Cleanroom Flooring: Options and Considerations
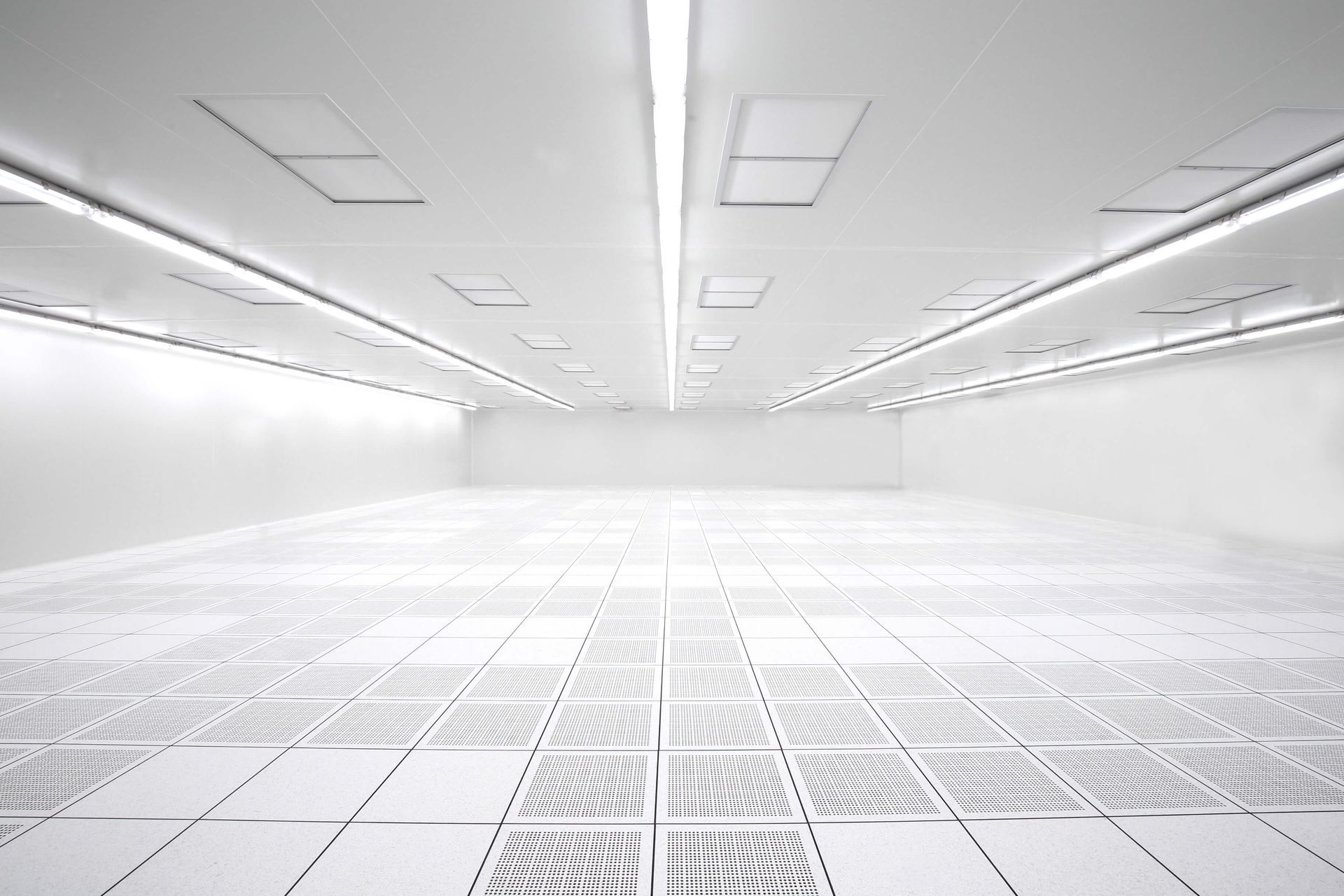
Introduction
Cleanrooms are environments meticulously controlled to maintain a specific level of cleanliness and to minimize contamination, such as dust, airborne particles, microbes, and chemical vapors. These environments are critical in industries such as pharmaceuticals, biotechnology, semiconductor manufacturing, aerospace, and medical device production, where the slightest contamination can have severe consequences for product quality, safety, and regulatory compliance. While most discussions about cleanrooms focus on air filtration, gowning procedures, and other aspects of contamination control, one area that deserves careful attention is the floor.
