Managing Cleanroom Contamination: Best Practices
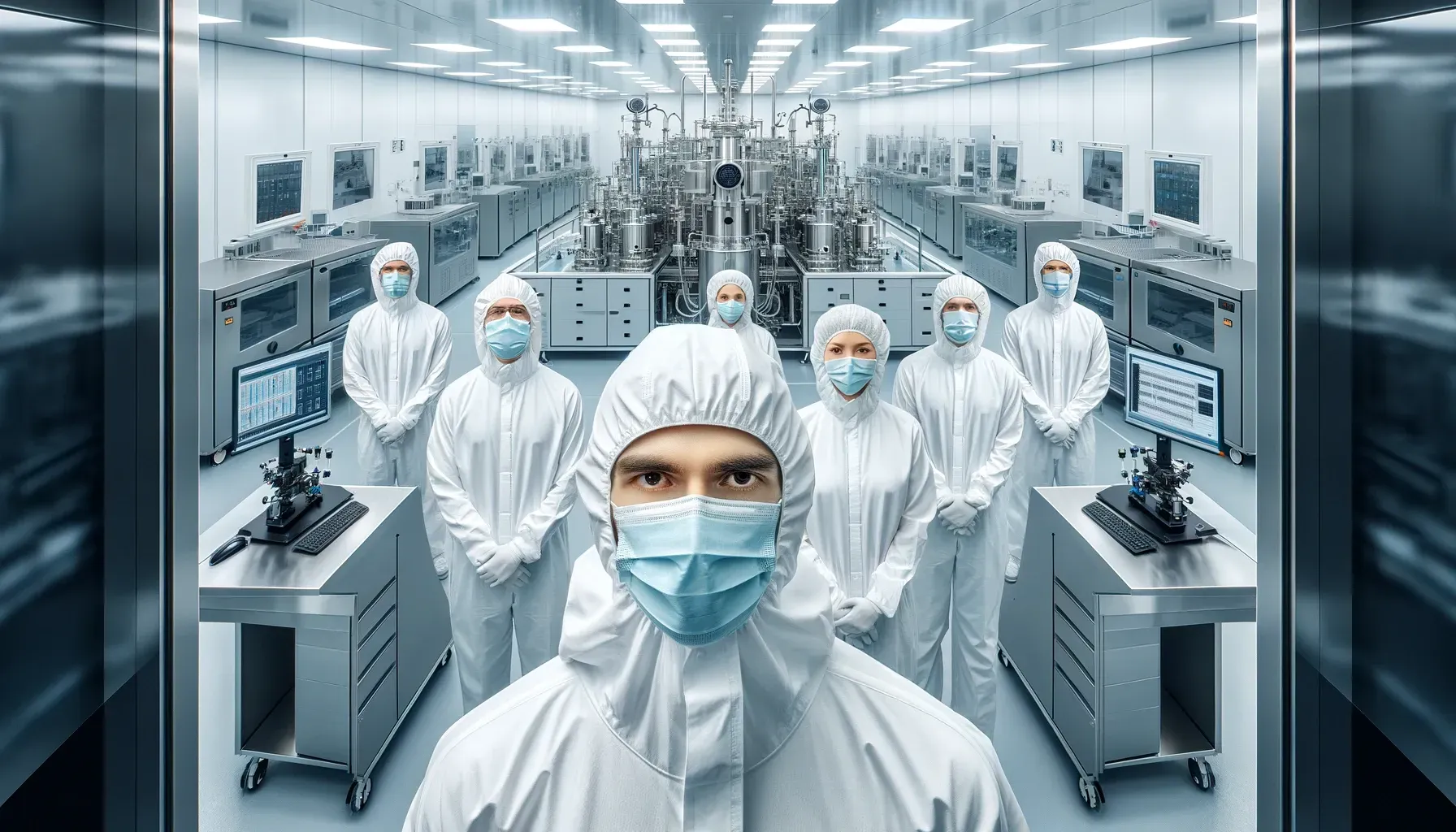
Introduction
Cleanrooms are critical environments in industries like pharmaceuticals, biotechnology, aerospace, semiconductors, and healthcare, where even minute contamination can compromise product quality, safety, and efficacy. Managing contamination in these controlled environments is paramount for ensuring compliance with regulatory standards, maintaining operational efficiency, and protecting both products and personnel. This article explores best practices for managing cleanroom contamination, providing detailed insights into contamination sources, control strategies, and operational protocols.
1. Understanding Cleanroom Contamination
Contamination in cleanrooms can stem from a variety of sources, including airborne particulates, biological contaminants, chemical residues, and even personnel working within the space. Contaminants are typically classified into two main categories:
- Particulate Contaminants: Dust, fibers, skin flakes, hair, and equipment-generated particles. Particulates are measured in terms of particle size and concentration.
