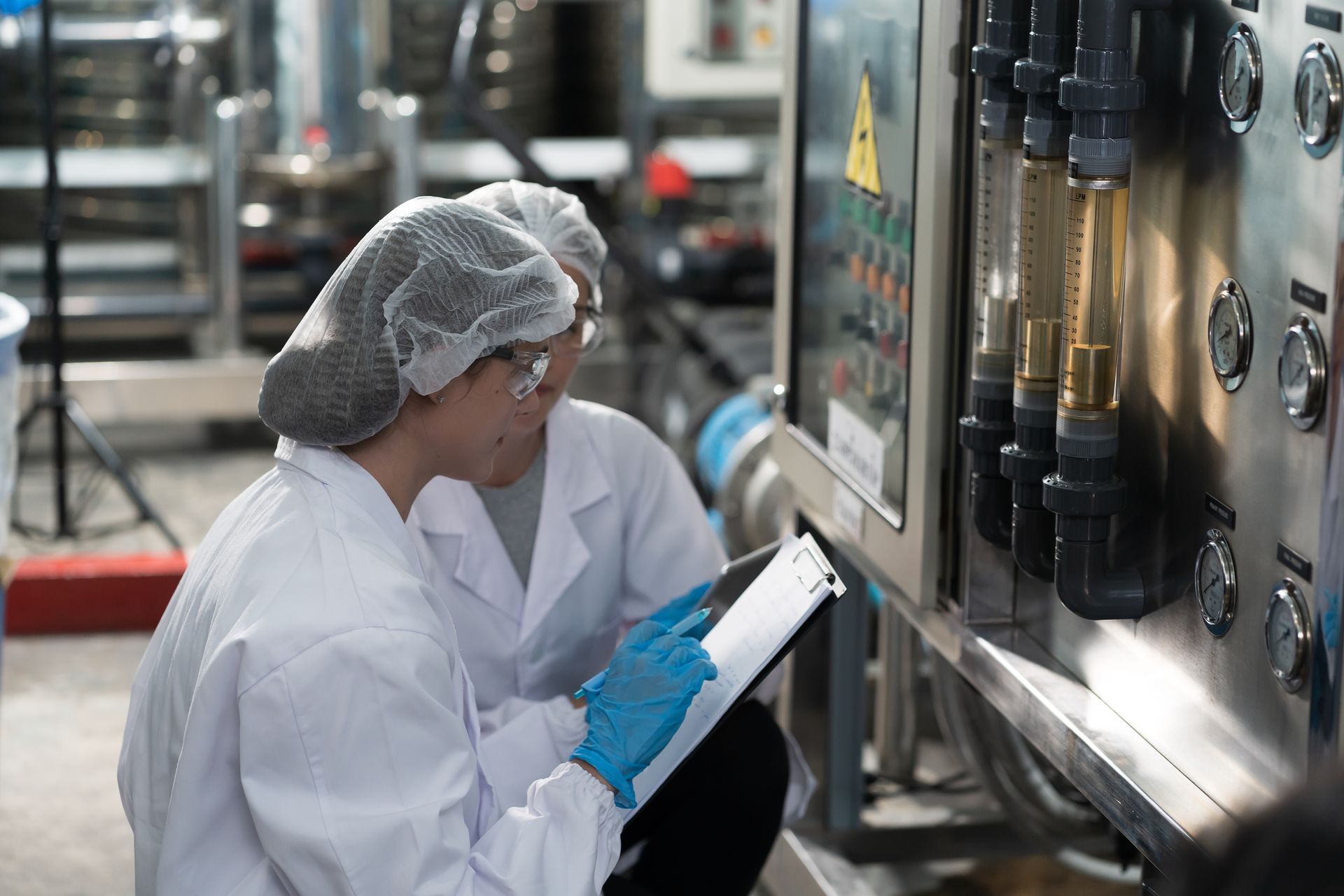
Introduction In the world of cleanroom technology, the effectiveness and reliability of filtration systems are paramount. Two critical standards that govern the performance and testing of High-Efficiency Particulate Air (HEPA) and Ultra-Low Particulate Air (ULPA) filters are EN 1822 and IEST-RP-CC001. These standards are instrumental in ensuring that filters meet stringent requirements, crucial for industries like pharmaceuticals, biotechnology, and semiconductors. Here, we delve deep into comparing these two standards, highlighting their similarities, differences, and impacts on filter technology. Overview of EN 1822 EN 1822, a European standard, is specifically designed for the classification, performance testing, and production monitoring of HEPA and ULPA filters used in cleanroom applications and other controlled environments. It is widely recognized in Europe and globally for its rigorous testing methodologies. The standard provides a detailed framework for determining the efficiency of filters by using the Most Penetrating Particle Size (MPPS), which ranges from 0.1 to 0.3 microns. The MPPS is recognized as the hardest particle size for a filter to capture, making this approach highly effective for assessing filter performance. Key features of EN 1822 include: Classification of Filters: The standard categorizes filters into several classes from E10 to U17, based on their efficiency at capturing particles of MPPS. Leak Testing: EN 1822 requires that each filter be individually tested for leaks to ensure there are no defects. Scan Testing: This involves scanning the filter media and frame for leaks using a particle counter to verify uniformity in performance. Overview of IEST-RP-CC001 Developed by the Institute of Environmental Sciences and Technology (IEST), the IEST-RP-CC001 provides guidelines for HEPA and ULPA filters regarding performance, testing, and specification. This standard is predominantly used in North America but also holds significance globally. IEST-RP-CC001 focuses on a comprehensive approach, including manufacturing practices, testing, and final certification of the filters. Highlights of IEST-RP-CC001 include: Testing Protocols: It outlines methods for testing filter efficiency and integrity, including aerosol testing and leak testing. Specification Guidance: The standard assists manufacturers in specifying conditions under which the filters should be tested, including airflow rates and particle concentrations. Quality Assurance: It mandates continuous quality assurance during production to ensure consistency in filter performance. Key Differences and Similarities While both standards aim to ensure the high quality and performance of HEPA and ULPA filters, there are notable differences in their approach and application: Methodology: EN 1822 focuses more on using the MPPS for determining filter efficiency, which is considered a more precise measurement, while IEST-RP-CC001 employs broader testing criteria which can vary based on specific conditions set by manufacturers. Application Scope: EN 1822 is stricter with its requirements and is generally used as a benchmark in Europe, whereas IEST-RP-CC001 offers more flexibility in testing and specification, making it versatile for different applications across industries. Leak Testing: Both standards include leak testing but differ in their methods and the extent of testing required, with EN 1822 often being seen as more stringent. Impact on Industries For industries reliant on cleanroom environments, choosing the right filter and corresponding standard is crucial. Pharmaceutical companies, for instance, might prefer EN 1822 for its stringent leak testing to prevent any cross-contamination, while semiconductor manufacturers might find the flexibility of IEST-RP-CC001 advantageous for adapting to different manufacturing environments. Conclusion Both EN 1822 and IEST-RP-CC001 play critical roles in shaping the effectiveness of filtration technologies in cleanrooms around the world. By understanding the nuances between these standards, companies can better decide which guideline aligns best with their operational requirements and regulatory obligations. As cleanroom technologies evolve, these standards will continue to be pivotal in guiding the development and implementation of next-generation filters that meet the increasing demands of industries requiring controlled environments. Read more: All About Cleanrooms - The ultimate Guide
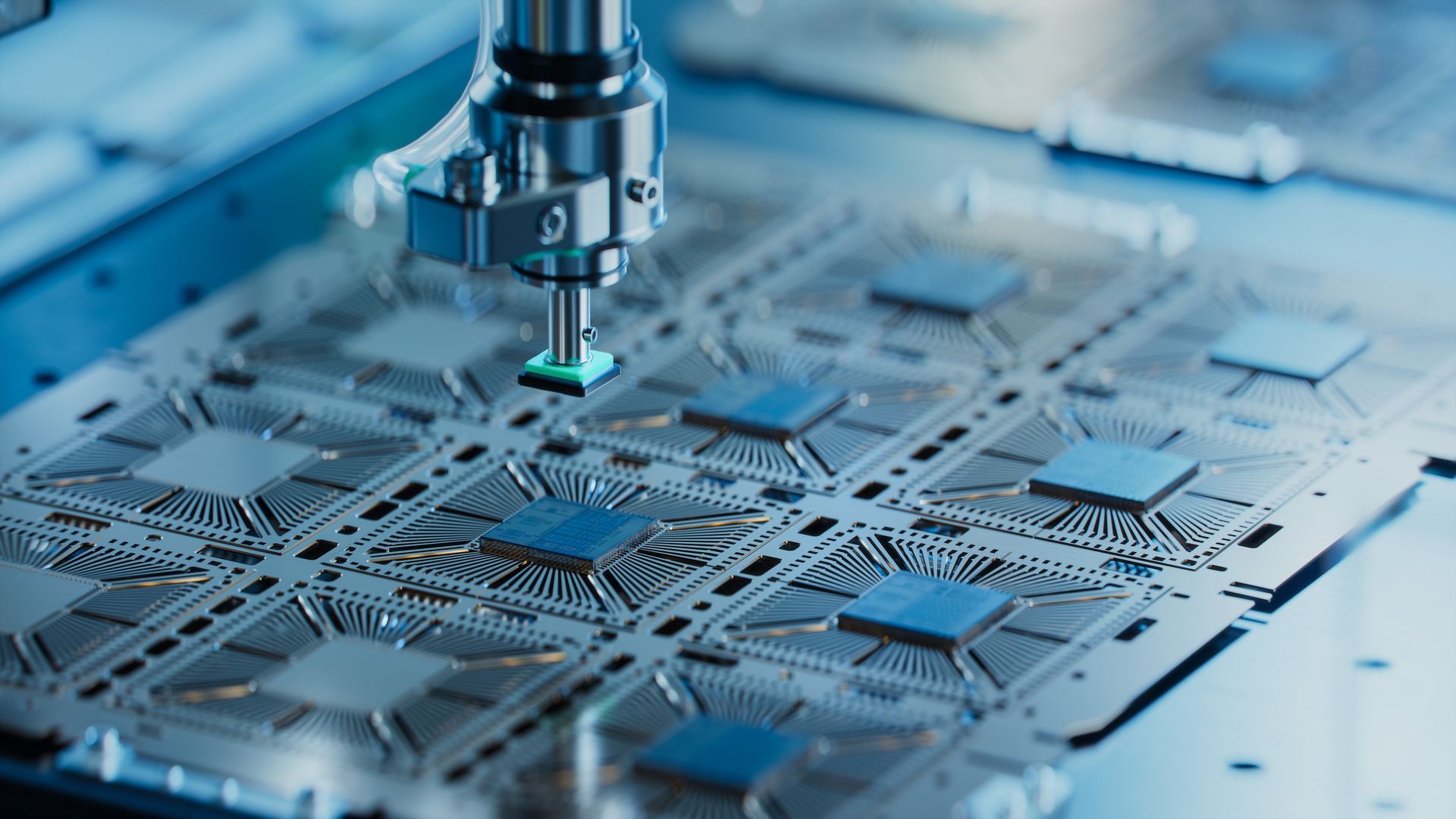
Introduction In industries where the slightest impurity can disrupt the manufacturing process or compromise product quality—such as in semiconductor fabrication, pharmaceutical production, and biotechnological applications—maintaining an immaculate cleanroom environment is crucial. This article delves into the fundamentals of contamination control within cleanrooms, exploring the sources of contaminants, strategies to mitigate them, and the importance of continuous monitoring to ensure compliance with industry standards. Understanding Sources of Contamination Contamination in cleanrooms can originate from several sources, commonly categorized into two types: particulate and microbial. Particulate contaminants include dust, skin flakes, and clothing fibers, which can originate from both inanimate objects and human operators within the cleanroom. Microbial contaminants, on the other hand, stem from bacteria, fungi, and viruses, which are often introduced by human operators or enter through inadequate filtration systems. Human-Related Contaminants: The human body is a significant source of contamination in cleanrooms. Operators can shed skin cells, hair, and emit body vapors, all of which can compromise the sterile environment. Equipment and Materials: Particulates can also be emitted from the degradation of cleanroom materials and equipment, including peeling paint, corroding metals, or outgassing from plastics used within the room. External Environment: Contaminants can infiltrate cleanrooms through air handling systems if filters are not properly maintained or if there are leaks in the containment structures. Strategies for Minimizing Contamination Effective contamination control in cleanrooms involves a multifaceted approach, combining stringent procedural protocols with state-of-the-art technologies designed to maintain an ultra-clean environment. Cleanroom Design and Air Filtration: The design of a cleanroom plays a pivotal role in contamination control. High-efficiency particulate air (HEPA) filters or ultra-low particulate air (ULPA) filters are used to trap particles as small as 0.1 to 0.3 microns. The cleanroom should also be designed to ensure proper airflow patterns, typically employing a unidirectional (laminar) flow that sweeps particles in a single direction, towards the filters. Controlled Access and Behavior: Entry and exit protocols are strictly regulated. Personnel must undergo comprehensive gowning procedures, using garments made from non-shedding materials, before entering cleanroom spaces. Additionally, behavior inside the cleanroom is subject to rigorous standards, including restrictions on rapid movements and guidelines for cleaning and maintenance activities. Regular Cleaning and Maintenance: Routine cleaning schedules are essential to maintain cleanliness standards. This includes the use of cleanroom-approved disinfectants for surfaces and specialized vacuum cleaners equipped with HEPA filters for floors and walls. Preventative maintenance of cleanroom equipment and immediate repair of any detected leaks or damages also help minimize risks of contamination. Material and Equipment Decontamination: Before introducing any new material or equipment into the cleanroom, it must be cleaned and, if necessary, sterilized according to the cleanroom’s standards. This might involve using autoclaves, UV-C light, or chemical disinfectants to ensure that these items do not introduce contaminants. Monitoring and Validation Continuous monitoring of environmental conditions within the cleanroom is crucial for early detection of deviations from standard cleanliness levels. This typically involves: Particle Counting: Real-time particle counters can detect increases in particulate levels, allowing for immediate corrective actions. These devices are critical for ongoing compliance with ISO class standards. Microbial Monitoring: Regular sampling of surfaces and air within the cleanroom for microbial contamination helps assess the efficacy of cleaning protocols and identify potential biological hazards. Airflow and Pressure Differential Testing: Ensuring that air pressure levels are appropriate and that the airflow patterns are uninterrupted can prevent the inflow of contaminants from less clean areas. Conclusion Contamination control in cleanrooms is a dynamic and complex task that requires a detailed understanding of contamination sources and a proactive approach to designing and implementing control strategies. It also demands rigorous training for all personnel and a commitment to continuous improvement and monitoring. By adhering to these principles, industries reliant on cleanroom environments can maintain the integrity of their manufacturing processes and produce high-quality, uncontaminated products. Read more: All About Cleanrooms - The ultimate Guide
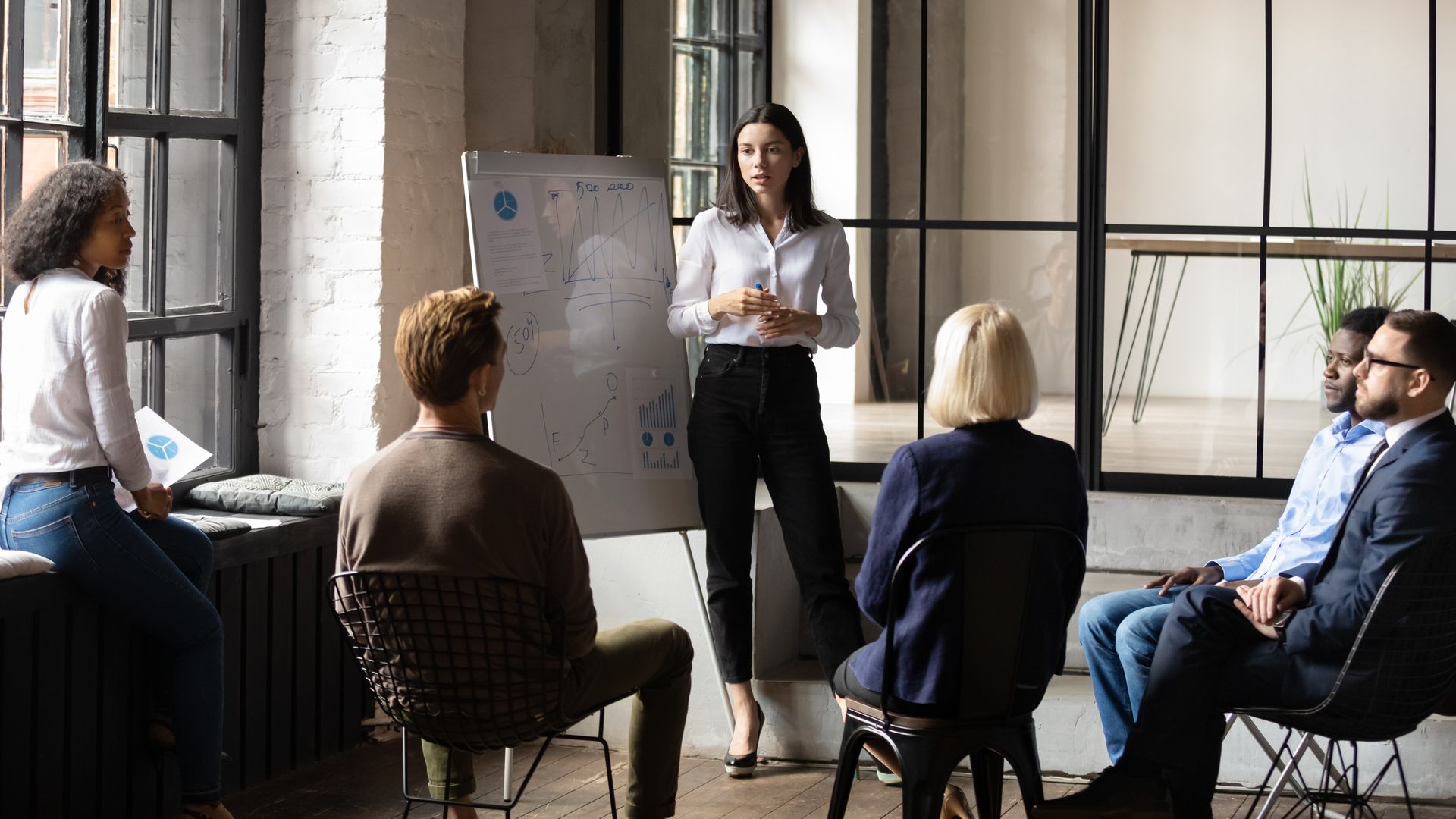
Introduction Cleanroom environments are specialized workspaces designed to maintain extremely low levels of environmental pollutants such as dust, airborne microbes, aerosol particles, and chemical vapors. These environments are crucial in industries such as pharmaceuticals, biotech, medical device fabrication, and semiconductor manufacturing. Due to the critical nature of the work conducted in these spaces, personnel must undergo comprehensive training. This article explores the components, importance, and outcomes of cleanroom training and education programs. 1. The Importance of Cleanroom Training In sectors where cleanrooms are employed, the smallest contamination can result in product failures, costly downtime, and health risks. Therefore, cleanroom training is not just a regulatory requirement but a critical investment in quality assurance and safety. It ensures that all personnel understand how their actions can affect cleanroom integrity and are skilled in preventing contamination. 2. Key Components of Cleanroom Training Programs Cleanroom training programs are typically tailored to the specific requirements of the industry and the individual facility, but there are several key components that are generally covered: Introduction to Cleanroom Standards and Protocols: Trainees learn about the standards that govern cleanroom operations, such as ISO 14644 and US Federal Standard 209E, which classify cleanrooms based on the cleanliness level of the air. Behavior and Cleanliness Protocols: This involves training on the proper gowning procedures, including the sequential steps to put on and take off cleanroom garments correctly. Additionally, personnel are taught how to behave inside a cleanroom to minimize the generation of contaminants. Equipment and Materials Handling: Proper techniques for handling tools, equipment, and materials within a cleanroom. This includes understanding how to clean and sanitize items before bringing them into a clean environment. Cleanroom Maintenance: Regular cleaning and maintenance protocols are essential to keep the cleanroom within the required standards. This section covers everything from daily cleaning procedures to the more thorough cleanings that might involve entire system shutdowns. Emergency Procedures: Training also includes responses to emergencies, such as chemical spills, breaches in cleanroom protocol, or equipment failures that could compromise the clean environment. 3. Delivery Methods and Educational Tools Training methods in cleanroom education can vary from in-person workshops and seminars to online courses and virtual simulations. The latter has become increasingly popular, offering interactive and immersive learning experiences that can simulate a variety of cleanroom scenarios without the risk of actual contamination. Hands-on Training: This is critical as it allows trainees to practice gowning procedures, cleanliness practices, and emergency responses in a controlled, supervised environment. Video Demonstrations: Often used to show correct procedures in a visually engaging way, helping to reinforce best practices among trainees. Regular Assessments and Certification: Testing is a regular feature of training programs, ensuring that knowledge is retained and applied. Certification, either from a recognized body or the training institution, helps in maintaining a qualified workforce. 4. Who Needs Cleanroom Training? Cleanroom training isn't just for new employees. It is crucial for everyone involved in cleanroom operations, from janitorial staff to engineers and management. Regular refresher courses are also important to ensure that all personnel are up-to-date with the latest standards and techniques. 5. Benefits of Effective Cleanroom Training Investing in high-quality cleanroom training has numerous benefits: Reduced Risk of Contamination: Well-trained staff significantly lower the risk of contamination, leading to higher product quality and fewer batch failures or product recalls. Regulatory Compliance: Effective training ensures compliance with industry regulations, which can protect against legal or regulatory penalties. Employee Confidence and Retention: Employees who are well-trained are more confident in their roles, which enhances job satisfaction and retention rates. Cost Efficiency: Reducing contamination reduces waste, thereby saving on material costs and avoiding expensive downtime needed for decontamination. Conclusion Cleanroom training and education programs are essential for maintaining the stringent cleanliness standards required in critical industries. By investing in thorough and effective training, companies can ensure that their products meet the highest standards of quality and safety, while also adhering to relevant regulatory requirements. This training not only supports compliance and operational excellence but also fosters a culture of continuous improvement and professionalism in high-tech industrial environments. Read more: All About Cleanrooms - The ultimate Guide
