Your Cleanroom Specialist
Competence from + 100 Cleanrooms and since 1992
Cleanroom 14644 ISO 1-9 FS209E EU GMP ABCD USP 797, 800, 825
Cleanroom Design, Construction, Operation
Limit Your Liability
Cleanroom End User
Limit Your Liability - I make sure that Your Cleanroom project meets Your demands, from Design to Operation.
Architects
Limit Your Liability- I make sure that Your Cleanroom Specification will meet the End Customer needs, and at the right budget/cost.
Contractors
Limit Your Liability- I make sure that all building processes are aligned, in line with the Cleanroom demand.
Consulting Engineers
Limit Your Liability- I offer extended Cleanroom competence
Alata
Alice
Open Sans
Noto Sans
Bebas Neue
Great Vibes
Rock Salt
Exo
Belgrano
Overlock
Cinzel
Indie Flower
Staatliches
Roboto Slab
Lato
Noto Serif
Open Sans
Montserrat
Ubuntu
Rubik
Delius
Amiri
Montserrat
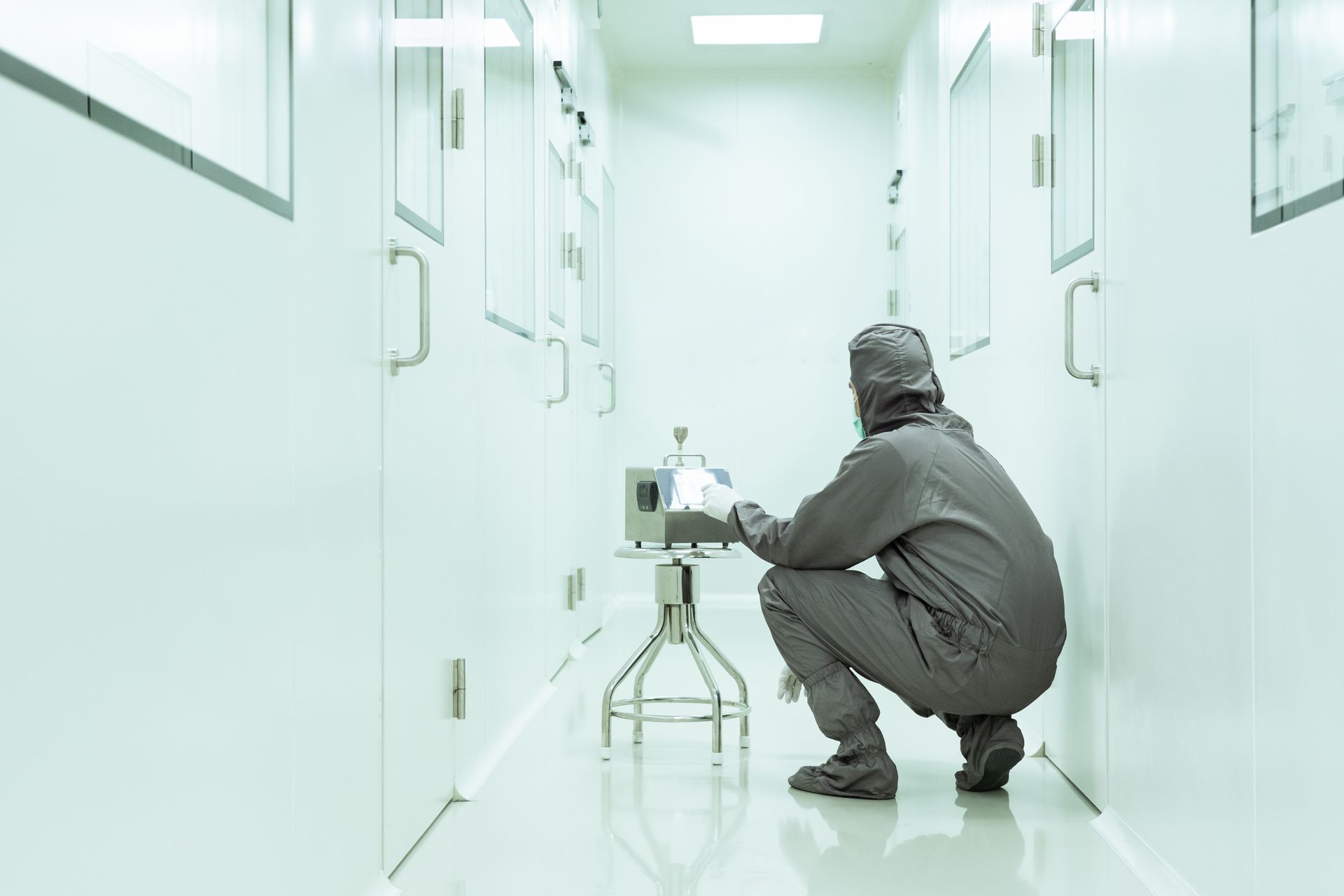
Introduction Cleanrooms are essential in various industries, including pharmaceuticals, biotechnology, semiconductor manufacturing, aerospace, and healthcare, where controlling contamination is critical to the success and safety of the products and processes. The integrity of a cleanroom environment, where particle, microbial, and chemical contamination must be tightly controlled, is fundamental in ensuring product quality, process reliability, and compliance with industry regulations. One of the key aspects of maintaining this controlled environment is risk assessment and management. Risk assessment in cleanrooms identifies potential hazards and vulnerabilities that may compromise the integrity of the cleanroom environment, product safety, and personnel health. Risk management then involves implementing strategies to minimize, control, and mitigate those risks. This article explores the importance of cleanroom risk assessment, the key areas of risk, how to conduct a thorough risk assessment, and the strategies for effective risk management within cleanroom environments. What is Cleanroom Risk Assessment? Cleanroom risk assessment is the process of identifying, evaluating, and prioritizing potential risks associated with contamination, environmental control failure, equipment malfunction, or human error that could compromise the cleanliness of the controlled environment. This process ensures that all aspects of the cleanroom’s operation are continuously monitored and managed to minimize risk. The goal of risk assessment is to maintain the highest possible level of cleanliness and integrity in the cleanroom while reducing the likelihood of contamination events that can lead to quality defects, safety issues, or regulatory non-compliance. A comprehensive risk assessment provides a solid foundation for implementing effective mitigation strategies to reduce these risks. Key Areas of Cleanroom Risk Cleanroom risk assessment encompasses a variety of potential hazards that can affect the environment, product quality, and personnel safety. The following are key areas of cleanroom risk that require careful analysis and management: 1. Contamination Risks Contamination is the most significant risk in cleanrooms. Contaminants can be particulate, microbial, or chemical in nature, and their presence can severely impact product quality, performance, and safety. Particulate Contamination : Dust, debris, or other particles present in the air or on surfaces can interfere with manufacturing processes, especially in sensitive industries like pharmaceuticals, where even microscopic particles can compromise sterility. Microbial Contamination : Microorganisms such as bacteria, fungi, and viruses are also a significant concern, especially in pharmaceutical and healthcare cleanrooms. Their presence can lead to product contamination, spoilage, or even endanger public health. Chemical Contamination : Chemicals, including solvents, reagents, or cleaning agents, can pose a risk if they are introduced into the cleanroom, either as airborne particles or through spills. Chemical contamination can damage sensitive equipment or products, leading to failures or degradation. 