- Microbiological Contaminants: Microorganisms such as bacteria, fungi, and viruses. These contaminants can compromise sterile processes, especially in pharmaceutical and biotechnological applications.
Common Contamination Sources:
- Personnel: The biggest source of contamination in cleanrooms, as human skin sheds cells and hair, while respiratory droplets can release microorganisms.
- Equipment and Materials: Machinery, tools, and incoming materials can introduce contaminants through wear, shedding, or insufficient cleaning.
- Airborne Particles: External air can bring in dust, pollen, and other particulates if filtration is inadequate.
- Process Materials: Solvents, chemicals, and gases used in the cleanroom can sometimes produce by-products that contribute to contamination.
2. Contamination Control Strategies
Effective contamination management in cleanrooms revolves around three key control strategies: Prevention, Minimization, and Mitigation. Let’s explore how these strategies can be applied in practice.
a. Facility Design and Airflow Control
The physical design of the cleanroom is the foundation of contamination control.
- Air Filtration and Ventilation: Cleanrooms rely on High-Efficiency Particulate Air (HEPA) or Ultra-Low Penetration Air (ULPA) filters to remove particles from the air. HEPA filters can capture 99.97% of particles as small as 0.3 microns, while ULPA filters capture 99.999% of particles as small as 0.12 microns. Proper placement of these filters in the cleanroom’s HVAC system ensures that only clean, filtered air enters the room.
- Positive Pressure: Maintaining a higher air pressure inside the cleanroom compared to adjacent spaces prevents contaminants from entering. This is particularly crucial for pharmaceutical and medical cleanrooms, where sterility is key. Conversely, negative pressure is used in cleanrooms where hazardous substances need to be contained within the environment.
- Laminar Flow: Cleanrooms often use laminar airflow systems to direct air in a uniform direction at a constant velocity. This creates a unidirectional airflow that sweeps particles away from critical areas, minimizing contamination risks.
- Air Change Rates (ACR): Cleanrooms typically experience multiple air changes per hour (ACH) to dilute and remove contaminants. Depending on the cleanroom class, the ACR can range from 30 to over 600 changes per hour. The appropriate ACR helps maintain a stable and clean environment.
b. Personnel Protocols and Hygiene Practices
Since personnel are the largest source of contamination, stringent protocols are essential to mitigate contamination risks.
- Gowning Procedures: Proper gowning is essential to minimize skin and hair shedding. Personnel entering the cleanroom must follow a step-by-step gowning procedure, which includes donning sterile suits, gloves, face masks, shoe covers, and sometimes full-face respirators. These garments should be made from non-linting materials to reduce particle shedding.
- Hand Hygiene: Before entering the cleanroom, personnel must thoroughly wash and sanitize their hands to remove potential contaminants. This reduces microbial contamination that could be transferred to gloves.
- Training and Behavior Protocols: Personnel should receive extensive training on proper cleanroom behavior, including minimizing movement, avoiding touching surfaces, and restricting unnecessary conversation. This is critical to reduce particle dispersion.
- Controlled Access: Limiting access to the cleanroom to only trained and authorized personnel helps reduce the overall contamination load.
c. Material and Equipment Handling
The way materials and equipment are handled in a cleanroom significantly impacts contamination levels.
- Cleaning and Disinfection: All equipment entering the cleanroom must be thoroughly cleaned and, if required, sterilized. Disinfectants should be carefully chosen based on their efficacy against specific contaminants (e.g., sporicidal agents for bacterial spores). Regular disinfection schedules must be adhered to, and surfaces should be frequently wiped down to remove residues and particles.
- Material Transfer Protocols: Items should be transferred into the cleanroom via airlocks or pass-through systems, where they are cleaned, wiped, or decontaminated before entry. Packaging materials should be kept to a minimum, as they can introduce fibers and particles.
- Minimizing Equipment Movement: Moving equipment or materials within the cleanroom can stir up contaminants. Wherever possible, fixed workstations should be used to reduce unnecessary equipment movement.
d. Environmental Monitoring
Routine monitoring of the cleanroom environment is essential to ensure compliance with cleanliness standards and identify potential contamination
risks early.
- Particle Counting: Automated particle counters are used to measure the concentration of airborne particles. Continuous monitoring ensures that particle levels remain within specified limits for the cleanroom class (e.g., ISO Class 5, 6, 7).
- Microbial Monitoring: Settling plates, swabs, and contact plates can be used to assess microbial contamination on surfaces and in the air. Regular testing helps detect potential contamination breaches, particularly in sterile environments.
- Temperature and Humidity Control: Maintaining appropriate temperature and humidity levels is vital for minimizing particle aggregation and preventing microbial growth. Excess moisture can promote mold and bacterial growth, while static electricity buildup from low humidity can attract dust and other particles.