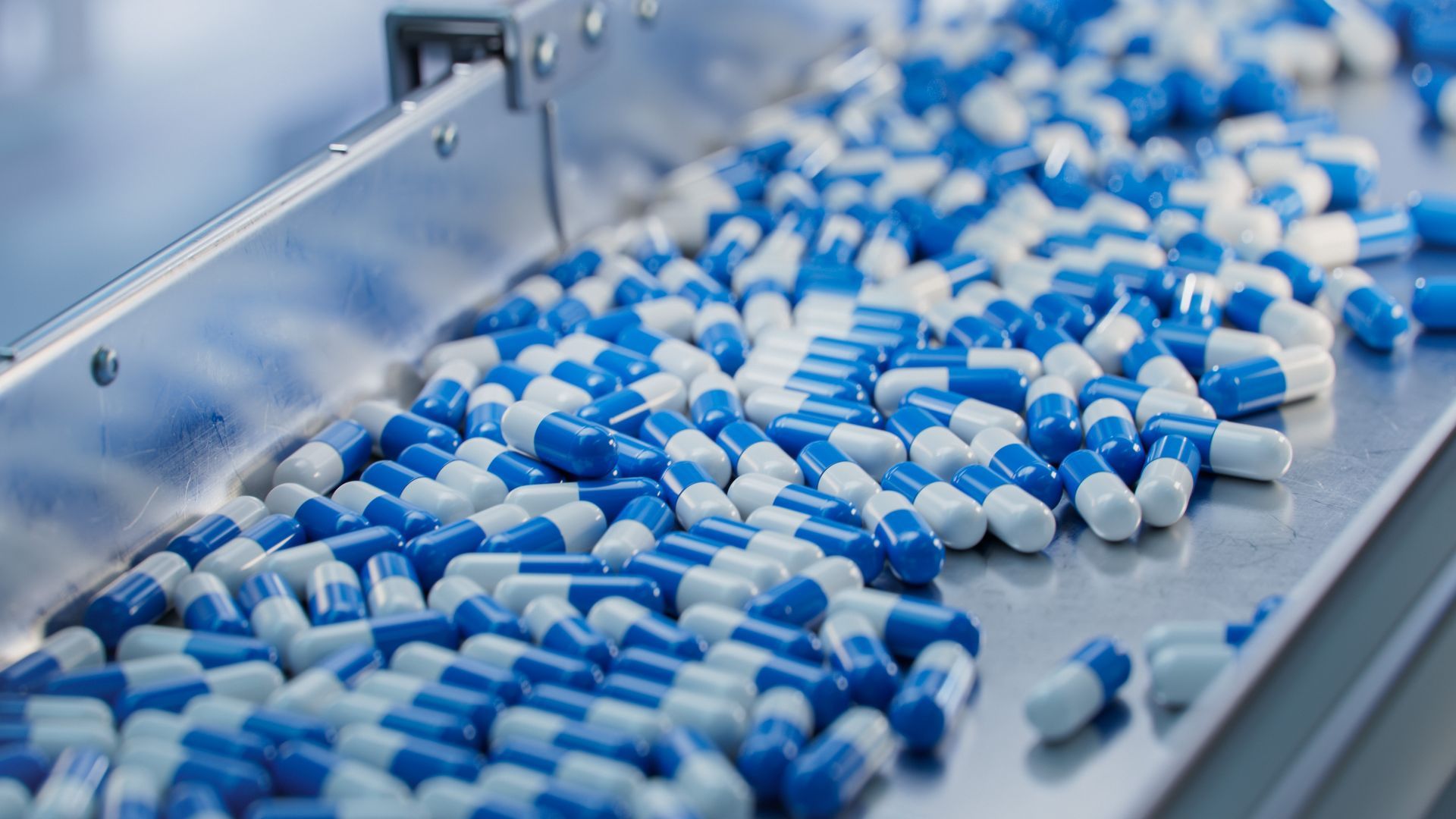
Introduction Cleanrooms are essential environments used in various industries such as pharmaceuticals, biotechnology, and electronics manufacturing where the presence of environmental pollutants like dust, airborne microbes, and aerosol particles must be minimized. These environments are regulated by stringent standards and certifications to ensure that they meet specific cleanliness levels required for the manufacturing processes conducted within them. In this article, we will delve into the complexities of cleanroom standards and certifications, highlighting their importance, the key standards used globally, and how organizations can achieve and maintain these standards. The Importance of Cleanroom Standards Cleanroom standards are critical as they define the level of cleanliness that must be maintained in a controlled environment to prevent contamination. The standards specify the maximum allowable number of particles, measured in microns, for a given volume of air. This is crucial for industries where even minuscule particles can cause significant damage to the manufacturing process, such as in the production of microchips or sterile pharmaceutical products. Key Cleanroom Standards The most commonly referenced standards for classifying cleanroom cleanliness levels are the ISO (International Organization for Standardization) 14644 series, the retired Federal Standard 209E (FS 209E), which was used primarily in the United States before being superseded by ISO standards, and the EU GMP standards including its crucial Annex 1. ISO 14644 Standards: T his series of standards includes different parts that cover various aspects of cleanroom technology, from the classification of air cleanliness to testing and monitoring methods. For example, ISO 14644-1 defines cleanroom classes based on the concentration of particles in the air of different sizes, ranging from 0.1 microns to 5 microns. A lower class number (e.g., ISO 5) corresponds to a cleaner environment, with fewer allowed particles per cubic meter. Federal Standard 209E: Although no longer in official use, FS 209E still influences cleanroom specifications, especially in legacy systems and in some U.S. industries. It categorized cleanrooms from Class 1 to Class 100,000, where the class number directly indicated the number of particles 0.5 microns or larger allowed per cubic foot of air. EU GMP and Annex 1: The European Union’s Good Manufacturing Practices (EU GMP) guidelines provide regulatory standards for the manufacture of sterile pharmaceutical products. Annex 1 of these guidelines specifically addresses the manufacture of sterile medicinal products, ensuring a high level of cleanliness through stringent requirements for cleanroom design, operation, and monitoring. It sets standards for particle and microbial contamination and focuses extensively on risk assessment, aseptic processing, and cleanroom qualification. Achieving Certification Achieving cleanroom certification involves several steps, starting with the design and construction of the cleanroom to meet the desired standard. This process includes selecting the appropriate cleanroom architecture, HVAC systems, and filtration systems that can achieve and maintain the required air purity levels. The layout must also facilitate proper airflow patterns to prevent the accumulation of contaminants. Once a cleanroom is constructed, it must undergo rigorous testing and validation to ensure it meets the specified standards. This testing is typically performed by certified professionals who use specialized equipment such as particle counters and microbial samplers. Common tests include: Airborne Particle Count Testing: To verify that the particle count meets the specified classification. Recovery Testing: To determine how quickly the cleanroom returns to its baseline particle count after a contamination event. Airflow Testing: To ensure that airflows correctly through the cleanroom, maintaining proper cleanliness levels throughout the area. Maintaining Certification Maintaining cleanroom certification requires ongoing monitoring and adherence to strict operational protocols. Regular testing must be conducted to ensure continuous compliance with the set standards. Additionally, all personnel working in cleanrooms must follow stringent procedures, including wearing proper cleanroom suits and adhering to cleaning and sanitation protocols. Training is also a crucial component, as employees must understand the importance of contamination control and how their actions can impact cleanroom cleanliness. Regular audits and inspections help ensure that procedures are followed correctly and that the cleanroom environment remains in compliance with the necessary standards. Conclusion Understanding and adhering to cleanroom standards and certification processes are crucial for industries that rely on controlled environments. These standards are not only a regulatory requirement but also a quality assurance measure that helps prevent contamination, ensuring the safety and effectiveness of products manufactured in these critical environments. By maintaining strict adherence to these standards, companies can avoid costly contamination issues and uphold their reputation for quality in highly competitive markets. Read more: All About Cleanrooms - The ultimate Guide
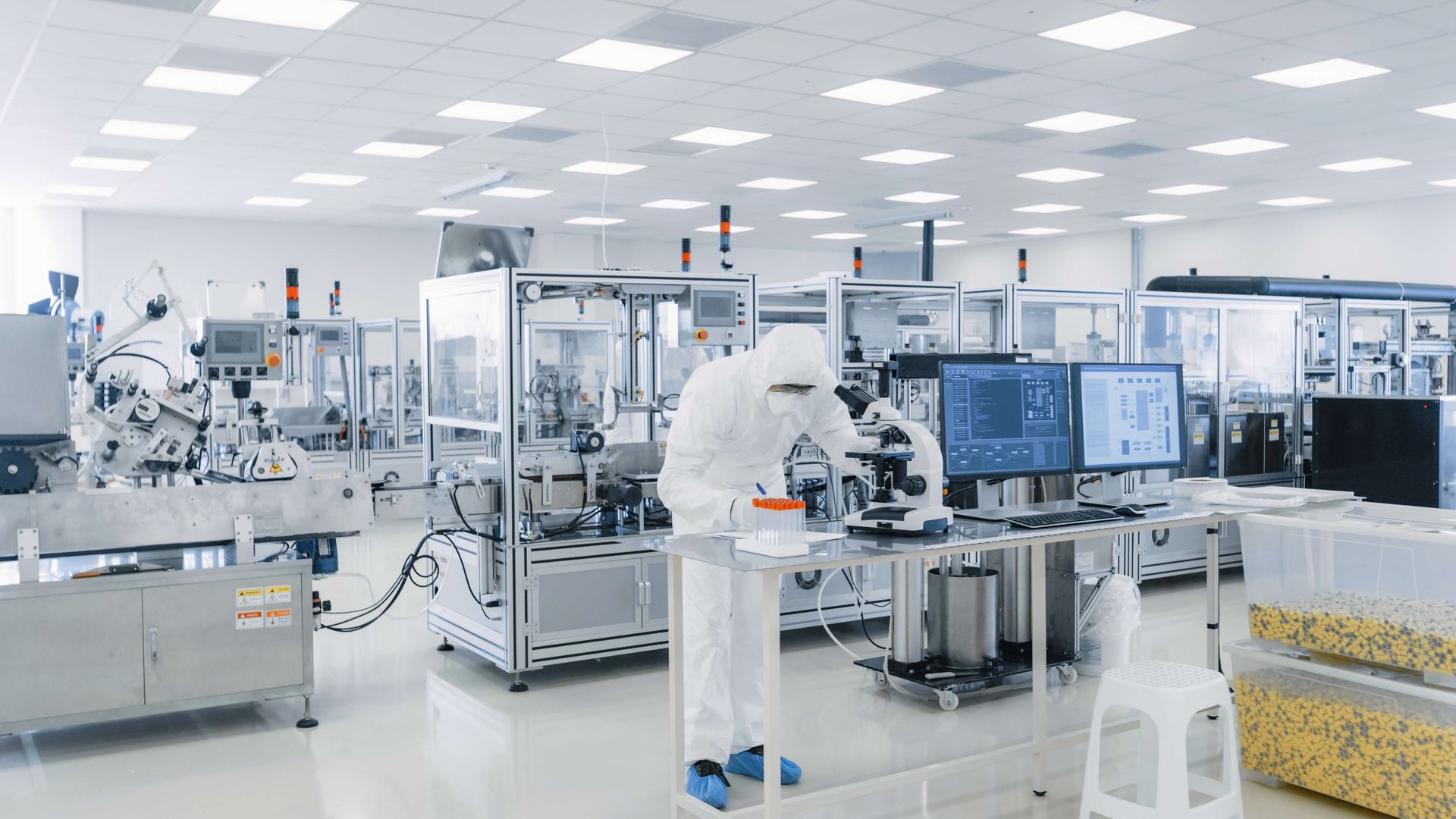
Introduction As industries like pharmaceuticals, biotechnology, semiconductor manufacturing, and aerospace continue to expand and evolve, the cleanrooms used in these fields must also adapt to meet new challenges and leverage emerging technologies. The future of cleanroom design and operation is likely to see significant advancements driven by innovations in technology, increased regulatory demands, and a greater focus on sustainability and efficiency. This detailed article explores the trends that are shaping the future of cleanroom design and operation. Automation and Robotics One of the most significant trends in cleanroom design and operation is the increased use of automation and robotics. Automation technology can reduce the need for human operators, who are often sources of contamination due to shedding skin cells, hair, and fibers from clothing. Robots and automated systems can perform repetitive or precision-based tasks with minimal risk of error and contamination, enhancing both the efficiency and reliability of cleanroom operations. For instance, in pharmaceutical manufacturing, robotic arms can handle the filling and packaging of sterile products. In semiconductor manufacturing, automation can be used to transport silicon wafers through various processing stages under tightly controlled conditions. The future will likely see an integration of AI with robotics to further optimize processes and predictive maintenance, reducing downtime and increasing productivity. Advanced Materials and Surfaces The development of new materials and surface treatments is crucial for the future of cleanrooms. Innovations in materials science are producing surfaces that are resistant to microbial growth and easy to clean, reducing the risk of contamination. For example, antimicrobial coatings that inhibit the growth of bacteria and fungi on cleanroom surfaces can significantly enhance cleanliness standards. Additionally, materials that generate fewer particles, such as advanced polymers and non-shedding metals, are being developed. These materials are not only used in the construction of cleanroom walls and floors but also in the manufacturing of furniture and equipment used within the cleanroom. Enhanced Filtration Technologies Filtration technology is at the heart of cleanroom design, and future advancements are expected to provide even higher levels of air purity. The development of more efficient HEPA and ULPA filters, capable of trapping nanoparticles, is ongoing. Moreover, innovations such as customizable filters that can adapt to specific contaminant types based on real-time air quality monitoring are on the horizon. This adaptive filtration technology could dynamically adjust the level of filtration needed based on the current state of cleanroom contamination, leading to more energy-efficient operations and prolonged filter lifespans. Energy Efficiency and Sustainability As energy efficiency becomes a more critical concern globally, future cleanroom designs will likely emphasize sustainability. Traditional cleanrooms are energy-intensive due to the need for constant air filtration and temperature control. Future trends may include the integration of energy recovery systems, which reuse the energy generated by cleanroom operations to heat or cool the rooms as necessary. Additionally, the use of more efficient LED lighting, energy-star-rated equipment, and the incorporation of green building materials are trends that help reduce the carbon footprint of cleanroom operations. The use of solar panels and other renewable energy sources could also become more prevalent. Real-Time Monitoring and IoT Integration The integration of Internet of Things (IoT) technology in cleanroom environments is set to revolutionize how these facilities are monitored and managed. IoT sensors can continuously collect data on various parameters such as temperature, humidity, particle count, and air pressure. This data can be analyzed in real-time to ensure that the cleanroom remains within operational parameters. Moreover, IoT enables predictive analytics, where data trends can predict when maintenance is needed before a system fails or contaminates the cleanroom. This proactive approach can significantly reduce downtime and maintenance costs. Regulatory Compliance and Global Standards As regulatory standards become more stringent, cleanroom designs will need to adapt to comply with global regulations. This is particularly relevant in the pharmaceutical and biotechnology industries, where regulatory oversight is rigorous. Cleanrooms in the future will need to be designed not only to meet current standards but also to be adaptable to changing regulations. Personalized Cleanrooms The concept of modular and personalized cleanrooms is emerging, where facilities are designed to be easily modified to meet the specific needs of different products or processes. Modular cleanrooms offer the flexibility to change layouts and scalability to increase or decrease in size based on production demands without significant disruptions to existing operations. Conclusion The future of cleanroom design and operation is marked by rapid advancements in technology and a shift towards more sustainable and efficient practices. As industries continue to develop and the demand for cleaner manufacturing environments grows, the evolution of cleanrooms will play a critical role in ensuring the quality, safety, and efficacy of products. Embracing these future trends will be essential for companies aiming to maintain competitiveness and compliance in an increasingly regulated and environmentally conscious world. Read more: All About Cleanrooms - The ultimate Guide
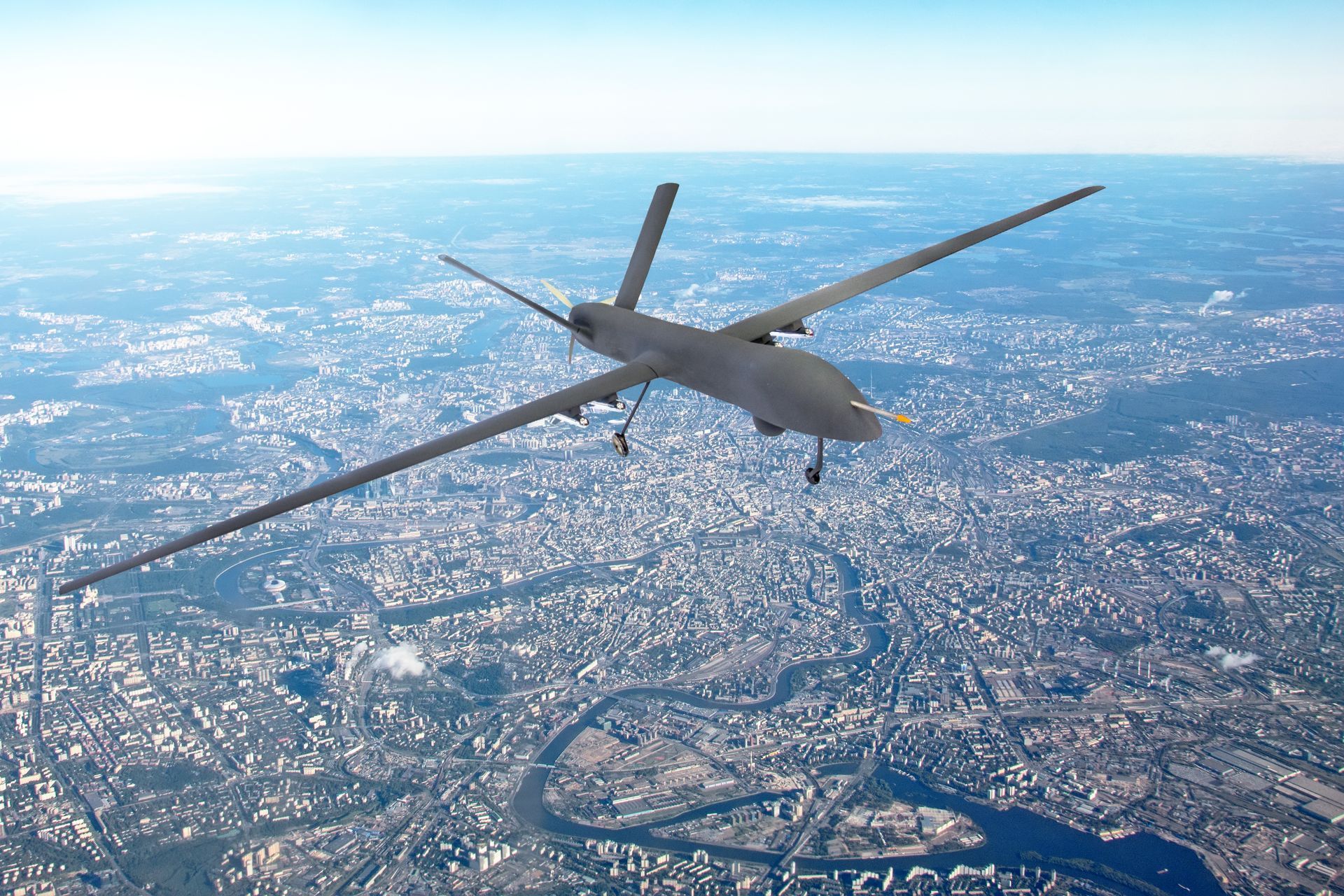