2. Environmental Control Failures Cleanrooms rely on precise control over environmental factors such as temperature, humidity, pressure, and airflow. Any deviation from the required environmental conditions can compromise the cleanroom’s classification and functionality. Temperature and Humidity Variations : Cleanrooms often require strict temperature and humidity control to prevent contamination and ensure process stability. Fluctuations in temperature or humidity can affect the properties of sensitive materials, cause microbial growth, or lead to unstable processes. Airflow and Filtration Failures : Cleanrooms use high-efficiency particulate air (HEPA) or ultra-low penetration air (ULPA) filters to trap contaminants. If these filters become clogged or ineffective, the cleanroom environment may no longer meet cleanliness standards. A failure in the HVAC system that affects airflow can lead to areas of poor air circulation or contamination buildup. Pressure Differentials : Maintaining proper pressure differentials between the cleanroom and adjacent areas is essential to prevent contamination from external sources. Any failure to maintain these pressure differentials could result in the ingress of contaminated air. 3. Human Error Human error is one of the most significant risk factors in cleanroom operations. Personnel who fail to follow proper gowning protocols, enter the cleanroom improperly, or mishandle equipment can introduce contaminants. Improper Gowning and Hygiene : Cleanroom personnel must wear specialized clothing such as gowns, gloves, masks, and hair covers to minimize the risk of shedding particles and microorganisms into the environment. Any failure to follow gowning protocols can lead to contamination. Equipment Handling : Mishandling of equipment or materials, including introducing foreign objects into the cleanroom or using unapproved tools, can lead to contamination or product defects. Training and Compliance : Insufficient training or lack of adherence to cleanroom procedures can result in mistakes or oversights that compromise the cleanliness of the environment. 4. Equipment Malfunctions and Failures Cleanroom equipment, including air filtration systems, monitoring devices, and environmental control systems, plays a critical role in maintaining the integrity of the cleanroom. Equipment malfunctions or failures can lead to serious risks to the cleanroom environment. Filter Failures : If HEPA or ULPA filters become clogged or degraded over time, they can no longer efficiently filter out airborne particles. This can lead to a breach in the cleanroom's contamination control. HVAC Failures : A failure in the HVAC system, such as an airflow disruption or temperature fluctuation, can cause contamination build-up or affect the cleanroom’s classification. Monitoring Equipment : Cleanrooms often rely on continuous monitoring systems to track particulate levels, temperature, humidity, and other critical parameters. If these monitoring systems fail, it may go unnoticed that the cleanroom is no longer operating within required conditions. 5. Regulatory and Compliance Risks Cleanroom environments are subject to strict regulatory standards that ensure safety, quality, and environmental compliance. Non-compliance with industry regulations can result in legal action, financial penalties, and even the shutdown of operations. Failure to Meet Cleanroom Standards : Cleanrooms must meet specific standards such as ISO 14644 for cleanliness classification, GMP (Good Manufacturing Practices), and FDA regulations for industries like pharmaceuticals and medical devices. Non-compliance with these standards can result in regulatory fines, product recalls, or loss of certification. Documentation and Audits : Cleanrooms must maintain proper documentation to prove compliance with regulations. Poor documentation practices or failure to keep records of inspections, maintenance, and equipment calibration can lead to compliance risks during audits. Conducting a Cleanroom Risk Assessment A cleanroom risk assessment involves systematically identifying and evaluating the risks associated with the factors mentioned above. The process typically includes the following steps: 1. Identify Hazards The first step is to identify potential hazards that could affect the cleanroom. This involves reviewing all areas of operation, from material handling and equipment maintenance to employee behavior and environmental control systems. Review the cleanroom layout and identify potential contamination sources. Examine environmental control systems and assess their reliability. Analyze employee actions and gowning protocols. Investigate the equipment used and identify failure points. 