3. Best Practices for Cleanroom Contamination Management
Here are consolidated best practices to ensure robust contamination control in cleanrooms:
a. Adherence to Cleanroom Classification Standards
Cleanrooms are classified based on the number and size of particles allowed per cubic meter of air, as specified by standards like ISO 14644. Regular validation and requalification of cleanroom performance (e.g., particle counts, airflow, pressure differentials) ensure continued compliance with these standards. This validation should be performed following any significant maintenance, repair, or change in operation.
b. Regular and Thorough Cleaning Protocols
Scheduled cleaning protocols should cover all surfaces (walls, floors, ceilings), workstations, and equipment in the cleanroom. Cleaning should be done with approved, low-shedding materials like lint-free wipes, and disinfectants should be rotated to prevent microbial resistance.
- Cleaning Tools: Use non-shedding mops and wipes made from microfiber or polyester materials that minimize particle generation. Avoid using tools that can harbor contaminants, like cotton or cellulose-based materials.
c. Environmental Controls for Critical Zones
Critical areas where contamination control is paramount, such as around product filling lines or exposed materials, should have stricter controls. These may include higher levels of HEPA filtration, increased airflow rates, and more stringent gowning requirements. Additionally, monitoring should be more frequent in these zones.
d. Waste and Disposable Management
Waste materials must be regularly removed from the cleanroom, and disposable items like gloves, wipes, and gowns should be used efficiently and discarded appropriately. Segregating waste into different categories (e.g., biological, chemical) helps reduce contamination risks.
e. Contamination Incident Response Plans