Introduction Cleanrooms play a crucial role in the aerospace industry, where precision, reliability, and compliance with stringent standards are paramount. From satellite assembly to the production of aircraft components and space exploration vehicles, maintaining a contaminant-free environment is vital to ensure the performance and safety of aerospace products. This article delves deeply into the role of cleanrooms in aerospace manufacturing, examining the specifications, technologies, and processes involved, as well as the challenges and advancements shaping this critical aspect of aerospace engineering. Introduction to Cleanrooms in Aerospace Manufacturing Cleanrooms are controlled environments with low levels of pollutants such as dust, airborne microbes, and aerosol particles. In aerospace manufacturing, these facilities are designed to control particulate contamination and ensure that the environment does not adversely affect the products being manufactured. The importance of cleanrooms in this sector cannot be overstated, given the catastrophic consequences that contamination could cause in aerospace applications. Specifications and Standards The aerospace industry adheres to stringent cleanroom standards, primarily governed by ISO 14644 and IEST standards for cleanrooms. The ISO 14644 series specifies cleanroom air cleanliness in terms of the number of particles per cubic meter at specified particle size. The required class of cleanroom varies depending on the particular aerospace application. For instance, manufacturing of spacecraft components typically requires ISO Class 5 or better, which allows no more than 3,520 particles (0.5 microns or larger) per cubic meter. In addition to ISO standards, aerospace manufacturers must also comply with specific industry standards such as those from NASA and the Department of Defense, which may have unique requirements for particular projects or components. Key Applications of Cleanrooms in Aerospace Manufacturing 1. Satellite Assembly: The assembly and testing of satellites require highly controlled environments to prevent the contamination of sensitive onboard electronics and optical components. Even microscopic particles can cause failure of sensors and circuits, which is unacceptable in space missions. 2. Aircraft Component Manufacturing: High-precision components such as turbine blades and avionics are manufactured in cleanrooms. Contamination in these components can lead to inefficiencies, increased fuel consumption, or catastrophic failures. 3. Space Exploration Vehicles: Cleanrooms are essential for the assembly of space exploration vehicles, including rovers and spacecraft. These vehicles operate in extreme conditions where any failure could jeopardize the entire mission and lead to significant financial losses. Technologies and Equipment The effectiveness of cleanrooms in aerospace manufacturing hinges on several key technologies and pieces of equipment: HEPA and ULPA Filters: These filtration systems are capable of trapping 99.97% to 99.9995% of particles, respectively, providing the necessary air purity for sensitive manufacturing processes. Air Showers and Pass-Through Chambers: Used to minimize contamination when personnel or materials enter the cleanroom. Temperature and Humidity Control Systems: Precise control over temperature and humidity is crucial to prevent static build-up and condensation, which can damage sensitive aerospace components. Laminar Air Flow Systems: These systems direct filtered air in a constant stream, reducing the chance of turbulent air that can stir up particles. Challenges in Aerospace Cleanroom Management 1. Maintaining Stringent Contamination Control: Continuous monitoring and maintenance are required to ensure that cleanrooms remain within the required specifications for particle counts, air purity, and environmental conditions. 2. High Operational Costs: Operating a cleanroom is expensive due to the energy costs of air handling systems and the need for specialized maintenance of filtration and HVAC systems. 3. Technological Advancements: Keeping up with advances in aerospace technology often requires upgrades to cleanroom facilities to handle new materials or components that have higher sensitivity to contaminants. Future Trends and Innovations The future of cleanrooms in aerospace manufacturing is likely to see several innovations: Automation and Robotics: To reduce human error and further minimize contamination, more processes within cleanrooms are expected to be automated or handled by robots. Advanced Materials: The development of new materials that are less prone to shedding particles or attracting contaminants could reduce the need for stringent cleanroom conditions. Real-Time Monitoring Technologies: Enhanced sensors and IoT technologies are expected to provide real-time data on cleanroom conditions, allowing for immediate adjustments and predictive maintenance. Conclusion Cleanrooms are indispensable in aerospace manufacturing, providing the necessary controlled environment to manufacture highly reliable and high-performance aerospace components. As the aerospace industry continues to push the boundaries of technology and exploration, the role of cleanrooms will only grow in importance, driven by advancements in cleanroom technologies and practices. Adhering to strict cleanroom standards and continually evolving with technological advancements ensures that aerospace products are manufactured with the highest reliability, supporting the overall safety and success of aerospace missions. Read more: All About Cleanrooms - The ultimate Guide
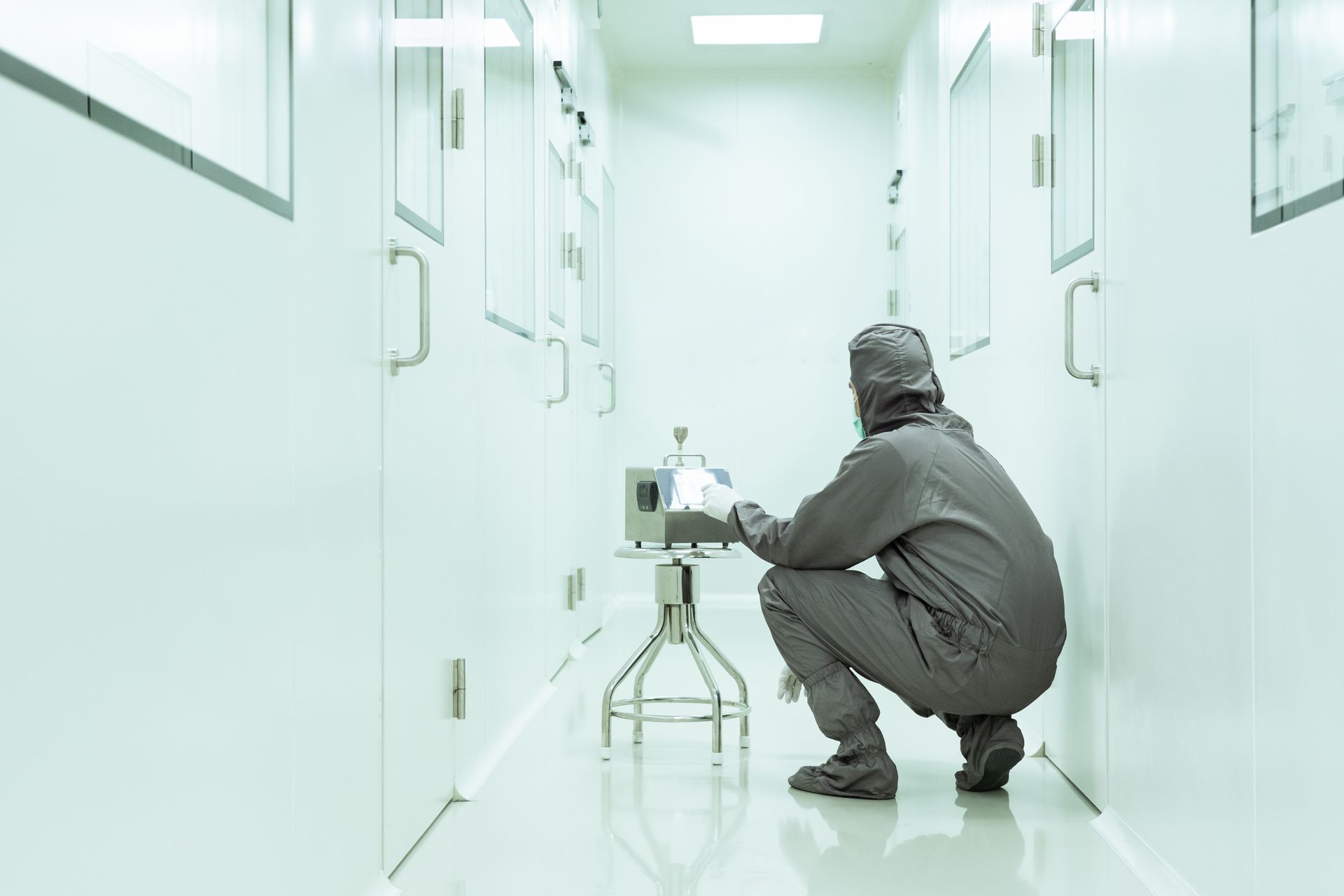
Introduction Cleanroom testing and validation are critical procedures to ensure that these specialized environments meet specific standards and regulations necessary for maintaining the integrity of the manufacturing process and product quality. Particularly in industries like pharmaceuticals, biotechnology, semiconductor manufacturing, and aerospace, where even the smallest contaminants can compromise the production, these procedures are not merely routine checks but integral to the operational excellence of the facility. Understanding Cleanroom Testing and Validation Cleanroom testing and validation involve a series of assessments that verify the cleanroom's performance meets the predefined standards and requirements. These standards are often governed by international norms such as ISO 14644 or, for pharmaceutical environments, could also adhere to GMP (Good Manufacturing Practice) standards. The primary goal of these procedures is to document and ensure that all aspects of the cleanroom environment—from air quality to equipment and surfaces—do not introduce contamination that could affect the manufacturing process or final product quality. Key Procedures in Cleanroom Validation 1. Installation Qualification (IQ): Installation Qualification is the first step in the validation process. IQ checks ensure that the equipment, components, and cleanroom setup comply with the manufacturer’s specifications and that everything has been installed correctly. This involves reviewing design specifications, verifying installation manuals, and ensuring that all components of the cleanroom are appropriately installed and configured. 2. Operational Qualification (OQ): Operational Qualification follows IQ and tests the cleanroom's performance under operational conditions. OQ involves testing equipment and systems to ensure they function according to their operational specifications within the cleanroom setting. This includes testing HVAC systems, filters, lighting, and any other critical systems for operational reliability. 3. Performance Qualification (PQ): Performance Qualification is the final stage of the validation process. PQ tests the cleanroom's performance over time to ensure it consistently meets the required operating standards under actual production conditions. This involves continuous monitoring of parameters such as particle counts, temperature, humidity, and pressure differentials over a specified period. Detailed Cleanroom Testing Methods Particulate Testing: This test measures the number of particles in the cleanroom air to verify that it meets the specific classification for which it is designed. For instance, an ISO 5 cleanroom allows no more than 3,520 particles (0.5 microns or larger) per cubic meter of air. Particulate testing uses particle counters to conduct this evaluation. Airflow Testing: Airflow tests measure the velocity and uniformity of the air supply within the cleanroom. Proper airflow is crucial to maintain cleanliness standards, as it ensures particles are swept away from critical areas and efficiently filtered out of the environment. Filter Integrity Testing: HEPA and ULPA filters are pivotal in maintaining cleanroom standards. Filter integrity tests, such as the DOP (Dispersed Oil Particulate) test, check for leaks or flaws in the filter media and sealing. This ensures that no unfiltered air bypasses the filtration system. Recovery Rate Testing: This test determines how quickly a cleanroom recovers to its baseline cleanliness level after a contamination event. The recovery rate is crucial for environments where cleanroom integrity needs to be quickly restored following routine operations or accidental breaches. Pressure Differential Testing: Maintaining specific pressure differentials between adjacent areas prevents contaminants from entering the cleanroom. This test ensures that the cleanroom maintains the correct pressure differential, essential for contamination control. Temperature and Humidity Control: Consistent temperature and humidity levels are essential for certain manufacturing processes and for minimizing static electricity, which can attract particles. Tests must confirm that the HVAC system maintains these parameters within the specified limits. Challenges in Cleanroom Testing and Validation Cleanroom validation is a complex, resource-intensive process that requires meticulous planning and execution. Challenges often arise from changes in production processes, upgrades to cleanroom facilities, or regulatory updates. Each of these factors can necessitate re-validation or adjustments in testing protocols. Additionally, human error and technical failures can introduce inconsistencies in test results. It is crucial to train personnel thoroughly and use well-calibrated, reliable testing equipment to mitigate these risks. Conclusion Cleanroom testing and validation are not just regulatory requirements but essential practices that protect the integrity of critical manufacturing processes and ensure product quality. As technology advances and regulatory environments evolve, cleanroom testing and validation procedures will continue to adapt, incorporating more sophisticated techniques and technologies to meet the stringent demands of modern manufacturing environments. For industries reliant on controlled environments, staying ahead in implementing advanced testing and validation methodologies is not just about compliance, but about gaining a competitive edge. Read more: All About Cleanrooms - The ultimate Guide
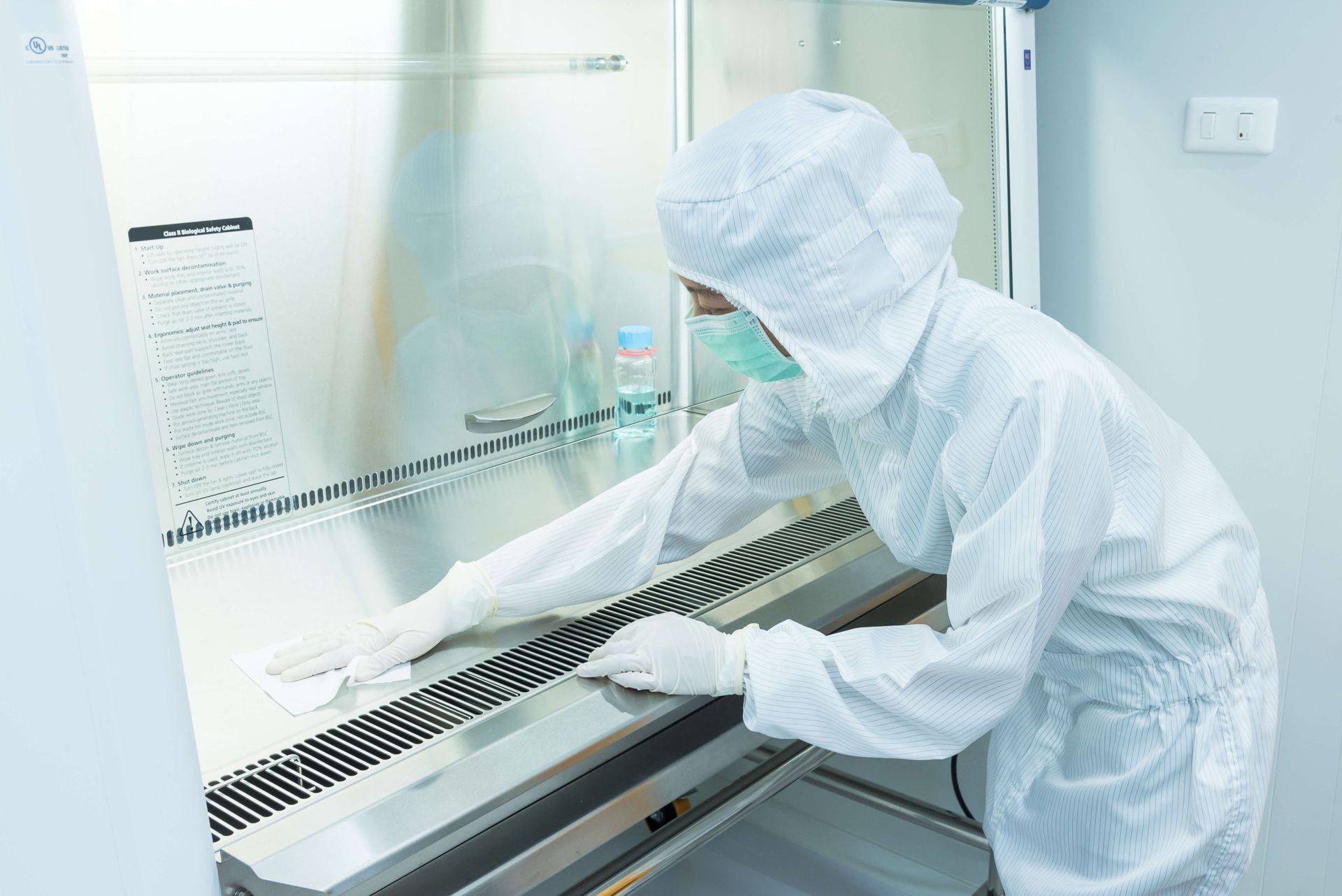
Introduction Cleanrooms are controlled environments designed to minimize contamination by particles, chemicals, and microorganisms. They play a critical role in industries such as pharmaceuticals, biotechnology, electronics, and aerospace. Microbial contamination poses a significant threat to these environments, potentially leading to product recalls, compromised research, and even risks to patient health. This article explores the impact of microbial contamination in cleanrooms, identifying sources, consequences, and best practices for prevention and control. Understanding Microbial Contamination Microbial contamination refers to the unintended presence of microorganisms, including bacteria, fungi, and viruses, in a cleanroom environment. Even trace amounts of microbial contamination can jeopardize the integrity of processes and products, particularly in sensitive fields like pharmaceuticals and semiconductor manufacturing. Sources of Microbial Contamination Personnel: Human operators are the most significant source of microbial contamination in cleanrooms. Skin flakes, hair, respiratory droplets, and clothing fibers all contribute to contamination. Materials and Equipment: Tools, packaging, and raw materials can introduce microbes if not properly sterilized or handled. Airborne Particles: Microorganisms can attach to dust particles or exist in aerosolized form, entering cleanrooms through compromised air filtration systems. Surface Contamination: Improper cleaning or infrequent disinfection of surfaces can lead to biofilm formation and persistent microbial presence. Water Systems: Microbial growth in water used for cleaning or in humidifiers can spread contamination throughout the facility. Risks and Consequences of Microbial Contamination Product Recalls and Financial Losses: I n industries like pharmaceuticals, microbial contamination can lead to product recalls, resulting in significant financial loss and reputational damage. Health Risks: I n medical device manufacturing and drug production, microbial contamination can compromise product sterility, potentially causing infections or adverse health effects for patients. Regulatory Non-Compliance: Failure to maintain microbial control can result in non-compliance with regulatory standards such as ISO 14644 and Good Manufacturing Practices (GMP), leading to legal penalties or facility shutdowns. Operational Downtime: Investigations and remediation of microbial contamination can halt production, delaying project timelines and reducing overall efficiency. Reduced Product Quality: In semiconductor and electronics industries, microbial contamination can lead to defects in products, affecting performance and longevity. Prevention and Control Strategies Personnel Training and Hygiene: Implement strict gowning procedures and hygiene protocols. Provide regular training on contamination control and proper cleanroom behavior. Cleanroom Design and Maintenance: Utilize high-efficiency particulate air (HEPA) and ultra-low penetration air (ULPA) filters. Maintain positive pressure to prevent external contamination. Design facilities with smooth, non-porous surfaces that are easy to clean. Air Quality Monitoring: Continuously monitor air quality for microbial and particulate contamination. Perform routine validation and maintenance of air filtration systems. Sterilization and Disinfection: Employ validated cleaning agents and sterilization techniques. Establish cleaning schedules for surfaces, tools, and equipment. Environmental Monitoring: Regularly sample and test air, surfaces, and personnel for microbial contamination. Use data from environmental monitoring to adjust and improve contamination control measures. Material and Equipment Control: Implement strict protocols for sterilizing incoming materials and equipment. Use sterilization techniques such as autoclaving and gamma irradiation where applicable. Conclusion Microbial contamination in cleanrooms presents significant risks across various industries, affecting product quality, patient safety, and regulatory compliance. By understanding contamination sources and implementing robust prevention and control measures, cleanroom operators can safeguard their processes and ensure the integrity of their products. Ongoing vigilance, regular training, and adherence to international standards are essential in minimizing the impact of microbial contamination and maintaining cleanroom excellence. Read more: All About Cleanrooms - The ultimate Guide