2. Assess the Likelihood and Severity of Risks Once hazards are identified, the next step is to assess the likelihood of each risk occurring and the potential severity of the consequences. This can be done using qualitative methods (e.g., expert judgment) or quantitative methods (e.g., risk matrices, probability calculations). Assess the frequency of human errors or equipment malfunctions. Estimate the potential impact on product quality or regulatory compliance. Consider the health and safety implications of contamination risks. 3. Evaluate Control Measures After identifying risks, assess the control measures already in place to mitigate these risks. Evaluate their effectiveness and determine if additional measures are necessary. Review the performance and maintenance of HVAC and filtration systems. Evaluate personnel training programs and compliance with gowning protocols. Examine the reliability and calibration of monitoring equipment. Assess existing contamination control procedures and cleanliness standards. 4. Develop Risk Mitigation Strategies Based on the assessment, develop strategies to mitigate identified risks. This may involve improving existing control measures or implementing new ones to reduce the likelihood or impact of potential hazards. Implement regular maintenance and testing of HVAC and filtration systems. Introduce more rigorous training and compliance monitoring for personnel. Enhance environmental monitoring systems with real-time alerts for deviations. Develop contingency plans for equipment failures or contamination events. 5. Monitor and Review Once risk mitigation strategies are implemented, it’s essential to continuously monitor the cleanroom environment and review the effectiveness of the strategies. Regular audits, inspections, and updates to risk management procedures help maintain compliance and ensure that the cleanroom environment remains safe and effective. Schedule routine audits and inspections of equipment and facilities. Continuously review environmental data from sensors and monitoring systems. Keep abreast of regulatory changes and update procedures accordingly. Conclusion Risk assessment and management are critical to maintaining the cleanliness, safety, and compliance of cleanroom environments. Given the potential for contamination, equipment failure, and human error, it is essential to proactively identify and mitigate risks in cleanroom operations. Regular risk assessments, combined with effective risk management strategies, ensure that cleanrooms operate at optimal performance while adhering to regulatory standards and industry best practices. By identifying risks early, evaluating control measures, and developing robust mitigation strategies, cleanroom operators can significantly reduce the potential for contamination, improve operational reliability, and ensure the quality of the products produced in these controlled environments. Effective cleanroom risk management not only minimizes the likelihood of costly failures but also promotes long-term success by maintaining high standards of cleanliness, safety, and regulatory compliance. Read more: All About Cleanrooms - The ultimate Guide
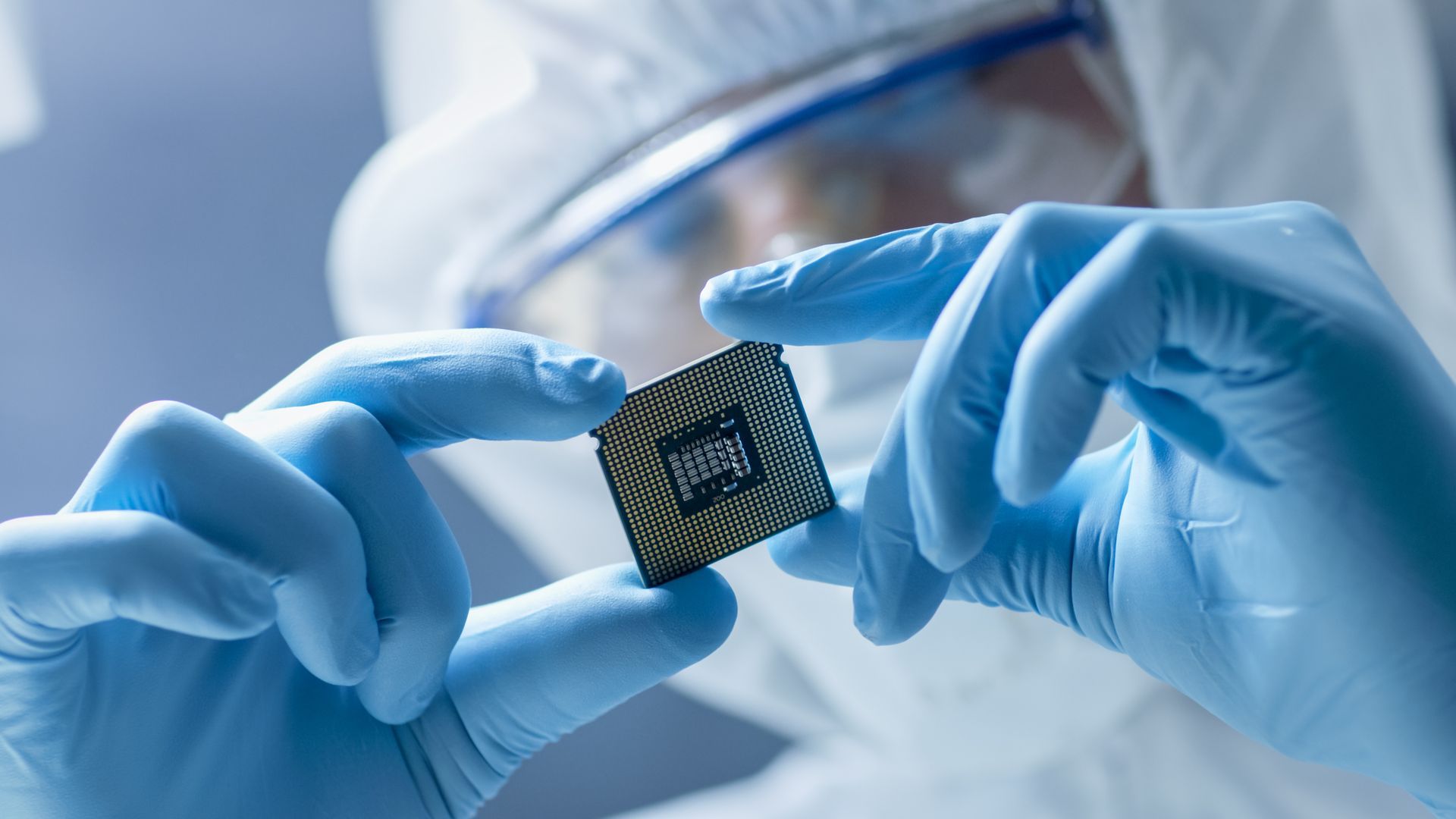
Introduction Solar panel manufacturing is a highly sophisticated process that requires a combination of advanced materials, precision engineering, and a contamination-free environment. As the demand for renewable energy sources grows, the solar energy industry has experienced rapid advancements in both technology and production methods. At the heart of these developments is the cleanroom – a controlled environment essential for ensuring the highest level of quality and efficiency in the production of solar panels. Cleanrooms are designed to maintain a controlled environment with minimal levels of dust, airborne particles, and other