The Role of Cleanrooms in Aerospace Manufacturing
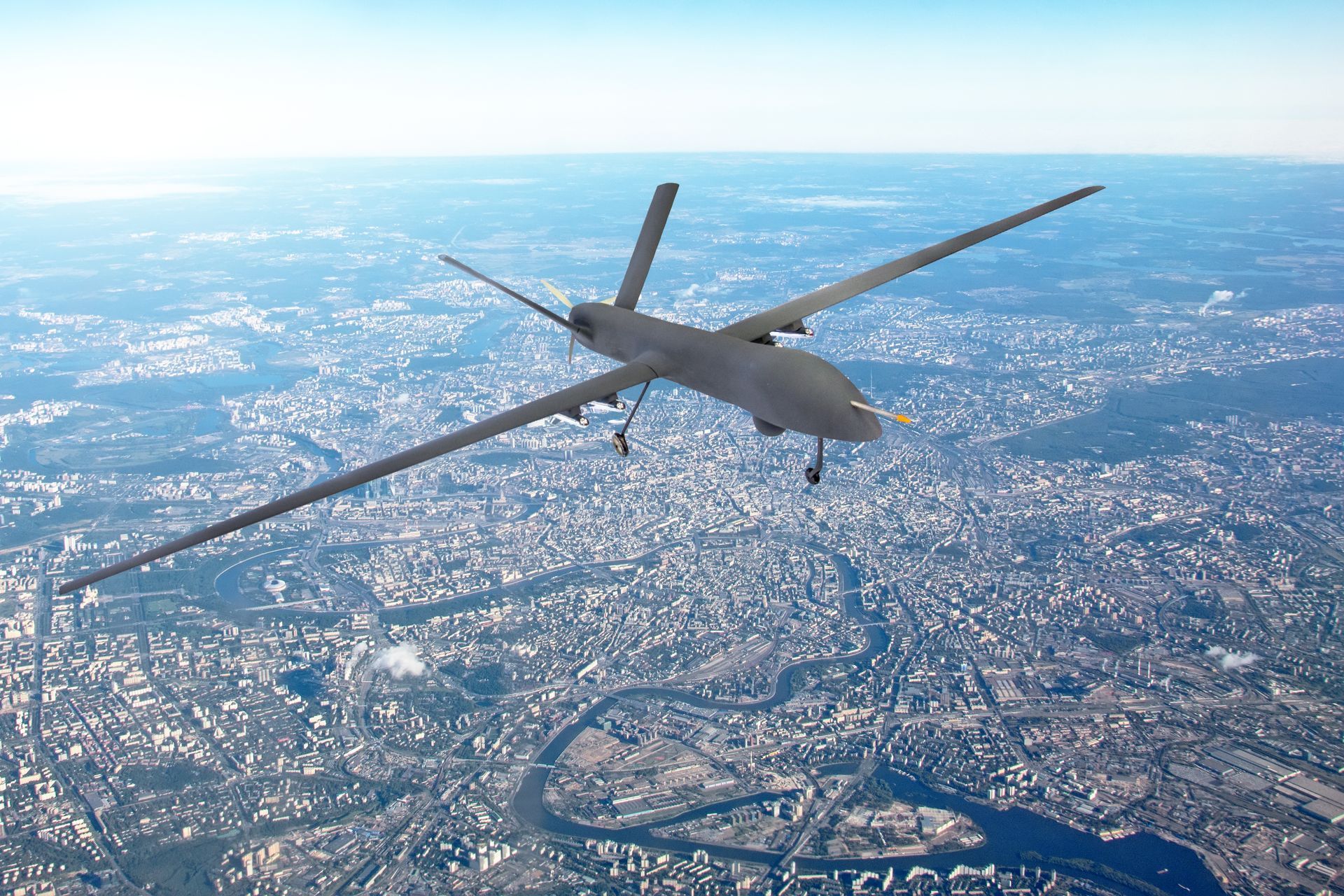
Introduction
Cleanrooms play a crucial role in the aerospace industry, where precision, reliability, and compliance with stringent standards are paramount. From satellite assembly to the production of aircraft components and space exploration vehicles, maintaining a contaminant-free environment is vital to ensure the performance and safety of aerospace products. This article delves deeply into the role of cleanrooms in aerospace manufacturing, examining the specifications, technologies, and processes involved, as well as the challenges and advancements shaping this critical aspect of aerospace engineering.
Introduction to Cleanrooms in Aerospace Manufacturing
Cleanrooms are controlled environments with low levels of pollutants such as dust, airborne microbes, and aerosol particles. In aerospace manufacturing, these facilities are designed to control particulate contamination and ensure that the environment does not adversely affect the products being manufactured. The importance of cleanrooms in this sector cannot be overstated, given the catastrophic consequences that contamination could cause in aerospace applications.
