Cleanroom Testing and Validation Procedures
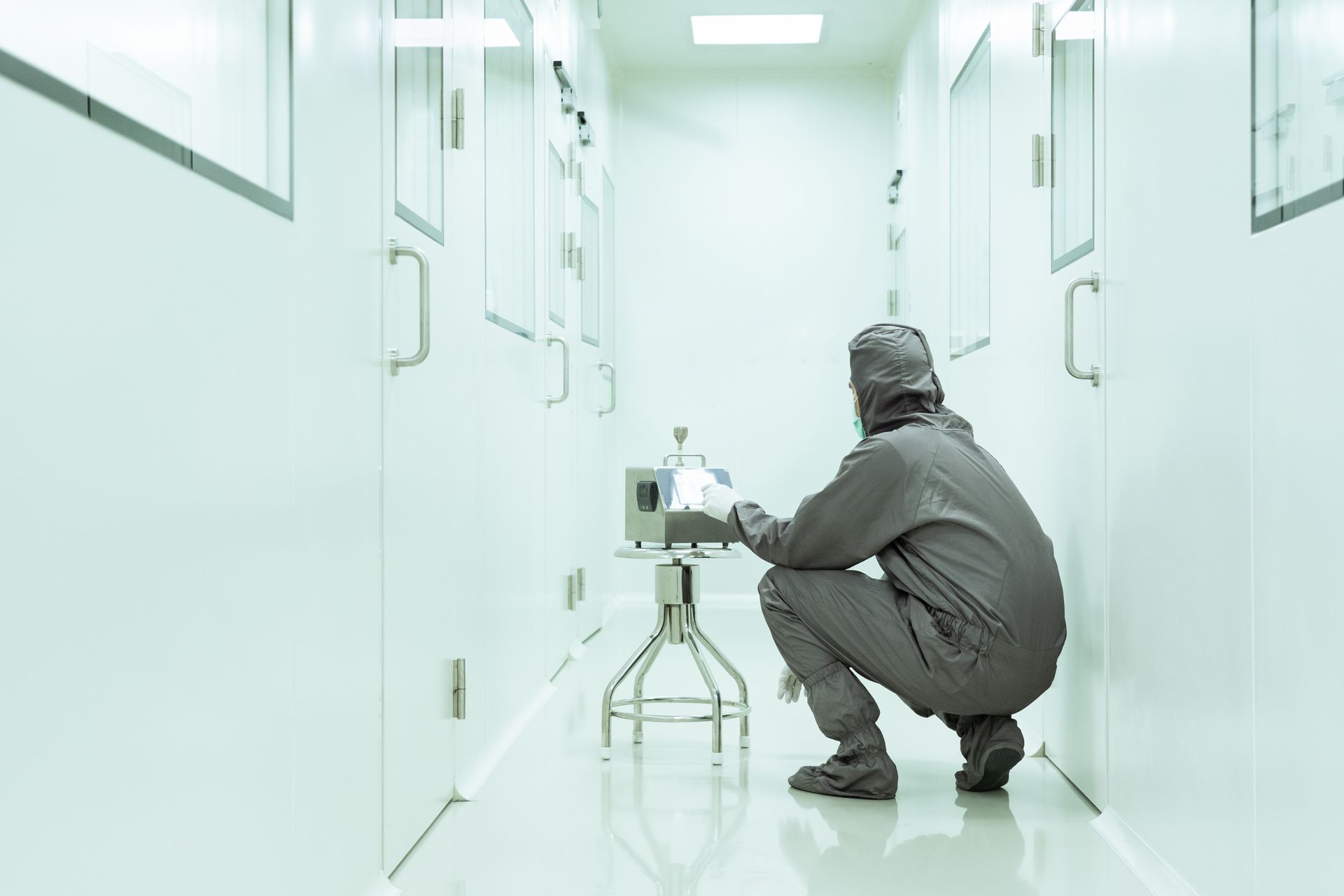
Introduction
Cleanroom testing and validation are critical procedures to ensure that these specialized environments meet specific standards and regulations necessary for maintaining the integrity of the manufacturing process and product quality. Particularly in industries like pharmaceuticals, biotechnology, semiconductor manufacturing, and aerospace, where even the smallest contaminants can compromise the production, these procedures are not merely routine checks but integral to the operational excellence of the facility.
Understanding Cleanroom Testing and Validation
Cleanroom testing and validation involve a series of assessments that verify the cleanroom's performance meets the predefined standards and requirements. These standards are often governed by international norms such as ISO 14644 or, for pharmaceutical environments, could also adhere to GMP (Good Manufacturing Practice) standards.
The primary goal of these procedures is to document and ensure that all aspects of the cleanroom environment—from air quality to equipment and surfaces—do not introduce contamination that could affect the manufacturing process or final product quality.