contaminants that could affect the delicate manufacturing process. In solar panel production, where minute defects can compromise efficiency and performance, the role of cleanrooms becomes paramount. This article explores the critical role of cleanrooms in solar panel manufacturing, the processes that require such environments, and the importance of contamination control in ensuring high-quality, reliable solar panels. Understanding Cleanrooms and Their Role Cleanrooms are environments that have controlled levels of airborne particles, temperature, humidity, and pressure. They are classified based on the concentration of particles of different sizes in the air, as specified by standards such as the ISO 14644 series. In the context of solar panel manufacturing, cleanrooms are required for various processes to ensure that even microscopic particles do not interfere with the production of highly efficient solar cells. The primary function of cleanrooms in solar panel manufacturing is to create an environment that prevents contaminants such as dust, chemicals, and even microbial particles from damaging the components and materials used to make solar panels. The introduction of foreign particles during production can lead to defects in the solar cells, reducing their efficiency, lifespan, and overall performance. The Solar Panel Manufacturing Process and Cleanroom Requirements The manufacturing process of solar panels is complex, involving multiple stages that require the use of highly refined materials and the integration of delicate components. These stages include the preparation of raw materials, the creation of solar cells, and the assembly of solar panels. Let’s explore these processes and examine why cleanroom environments are crucial at each step. 1. Silicon Wafer Production The foundation of most solar panels is the silicon wafer. Silicon is the most widely used material for creating solar cells, and its purity is critical to ensuring the efficiency of the solar panel. Silicon wafers are thin slices of silicon crystal, and any contaminants introduced during the slicing process can affect the quality of the wafer. Cleanrooms are vital in this early stage of solar panel manufacturing, as even tiny particles of dust or contaminants can alter the structure of the silicon, leading to defects. Silicon wafers must be cut, polished, and chemically treated in a cleanroom environment to remove surface contaminants and prepare them for the next stage of manufacturing. In these controlled environments, the silicon wafer is treated with chemicals and heated to high temperatures in vacuum chambers, processes that require meticulous contamination control to prevent particle buildup. 2. Solar Cell Production Once the silicon wafers are prepared, they undergo a series of processes to create the solar cells. This includes doping, where materials such as phosphorous or boron are introduced to the silicon to create the p-n junction, which is essential for the photovoltaic effect that generates electricity when exposed to sunlight. The doping process must be performed under stringent conditions, as even the slightest impurity can interfere with the efficiency of the solar cell. The introduction of doping materials in cleanrooms ensures that the process is controlled and free from contaminants that could affect the material properties of the silicon. In addition to doping, solar cells undergo a process called passivation, where a thin layer is applied to the surface of the cell to reduce recombination losses and improve efficiency. Again, these processes require extremely clean environments to ensure that the surface of the cell remains free from dust and particles that could disrupt the passivation layer or the overall structure of the solar cell. 3. Cell Testing and Sorting Once solar cells are manufactured, they are tested for efficiency, performance, and reliability. Solar cells are typically tested under simulated sunlight to evaluate how much energy they can generate. Cleanrooms play a crucial role during this testing phase by ensuring that the cells are not exposed to dust or particles that could interfere with the test results. During testing, solar cells must be handled with care to avoid contamination or physical damage. Cleanrooms provide the necessary environment to perform testing in a controlled space, where temperature, humidity, and cleanliness can be maintained to guarantee consistent results. The sorting of cells based on their efficiency is also performed in cleanrooms to ensure that only the highest-performing cells are used in the final assembly of the solar panels. 