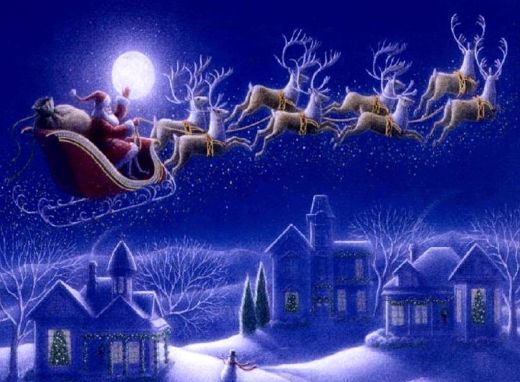
As we celebrate the joy of the season, we reflect on the trust, collaboration, and friendships that have made this year truly special. To our valued customers, trusted partners, and dear friends: May your Christmas be wrapped in warmth, joy, and love, surrounded by those who matter most. As the New Year unfolds, we wish you abundant happiness, good health, and continued success in all your endeavors. Thank you for being an integral part of our journey. We look forward to creating new milestones together in the coming year. Merry Christmas and a Radiant New Year! With gratitude, 14644 Cleanroom - Kjeld Lund
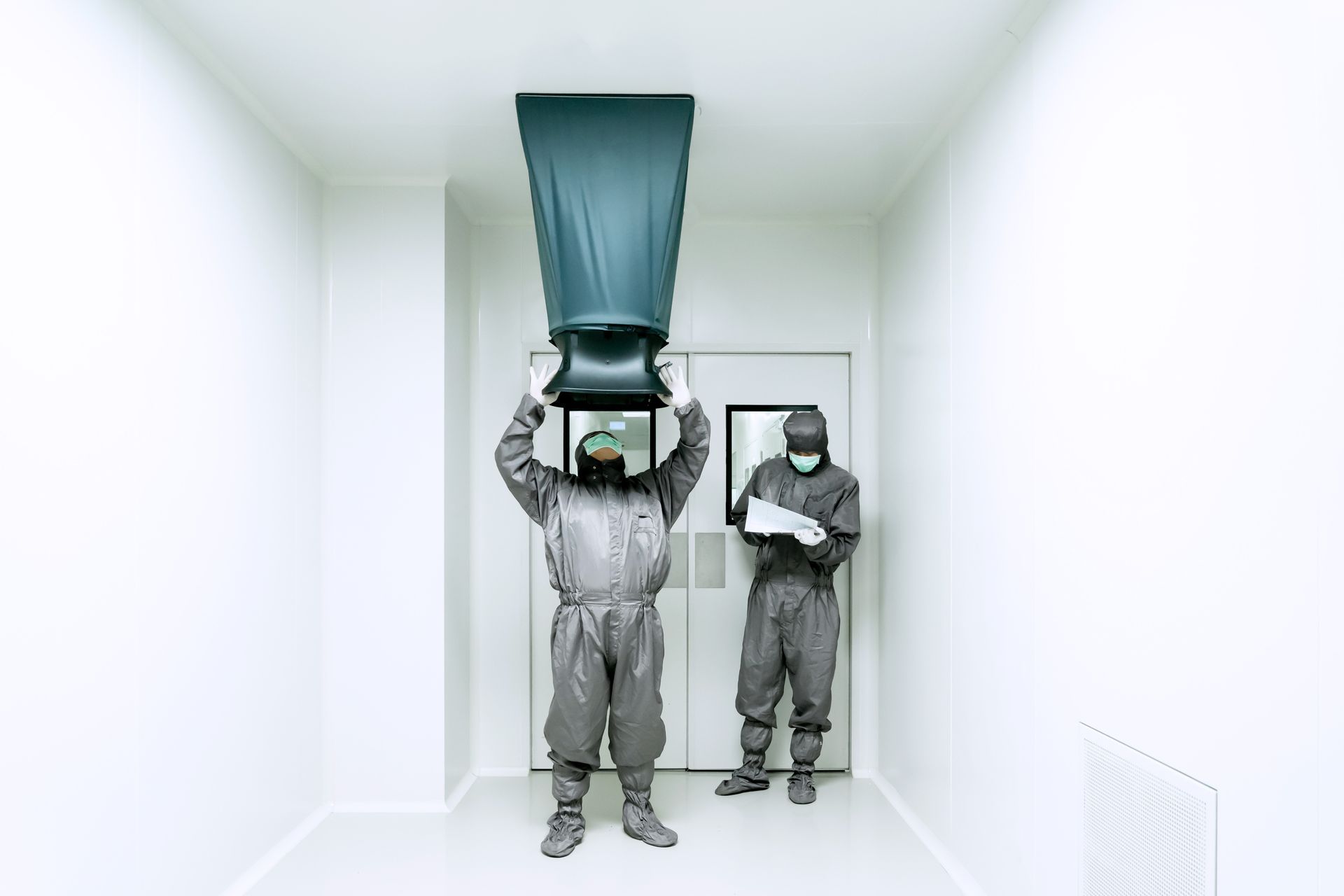
Introduction Cleanrooms are critical environments in industries ranging from pharmaceuticals to semiconductor manufacturing. Ensuring their efficiency, cleanliness, and compliance with stringent regulatory standards is paramount. Central to the operation of cleanrooms is their Heating, Ventilation, and Air Conditioning (HVAC) systems. Innovations in cleanroom HVAC systems are transforming these spaces by enhancing energy efficiency, improving contamination control, and reducing operational costs. Below, we explore the latest advancements driving this evolution. 1. Advanced Filtration Technologies Filtration is the cornerstone of cleanroom operation, as it ensures particulate control to maintain air cleanliness standards. Modern cleanroom HVAC systems employ advanced High-Efficiency Particulate Air (HEPA) and Ultra-Low Penetration Air (ULPA) filters. Innovations in filtration include: Nanofiber Filters: These filters use nanotechnology to achieve higher filtration efficiencies with reduced air resistance, leading to lower energy consumption. S elf-Cleaning Filters: Equipped with automated mechanisms, these filters maintain performance over longer periods by removing accumulated particulates, reducing maintenance needs. Electrostatic Precipitators: Leveraging electrical charges to capture contaminants, these systems enhance filter performance and reduce the frequency of replacements. 2. Energy-Efficient HVAC Designs Energy consumption is a major cost driver for cleanroom operations. New HVAC system designs are minimizing energy use without compromising performance through the following innovations: Variable Air Volume (VAV) Systems: Unlike traditional Constant Air Volume (CAV) systems, VAV adjusts airflow based on the cleanroom’s needs, reducing energy waste. Energy Recovery Ventilators (ERVs): These devices recover heat or cooling from exhaust air and transfer it to incoming air, significantly reducing the energy required to condition the air. High-Performance Fans and Motors: Modern HVAC systems incorporate electronically commutated motors (ECMs) and high-efficiency fans to optimize airflow while consuming less power. 3. Digital Monitoring and Control Systems The integration of digital technologies has revolutionized the way cleanroom HVAC systems are managed. Smart systems improve efficiency and ensure compliance by: IoT-Enabled Sensors: These sensors continuously monitor air quality, temperature, humidity, and pressure differentials, providing real-time data for precise control . Building Management Systems (BMS): Centralized platforms enable automated adjustments to maintain optimal environmental conditions while reducing energy consumption. Predictive Maintenance Algorithms: Using machine learning, HVAC systems can predict and address potential issues before they result in downtime or contamination events. 4. Modular and Flexible Cleanroom Designs The demand for adaptable cleanroom environments has led to the development of modular HVAC systems. Key innovations include: Scalable Air Handling Units (AHUs): These units can be configured or expanded to accommodate changes in cleanroom size or operational requirements. Plug-and-Play Duct Systems: Modular ductwork allows for easier installation and reconfiguration, reducing downtime and costs during upgrades or renovations. Zoning Capabilities: Advanced systems allow cleanrooms to be divided into zones with independent HVAC controls, enabling tailored environmental settings for different processes. 5. Sustainable and Green Solutions As industries focus on sustainability, cleanroom HVAC systems are incorporating environmentally friendly practices and technologies: Low Global Warming Potential (GWP) Refrigerants: These refrigerants reduce the environmental impact of HVAC operations while maintaining efficiency. Solar-Powered Systems: Integration with solar panels provides a renewable energy source for HVAC operations, significantly cutting carbon footprints. Lifecycle Assessments: New software tools help design HVAC systems with minimal environmental impact by evaluating the entire lifecycle of the equipment. 6. Improved Airflow Management Efficient airflow is critical for contamination control and energy savings. Innovative airflow management solutions include: Laminar Flow Optimization: Computational Fluid Dynamics (CFD) modeling is used to design systems that deliver uniform airflow, minimizing turbulence and contamination risks. Air Curtains: Strategically placed air curtains help maintain pressure differentials and prevent contamination without overburdening the HVAC system. Active Flow Control Systems: These systems adjust airflow in real-time to meet varying operational demands, enhancing both performance and efficiency. 7. Integration of Advanced Materials Innovative materials are enhancing the performance and durability of HVAC components: Antimicrobial Coatings: Applied to ducts and filters, these coatings inhibit microbial growth, ensuring cleaner air and reducing contamination risks. Lightweight Composite Materials: Used in ductwork and structural components, these materials reduce the overall weight of HVAC systems, lowering energy consumption. Phase-Change Materials (PCMs): Integrated into HVAC systems, PCMs store and release thermal energy, helping stabilize cleanroom temperatures with less active heating or cooling. 8. Compliance with Evolving Standards Regulatory requirements for cleanrooms are becoming increasingly stringent. Innovations in HVAC systems are enabling industries to meet these standards more effectively: Dynamic Validation Tools: Automated systems streamline the validation process by continuously assessing and documenting compliance with ISO and GMP standards. Real-Time Reporting Dashboards: Comprehensive platforms provide instant access to compliance metrics, simplifying audits and regulatory submissions. Conclusion The latest innovations in cleanroom HVAC systems are setting new benchmarks in performance, energy efficiency, and adaptability. By embracing these advancements, industries can achieve cleaner environments, lower operational costs, and a smaller environmental footprint. As technology continues to evolve, the future of cleanroom HVAC systems promises even greater efficiency and sustainability, enabling critical industries to thrive in an increasingly demanding world. Read more: All About Cleanrooms - The ultimate Guide
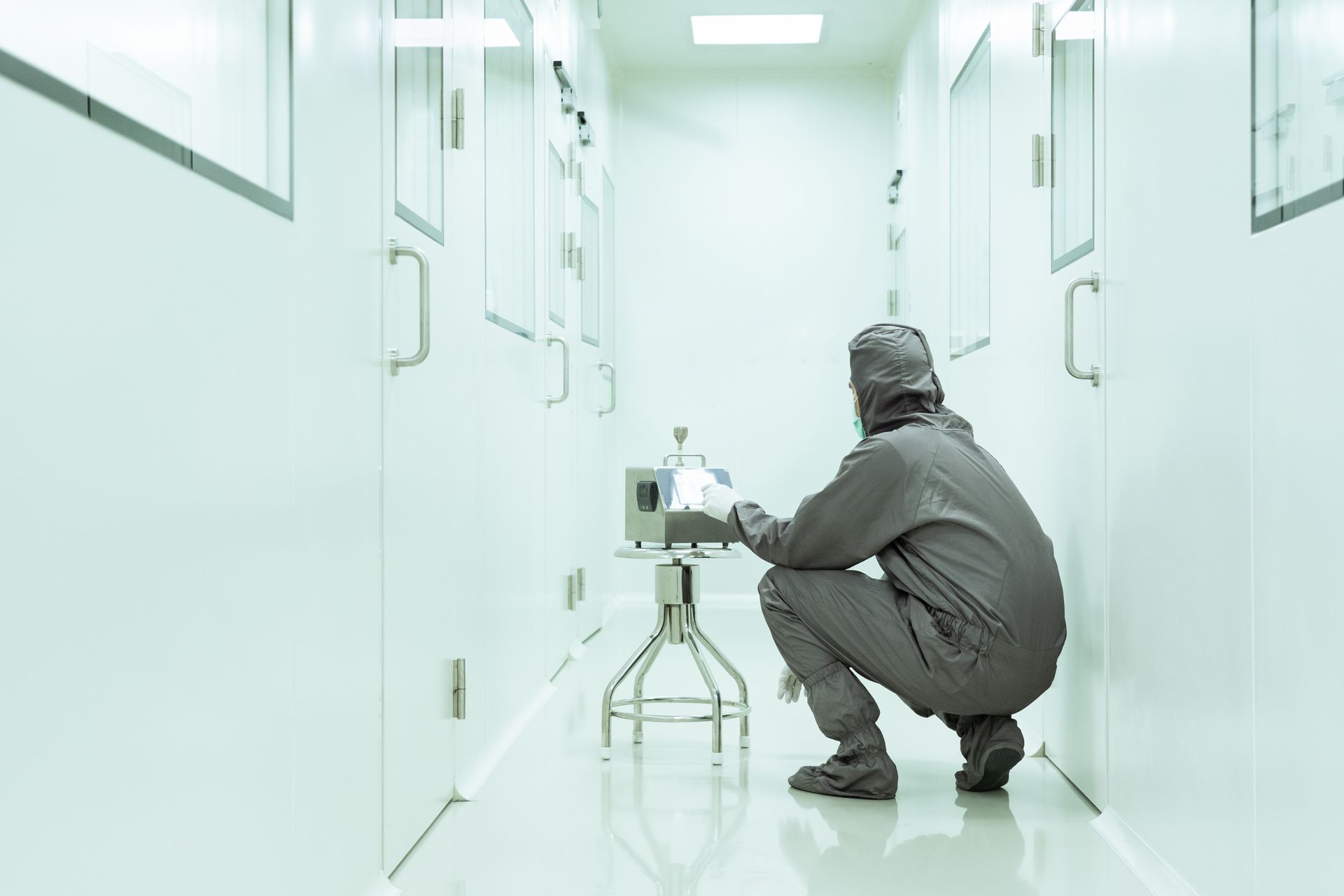
Introduction ISO 21501-4 is a part of the ISO 21501 series, which outlines standards for instruments used in the measurement of particle size distribution. Specifically, ISO 21501-4 is tailored to the calibration and performance evaluation of light-scattering airborne particle counters (LSAPCs). These devices are critical in monitoring air cleanliness in controlled environments, such as cleanrooms, pharmaceutical manufacturing facilities, and semiconductor production. This article provides a detailed exploration of ISO 21501-4, including its purpose, scope, technical specifications, and implications for industries requiring strict contamination control. Purpose and Scope of ISO 21501-4 ISO 21501-4 establishes calibration standards for airborne particle counters that use light scattering to detect and measure particles in the air. The standard ensures that these instruments produce reliable, repeatable, and accurate data essential for verifying compliance with cleanliness standards like ISO 14644, which governs cleanroom classifications. The standard covers the following areas: Calibration Requirements: Provides guidance for the calibration process to ensure instruments produce traceable and reproducible results. Performance Criteria: Defines acceptable levels of accuracy, resolution, and linearity for particle counters. Traceability: Ensures measurement results are linked to international standards through traceable calibration processes. Measurement Uncertainty: Establishes methodologies to quantify and minimize uncertainties in measurements. Key Technical Aspects of ISO 21501-4 ISO 21501-4 contains detailed technical requirements for airborne particle counters. Below are the primary aspects: 1. Principle of Light Scattering The standard applies to instruments that measure particles using the principle of light scattering. In these devices, a laser beam illuminates airborne particles as they pass through a measurement chamber. The scattered light is detected, and its intensity is used to estimate the size of the particle. 2. Calibration Procedure ISO 21501-4 specifies how instruments should be calibrated using monodisperse polystyrene latex (PSL) spheres of known sizes. Key calibration steps include: Particle Size Calibration : Ensures the counter accurately measures particle sizes within the required range. Counting Efficiency : Verifies the instrument’s ability to count particles at various sizes, typically requiring a counting efficiency of 50% for the smallest measurable particles and near 100% for larger ones. False Count Rate : Ensures that the instrument does not report spurious particles when no particles are present in the air stream. Flow Rate Calibration : Confirms the consistency of the airflow through the device, as accurate particle measurements depend on stable flow. 3. Resolution and Linearity Resolution: The standard defines how well an instrument can differentiate between particles of similar sizes. This is critical in applications like cleanroom monitoring, where particles near size thresholds are significant. Linearity: Particle counters must maintain consistent performance across their entire size measurement range, from the smallest detectable particles to the largest. 4. Measurement Uncertainty and Traceability ISO 21501-4 emphasizes minimizing measurement uncertainty by adhering to strict calibration protocols. The use of PSL spheres traceable to recognized standards ensures that the data generated by particle counters is consistent and comparable across different instruments and settings. 5. Detection Range The standard defines a typical detection range for LSAPCs, often between 0.1 μm and 10 μm. This range aligns with the particle sizes of interest in cleanroom standards, where larger particles may indicate contamination risks. Applications of ISO 21501-4 Industries requiring highly controlled environments rely on particle counters adhering to ISO 21501-4 for maintaining compliance with cleanliness standards. Key applications include: 1. Cleanroom Monitoring Cleanrooms are classified based on the concentration of airborne particles of specific sizes. ISO 21501-4-compliant particle counters are essential for: Classifying cleanrooms per ISO 14644-1. Verifying that contamination control measures are effective. Ensuring cleanroom integrity during operations. 