Key Procedures in Cleanroom Validation
1. Installation Qualification (IQ): Installation Qualification is the first step in the validation process. IQ checks ensure that the equipment, components, and cleanroom setup comply with the manufacturer’s specifications and that everything has been installed correctly. This involves reviewing design specifications, verifying installation manuals, and ensuring that all components of the cleanroom are appropriately installed and configured.
2. Operational Qualification (OQ): Operational Qualification follows IQ and tests the cleanroom's performance under operational conditions. OQ involves testing equipment and systems to ensure they function according to their operational specifications within the cleanroom setting. This includes testing HVAC systems, filters, lighting, and any other critical systems for operational reliability.
3. Performance Qualification (PQ): Performance Qualification is the final stage of the validation process. PQ tests the cleanroom's performance over time to ensure it consistently meets the required operating standards under actual production conditions. This involves continuous monitoring of parameters such as particle counts, temperature, humidity, and pressure differentials over a specified period.
Detailed Cleanroom Testing Methods
- Particulate Testing: This test measures the number of particles in the cleanroom air to verify that it meets the specific classification for which it is designed. For instance, an ISO 5 cleanroom allows no more than 3,520 particles (0.5 microns or larger) per cubic meter of air. Particulate testing uses particle counters to conduct this evaluation.
- Airflow Testing: Airflow tests measure the velocity and uniformity of the air supply within the cleanroom. Proper airflow is crucial to maintain cleanliness standards, as it ensures particles are swept away from critical areas and efficiently filtered out of the environment.
- Filter Integrity Testing: HEPA and ULPA filters are pivotal in maintaining cleanroom standards. Filter integrity tests, such as the DOP (Dispersed Oil Particulate) test, check for leaks or flaws in the filter media and sealing. This ensures that no unfiltered air bypasses the filtration system.