Specifications and Standards
The aerospace industry adheres to stringent cleanroom standards, primarily governed by ISO 14644 and IEST standards for cleanrooms. The ISO 14644 series specifies cleanroom air cleanliness in terms of the number of particles per cubic meter at specified particle size. The required class of cleanroom varies depending on the particular aerospace application. For instance, manufacturing of spacecraft components typically requires ISO Class 5 or better, which allows no more than 3,520 particles (0.5 microns or larger) per cubic meter.
In addition to ISO standards, aerospace manufacturers must also comply with specific industry standards such as those from NASA and the Department of Defense, which may have unique requirements for particular projects or components.
Key Applications of Cleanrooms in Aerospace Manufacturing
1. Satellite Assembly: The assembly and testing of satellites require highly controlled environments to prevent the contamination of sensitive onboard electronics and optical components. Even microscopic particles can cause failure of sensors and circuits, which is unacceptable in space missions.
2. Aircraft Component Manufacturing: High-precision components such as turbine blades and avionics are manufactured in cleanrooms. Contamination in these components can lead to inefficiencies, increased fuel consumption, or catastrophic failures.
3. Space Exploration Vehicles: Cleanrooms are essential for the assembly of space exploration vehicles, including rovers and spacecraft. These vehicles operate in extreme conditions where any failure could jeopardize the entire mission and lead to significant financial losses.
Technologies and Equipment
The effectiveness of cleanrooms in aerospace manufacturing hinges on several key technologies and pieces of equipment:
- HEPA and ULPA Filters: These filtration systems are capable of trapping 99.97% to 99.9995% of particles, respectively, providing the necessary air purity for sensitive manufacturing processes.
- Air Showers and Pass-Through Chambers: Used to minimize contamination when personnel or materials enter the cleanroom.
- Temperature and Humidity Control Systems: Precise control over temperature and humidity is crucial to prevent static build-up and condensation, which can damage sensitive aerospace components.