Having a well-documented response plan for contamination events (e.g., microbial breaches, equipment failure) is essential. This should include immediate steps for containment, root cause investigation, corrective actions, and preventative measures to avoid recurrence. All incidents should be thoroughly documented for audit purposes.
4. Technology and Innovations in Cleanroom Contamination Control
Advancements in technology are continuously improving cleanroom contamination management. Some emerging trends include:
- Robotics and Automation: Automated systems for material handling, disinfection, and environmental monitoring reduce human interaction and, therefore, contamination risks.
- Wearable Technology for Monitoring Personnel: Smart garments that monitor the behavior of personnel (e.g., movement, time spent in the cleanroom) can help in understanding contamination trends and identifying areas for improvement.
- Improved Filtration Systems: HEPA and ULPA filtration technology is evolving to provide better efficiency and longevity, while innovations in nanotechnology offer potential for advanced contamination control solutions at the molecular level.
Conclusion
Managing cleanroom contamination is a complex, multifaceted process that requires adherence to stringent protocols, the implementation of advanced technologies, and a culture of cleanliness and discipline. By focusing on facility design, personnel protocols, material handling, environmental monitoring, and continuous improvement, industries can maintain the necessary levels of cleanliness to ensure product integrity, regulatory compliance, and operational success. In industries where precision and sterility are paramount, the effective management of cleanroom contamination is not just a best practice—it is a critical necessity.
Read more: All About Cleanrooms - The ultimate Guide
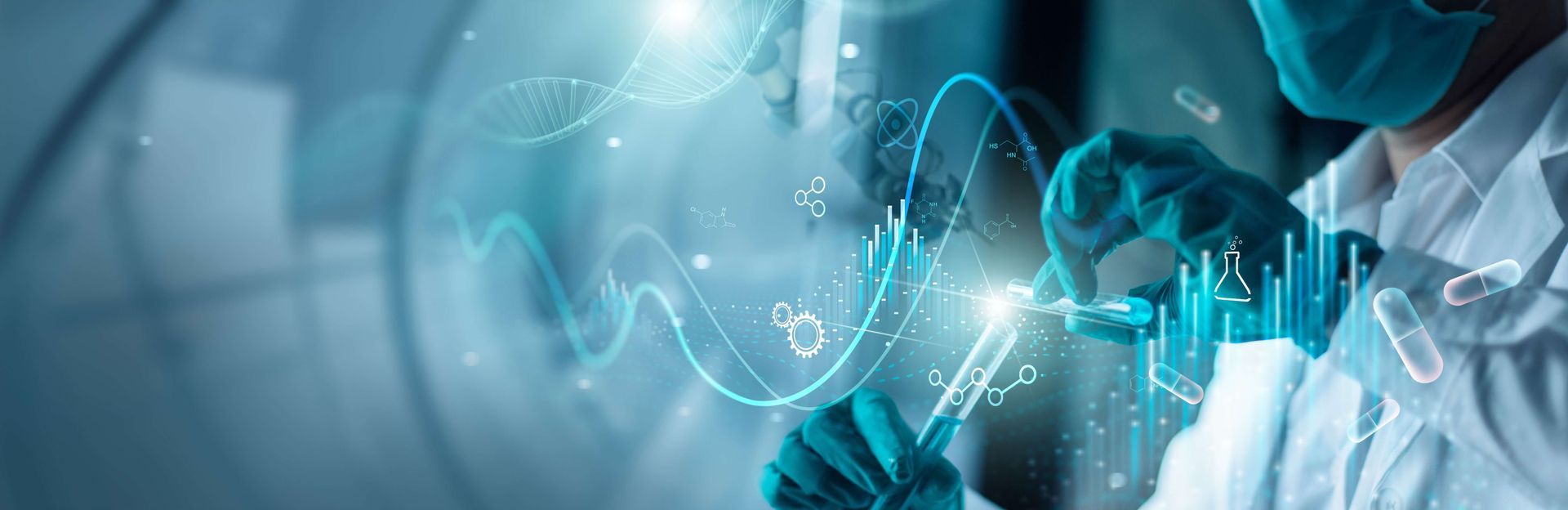
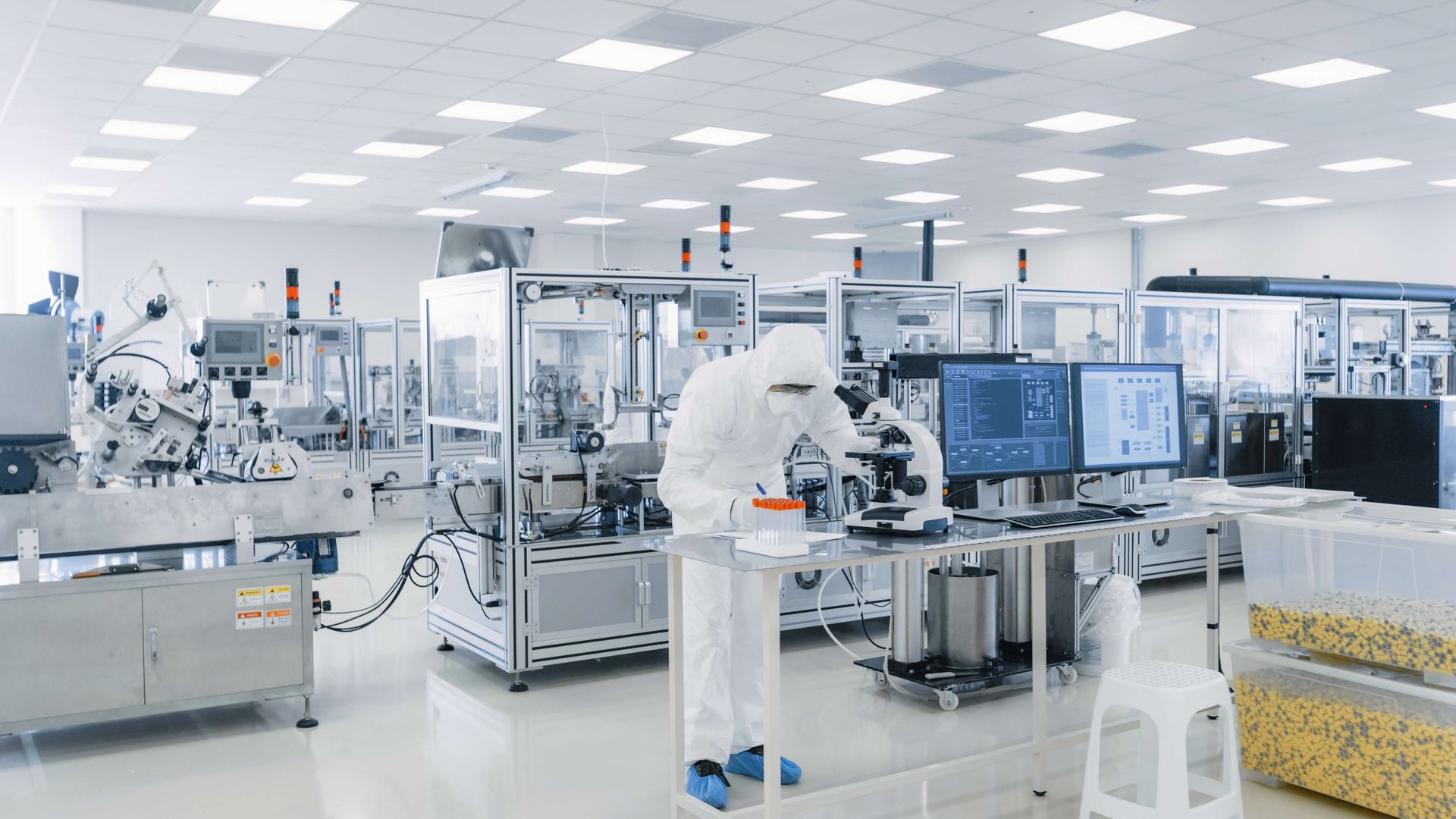