Cleanroom flooring plays a crucial role in maintaining the integrity of the controlled environment. It must support the high standards of cleanliness required in such spaces while also providing durability, ease of maintenance, and safety. Flooring in a cleanroom is subjected to foot traffic, machinery, spills, and harsh cleaning protocols, which all require careful consideration in selecting the appropriate material and system.
This article delves into the various options for cleanroom flooring, the factors that influence the choice of flooring, and the key considerations to ensure that the flooring helps to maintain the cleanroom's stringent cleanliness and safety standards.
Importance of Cleanroom Flooring
Cleanroom flooring is not just about aesthetic appeal; it plays a vital role in several important aspects of cleanroom functionality. Cleanroom floors help in the following areas:
- Contamination Control: Flooring is a primary surface in cleanrooms that must not contribute to contamination. It needs to be resistant to particulate buildup and easy to clean to ensure the elimination of potential contaminants.
- Safety: In some industries, such as pharmaceuticals or food production, safety is paramount. Cleanroom flooring needs to offer slip resistance, especially in areas where fluids or chemicals may be present.
- Durability: Given the heavy equipment, foot traffic, and cleaning routines in cleanrooms, the flooring must be robust enough to withstand wear and tear without compromising its ability to maintain cleanliness standards.
- Maintenance: Flooring should be easy to maintain, as cleanroom environments require constant cleaning. The material chosen should be resistant to staining, chemical damage, and abrasion, allowing for quick and effective cleaning routines.
Cleanroom Flooring Options
The type of flooring selected for a cleanroom will depend on factors such as the cleanroom’s ISO classification, the nature of the industry, and the anticipated traffic levels. Below are some of the most common cleanroom flooring options:
1. Epoxy Resin Flooring
Epoxy resin flooring is one of the most popular choices for cleanroom environments due to its excellent durability, seamless surface, and resistance to chemicals, wear, and abrasion. Epoxy floors consist of a two-part system: a hardener and a resin that, when mixed, form a chemical bond, creating a strong and long-lasting floor.
Advantages of Epoxy Flooring:
- Seamless Surface: Epoxy floors are seamless, meaning there are no joints or seams where dust and debris can accumulate, which helps in maintaining a high level of cleanliness.
- Chemical Resistance: Epoxy flooring is resistant to many industrial chemicals, making it an excellent choice for cleanrooms in industries like pharmaceuticals, biotechnology, and food production.
- Durability: Epoxy floors are highly resistant to wear, abrasion, and impact, ensuring that they can withstand heavy foot traffic and equipment movement.
Considerations:
- Surface Hardness: While epoxy flooring is durable, it can be prone to cracking under extreme impacts, and its hardness may cause damage to equipment if something is dropped.
- Initial Setup Costs: Epoxy floors can be costly to install, and the process may involve preparation of the substrate before application to ensure proper adhesion.
2. Vinyl Flooring
Vinyl flooring, specifically static-dissipative and conductive vinyl, is another common cleanroom flooring option. It is available in rolls or tiles and is highly valued for its cost-effectiveness and ease of installation.
Advantages of Vinyl Flooring:
- Ease of Installation: Vinyl flooring is easy to install and can be laid down quickly, making it ideal for projects where speed is of the essence.
- Antistatic Properties: Certain types of vinyl flooring are designed with antistatic properties, which is especially important in environments like semiconductor manufacturing, where static electricity could damage sensitive components.
- Comfort: Vinyl flooring is more forgiving underfoot than epoxy or tile, offering a degree of comfort for workers who spend long hours on their feet.
Considerations:
- Durability: While vinyl is durable, it is generally less robust than epoxy flooring and can be more susceptible to damage from sharp objects or heavy equipment.
- Cleaning Requirements: Vinyl floors can show signs of wear over time, especially in high-traffic areas, and may require periodic polishing or refinishing to maintain their appearance and effectiveness.
3. Rubber Flooring
Rubber flooring is another option that is particularly beneficial in cleanrooms where durability and safety are essential. Rubber floors are available in various thicknesses and are often used in cleanrooms where noise reduction and slip resistance are priorities.