2. Pharmaceutical Manufacturing In pharmaceutical production, particle monitoring ensures adherence to Good Manufacturing Practices (GMP) and regulatory requirements from agencies like the FDA. Particle counters verify air cleanliness in critical areas such as sterile filling zones. 3. Semiconductor Manufacturing Semiconductor facilities require ultra-clean environments to prevent defects caused by particle contamination. ISO 21501-4-compliant counters are used to maintain air purity levels within stringent tolerances. 4. Hospital and Laboratory Environments Healthcare facilities and laboratories use particle counters for infection control, ensuring that cleanrooms and laminar flow cabinets meet required cleanliness standards. Benefits of ISO 21501-4 Compliance Adhering to ISO 21501-4 offers numerous benefits: Enhanced Accuracy: Precise calibration ensures accurate particle size and count measurements. Global Consistency: Instruments calibrated to ISO 21501-4 provide results consistent with international standards, facilitating cross-border compliance. Regulatory Compliance: Compliance with ISO 21501-4 supports adherence to regulatory requirements in critical industries. Improved Quality Control: Reliable particle counting enhances product quality and reduces contamination risks. Challenges and Considerations While ISO 21501-4 offers robust guidelines, implementation can be challenging: Calibration Complexity: The calibration process requires specialized equipment and expertise, increasing operational complexity. Cost: Compliant particle counters and calibration services can be expensive, particularly for small-scale operations. Regular Maintenance: Instruments must undergo regular recalibration to maintain compliance, adding to operational costs. Future Trends and ISO 21501-4 The importance of ISO 21501-4 is likely to grow as industries demand higher levels of contamination control. Emerging trends include: Automation in Particle Monitoring: Integration with smart systems for real-time monitoring and automated reporting. Expanded Detection Ranges: Development of particle counters capable of measuring smaller particles, down to the sub-0.1 μm range, for advanced applications. Sustainability: Design of energy-efficient instruments and eco-friendly calibration processes. Conclusion ISO 21501-4 is a cornerstone standard for light-scattering airborne particle counters, ensuring their accuracy, reliability, and traceability. Its implementation is critical in industries that demand rigorous contamination control, such as cleanroom operations, pharmaceuticals, and semiconductor manufacturing. By adhering to ISO 21501-4, organizations can achieve higher levels of quality assurance and regulatory compliance, laying the foundation for safe and efficient operations in controlled environments. Read more: All About Cleanrooms - The ultimate Guide
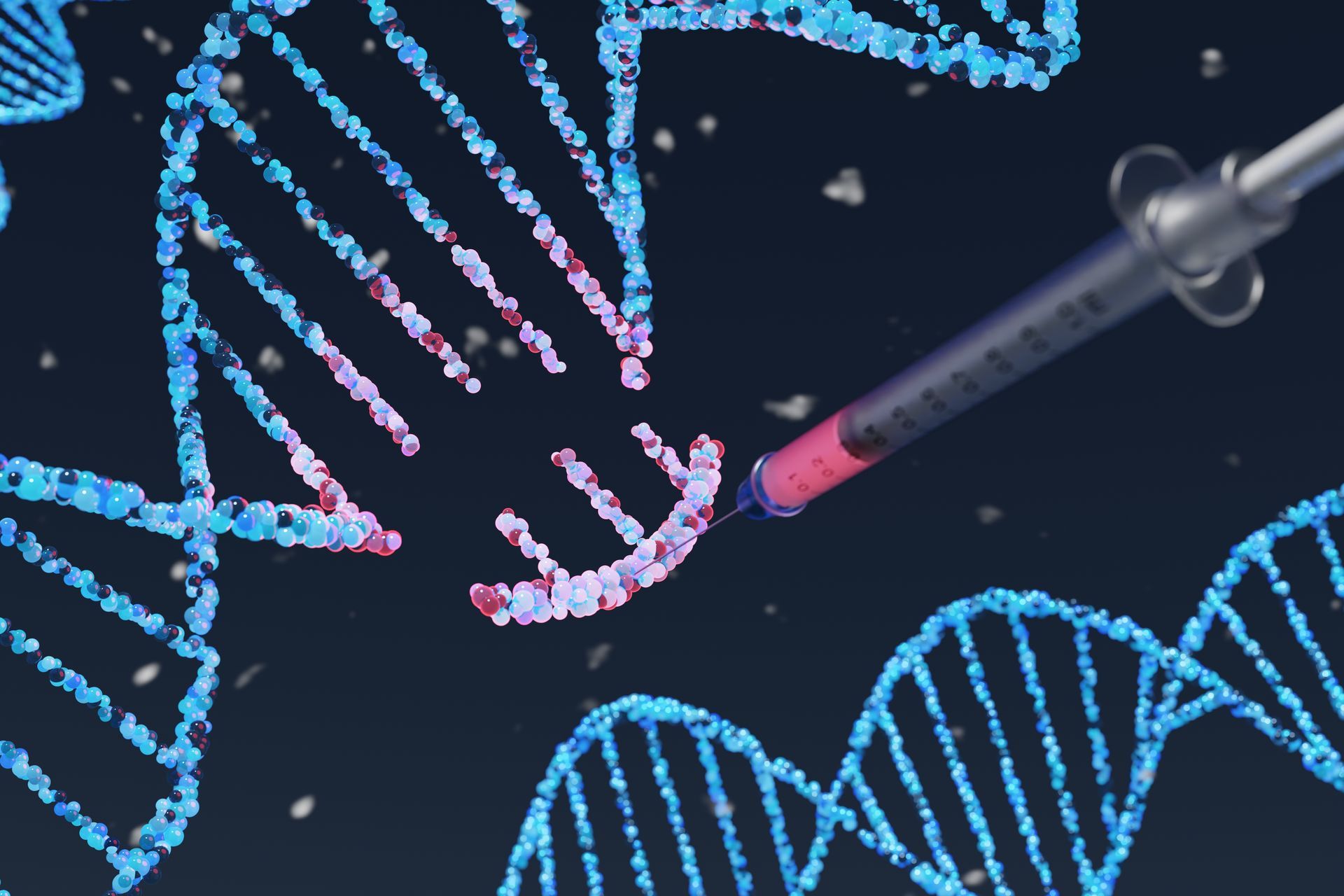
Introduction The fields of cellular and gene therapy are transforming medicine by offering potential cures for diseases that were once considered incurable. As interest in these cutting-edge therapies grows, so does the need to understand the complexities involved in their development. This detailed FAQ provides insights into the key aspects of developing cellular and gene therapy products, from scientific foundations to regulatory considerations. 1. What Are Cellular and Gene Therapy Products? Cellular Therapy: Cellular therapy involves the transfer of cells into a patient to replace or repair damaged tissue or treat diseases. Examples include: Hematopoietic stem cell transplantation (HSCT): Used to treat blood disorders. CAR-T cell therapy: Genetically modified T-cells designed to target specific cancers. Gene Therapy: Gene therapy aims to modify a patient’s genetic material to treat or cure diseases. This can involve: Gene addition: Introducing a new, functional gene to replace a missing or defective one. Gene editing: Using technologies like CRISPR-Cas9 to correct mutations within a gene. Gene silencing: Suppressing harmful gene expression using RNA interference (RNAi). 2. What Types of Diseases Can These Therapies Address? Cellular and gene therapies have shown promise in treating: Inherited genetic disorders: Such as sickle cell anemia, cystic fibrosis, and hemophilia. Cancers: CAR-T cell therapies are effective against certain types of leukemia and lymphoma. Neurodegenerative diseases: Experimental therapies target conditions like Parkinson’s and Huntington’s diseases. Autoimmune diseases and organ transplantation: Cellular therapies may modulate the immune response to reduce rejection. 3. What Are the Key Steps in Developing These Therapies? Step 1: Research and Preclinical Development Identify Target Disease and Mechanism: Understanding the underlying genetic or cellular cause of the disease. Develop the Product: This involves creating the cellular or genetic construct, testing its safety, and ensuring functionality. Preclinical Testing: Using in vitro and animal models to assess safety and efficacy. Step 2: Clinical Development Phase 1 Trials: Assess safety and dosage in a small group of patients. Phase 2 Trials: Evaluate efficacy and further assess safety in a larger group. Phase 3 Trials: Confirm efficacy in a large patient population and monitor side effects. Step 3: Regulatory Approval Submitting a Biologics License Application (BLA) or Investigational New Drug (IND) application to agencies like the FDA or EMA. Step 4: Post-Marketing Surveillance Monitoring for long-term safety and efficacy in the broader patient population. 4. What Are the Main Challenges in Development? Scientific Challenges Delivery Methods: Ensuring the therapy reaches the target cells or tissues effectively (e.g., viral vectors, lipid nanoparticles). Durability of Effect: Determining how long the therapy remains effective and whether re-treatment is needed. Off-Target Effects: Avoiding unintended changes to other genes or cells. Manufacturing Challenges Scalability: Producing therapies consistently at a commercial scale while maintaining quality. Cost: Gene and cellular therapies are resource-intensive to manufacture and administer. Supply Chain: Maintaining the viability of sensitive biological materials during transportation and storage. Regulatory and Ethical Challenges Complexity of Approval: Regulatory pathways can be more complex for these therapies due to their novelty. Ethical Considerations: Concerns about germline editing, equitable access, and long-term effects. 5. How Are Gene and Cellular Therapies Delivered? Gene Therapy Delivery Methods: Viral Vectors:Adeno-associated virus (AAV): Popular for its safety and efficiency in delivering genetic material. Lentivirus: Effective for integrating genes into dividing and non-dividing cells. Non-Viral Methods:Electroporation: Using electric pulses to introduce genes into cells. Lipid Nanoparticles: Deliver genetic material without viral components. Cellular Therapy Delivery : Intravenous (IV) Infusion: Common for CAR-T cells or stem cell products. Localized Injection: For specific tissues like joints or the brain. 6. What Regulatory Pathways Govern These Therapies? In the United States: Regulated by the FDA’s Center for Biologics Evaluation and Research (CBER). Key pathways include: IND Application: Required to start clinical trials. BLA Submission: For market approval. Expedited Programs: Including Breakthrough Therapy and Regenerative Medicine Advanced Therapy (RMAT) designations. In Europe: Oversight by the European Medicines Agency (EMA). Advanced Therapy Medicinal Products (ATMPs) classification is used for cellular and gene therapies. 7. How Are These Therapies Manufactured? Manufacturing involves stringent processes to ensure safety, efficacy, and consistency. Key Steps: Cell Collection: Cells are harvested from the patient (autologous) or a donor (allogeneic). Genetic Modification: For gene therapies or engineered cells, genetic material is inserted using viral or non-viral techniques. Expansion and Culturing: Cells are grown under controlled conditions to the required volume. Purification: Removal of impurities or residual materials. Formulation and Cryopreservation: Preparing the product for storage and transport. Quality Control: Manufacturing must comply with Good Manufacturing Practices (GMP), with rigorous testing for potency, purity, and sterility. 8. What Are the Costs Associated with Developing These Therapies? Developing cellular and gene therapies is resource-intensive: R&D Costs: High due to the complexity of preclinical studies and clinical trials. Manufacturing Costs: Specialized facilities and raw materials drive up production costs. Regulatory Costs: Meeting regulatory requirements involves significant investment. Therapies like CAR-T treatments can cost over $350,000 per patient due to these factors. Efforts to reduce costs include automating manufacturing processes and increasing scalability. 9. How Long Does It Take to Develop These Therapies? The development timeline for cellular and gene therapies ranges from 7-15 years , depending on: Complexity of the therapy. Regulatory requirements. Challenges in clinical trials and manufacturing. 10. What Is the Future of Cellular and Gene Therapy? Emerging Trends: CRISPR and Gene Editing: Making gene editing more precise and accessible. Off-the-Shelf Cellular Therapies: Allogeneic cell therapies that eliminate the need for patient-specific products. Combination Therapies: Integrating gene therapy with other treatments for enhanced efficacy. Expansion of Indications: Expanding from rare genetic diseases to more common conditions like diabetes, cardiovascular disease, and Alzheimer’s. Global Accessibility: Efforts are underway to make these therapies more affordable and accessible in low-resource settings. Conclusion Developing cellular and gene therapy products requires navigating complex scientific, manufacturing, and regulatory landscapes. Despite the challenges, these therapies hold the potential to revolutionize medicine, offering hope for patients with previously untreatable conditions. By understanding the FAQs covered here, stakeholders can better appreciate the intricacies of this promising field and its profound impact on healthcare. Read more: All About Cleanrooms - The ultimate Guide
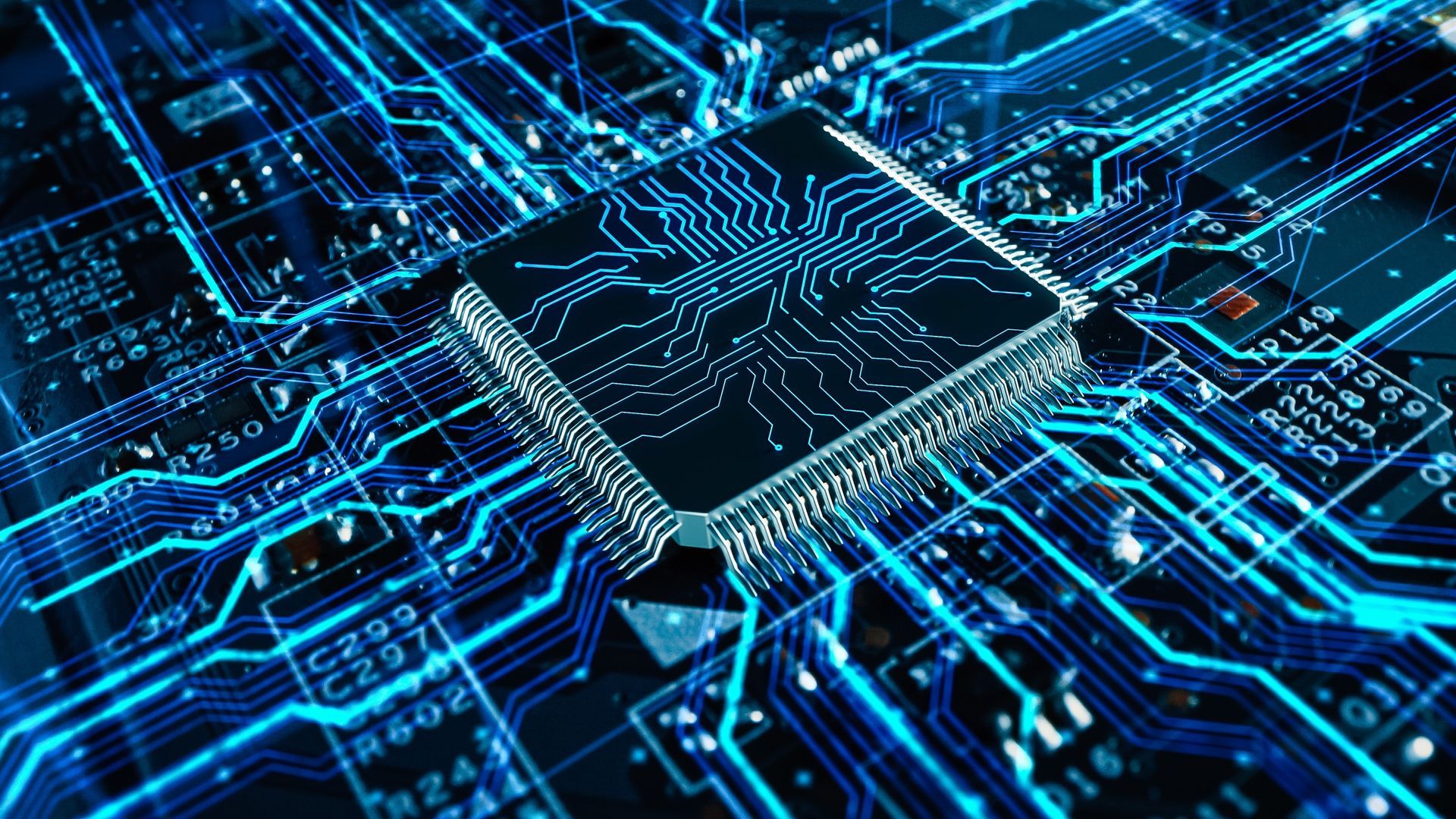
Introduction Semiconductor manufacturing is a cornerstone of modern technology, enabling the production of integrated circuits (ICs) that power everything from smartphones and computers to automobiles and medical devices. This highly intricate process involves multiple steps of precision engineering and fabrication. The production environment, especially the cleanroom, plays a critical role in ensuring product quality and yield. Cleanrooms are meticulously controlled environments designed to minimize contamination from particles, microbes, and chemical vapors, as even microscopic contaminants can ruin semiconductors. This article delves into the intricacies of semiconductor manufacturing, the stringent requirements of cleanrooms, and the interdependencies between the two. Semiconductor Manufacturing Process The manufacturing of semiconductors is a multi-step process that transforms silicon wafers into functional chips. Each stage requires advanced equipment, materials, and environmental controls to achieve the high levels of precision needed for modern semiconductors. 1. Silicon Wafer Preparation Raw Material Extraction: The process begins with high-purity silicon, derived from quartz or sand, which undergoes chemical purification. Crystal Growth: Using the Czochralski process , a single crystal ingot is grown by pulling a seed crystal from molten silicon. Wafer Slicing and Polishing: The ingot is sliced into thin wafers, polished to a mirror finish, and cleaned to remove impurities. 2. Photolithography This is a core step in patterning the microscopic circuits on the wafer. Coating with Photoresist: A light-sensitive material is applied to the wafer surface. Mask Alignment and Exposure: A photomask defines the desired pattern, which is transferred onto the photoresist through exposure to ultraviolet (UV) light. Development and Etching: The exposed photoresist is developed, leaving a precise pattern that allows for selective etching of the wafer. 3. Etching and Deposition Etching: The unwanted material is removed either through wet chemical etching or dry plasma etching . Deposition: Layers of materials like silicon dioxide or metal are deposited using techniques such as chemical vapor deposition (CVD) or atomic layer deposition (ALD). 4. Doping Doping introduces impurities into specific areas of the silicon wafer to modify its electrical properties. This is typically done using ion implantation , where ions are accelerated into the wafer under precise conditions. 5. Metallization This step involves depositing and patterning metal layers that form the electrical connections between transistors. 6. Testing and Packaging Before chips are packaged, they are subjected to rigorous testing to ensure functionality. The wafers are then diced into individual chips, packaged, and further tested. Cleanroom Requirements in Semiconductor Manufacturing Cleanrooms are essential for maintaining the quality and reliability of semiconductor products. Contamination during any stage of the manufacturing process can lead to defects, reducing yield and increasing costs. 