4. Panel Assembly The final stage in solar panel manufacturing is the assembly of individual solar cells into complete modules or panels. This process involves wiring the solar cells together and encapsulating them in protective layers. Cleanrooms are particularly important in this stage, as the cells must be carefully aligned and soldered to ensure proper electrical conductivity. The encapsulation process, which involves placing the cells in layers of protective materials like glass, plastic, and EVA (Ethylene Vinyl Acetate), also requires a cleanroom environment. Any dust or debris that settles on the cells during this process can reduce the efficiency of the panel or cause long-term degradation. Cleanroom environments prevent such contamination, allowing for the precise assembly of high-quality solar panels that can withstand environmental conditions over time. Importance of Contamination Control in Solar Panel Manufacturing Contamination control is the backbone of cleanroom environments and is crucial in ensuring that solar panels meet the highest quality standards. In solar panel manufacturing, contamination can take many forms, including dust, airborne particles, chemicals, and even human particles such as skin cells or hair. These contaminants can interfere with the delicate materials used in the production of solar cells and panels. Here are the key reasons why contamination control is essential in solar panel manufacturing: 1. Improved Efficiency Solar panels are designed to convert as much sunlight as possible into electricity. Contaminants, even at microscopic levels, can impede the electrical performance of the solar cells, leading to decreased efficiency. For instance, dust particles or impurities can cause hotspots within the cells or interfere with the electrical connections, reducing the panel’s overall ability to generate power. By maintaining strict contamination control in cleanrooms, manufacturers can ensure that solar panels are as efficient as possible, with minimal defects and maximum performance. 2. Increased Lifespan Solar panels are designed to last for decades, but contamination during the manufacturing process can lead to long-term degradation. For example, contamination on the surface of solar cells can create weak spots that are more susceptible to damage from UV radiation or environmental factors. By using cleanroom environments to eliminate contaminants during production, manufacturers can increase the longevity of the solar panels, ensuring that they continue to perform well over time. 3. Consistency and Reliability In industries like solar energy, where performance and reliability are critical, even small variations in manufacturing quality can have significant impacts. Contamination can lead to inconsistencies in the manufacturing process, resulting in panels that perform differently from one another. By maintaining a cleanroom environment, manufacturers can ensure that each solar panel is produced to the same high standard, providing consistent and reliable performance across all units. 4. Meeting Regulatory Standards Solar panel manufacturers are often required to meet specific regulatory standards for quality, safety, and environmental impact. These standards ensure that the solar panels are safe to use and will perform as expected throughout their lifespan. Cleanrooms are essential for meeting these standards, as they provide the necessary environment for producing high-quality panels that comply with regulatory requirements. Energy Efficiency and Sustainability in Cleanroom Design In the context of solar panel manufacturing, energy efficiency is a crucial consideration. While cleanrooms are necessary for ensuring product quality, they are also energy-intensive environments due to the HVAC systems required to maintain strict