Advantages of Rubber Flooring:
- Slip Resistance: Rubber provides excellent slip resistance, which is crucial in environments where wet conditions or spills are likely.
- Noise Reduction: Rubber flooring can help to absorb sound, making it ideal for cleanrooms in laboratories or production areas where noise can be an issue.
- Flexibility: Rubber flooring is highly flexible and can be cut to fit any shape or layout, providing versatility in design.
Considerations:
- Chemical Resistance: While rubber is resistant to many chemicals, it may not be as effective as vinyl or epoxy in environments with highly corrosive substances.
- Surface Maintenance: Rubber floors require more frequent cleaning and may show signs of wear or staining over time.
4. Antistatic and Conductive Flooring
In industries like semiconductor manufacturing and electronics assembly, the risk of static discharge is a significant concern. Antistatic and conductive flooring options are designed to dissipate electrostatic charges, preventing damage to sensitive equipment or components.
Advantages of Antistatic Flooring:
- Electrostatic Discharge (ESD) Protection: These floors prevent the buildup of static electricity, which could otherwise damage sensitive electronic components.
- Seamless and Durable: Similar to epoxy floors, antistatic flooring options are often seamless and durable, providing a clean and safe environment for critical production activities.
Considerations:
- Cost: Antistatic and conductive flooring solutions tend to be more expensive than standard flooring options.
- Maintenance: These floors require regular maintenance to ensure that their conductive properties are preserved over time.
5. Ceramic or Porcelain Tile Flooring
Ceramic or porcelain tile flooring is a traditional option that is sometimes used in cleanrooms, particularly in environments where temperature fluctuations, chemical resistance, and easy cleaning are priorities.
Advantages of Ceramic/Porcelain Flooring:
- Chemical Resistance: Tiles are resistant to most chemicals, making them suitable for cleanrooms in industries like pharmaceuticals and food production.
- Durability: Tiles are highly durable and resistant to scratching and impact, making them ideal for areas with heavy foot traffic.
Considerations:
- Seams: The grout between tiles can collect dust and debris, making cleaning more difficult than with seamless options like epoxy or vinyl.
- Installation Complexity: Installing tile flooring can be more complex and time-consuming than other options, particularly in cleanrooms where a high level of precision is required.
Raised Flooring in Cleanrooms: A Key Consideration
In many high-class cleanrooms, such as those classified under ISO 5, 4, 3, 2, and 1, a raised floor system is essential to meet the specific needs of cleanliness, safety, and airflow. A raised floor system creates an elevated platform above the subfloor, allowing for the placement of air filtration systems, wiring, cables, and utilities beneath the floor. This system is particularly important in cleanrooms where strict environmental control is required.
Advantages of Raised Flooring:
- Airflow and Ventilation: Raised floors allow for optimal airflow management, essential for maintaining the required cleanliness levels. With a raised floor, the air distribution system (typically underfloor ventilation) can maintain laminar airflow, which is crucial in controlling particulate contamination.
- Utility Management: In cleanrooms, there is a need to hide utilities, cables, and other equipment that should not be exposed to the cleanroom environment. Raised floors provide an efficient way to route all these utilities under the floor, ensuring they do not interfere with the cleanliness or the room’s functionality.
- Flexibility: Raised flooring systems provide flexibility in terms of layout and redesign. As cleanroom requirements change over time, the layout can be easily adjusted without the need for major renovations.
- Easy Maintenance: With a raised floor, cleaning and maintenance become easier as utilities and air systems are accessible without disturbing the cleanroom environment itself.
Considerations:
- Initial Installation Costs: Raised flooring systems can increase the initial cost of setting up a cleanroom, especially in high-class environments where precision is paramount.
- Potential Contamination Sources: If the raised floor is not maintained properly, it can become a source of contamination. The space between the raised floor and the subfloor must be regularly cleaned to prevent the accumulation of dust or particles that could compromise the cleanroom environment.
Conclusion
Cleanroom flooring is an essential component of any controlled environment, and the right choice of flooring can help maintain cleanliness, enhance safety, and ensure compliance with industry regulations. Each flooring option—be it epoxy, vinyl, rubber, ceramic, or antistatic—has its own set of advantages and considerations. When choosing the appropriate flooring for a cleanroom, it is critical to consider factors such as the cleanroom’s classification, the level of foot traffic, the potential for chemical exposure, and the ease of maintenance.