- Recovery Rate Testing: This test determines how quickly a cleanroom recovers to its baseline cleanliness level after a contamination event. The recovery rate is crucial for environments where cleanroom integrity needs to be quickly restored following routine operations or accidental breaches.
- Pressure Differential Testing: Maintaining specific pressure differentials between adjacent areas prevents contaminants from entering the cleanroom. This test ensures that the cleanroom maintains the correct pressure differential, essential for contamination control.
- Temperature and Humidity Control: Consistent temperature and humidity levels are essential for certain manufacturing processes and for minimizing static electricity, which can attract particles. Tests must confirm that the HVAC system maintains these parameters within the specified limits.
Challenges in Cleanroom Testing and Validation
Cleanroom validation is a complex, resource-intensive process that requires meticulous planning and execution. Challenges often arise from changes in production processes, upgrades to cleanroom facilities, or regulatory updates. Each of these factors can necessitate re-validation or adjustments in testing protocols.
Additionally, human error and technical failures can introduce inconsistencies in test results. It is crucial to train personnel thoroughly and use well-calibrated, reliable testing equipment to mitigate these risks.
Conclusion
Cleanroom testing and validation are not just regulatory requirements but essential practices that protect the integrity of critical manufacturing processes and ensure product quality. As technology advances and regulatory environments evolve, cleanroom testing and validation procedures will continue to adapt, incorporating more sophisticated techniques and technologies to meet the stringent demands of modern manufacturing environments. For industries reliant on controlled environments, staying ahead in implementing advanced testing and validation methodologies is not just about compliance, but about gaining a competitive edge.
Read more: All About Cleanrooms - The ultimate Guide
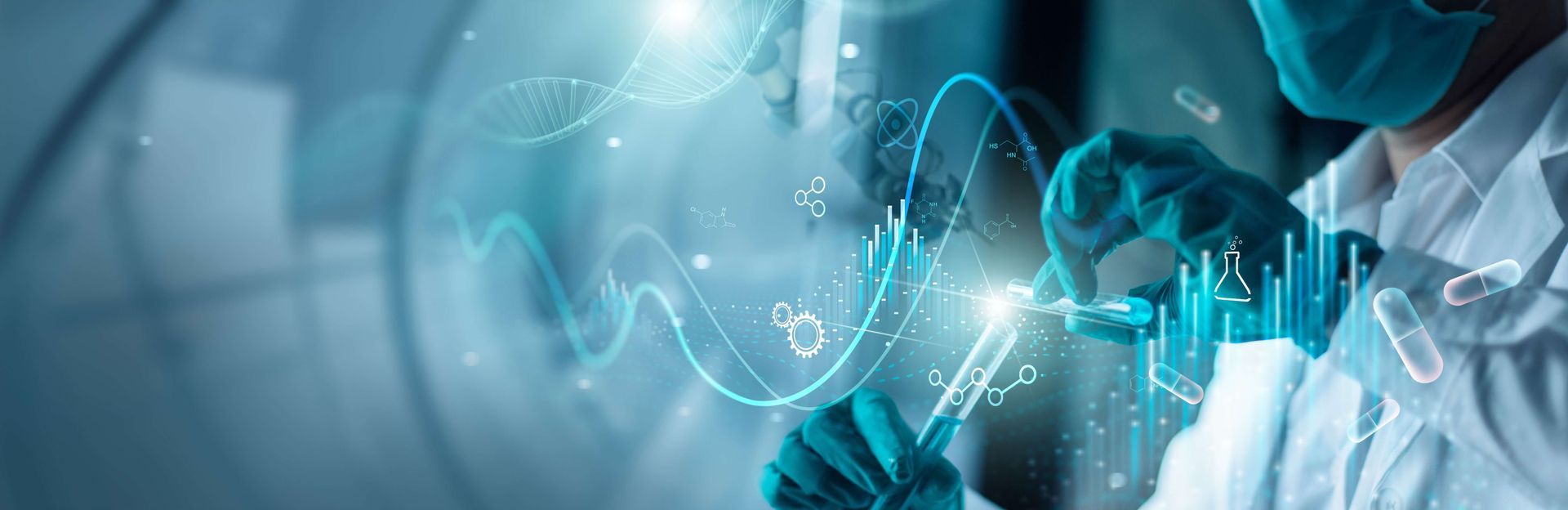
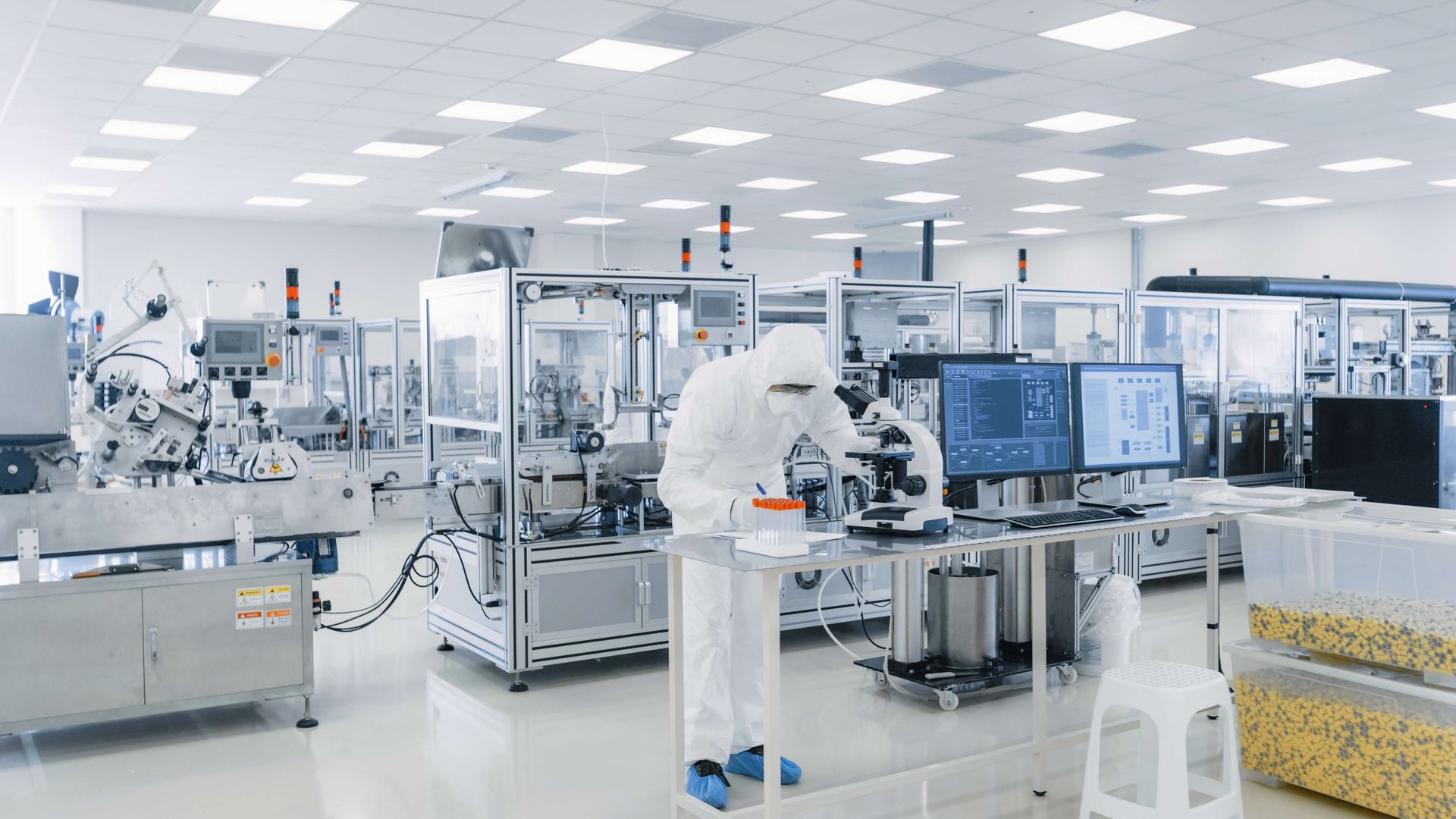