1. Key Contamination Risks Particulate Matter: Dust, fibers, and other particles can interfere with photolithography or cause short circuits. Chemical Contamination: Vapors from outgassing materials can react with sensitive processes or materials. Microbial Contamination: Bacteria and other microorganisms can introduce particulates or biological residues. Electrostatic Discharge (ESD): Static electricity can damage the microscopic features on a chip. 2. Cleanroom Classifications Cleanrooms are classified based on the maximum allowable particle count per cubic meter of air. The most common standards are: ISO 14644-1: Defines classes from ISO Class 1 (cleanest) to ISO Class 9 (least clean). Federal Standard 209E (Retired but still used): Defines classes as Class 1, 10, 100, etc., representing particle counts per cubic foot of air. For semiconductor fabrication: Photolithography and deposition areas often require ISO Class 3 or Class 4. General manufacturing areas may use ISO Class 5 or higher. 3. Environmental Controls Temperature and Humidity: Temperature is maintained between 20-22°C (68-72°F) with variations under ±1°C. Humidity is controlled to prevent condensation or electrostatic issues, typically at 30-50%. Airflow and Filtration: High-efficiency particulate air (HEPA) filters or ultra-low penetration air (ULPA) filters ensure clean air. Laminar airflow minimizes turbulence and particle deposition. Pressure: Cleanrooms are kept at positive pressure relative to surrounding areas to prevent ingress of contaminants. 4. Personnel and Equipment Garments: Operators wear cleanroom suits (bunny suits) made of non-linting materials. Gloves, masks, goggles, and shoe covers prevent particle shedding. Behavior Protocols: Movement is minimized to reduce particle generation. Strict no-touch policies are enforced for sensitive surfaces. Equipment Cleanliness: Tools are cleaned regularly, and materials are stored in particle-free environments. 5. Monitoring and Maintenance Continuous monitoring ensures that cleanroom parameters stay within specification. Particle Counters: Measure air quality in real time. Environmental Sensors: Monitor temperature, humidity, and pressure. Preventative Maintenance: Regular servicing of filters, equipment, and systems prevents contamination risks. Advances in Cleanroom Technology As semiconductor processes evolve, cleanroom technology must adapt to meet stricter requirements. Nanotechnology Applications: Cleanrooms for <3 nm semiconductor processes demand sub-ISO Class 1 environments. AI and IoT Integration: Smart sensors and AI-driven systems provide predictive maintenance and real-time optimization. Sustainability Initiatives: Efforts to reduce energy and water use include efficient HVAC systems and closed-loop water recycling. Conclusion Semiconductor manufacturing relies heavily on advanced cleanroom environments to ensure the integrity of the fabrication process. As chips become smaller and more complex, the demands on cleanroom technology will continue to increase, driving innovations in contamination control, environmental sustainability, and real-time monitoring. Ensuring adherence to these stringent cleanroom requirements is critical for producing reliable, high-performance semiconductor devices. Read more: All About Cleanrooms - The ultimate Guide
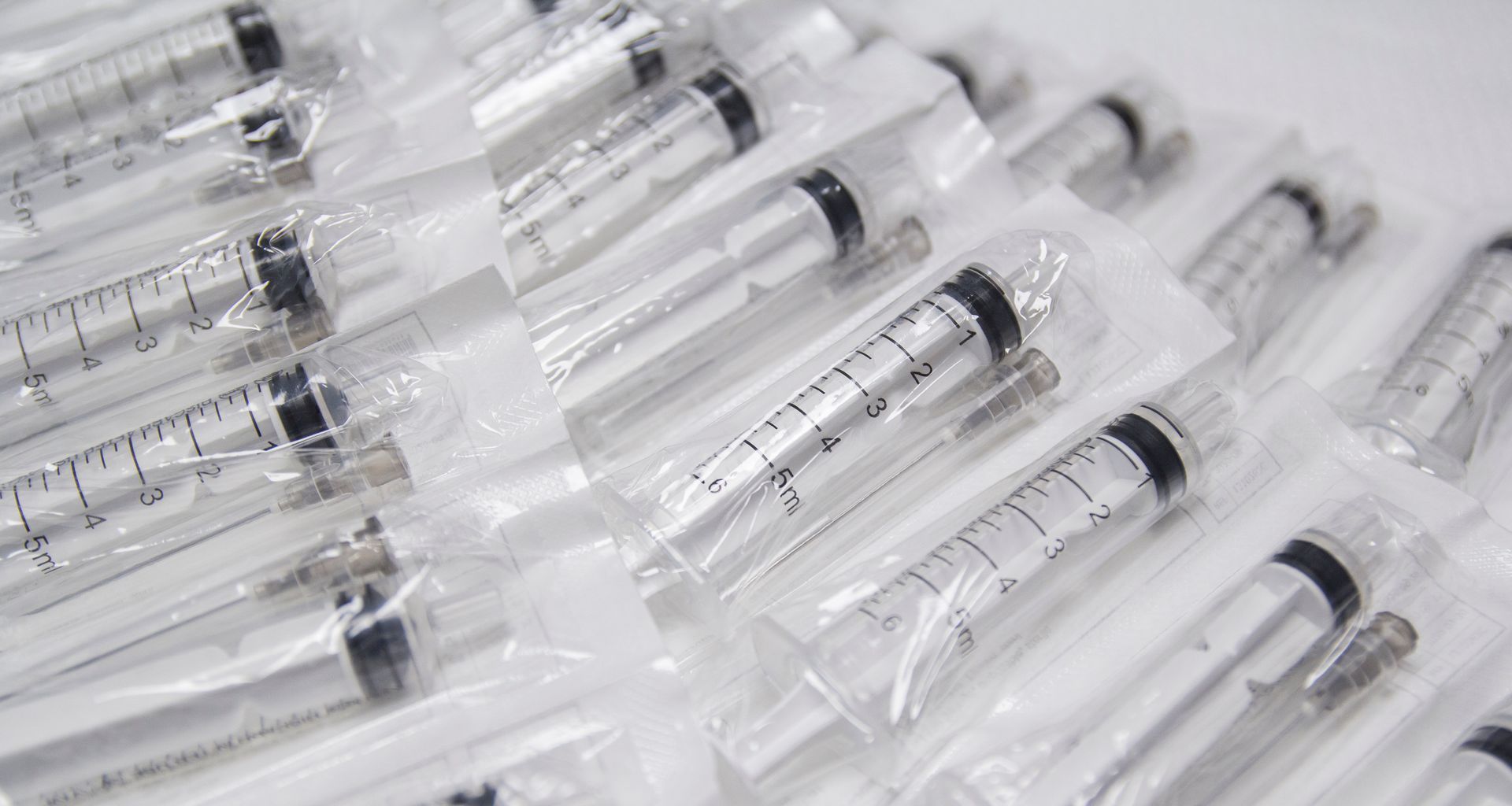
Introduction ISO 13485 is an internationally recognized standard for quality management systems (QMS) specifically designed for medical devices. Published by the International Organization for Standardization (ISO), it provides a framework to ensure the consistent design, development, production, installation, and servicing of medical devices. ISO 13485 is crucial for manufacturers, suppliers, and other organizations involved in the medical device supply chain, as it sets the requirements necessary to ensure the safety and effectiveness of medical devices. Here’s a comprehensive overview of ISO 13485, its structure, requirements, benefits, and key considerations. 1. Understanding ISO 13485 and Its Purpose ISO 13485 aligns with regulatory requirements for medical device production, focusing on risk management, quality assurance, and the specific requirements related to the life cycle of medical devices. Unlike ISO 9001, which is more general, ISO 13485 tailors its quality management framework for medical device safety and efficacy. The purpose of ISO 13485 is to provide organizations with a practical foundation for: Meeting regulatory requirements related to medical devices. Managing risks associated with medical devices. Improving the quality and safety of medical products. Consistently meeting customer expectations regarding the quality of medical devices. ISO 13485 certification can also be a regulatory requirement in various countries, including Canada, the European Union, and certain regions in Asia, as part of the requirements for marketing and distributing medical devices. 2. Scope and Structure of ISO 13485 ISO 13485 addresses the entire lifecycle of a medical device, covering areas like design, manufacturing, distribution, installation, and maintenance. While it closely aligns with the structure of ISO 9001, ISO 13485 is more prescriptive in its requirements, reflecting the higher degree of risk involved in medical device production. The main sections of ISO 13485 are as follows: Scope: Defines the applicability and intent of the standard. Normative References: Lists documents referenced in the standard. Terms and Definitions: Establishes specific terminology related to medical devices and quality management. Quality Management System (QMS): Details the requirements for establishing, documenting, and maintaining a QMS for medical devices. Management Responsibility: Outlines the commitment of management to establish and implement the QMS. Resource Management: Specifies requirements for allocating resources, training staff, and maintaining a clean and safe work environment. Product Realization: Describes the stages of product realization, including design, development, and manufacturing. Measurement, Analysis, and Improvement: Focuses on maintaining and improving the QMS through regular reviews, audits, and continuous improvement processes. Each section provides specific requirements for ensuring quality and safety, often requiring documentation, records, and verifications at various stages of the product lifecycle. 3. Key Requirements of ISO 13485 ISO 13485’s key requirements focus on critical areas in medical device manufacturing and the management of related processes. Here’s a breakdown of these requirements: a) Quality Management System (QMS) Requirements Establish and document the QMS with policies, procedures, and records relevant to medical devices. Define QMS scope based on the organization’s activities. Implement regular updates and improvements to the QMS based on performance data and risk assessment. b) Management Responsibility Top management must demonstrate a commitment to the QMS, setting a quality policy, establishing measurable objectives, and conducting regular management reviews. Ensure that responsibilities, authorities, and roles within the organization are well defined, documented, and communicated. c) Resource Management Ensure sufficient resources are allocated, including personnel, infrastructure, and equipment. Ensure that personnel are properly trained and qualified for tasks that impact product quality. Maintain a controlled work environment that complies with regulatory requirements. d) Product Realization Outline a systematic approach to product realization, including design and development, planning, purchasing, and production. Conduct risk analysis to identify potential product risks at each stage. Implement rigorous controls in procurement, verification, and validation activities to ensure suppliers meet quality standards. e) Design and Development Controls Document all stages of product design and development, including design input, output, review, verification, and validation. Maintain traceability of design changes and approvals throughout the development process. f) Production and Process Controls Establish detailed production processes and monitor them to ensure consistent product quality. Implement product traceability measures throughout manufacturing and, where necessary, post-market. Maintain equipment and environmental controls to prevent contamination and ensure product sterility. g) Measurement, Analysis, and Improvement Monitor and measure processes to assess QMS effectiveness, customer satisfaction, and product conformity. Implement corrective and preventive actions (CAPA) in response to nonconformities or potential improvements. Regularly conduct internal audits and management reviews to ensure ongoing compliance. 4. Benefits of ISO 13485 Certification Obtaining ISO 13485 certification offers numerous advantages for medical device manufacturers, suppliers, and other stakeholders: Regulatory Compliance: ISO 13485 aligns closely with many international regulatory requirements, such as the FDA’s 21 CFR Part 820 and the EU’s MDR. Certification can streamline the regulatory approval process. Enhanced Product Quality and Safety: By standardizing processes and implementing risk-based controls, ISO 13485 reduces the likelihood of defects or safety issues in medical devices. Market Access: Certification is often a prerequisite for accessing global markets, including the EU, Canada, and many countries in Asia and Latin America. Improved Efficiency: The standard promotes a structured approach to production and process management, often leading to cost reductions and operational efficiencies. Customer Trust: Certification assures clients and patients that a medical device manufacturer is committed to quality and safety. 5. ISO 13485 vs. ISO 9001: Key Differences ISO 13485 and ISO 9001 share a similar structure, but ISO 13485 is specifically tailored to medical devices, with additional emphasis on risk management, traceability, and regulatory compliance. Key differences include: Risk Management: ISO 13485 requires a risk-based approach at all stages, while ISO 9001 only suggests it in certain areas. Product Realization: ISO 13485 includes additional controls specific to the medical device industry, such as product traceability and sterilization requirements. Documentation: ISO 13485 mandates extensive documentation and validation for processes, making it more prescriptive than ISO 9001. 6. Implementing ISO 13485: Steps to Compliance For organizations looking to implement ISO 13485, the process can be broken down into these fundamental steps: Gap Analysis: Assess current practices against ISO 13485 requirements to identify areas needing improvement. QMS Development: Establish a comprehensive QMS, addressing documentation, policies, and procedures for all applicable areas. Training and Resource Allocation: Train personnel on the standard’s requirements and assign resources as needed. Process and Product Control: Document design, manufacturing, and process controls specific to medical device production. Conduct Internal Audits: Regular internal audits are essential to identify and address issues before formal certification audits. Certification Audit: Engage a certified auditing body to conduct the certification audit, followed by re-certification audits as required. 7. The Role of Risk Management in ISO 13485 ISO 13485 places a strong emphasis on risk management, recognizing that medical devices often impact patient health and safety. Organizations must identify and mitigate risks at each stage of the device lifecycle, including design, manufacturing, storage, and distribution. This includes establishing a risk management file, conducting regular risk assessments, and implementing controls to reduce risks to acceptable levels. 