environmental conditions. Solar panel manufacturers are increasingly adopting energy-efficient cleanroom designs that minimize energy consumption while maintaining the required standards for cleanliness and contamination control. Energy-saving technologies such as variable air volume (VAV) systems, heat recovery systems, and high-efficiency air filtration systems are being implemented in cleanroom designs to reduce their environmental impact. These innovations not only lower operating costs but also align with the sustainability goals of the solar energy industry, making cleanroom manufacturing more energy-efficient and environmentally friendly. Conclusion Cleanrooms are indispensable in the manufacturing of solar panels, where even the smallest contaminant can compromise the efficiency, performance, and reliability of the final product. From the production of silicon wafers to the final assembly of solar panels, cleanrooms ensure that the manufacturing process remains free from dust, particles, and other contaminants that could degrade the quality of the solar cells. The controlled environments provided by cleanrooms help manufacturers produce high-efficiency, long-lasting, and reliable solar panels that meet regulatory standards and contribute to the growth of the renewable energy industry. As the demand for solar energy continues to rise, cleanroom technology will play an even more significant role in driving innovation and ensuring the production of high-quality solar panels. Read more: All About Cleanrooms - The ultimate Guide
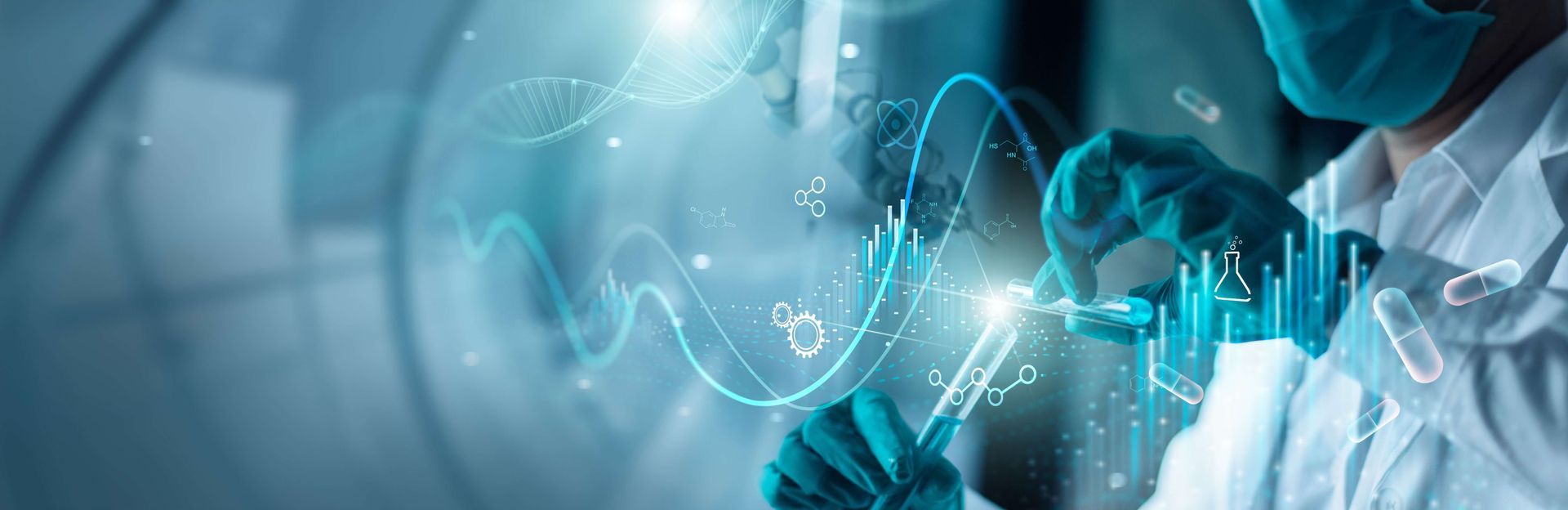
Introduction Cleanrooms, crucial environments in industries like pharmaceuticals, biotechnology, semiconductor manufacturing, aerospace, and healthcare, are designed to minimize contamination and maintain stringent environmental controls. These spaces require high levels of energy input to maintain optimal conditions, such as precise temperature, humidity, air filtration, and pressure regulation. Cleanroom systems typically operate continuously, making them some of the most energy-intensive spaces within manufacturing and research facilities. While cleanrooms are designed with safety, product integrity, and contamination control in mind, it is equally important for businesses to consider energy efficiency. With rising energy costs, growing environmental concerns, and increasing regulatory pressure, cleanroom operators must find ways to minimize energy consumption without compromising performance, cleanliness, or safety. This article explores key strategies and technologies for improving energy efficiency in cleanroom operations, focusing on sustainable approaches that can reduce operating costs, enhance environmental impact, and improve overall system performance. The Energy Demands of Cleanrooms Before diving into strategies for energy efficiency, it's important to understand why cleanrooms are so energy-demanding. Cleanrooms typically require: HVAC Systems : Cleanrooms rely on high-efficiency heating, ventilation, and air conditioning (HVAC) systems to maintain precise temperature, humidity, and air quality standards. HVAC systems must continuously filter and circulate large volumes of air, ensuring that the air is free from particles, microorganisms, and chemical contaminants. This high airflow and filtration requirement consumes a significant amount of energy. Air Filtration : Cleanrooms use specialized filtration systems, such as HEPA (High-Efficiency Particulate Air) or ULPA (Ultra-Low Penetration Air) filters, to remove airborne particles. These filters need to be replaced or cleaned regularly, and the ventilation systems must work harder as filters become clogged, leading to higher energy usage. Pressure Control : Cleanrooms must maintain precise pressure differentials to prevent contaminants from entering the space from adjacent areas. This requires continuous control and monitoring of airflow, which is energy-intensive. Lighting and Equipment : Cleanrooms also use specialized lighting and equipment that are designed for cleanroom environments. These may include bright, flicker-free LED lights, which are energy-efficient but still add to the overall energy load, especially when the cleanroom