Additionally, for high-class cleanrooms (ISO 5, 4, 3, 2, 1), raised floor systems provide significant advantages in maintaining airflow, managing utilities, and ensuring flexibility, making them a vital part of the cleanroom design.
By selecting the right flooring material and system for the specific needs of the cleanroom, businesses can ensure that their cleanroom remains a safe, functional, and contamination-free environment. Whether the focus is on durability, chemical resistance, or static control, the right cleanroom flooring choice is key to maintaining the overall effectiveness of the cleanroom and supporting the industries that rely on them.
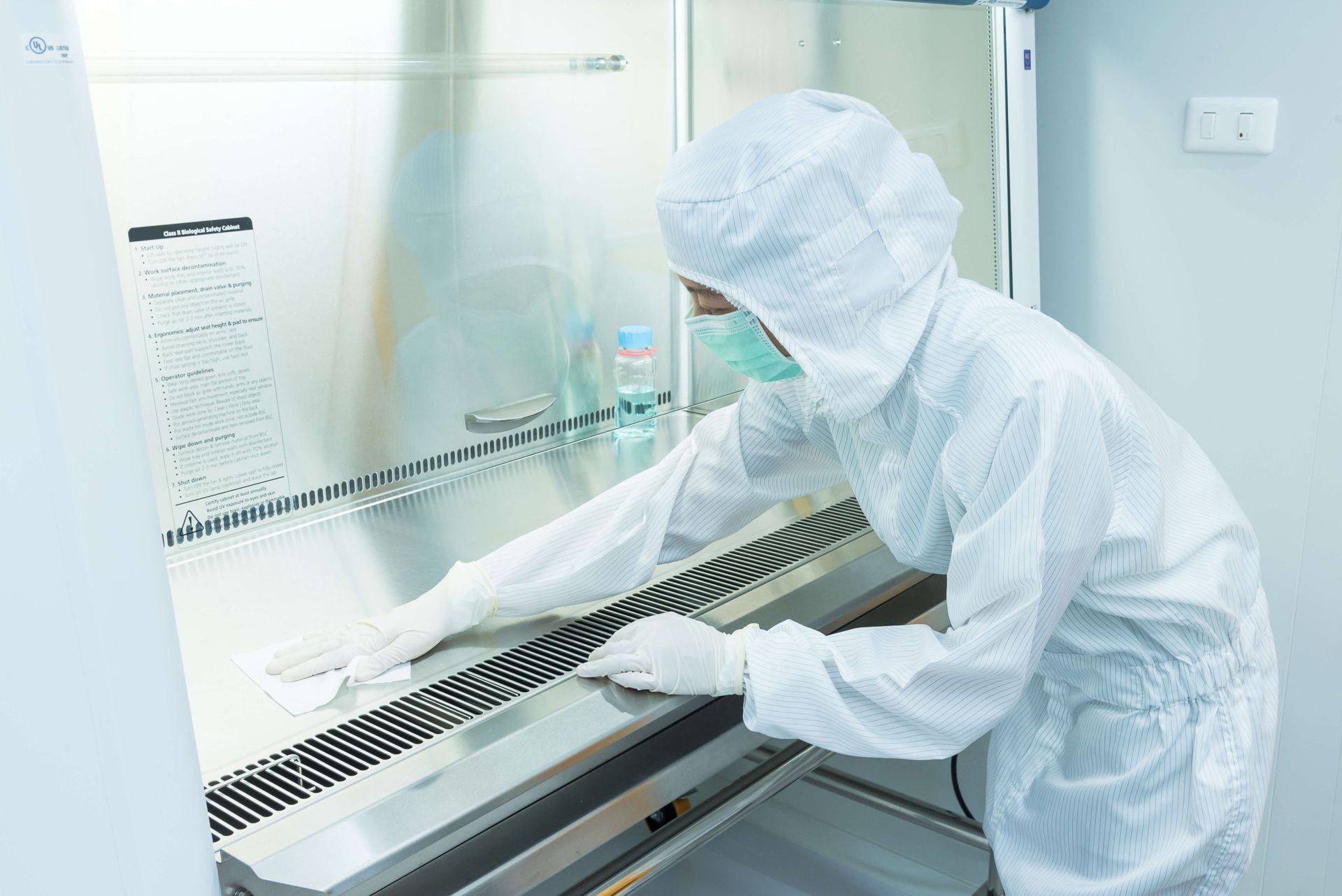
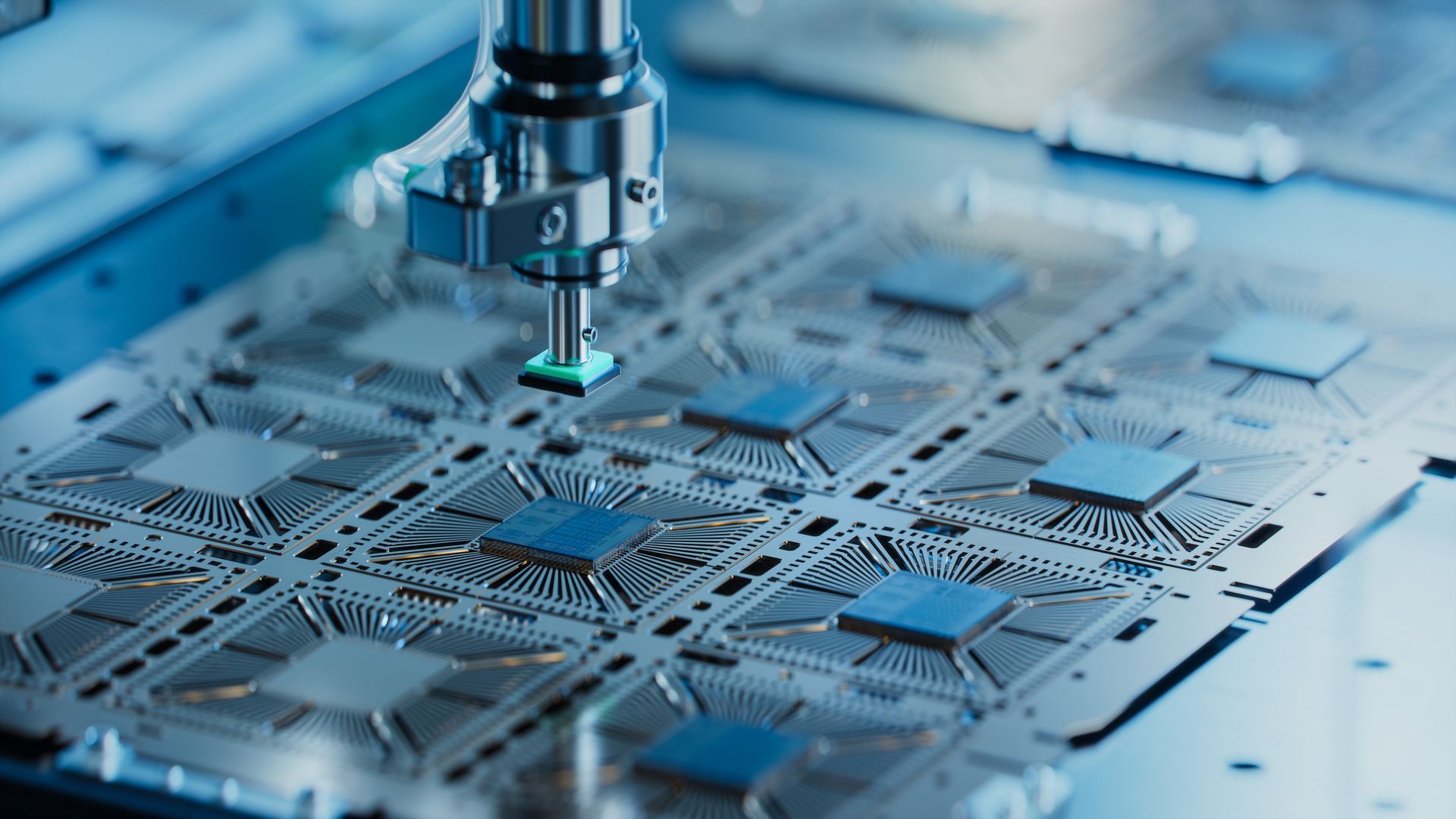