8. Revisions and Updates to ISO 13485 The current version, ISO 13485:2016 , introduced several important updates, including: Greater focus on risk-based decision-making. Enhanced controls over suppliers and outsourced processes. Expanded requirements for design and development procedures. Greater emphasis on regulatory documentation and reporting. These updates reflect the evolving regulatory landscape and the increasing complexity of medical device technology. Conclusion ISO 13485 is an essential standard for organizations involved in the medical device industry, providing a robust framework for quality and safety. Certification can enhance a company’s marketability, improve product quality, and ensure compliance with global regulations. By understanding and implementing ISO 13485, companies can achieve a systematic approach to quality management, ultimately supporting the safety and well-being of patients and healthcare providers worldwide. Medical Devices Below is a comprehensive list of the top 50 essential medical devices widely used across healthcare settings. These devices range from diagnostics to treatment, surgery, and patient care, making them crucial for effective medical practice: Diagnostic Devices Stethoscope – For listening to internal sounds. Blood Pressure Monitor – Measures blood pressure levels. Thermometer – Measures body temperature. Electrocardiogram (ECG/EKG) Machine – Records electrical activity of the heart. Pulse Oximeter – Monitors oxygen saturation in blood. Ultrasound Machine – Uses sound waves to visualize internal organs. X-ray Machine – Captures images of bones and tissues. MRI Scanner – Provides detailed images of soft tissues. CT Scanner – Offers cross-sectional imaging of the body. Glucose Meter – Monitors blood glucose levels. Surgical and Operating Room Equipment Surgical Scalpel – For precise incisions. Defibrillator – Delivers electric shock to the heart during cardiac arrest. Anesthesia Machine – Delivers anesthetics during surgery. Infusion Pump – Administers controlled amounts of fluids. Surgical Lights – Provides high-intensity lighting in operating rooms. Endoscope – Allows viewing of internal organs during minimally invasive procedures. Laparoscope – Specialized for laparoscopic (minimally invasive) surgeries. Electrosurgical Unit – Uses electric current for cutting or coagulating tissue. C-arm X-ray Machine – Used in orthopedic and trauma surgery for imaging. Surgical Microscope – For high-precision surgeries. Respiratory and Life-Support Equipment Ventilator – Assists or controls breathing. Nebulizer – Delivers medication directly to the lungs. Oxygen Concentrator – Provides supplemental oxygen to patients. CPAP Machine – Treats sleep apnea by providing continuous airway pressure. ECMO Machine – Provides cardiac and respiratory support for critically ill patients. Patient Monitoring Equipment Heart Rate Monitor – Continuously measures heart rate. EEG Machine – Monitors electrical activity in the brain. Fetal Monitor – Tracks fetal heartbeat and contractions. Holter Monitor – Portable device for continuous ECG monitoring. ICU Patient Monitor – Monitors vital signs in intensive care units. Rehabilitation and Mobility Devices Wheelchair – Provides mobility for those with physical disabilities. Prosthetic Limb – Replaces missing limbs. Orthopedic Brace – Supports injured or weakened limbs. Hearing Aid – Enhances hearing for those with hearing loss. Pacemaker – Helps regulate heartbeats for arrhythmia patients. Laboratory and Diagnostic Testing Equipment Microscope – For magnifying small structures in clinical labs. Centrifuge – Separates components in blood samples. PCR Machine – Amplifies DNA for genetic testing. Urine Analyzer – Analyzes components of urine samples. Hemoglobin Analyzer – Measures hemoglobin levels in blood. Home Healthcare and Wearable Devices Wearable Fitness Tracker – Monitors physical activity and vital signs. Blood Glucose Monitor – For at-home blood sugar monitoring. Digital Thermometer – Allows patients to take temperature at home. Home Blood Pressure Monitor – For regular blood pressure tracking at home. Smart Pill Dispenser – Ensures medication is taken on schedule. Sterilization and Cleaning Equipment Autoclave – Sterilizes medical equipment using high-pressure steam. UV Sterilizer – Uses UV light to disinfect surfaces and equipment. Ultrasonic Cleaner – Cleans equipment with ultrasonic waves. Disinfection Sprayer – Disinfects surfaces in patient care areas. Air Purifier – Maintains clean air, especially in sterile environments. These top 50 devices play a pivotal role in diagnostics, treatment, surgery, patient care, and rehabilitation, helping healthcare professionals deliver precise, efficient, and effective care. Read more: All About Cleanrooms - The ultimate Guide
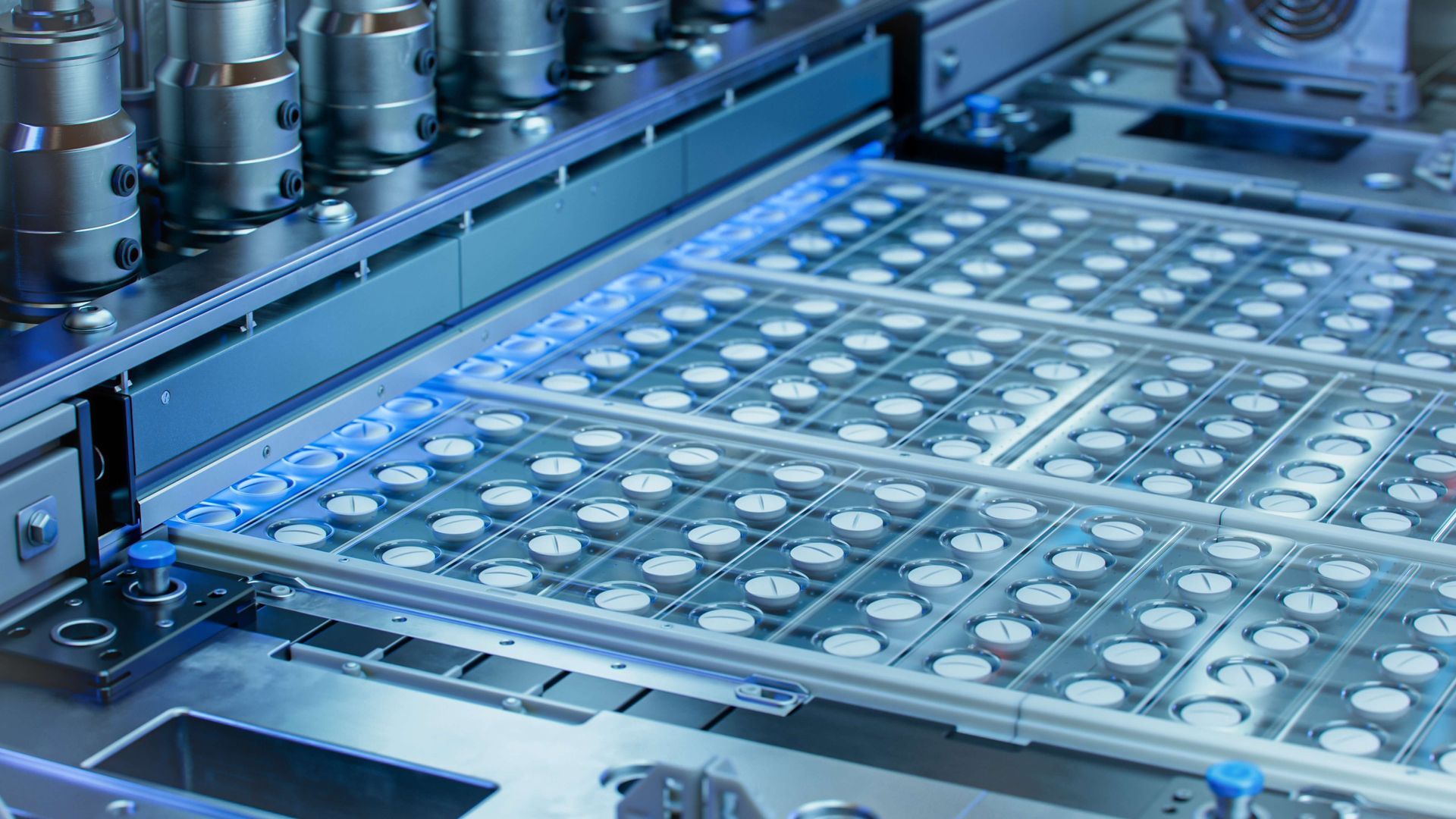
Introduction Cleanrooms are a crucial aspect of the pharmaceutical industry, where high standards of cleanliness, environmental control, and contamination prevention are paramount. These controlled environments enable the production of drugs, biologics, and other therapeutic products under conditions that minimize contamination from particles, microorganisms, and chemicals. Despite stringent regulations and advanced technologies, cleanroom operations in pharmaceuticals face a number of challenges, particularly as new products like cell and gene therapies demand higher standards of sterility and precision. This article delves into some of the primary challenges in maintaining cleanrooms within the pharmaceutical sector, examining both traditional difficulties and emerging complexities. 1. Stringent Regulatory Compliance Pharmaceutical cleanrooms must comply with a wide range of regulations, including those set by the Food and Drug Administration (FDA), European Medicines Agency (EMA), and international guidelines like ISO 14644, which defines cleanroom classifications based on particle counts. These standards require not only stringent environmental controls but also regular validation, testing, and reporting. Challenge: The evolving regulatory landscape can be difficult to keep up with, especially with the increasing scrutiny on sterile processing and aseptic manufacturing. New guidelines often require changes in equipment, testing protocols, or operational procedures, adding complexity to already rigid processes. Solution: Pharmaceutical companies need robust compliance teams and flexible systems that can adapt quickly to regulatory updates, including automated reporting and digital compliance monitoring tools. 2. Particle and Microbial Contamination Control Particulate and microbial contamination in cleanrooms can lead to product recalls, batch losses, and potentially harmful impacts on patient health. Cleanrooms are designed to control particles from various sources, including humans, materials, equipment, and ventilation systems. However, achieving and maintaining this level of control can be an ongoing challenge. Challenge: Even with stringent gowning procedures and air handling systems, particles can be introduced by personnel, equipment wear, and even the production materials themselves. Microbial contamination is particularly challenging as many microbes can survive in low-nutrient environments and persist in hard-to-clean areas. Solution: Enhanced monitoring with real-time particle and microbial detectors, improved cleaning protocols, and implementing advanced filtration systems, like HEPA and ULPA filters, can reduce the risk of contamination. Routine personnel training on contamination control procedures is also crucial. 3. Environmental Monitoring and Data Management Continuous environmental monitoring is required to maintain cleanroom standards and detect potential contamination issues before they impact product quality. Data collected on temperature, humidity, airflow, pressure differentials, and contamination levels must be managed meticulously. Challenge: Managing vast amounts of data from multiple sources can be difficult, especially if facilities lack centralized, automated systems. Manual data management increases the risk of errors, potentially leading to compliance violations. Solution: Automated environmental monitoring systems that integrate data collection, storage, and analysis in real-time are increasingly used in pharmaceutical cleanrooms. Cloud-based data storage can also improve accessibility and traceability while reducing the potential for human error. 4. Personnel-Related Contamination Risks Personnel are often the largest source of contamination in cleanrooms, despite rigorous gowning and hygiene protocols. Human skin, hair, respiratory droplets, and even movement can introduce particles and microbes into a sterile environment. Challenge: Managing contamination risks related to personnel requires a fine balance between rigorous protocols and practical usability. High turnover rates in the industry can make consistent training and enforcement challenging. Solution: Automated systems like robotics and remote-operated tools can minimize the need for human presence in critical areas. Virtual reality (VR) training for cleanroom protocols also shows promise in improving staff performance and awareness of contamination risks. 5. Energy and Cost Efficiency Cleanrooms are energy-intensive environments due to the need for high-efficiency ventilation systems, temperature and humidity controls, and rigorous cleanliness standards. Maintaining such environments requires significant energy input and cost, which can be challenging to manage sustainably. Challenge: Balancing operational costs with environmental responsibility is difficult, especially as cleanroom standards continue to become more demanding. Cleanrooms operating at ISO Class 5 or better are particularly costly, requiring 100% HEPA filtration and maintaining positive air pressure. Solution: Energy-efficient technologies, such as advanced HVAC controls, energy recovery ventilators, and variable-speed motors, can help reduce costs. Lean manufacturing principles and optimizing cleanroom design to reduce unnecessary air exchanges can also improve energy efficiency without compromising cleanliness. 6. Cross-Contamination in Multiproduct Facilities Many pharmaceutical companies operate multiproduct facilities where different drugs or biologics are manufactured in shared spaces, raising the risk of cross-contamination. This issue is particularly pressing for facilities producing both traditional drugs and new biologics or cell and gene therapies, which require different contamination control standards.7 Challenge: Ensuring no cross-contamination between products requires robust cleaning protocols, validated containment procedures, and sometimes complete room shutdowns for cleaning. Multiproduct facilities may also need to segment their cleanrooms or install specialized air handling to prevent cross-contamination. Solution: Modular cleanroom setups allow sections of a cleanroom to be isolated and dedicated to a specific product for a particular production run, reducing the risk of cross-contamination. Dedicated air-handling systems for each production area also enhance containment. 7. Risk of Contamination in New Therapeutic Product Manufacturing Innovative therapies such as cell and gene therapies pose unique challenges for cleanroom environments due to their sensitivity to environmental factors and the need for even higher sterility levels. These therapies are often produced in small batches, increasing the risk of contamination from any procedural lapse. Challenge: Cell and gene therapies often require handling of live cells and genetic materials, which are susceptible to contamination that could ruin the entire batch and impact patient safety. These therapies also require a higher level of operator interaction, increasing contamination risks. Solution: Single-use technologies (SUTs), such as disposable bioreactors, tubing, and filters, reduce the risk of contamination by eliminating the need to sterilize reusable components. Closed-system processing, where production occurs in a sealed environment, is another solution gaining traction in cell and gene therapy manufacturing. 8. Cleanroom Automation and Technological Integration The complexity of modern cleanroom operations calls for sophisticated automation, such as robotic systems, process automation, and remote monitoring. Automation is highly beneficial in reducing human error and contamination, but it also introduces new challenges. Challenge: Integrating automation into cleanroom environments is often challenging due to compatibility issues with existing systems and the potential for introducing particles through mechanical wear. Additionally, the high upfront cost of automation technology and the need for specialized staff training can be prohibitive. Solution: Robust maintenance programs for automated equipment and careful planning of automation integration can mitigate these risks. Implementing modular automation that can be scaled or adjusted as needs evolve is another effective strategy. 9. Quality Control and Sterility Testing Quality control in cleanrooms involves regular sterility testing and validation procedures to ensure compliance and maintain product safety. The sterility testing process is often time-consuming and costly, particularly for high-value batches like biologics or gene therapies. Challenge: The challenge lies in balancing the thoroughness of quality control with production efficiency. Traditional sterility testing methods can be time-consuming, with long incubation periods that delay production timelines. Solution: Rapid microbial detection methods, such as ATP (adenosine triphosphate) bioluminescence, can help reduce the time needed for sterility testing. In addition, advanced methods like real-time PCR (Polymerase Chain Reaction) enable faster microbial detection, facilitating quicker batch release. Conclusion Cleanroom challenges in the pharmaceutical industry are multifaceted, spanning from stringent regulatory compliance to managing personnel-related contamination risks. With the rise of advanced therapeutic products like cell and gene therapies, the demand for precise control and contamination prevention has never been higher. While technological advances in automation, monitoring, and containment offer potential solutions, the industry must continuously adapt to maintain the high standards required for patient safety and product efficacy.