is operational 24/7. Why Energy Efficiency Matters in Cleanrooms Energy efficiency in cleanrooms is vital for several reasons: Cost Savings : Given the constant energy demand for HVAC systems, filtration, lighting, and equipment, energy consumption in cleanrooms can account for a significant portion of a facility's total energy costs. Implementing energy-saving strategies can reduce electricity and heating/cooling expenses over time, helping businesses control costs. Environmental Responsibility : As businesses become more aware of their environmental impact, reducing energy consumption helps minimize carbon footprints. Many industries, particularly those in high-regulation sectors, are facing increasing pressure to demonstrate environmental stewardship and sustainability. Compliance with Regulations : Government regulations and industry standards for energy use are tightening. Cleanroom operators need to comply with these standards to avoid penalties or fines. Additionally, energy-efficient practices may also be mandated in certain sectors to align with sustainability goals and reduce overall environmental impact. Operational Performance : Inefficient energy systems can lead to unnecessary wear and tear on equipment, increased maintenance costs, and, in some cases, disruptions in cleanroom operations. Efficient systems are often more reliable and cost-effective to maintain. Strategies for Improving Energy Efficiency in Cleanrooms There are several strategies that cleanroom operators can implement to improve energy efficiency without compromising the integrity of the cleanroom environment. These strategies can be broadly categorized into operational, technological, and design-based approaches. 1. Optimizing HVAC Systems Given that HVAC systems are the most energy-intensive component of a cleanroom, improving the efficiency of these systems should be a primary focus. Several techniques can enhance HVAC energy efficiency: Variable Air Volume (VAV) Systems : A variable air volume system adjusts the amount of airflow depending on the cleanroom's needs. By reducing airflow when less filtration is required (e.g., during periods of low activity), VAV systems help lower energy consumption. The system only increases airflow when high air exchange rates are necessary, such as during production or cleaning cycles. Demand-Controlled Ventilation (DCV) : DCV adjusts ventilation rates based on real-time occupancy or contaminant levels. For instance, during periods when fewer people are in the cleanroom, or when the contaminants are minimal, the system can reduce airflow, saving energy. Sensors can be used to monitor CO2 levels, air quality, and particle counts to control the ventilation rates dynamically. Heat Recovery Ventilation (HRV) : Heat recovery ventilation systems capture energy from the exhaust air and use it to precondition incoming air. This can significantly reduce the need for heating and cooling energy, as the HRV system recycles energy that would otherwise be wasted. In cold climates, this can reduce heating costs, while in warm climates, it reduces the cooling load. Airflow Optimization : Optimizing airflow through careful layout and design of air distribution systems can improve HVAC efficiency. Strategies include eliminating unnecessary ducts, reducing air leakage, and placing air inlets and outlets in optimal locations for effective air distribution. Proper sealing and insulation also ensure that air does not escape through cracks or gaps in the cleanroom envelope. 2. Energy-Efficient Filtration Systems The filtration system is another significant energy consumer in cleanrooms. To improve energy efficiency, consider the following options: Filter Efficiency and Maintenance : The efficiency of filters plays a major role in how hard HVAC systems have to work. Choosing the right filter for the cleanroom’s needs—whether HEPA or ULPA—ensures optimal performance. Furthermore, regular maintenance, such as cleaning or replacing filters, reduces strain on HVAC systems and ensures that air filtration is both effective and energy-efficient. Low-Resistance Filters : Newer technologies have introduced low-resistance filters that require less power to move air through