- Laminar Air Flow Systems: These systems direct filtered air in a constant stream, reducing the chance of turbulent air that can stir up particles.
Challenges in Aerospace Cleanroom Management
1. Maintaining Stringent Contamination Control: Continuous monitoring and maintenance are required to ensure that cleanrooms remain within the required specifications for particle counts, air purity, and environmental conditions.
2. High Operational Costs: Operating a cleanroom is expensive due to the energy costs of air handling systems and the need for specialized maintenance of filtration and HVAC systems.
3. Technological Advancements: Keeping up with advances in aerospace technology often requires upgrades to cleanroom facilities to handle new materials or components that have higher sensitivity to contaminants.
Future Trends and Innovations
The future of cleanrooms in aerospace manufacturing is likely to see several innovations:
- Automation and Robotics: To reduce human error and further minimize contamination, more processes within cleanrooms are expected to be automated or handled by robots.
- Advanced Materials: The development of new materials that are less prone to shedding particles or attracting contaminants could reduce the need for stringent cleanroom conditions.
- Real-Time Monitoring Technologies: Enhanced sensors and IoT technologies are expected to provide real-time data on cleanroom conditions, allowing for immediate adjustments and predictive maintenance.
Conclusion
Cleanrooms are indispensable in aerospace manufacturing, providing the necessary controlled environment to manufacture highly reliable and high-performance aerospace components. As the aerospace industry continues to push the boundaries of technology and exploration, the role of cleanrooms will only grow in importance, driven by advancements in cleanroom technologies and practices.
Adhering to strict cleanroom standards and continually evolving with technological advancements ensures that aerospace products are manufactured with the highest reliability, supporting the overall safety and success of aerospace missions.
Read more: All About Cleanrooms - The ultimate Guide
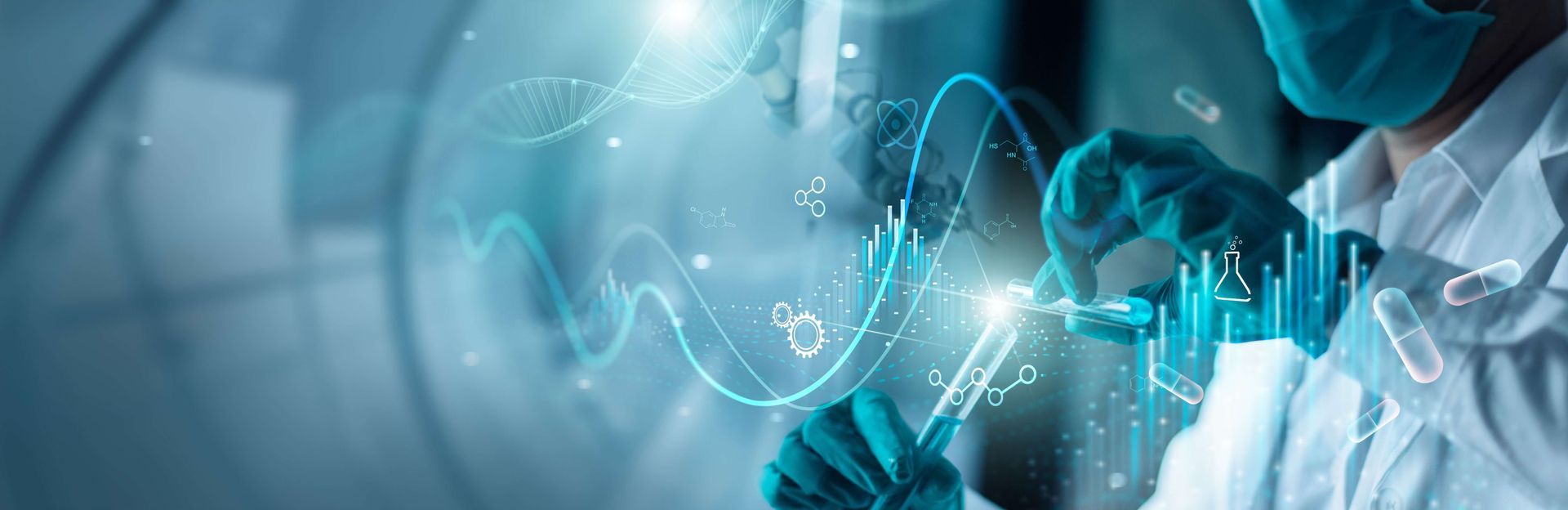
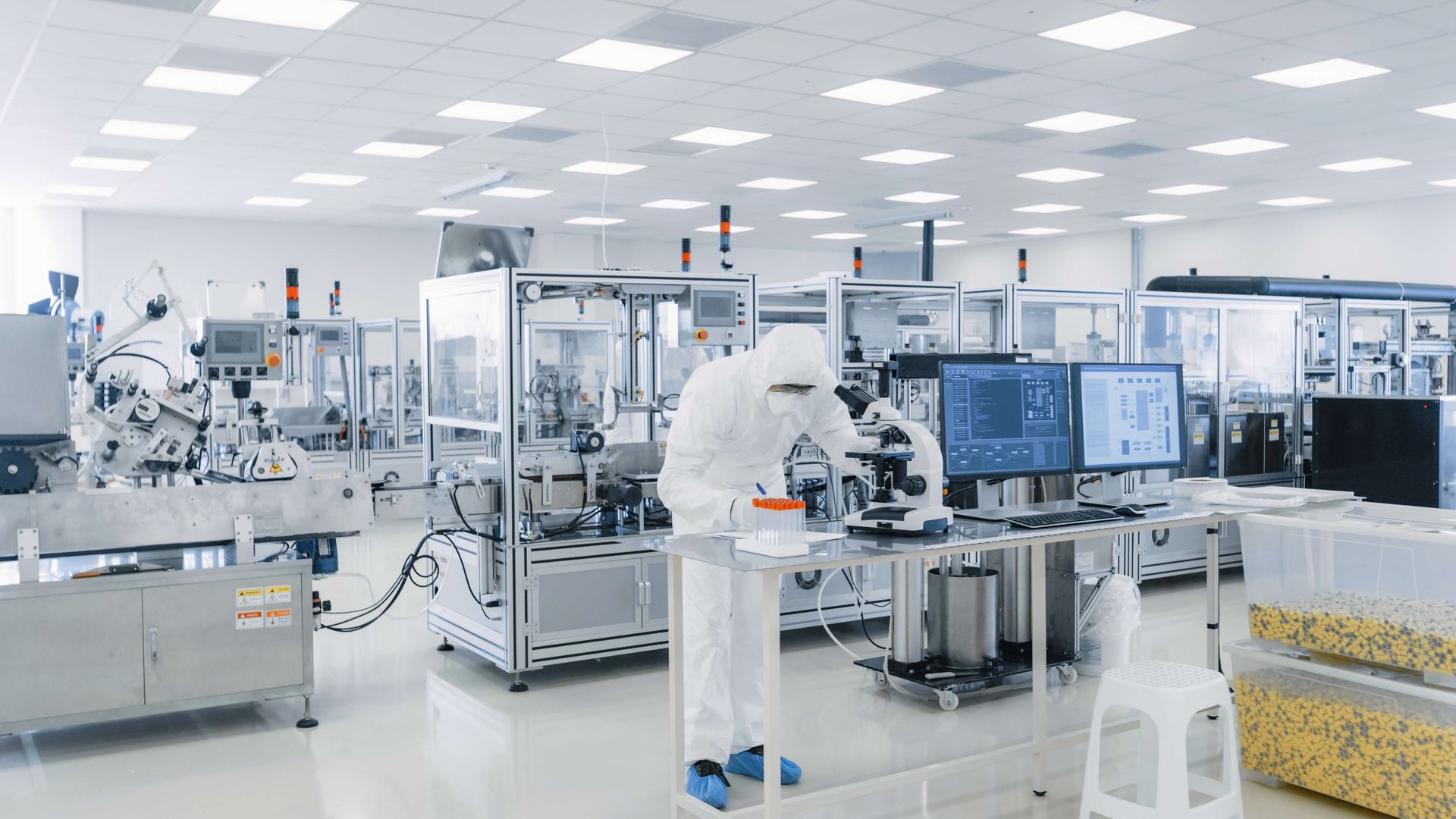