Dear all, We are excited to invite you to visit 14644 Cleanroom at Cleanroom EXPO in Copenhagen, taking place October 22-23, 2024. As a global leader in cleanroom consultancy, we specialize in providing expert guidance on every aspect of cleanroom environments, from initial design to day-to-day operations. Stop by Booth #6 to learn how our tailored solutions can support your cleanroom projects with the highest level of specialist competence. Whether you're looking to optimize existing facilities or planning a new build, our team is here to help. We look forward to meeting you at Cleanroom EXPO! Read more: All About Cleanrooms - The ultimate Guide
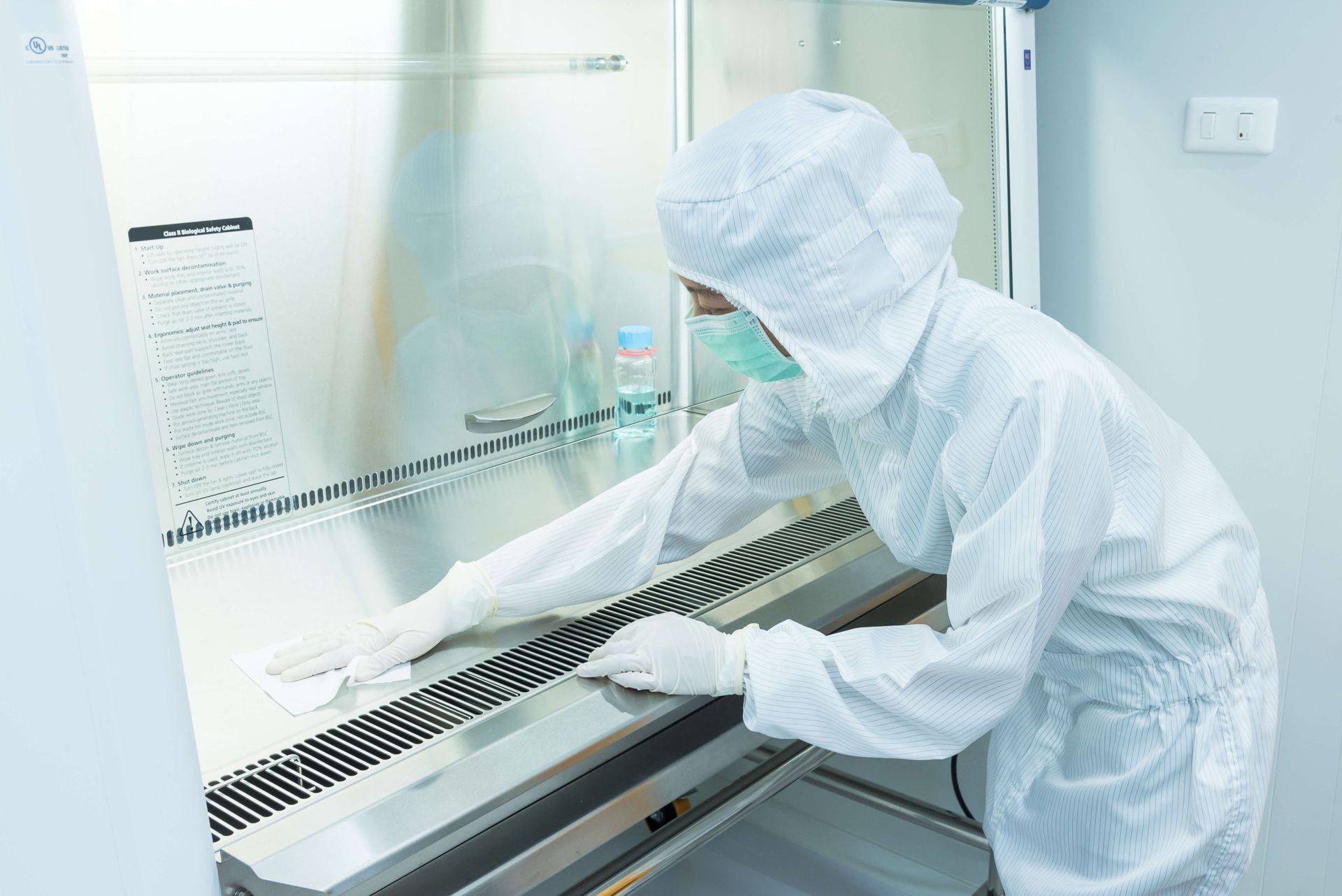
Introduction Cleanrooms are highly controlled environments designed to minimize the presence of contaminants such as dust, airborne particles, microorganisms, and chemical vapors. These contaminants can be harmful to the sensitive processes carried out in industries like pharmaceuticals, biotechnology, aerospace, microelectronics, and healthcare. The effectiveness of a cleanroom relies on maintaining stringent environmental controls, which is why regular maintenance and cleaning schedules are essential. This article delves into the importance of cleanroom maintenance and the need for structured cleaning schedules to ensure optimal performance, product quality, and safety. 1. Understanding Cleanrooms and Contamination Control A cleanroom is a controlled environment where parameters like air quality, temperature, humidity, and particle count are strictly regulated. These rooms are classified based on the number of particles per cubic meter of air, with each classification specifying a maximum threshold for airborne contaminants. For example, an ISO Class 1 cleanroom allows only 12 particles per cubic meter, while a Class 9 cleanroom allows up to 35,200,000 particles. Contaminants in a cleanroom can arise from various sources, including: Personnel: Skin flakes, hair, and oils from human bodies are significant contributors. Materials: Packaging materials, equipment, and supplies can introduce particles and microorganisms. Processes: Operations such as soldering, painting, or chemical handling can release particulates and volatile organic compounds (VOCs). Airflow and Ventilation Systems: Even small inefficiencies in filtration or airflow patterns can lead to contamination. In industries where microscopic contamination can compromise product integrity, such as semiconductor manufacturing or drug production, cleanroom standards must be met meticulously. A single lapse in cleanliness can result in costly production failures, product recalls, regulatory non-compliance, and potentially endanger human lives. 2. The Importance of Cleanroom Maintenance Proper maintenance ensures that cleanrooms continuously meet stringent operational standards. Cleanroom maintenance extends beyond simple cleaning— it includes regular inspection, calibration, and repair of the infrastructure, air filtration systems, and environmental control equipment. Key areas where maintenance is critical include: a) HVAC and Air Filtration Systems HVAC (Heating, Ventilation, and Air Conditioning) systems are the backbone of any cleanroom. These systems control airflow, temperature, and humidity, all of which are essential in minimizing airborne particles. The air is filtered through HEPA (High-Efficiency Particulate Air) or ULPA (Ultra-Low Penetration Air) filters, which need regular maintenance and replacement. If filters become clogged or inefficient, contaminants can bypass filtration, putting cleanroom integrity at risk. Regular inspection and validation of these systems are crucial for maintaining proper airflow patterns and particle control. b) Environmental Monitoring Systems Cleanrooms are outfitted with various monitoring systems that track temperature, humidity, pressure differentials, and particle counts. These systems must be calibrated periodically to ensure accurate readings. Failure to maintain these systems can result in undetected shifts in environmental conditions, which could lead to contamination. c) Surfaces, Equipment, and Furniture All surfaces in a cleanroom, from workbenches to walls, must be designed to minimize particle accumulation and facilitate easy cleaning. Any scratches, dents, or porous materials can become breeding grounds for microorganisms or places where dust accumulates. Equipment maintenance involves not only cleaning but also ensuring that machines operate without generating excess particles or emissions. d) Personnel Protocols Personnel are one of the most significant contamination sources in cleanrooms. Proper training, gowning procedures, and adherence to operational protocols are critical. However, even with perfect behavior, cleanroom garments, gloves, and other personal protective equipment (PPE) degrade over time. Regular inspection of PPE, replacement of worn garments, and retraining staff on contamination risks are key aspects of ongoing cleanroom maintenance. 3. The Role of Cleaning Schedules A well-structured cleaning schedule is fundamental in maintaining cleanroom standards. The cleaning process itself needs to be meticulous, as improper cleaning can introduce more contaminants than it removes. Cleanroom cleaning must adhere to specific protocols, including the use of approved cleaning agents, specialized equipment, and techniques designed to avoid spreading contaminants. a) Regularity of Cleaning How often a cleanroom is cleaned depends on its classification, use, and contamination risks. High-class cleanrooms, like those in the semiconductor industry (ISO Class 1 or 2), may require daily or even hourly cleaning. Lower-class cleanrooms (e.g., Class 8 or 9) may require less frequent cleaning, but should still follow a strict schedule to avoid contamination buildup. A typical cleaning schedule might involve: Daily cleaning: Wiping down surfaces, cleaning floors, and disinfecting door handles or equipment surfaces. Weekly cleaning: Deeper cleaning tasks like cleaning walls, ceilings, and more intensive equipment disinfection. Monthly or Quarterly cleaning: HEPA filter validation, deep cleaning of hard-to-reach areas, and full equipment calibration. b) Specialized Cleaning Procedures Different areas of the cleanroom may require specific cleaning approaches. For example, areas near entrances (airlocks or gowning rooms) tend to have higher contamination risks, so they may require more frequent and thorough cleaning than the interior spaces. Similarly, areas where high-risk processes are carried out, such as sterile drug production, will require stringent cleaning procedures and sterilization techniques. c) Cleaning Agents and Methods The cleaning agents used in cleanrooms must be carefully selected to avoid introducing harmful chemicals, residues, or particles. Some common cleaning agents include isopropyl alcohol (IPA), hydrogen peroxide, and quaternary ammonium compounds. The tools used, such as lint-free wipes, vacuum cleaners with HEPA filters, and non-shedding mops, are also critical in preventing contamination. Cleaning methods typically follow a top-down approach, starting from the ceilings and working down to the floors to avoid spreading contaminants. In some industries, specialized techniques like fogging or sterilization with vaporized hydrogen peroxide may be employed to achieve ultra-clean environments. 4. Benefits of Adhering to a Cleanroom Maintenance and Cleaning Schedule a) Enhanced Product Quality Regular maintenance and cleaning minimize the presence of contaminants, ensuring that products—whether they are pharmaceuticals, semiconductors, or medical devices—meet high-quality standards. This is particularly crucial in industries where even the smallest contaminant can render a product unusable, such as microelectronics, where particles can cause circuitry failures. b) Regulatory Compliance Many industries are subject to strict regulatory oversight, with governing bodies like the FDA, ISO, and EU GMP (Good Manufacturing Practices) setting forth guidelines for cleanroom operations. Failing to maintain proper cleanliness and environmental conditions can lead to non-compliance, product recalls, or even plant shutdowns. Regular cleaning and maintenance help ensure that cleanrooms remain compliant with all relevant regulations. c) Increased Equipment Longevity Cleanrooms house expensive equipment, and contamination can cause damage or malfunctions. For example, particle build-up in sensitive manufacturing tools can cause inaccuracies or downtime. Regular maintenance, including cleaning, calibration, and repair of equipment, ensures a longer lifespan and smoother operation, preventing costly repairs and replacements. d) Safety of Personnel and Patients In industries such as pharmaceuticals or healthcare, cleanroom contamination can directly impact human health. For instance, in sterile drug production, microbial contamination could lead to patient infections or compromised drug efficacy. Regular maintenance and cleaning schedules reduce these risks, ensuring that products remain sterile and safe for use. e) Cost Savings While cleanroom maintenance and cleaning may seem like a significant expense, the costs associated with contamination—lost production time, damaged products, equipment failures, and regulatory penalties—far outweigh the price of regular upkeep. Proactively maintaining a cleanroom can prevent costly incidents, reduce waste, and increase operational efficiency. Conclusion Cleanroom maintenance and cleaning schedules are essential components of contamination control. Without rigorous maintenance and structured cleaning routines, cleanrooms would quickly become ineffective, risking product quality, regulatory compliance, and personnel safety. Industries that rely on cleanrooms must prioritize regular inspection, calibration, and cleaning to ensure that they meet the highest standards of cleanliness and performance. By adhering to a comprehensive maintenance and cleaning schedule, companies can safeguard their operations, protect their reputation, and ensure that their products are both safe and effective. Read more: All About Cleanrooms - The ultimate Guide