them. These filters maintain the high filtration standards necessary for cleanrooms but reduce the pressure drop across the filter, thereby reducing energy use. Modular Filter Banks : Modular filter banks allow for the addition or removal of filters as needed. This helps maintain airflow without overburdening the system. If the cleanroom’s requirements change (e.g., higher particle filtration or changing regulatory standards), the system can be adjusted without significantly impacting energy use. 3. Energy-Efficient Lighting Lighting is an important component of cleanroom energy use. Cleanrooms often require bright, uniform lighting to ensure optimal working conditions. However, this can result in high energy consumption. To optimize lighting: LED Lighting : LED lighting is much more energy-efficient than traditional fluorescent lighting. LED bulbs consume less energy, last longer, and generate less heat. Additionally, LEDs can be integrated with smart lighting systems that adjust based on the time of day or occupancy, further reducing energy consumption. Motion Sensors and Timers : Installing motion sensors and timers can ensure that lights are only on when needed. For example, lights can automatically dim or turn off when no personnel are present in the cleanroom, which significantly reduces energy consumption without affecting operations. Daylight Harvesting : If the cleanroom has access to natural light, consider using daylight harvesting systems that adjust artificial lighting levels based on available natural light. This can reduce the amount of electricity needed to illuminate the space during daylight hours. 4. Energy-Efficient Equipment Other energy-consuming equipment, such as sterilizers, autoclaves, and other machinery, also contributes to the overall energy usage of a cleanroom. To improve energy efficiency in equipment: Upgrading Equipment : Older equipment may not be optimized for energy use. Upgrading to newer, energy-efficient models can result in significant energy savings. For instance, modern sterilizers are designed to use less water, energy, and time compared to older models. Scheduling Equipment Use : In some cases, the timing of equipment use can affect energy consumption. For example, scheduling equipment like autoclaves to run during off-peak hours or during low-energy-demand periods helps reduce the overall energy load on the system. 5. Design Considerations for Cleanroom Energy Efficiency The design phase offers many opportunities to incorporate energy efficiency into cleanroom operations. These strategies include: Room Layout : Properly designing the cleanroom layout can optimize airflow and minimize the need for excessive HVAC energy. The placement of equipment, personnel areas, and materials should be considered to ensure efficient air distribution, minimize contamination, and reduce energy use. Building Envelope : The cleanroom's exterior walls, windows, and roof should be well insulated to prevent heat loss in cold climates and heat gain in hot climates. Proper insulation reduces the heating and cooling demands of the HVAC system. Energy-Efficient Materials : The use of energy-efficient materials in the construction and design of cleanrooms, such as energy-efficient doors, windows, and walls, can help optimize energy use and prevent unnecessary energy loss. Conclusion Energy efficiency in cleanrooms is critical for reducing operational costs, improving environmental sustainability, and ensuring long-term operational performance. By implementing strategies such as optimizing HVAC systems, improving filtration efficiency, utilizing energy-efficient lighting, and upgrading equipment, cleanroom operators can significantly reduce their energy consumption while maintaining the cleanliness and functionality required for sensitive manufacturing processes. Cleanroom design, including room layout and material selection, also plays an important role in achieving energy efficiency. Ultimately, by adopting these energy-efficient strategies, cleanroom operators can not only lower costs but also contribute to broader sustainability goals and comply with increasingly stringent regulatory requirements. Read more: All About Cleanrooms - The ultimate Guide